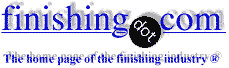
-----
Problems in cyanide copper plating
< Prev. page (You're on the last page of the thread)
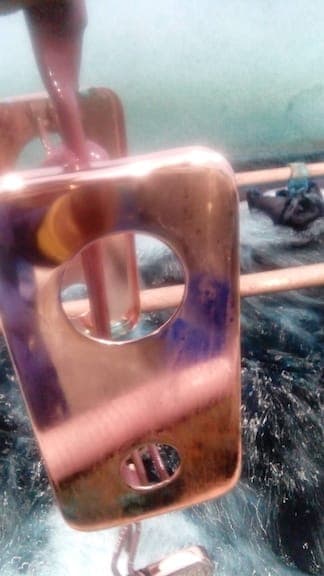
Q. Hello... In copper cyanide plating I am facing multiple issues.
At first I was facing issue of low throwing power. At low current density areas I was facing issues of low coverage.
After that I decided to add 1 kg of sodium cyanide to the solution.
After this the issue of covering has been solved. But now the job is having burnt likes patches. I cannot recognize it as burning or something else. But you can say that it is like roughness all over the job.
The tank is of 650 litres.
Should I add copper cyanide to the bath.
I had never made addition of caustic to the solution.
Does caustic helps in increasing throwing power.
Does caustic causes roughness on the job?
What is the main sodium thiosulphate
⇦ on
eBay
or
Amazon [affil link]
in cyanide bath.
Is there any regular addition required.
- jalandhar, Punjab, India
A. If your free cyanide is OK (1 - 1.5 oz/gal, if memory serves) you might try adding some Rochelle salts (sodium potassium tartrate)
⇦ on
eBay
or
Amazon [affil link]
.
This is not easy to test for; a modest addition (0.5 oz/gal) will not hurt.
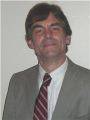
Dave Wichern
Consultant - The Bronx, New York
December 1, 2016
December 6, 2016
A. Good day Sikhil.
From your photo, it is apparent that this bath is an acid copper. The anode bags appear to be blue in colour. If this is true, do not add any more cyanide.
In cyanide copper baths, hydroxide will increase bath conductivity, aide in anode dissolution, causing the metal content to rise. Watch the pH here.
Rochelle salts act as a grain refiner, and also aid in anode dissolution, causing the metal also to rise.
In acid copper baths, the ratio of sulfuric to sulphate is important eg: 1:4 max., as sulphate has a limited solubility. What is the chloride content, and are you within range of the brighteners/carrier concentrations?
Come back with more specific info.
Regards,
Aerotek Mfg. Ltd. - Whitby, Ontario, Canada
Q. Hi,
I'd like to have more information regarding Mr Robert H Probert's suggestion to use pure zinc to plate on zinc cast alloy's. Is it melting zinc or is it acid zinc?
Regards
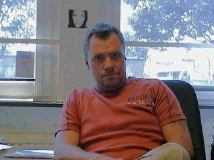
Anders Sundman
4th Generation Surface Engineering
Consultant - Arvika,
Sweden
December 1, 2016
Hi Anders. I'm sure Robert is speaking of zinc electroplating not hot-dip galvanizing. Electroplating of zinc castings with zinc is also often done before chromate conversion coating instead of trying to directly chromate conversion coat the casting.
Regards,
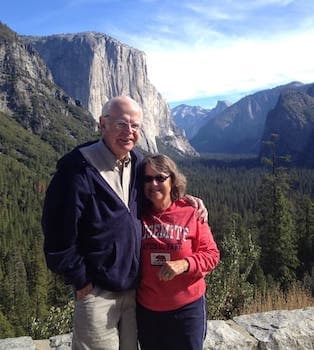
Ted Mooney, P.E. RET
Striving to live Aloha
(Ted can offer longterm or instant help)
finishing.com - Pine Beach, New Jersey
December 2016
Q. Hi Ted,
Did you know if it in cyanide, acid or alkali zinc they plate zinc castings?
Regards
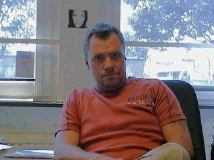
Anders Sundman
4th Generation Surface Engineering
Consultant - Arvika,
Sweden
December 5, 2016
A. Hi Anders. Several respondents on letter 16200 recommend alkaline zinc plating of zinc diecastings before chromating. Although I am not personally familiar with Robert's idea of zinc plating zinc die-castings before copper plating, from that it would seem that alkaline zinc would be the best process.
Regards,
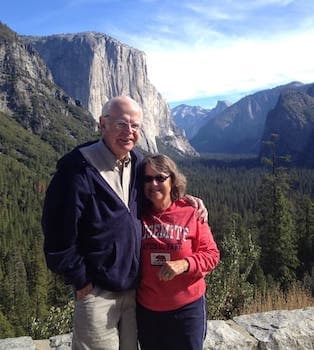
Ted Mooney, P.E. RET
Striving to live Aloha
(Ted can offer longterm or instant help)
finishing.com - Pine Beach, New Jersey
December 2016
Cyanide copper plating pits in low current density areas
December 15, 2016Q. I have tried carbon treating my cyanide bath. It has helped a bit. But the problem is not solved completely. At low current density areas. There is pitting-like patterns. The problem is coming on flat surfaces at low current density areas.
At high current density areas, there is no pitting.
The pitting looks like small dots all over the surfaces of low current density areas.
I am not using Rochelle salt at all.
My bath is completely based on copper cyanide and sodium cyanide.
There was no such problem in the beginning.
Whenever problem arises I add 5 kgs of copper cyanide and 7.5 kgs of sodium cyanide. It generally resolved my issues in the past.
But now carbon treating and additions of copper cyanide and sodium cyanide is not helping.
While carbon treating I had used 500 grams to 650 liters of solution.
It is adamant to the solution?
I had also tried dummying.
In the dummy also small bubbles like roughness is appearing on low current density areas.
Is this pitting because of impurity or I need to add some copper cyanide and sodium cyanide to the solution?
Please help me out.
- jalandhar, Punjab, India
Q. Hi.
Sorry, I have another request about copper cyanide bath: after plating and hot drying, the workpiece's color converts to orange.
Can you help me about this problem?
Chemical Engineer - Alexandria, egypt
March 20, 2017
Q. Hi,
I am Facing problem each time I put sodium cyanide in copper cyanide bath, it converts to brass deposit.
Analysis sodium cyanide 99.9% and there isn't zinc, and if we put sodium in another copper bath it's ok
Can you help me about this problem in the bath and the source of zinc ions?
Chemical Engineer - Alexandria, egypt
April 11, 2017
A. Hi Asmaa,
Zinc ions might come from copper anode or other plating accessories like anode basket, heater, circulation pump, etc.
Regards,
David
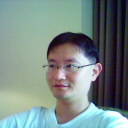
David Shiu
- Singapore
April 17, 2017
Q. Sir,
I have problem in my cyanide copper plating bath. The problem is colour of plating is getting reddish. How to solve this issue? Kindly give me suggestion to solve the problem. Copper metal is 48.5 g/l and free KCN is 8.5 gm/l in strike bath; and 46.9 g/l and free KCN is 9.10 g/l in main bath.
Regards,
Nilesh mavani
Baroda, gujarat, India
April 26, 2018
A. Morning Nilesh, Hope you have already resolved your problem. I have had similar issues with copper strikes in the past. First, 48.5 g/L (6.4 oz/gal) seems a bit high for metal content. Not that I assume it is the cause of the discoloration. I'v always tried to keep copper between 2 and 3 oz/gal (14-23 G/L). The first time I experienced this deep red color in a KCN Cu strike it was due to drag in contamination from prior rinses. Check your bath for any contamination. if there is any suspicion I suggest changing any Swills or drag out baths prior to the strike. Once I saw this problem develop due to over temp as well. An operator bumped the heat control and pushed the temp way up. It was only noticed because the copper started to get a deep red tarnished color. What are you putting the copper over? Amps-dwell time? What is the potassium carbonate concentration? And what is the "Main" bath you mention? Also copper? Is the redness starting at the strike or after that "main" bath you mentioned?

Chance Dunstan
Electroplating/Forming/Coating Manager
Placerville, California USA
May 21, 2018
Roughness in copper cyanide bath
July 25, 2018Q. We have had roughness on the high current density areas of our parts and on the Hull Cell
⇦ huh?
plates. from what I can tell its not shelf roughness because its not just on the top surface of parts. the bath is a cupralite cyanide copper plating bath prepared with sodium copper cyanide solution and sodium cyanide. brightener additions are cupralite 10 and Cupralite 20
analysis as follows
copper metal: 5.03 oz/gal (spec 4-6)
free cyanide: 1.82 oz/gal (spec 1-2)
cupralite 20: 6 %v/v (spec 4-8)
total carbonates: 8.44 oz/gal (Spec nmt 10 oz/gal)
1.so far the bath has been carbon filtered with flow king pelletized in a carbon filter bag carbon to remove some organic impurities the filter was flushed to ensure that carbon doesn't contribute to particulates
2. the entire bath was decanted into totes through a 10 micron filter bag the tank was rinsed and cleaned then the anodes were returned to the bath and solution was returned to the bath through a fresh filter bag.
3. we were running very low on copper in the anodes a portion of copper was added to each anode
4. the anode bags are old we have new anode bags on the way to replace them.
i was thinking maybe the roughness was due to particulates in the bath but we still have the problem despite the bath decant and filtration. would any of you have another idea to try and fix the problem.
plating chemist - detroit, Michigan,USA
Seeking alternative methods for lowering Copper Cyanide in Alkaline Bath
Q. We barrel plate lead cores with copper in a sodium cyanide and caustic bath. Our copper cyanide naturally rises over a period of time, and we have been experimenting replacing a few of our titanium baskets loaded with copper anodes with iron baskets loaded with iron anodes. We have found that our Copper Cyanide concentration is lowered and it raises the free cyanide. This practice does produce a desired outcome, but the drawback is the exponential increased production of Carbonates in the bath and an increase in Copper Oxide buildup on the iron baskets containing the iron anodes. Please advise if there are other methods to lowering the Copper Cyanide concentration without using iron. We are also seeking the pro's and Con's of using Iron in the baths at any point.
Bobby FarnerShop Chemist - St George, Utah USA
September 18, 2018
Q. My copper cyanide bath is not catching plating. Please what to do?
Jamiu ochawu- kano state, nigeria
July 13, 2019
A. Hi Jamiu. This could be absolutely anything from a defective rectifier to the parts that you're trying to plate actually being aluminum rather than zinc. Step 1 is probably plating a Hull Cell panel to narrow it down at least a little bit. Good luck.
Regards,
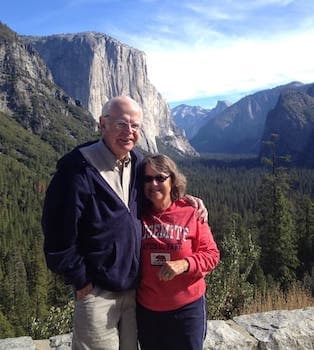
Ted Mooney, P.E. RET
Striving to live Aloha
(Ted can offer longterm or instant help)
finishing.com - Pine Beach, New Jersey
July 2019
Cyanide copper plating blisters
Q. Sir please tell me what is the reason of bubble in cyanide copper electroplating?
Sir, base is aluminum and first plating nickel then cyanide copper on this.
- Delhi, India
August 23, 2019
A. Hi Amit. Have you burst these bubbles and examined them? Underneath the bubble on the substrate is bright shiny nickel, and the underside of the blisters is definitely copper?
This is an unusual plating sequence ... what kind of components are you making? And are you sure that you proceed from nickel plating directly to copper plating with no delay other than quick rinsing?
Regards,
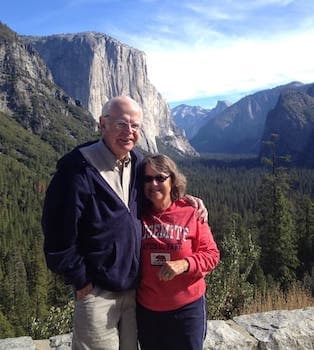
Ted Mooney, P.E. RET
Striving to live Aloha
(Ted can offer longterm or instant help)
finishing.com - Pine Beach, New Jersey
August 2019
Q. I am using copper cyanide bath. The issue is that whenever I am plating mild screws, after nickel plating there are two shades in plating resulting, orange and red. I have added copper cyanide and caustic soda ⇦liquid caustic soda in bulk on
Amazon [affil link]
, heated the solution up to 30 °C but the result is same. The density is 12 and pH is 11.
Kindly help me out.
- Karachi Pakistan
August 30, 2019
Q. We are doing copper plating on iron rod in Barrel plating in Rochelle copper bath.
Bath concentration 20 g/ltr Cu metal
Free cyanide is 5 g/ltr.
When we start giving 6 VDC voltage my copper plate become black, and which results in black or patches type plating on wire rods.
I made new solution but the problem is still the same. Should I add some NaOh to solution?
Please help me.
- Jaipur, Rajastha, India
February 26, 2020
A. Hello Dheeresh,
The common Rochelle bath contains sodium potassium tartrate. You don't mention that in your bath makeup.
Retired - Winston Salem, North Carolina USA
February 28, 2020
Q. Good afternoon sir,
I have cyanide copper plant and doing copper platting on ms plates. I am facing issue regarding quality of components -- issues like black patch observed after plating, and uneven plating thickness. Please provide me solution for above.
- Ahmednagar, Maharatra
August 22, 2020
Good day to you. I have a question I hope someone can help me with. My company uses a bright copper cyanide plating solution at about 150 °F (Copper-lume). The problem is we use a 304 stainless steel steam coil inside the tank, which more than once has developed a hole and bled back into our boiler, which is really bad for the boiler. In the past, even now I should say, the reason we find out is our in-house lab people check the out going water daily. After checking all 4 cyanide tanks with air, we are able to see the air leak. Is there anything else besides 304 s.s. that will stand up to the aggressive solution? Thank you for any help. Oscar
oscar estradamaintenance - el paso texas
August 10, 2021
A. Hi Oscar. Hopefully this is a 15 psi low pressure boiler just for the plating lines, not a big high pressure unit for a major factory. I don't like to see high pressure steam used in plating tanks -- too dangerous here in 2021.
Switching to Teflon coils would fix the problem, but they would be much bigger and quite expensive, and probably not necessary.
First off, you should be able to reduce the chance of contaminated condensate getting to the boiler by installing vacuum breakers if you don't yet have them. They should be standard practice, and what they do is: when the steam cools and contracts and pulls a vacuum, they let air into the coil instead of the vacuum pulling plating solution into the coil.
But secondly, you should be using dielectric unions or at the least "radiator hose" to electrically isolate the coils from the plating current if you're not already. I don't think a cyanide copper plating solution is likely to be chemically corroding your coils, I think it's more likely to be a stray electrical current.
Luck & Regards,
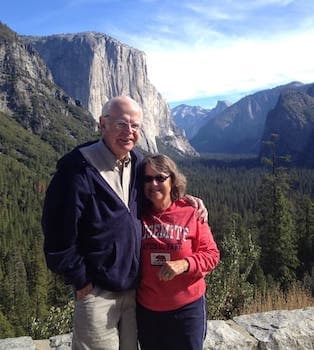
Ted Mooney, P.E. RET
Striving to live Aloha
(Ted can offer longterm or instant help)
finishing.com - Pine Beach, New Jersey
August 2021
Q. My cyanide copper solution temperature rises automatically and goes over 70 °C and anodes are showing a black and grey layer on it. Please suggest a better solution.
Thank you so much in advance.
- New delhi (india)
September 10, 2021
A. Hi B.D., Your rectifier puts Watts of Heat (Volts X Amps) into the plating tank, tending to cause its temperature to rise; whereas evaporation and other heat losses tend to cause the temperature to drop.
If the power input from the rectifier exceeds the evaporation and other losses, the temperature will rise. However, 70 °C (158 °F) is quite hot, so evaporation and other heat losses are significant, and I am not personally familiar with a copper cyanide plating tank operating at that temperature requiring a cooling system ... so it strikes me that something may be strange or wrong. Do you have choffles (floating plastic balls) on the surface reducing the evaporation loss?
Please tell us something about the plating solution, and what you are plating, and barrel or rack, and the rectifier voltage and amperage readings. Also please tell us about your anodes, cast or balls (steel anode baskets?). Unfortunately it's very difficult to sort out what is going on until you give us details. Thanks.
Luck & Regards,
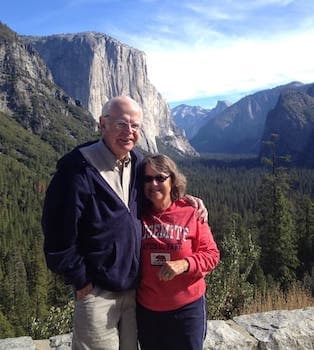
Ted Mooney, P.E. RET
Striving to live Aloha
(Ted can offer longterm or instant help)
finishing.com - Pine Beach, New Jersey
September 2021

Q, A, or Comment on THIS thread -or- Start a NEW Thread