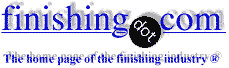
-----
Process of Zinc-Nickel Plating
< Prev. page (You're on the last page of this topic)
This meeting place welcomes Q&As, photos, history, & interesting tidbits.
Please engage with other posters
• When people show interest in each other's situations, the page quickly becomes a fun & informative learning experience for everyone !
• When people show no interest in other people's postings, and just post their own, it often quickly deteriorates into a string of unanswered questions 🙂
Q. Hi all. I have a question about zinc-nickel plating. We are making a part and have to send to our finisher for getting zinc-nickel plating. This part has two PEMs; if we use zinc plated PEMs, after plating the color of PEMs turn black. I do not know what is the reason? Material of PEMs, thickness of zinc on the PEMs, or washing time and composition before plating?
Thanks.
quality engineer - Vancouver, BC, Canada
March 31, 2016
Q. We are facing problem in Alkaline Zinc Nickel Plating Self Tap screws M5 x 18 . Carbo-nitriding process with 340 HV hardness. Even after 3 Hours of Plating coating thickness found 2 - 4 Microns in the parts. Load Qty : 40 Kgs Current : 500 Amps.
Any suggestion to overcome this problem.
- Tamil Nadu, India
April 12, 2016
Q. Hi,
We are doing zinc nickel plating on alloy steel components. Some of these components have tubular shapes and cavities about 40 mm in dia and 50 mm deep. We are getting zero thickness in the inner side of these cavities and the salt spray fails within 120 -150 hrs. On the outside, the thickness achieved is around 25 - 30 micron and the salt spray test is also okay from the outside area only. Can you please suggest any remedy to achieve thickness at the inside area of these parts. Voltage = 4-6 V. Time = 30 minutes.
- Karachi, Pakistan
June 14, 2016
Q. Dear sir,
Please help me regarding acid zinc-nickel. I am starting acid zinc-nickel plating in barrel plating; I don't know what are the standard parameters of this bath, and some problems face me every day. After 2 barrel plating the fastener threads are not bright and if I am doing Hull Cell test then Hull panel LCD area is full dull. What should I do I don't understand. Please help me with standard bath parameters and maintenance of acid zinc-nickel bath.
Thanks sir .
- Mumbai, Maharastra, India
July 14, 2016
A. Hi, Amit. The supplier you are purchasing your zinc-nickel plating process from will have a "technical data sheet" instructing you how to operate it. It's a fairly complex process because you don't just need the right thickness and brightness, you need to maintain the correct percentage of nickel in the deposit or it will not offer the proper corrosion resistance. Good luck.
Regards,
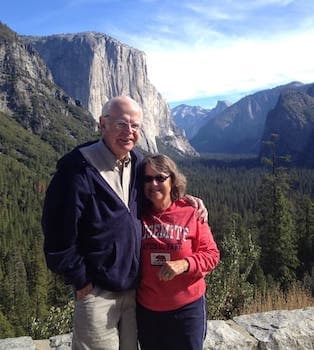
Ted Mooney, P.E. RET
Striving to live Aloha
finishing.com - Pine Beach, New Jersey
Q. We want to use Zn-Ni Electroplated coating for our clamps and thinking to get the 25 µm to 30 µm Zn-Ni electroplated coating thickness with 12 wt% of Nickel content. Does this thickness improve the corrosion resistance purposes or it's detrimental? Should we need to adhere to 8 µm to 14 µm coating thickness to achieve the optimal performance?
John Stacey- Sydney, Australia
July 22, 2016
A. Hi John. For standard zinc plating there is no doubt that 25 microns is better than 8 to 14. Standards like ASTM B633 call for 5 microns for mild exposure, 8 for moderate, 13 for severe, and 25 for very severe. To my knowledge 25-30 microns of zinc-nickel is not deleterious, but you might check with your supplier because there might possibly be difficulty with chromating, roughness, or something else they caution you about for their process at that thickness.
Regards,
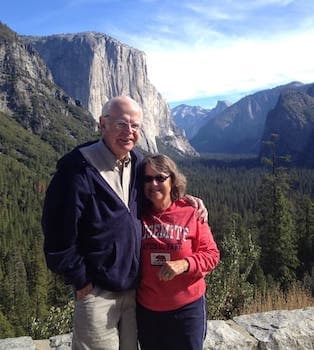
Ted Mooney, P.E. RET
Striving to live Aloha
finishing.com - Pine Beach, New Jersey
Q. I am trying to deposit Zn-Ni on 4 inch x 2 inch CM steel sample using a chloride bath with pH 5.5-6.0. I am plating two samples simultaneously using a 15 L bath. I am seeing black and burnt coating at the bottom up to a height of nearly 1.5cm. Kindly suggest how to overcome. I am using a filtration system and the cathode movement is very slow.
Regards
- UP, India
December 9, 2016
A. Hi Manju,
Please enlighten us with:
- Barrel or rack plating?
- Acid Zinc-Nickel: which nickel percentage (low or high)? Do you test in hull cell? What are your parameters (potassium chloride, metallic zinc, voltage, time, temperature)? Do you test for iron?
I think that we can help you if you can give us more information.
Best regards!
Daniel
N FERRARIS S.A. - Cañuelas, Buenos Aires, Argentina
Q. I am doing rack plating. The Ni content in close to 17g/L and the current density is around 2A/dm2.The plating duration is 30mins.
Manju Srinivasan [returning]- UP, India
A. to Mr.Srinivasan:
Dear Sir:
As I got, in the production line you are having some kind of heat treatment i forging. May you should have a look to the Hydrogen Brittleness effect on your parts. to remove hydrogen from your surface, you can have a solution with HCl and a corrosion inhibitor such as Hexamine and a wetting agent like Texapon (or N70 as a gel or viscose liquid). All the materials should be there in the solution.
Regards.
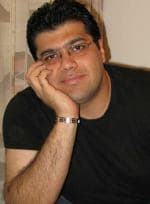
Alireza Reyhan
- Istanbul, Turkey
Q. I AM STARTING THE ZINC NICKEL PLATING, PLEASE HELP ME.
by V Narasimhamurthy
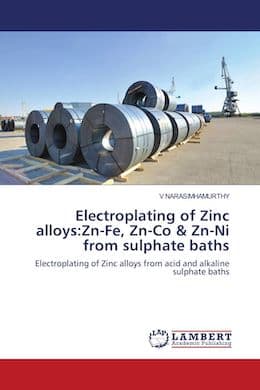
on eBay or Amazon
or AbeBooks
(affil link)
- Punjab, India
January 13, 2017
A. Hi Gagandeep. Everybody would like to help, but there are whole aisles in technical libraries about how to do plating. Please start with a paragraph or two summarizing your situation, and hopefully we can begin a back & forth and make progress. For example, if you are an experienced zinc plater now venturing into zinc nickel, we can probably explain the differences. Thanks!
Luck & Regards,
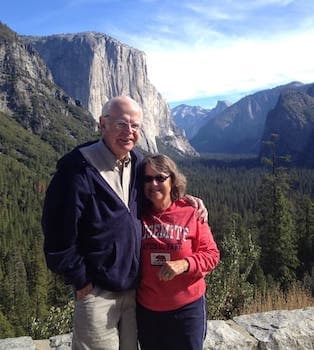
Ted Mooney, P.E. RET
Striving to live Aloha
finishing.com - Pine Beach, New Jersey
Q. Respected sir, I'm running acid zinc nickel plating. All parameters are maintained, but after plating a white salt appears on plated parts both before and after passivation. Please tell me the solution.
Kamaldeep singh- Delhi, India
January 13, 2018
A. Hi Kamaldeep.
Because the problem is visible before passivation, passivation is obviously not what is causing it. It sounds like your rinsing after plating is not adequate.
Luck & Regards,
Ted Mooney, P.E. RET
Striving to live Aloha
finishing.com - Pine Beach, New Jersey
Q. I'm having difficulties of high insertion forces (8-12 kn) of a steel tube into an Aluminum housing. The tube with Zn-Ni plating per Ford standard WSS-M1P87-B4.
Ra =0.9 vs. a normal zinc plating of 0.2.
The tube diameter is 19.03 mm in a machined hole of 18.950 (0.080 mm interference)
A normal Zinc plated tube is inserted with 3kn.
The total thickness of the plating is 0.017 - 0.024 mm.
The inorganic sealant is FINIGARD 200A.
I get values of chemical composition of a 12.4 % nickel concentration in plating.
It looks like it has a Cr 0.06 layer after Zn-Ni..
Bocar - Mexico City, Mexico
February 26, 2018
A. Hello Jaime!
Finigard 200A has an (approximate) friction coefficient of 0,22. This is a little high for this application. Talk to you vendor to use another sealer with a friction coefficient more like 0,12-0,10. I think that with this values you will have a better (and stable) performance in this application.
Best of luck!
TEL - N FERRARIS - Cañuelas, Buenos Aires, Argentina
Q. Sir, we [don't know?] required SST life of (MFZn Ni 1 - B) Zinc Nickel plating salt spray life, like for white rust and red rust, because we have not found HES D2003-03 [Honda Electroplating Standard (for corrosion prevention, rust prevention and decoration)].
Ravinder SinghSHRI PRABHU FASTENERS - Rohtak , Haryana , India
March 3, 2018
A. Hi Ravinder. If you are a Honda supplier, ask for this spec. They should give it to you because they are the only source of up-to-date Honda specs. I don't recall the "B" in Zn-Ni Honda specs, so it may be a new type of topcoat or a typing error.
Best of luck!
TEL - N FERRARIS - Cañuelas, Buenos Aires, Argentina
Black spots on Zn-Ni plated parts from water soluble cutting oil
Q. Issue of black spots on Zn-Ni plated parts when comes in contact with water soluble cutting oil, please guide what is the element which which causes the same from either cutting oil or plating.
Laxman Ramdasi- India
August 20, 2018
A. Hello Mr. Ramdasi,
Some waterborne cutting fluids can be rather caustic. They may contain detergents, and also substances to prevent mould growing. To begin your troubleshooting, you should determine the pH of the fluid in question. That information will give you a clue as to what the reaction could be.
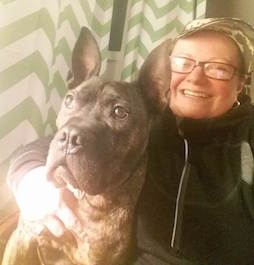
Rachel Mackintosh
lab rat - Greenfield, Vermont
That was a concise and practical answer, Rachel. Should have thought of it myself … maybe I will next time :-)
Regards,
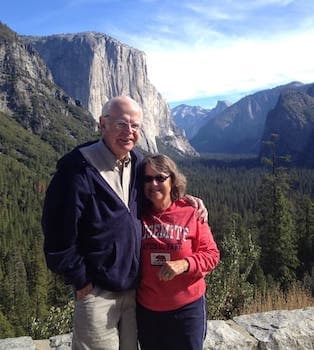
Ted Mooney, P.E. RET
Striving to live Aloha
finishing.com - Pine Beach, New Jersey
There's a first time for everything. Even brevity ;)
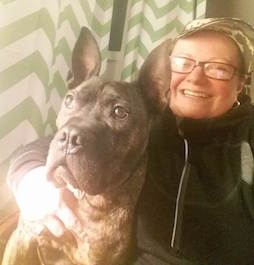
Rachel Mackintosh
lab rat - Greenfield, Vermont
Black patches, pit marks on Zn-Ni plating
Q. Dear all,
we are suffering quality issue black patches, pit mark and rust on Zn-Ni plating.
Due to this issue, we get much more rejects.
Kindly anybody suggest a reworkable method to remove black patches.
So suggest how to remove black patches.
employee - Pune, India
September 4, 2018
A. Hi Mangesh. For some fast ideas, please read this thread which we appended your inquiry to.
To take it further, please give us some data: pictures of the defects, substrate material, barrel vs. rack plating, alkaline vs. acid plating, chromate and sealer details. Is this a problem that just came up or have you been suffering from it for years? One reject per hundred parts or 99?
I'm not sure if we have a language difficulty or if you are actually looking for a salvage method rather than corrective action, so please clarify that point. Thanks.
Regards,
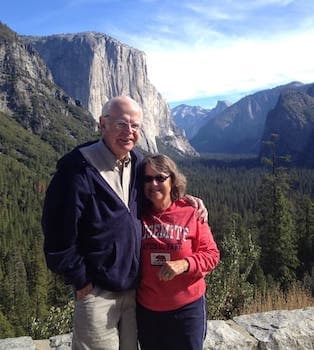
Ted Mooney, P.E. RET
Striving to live Aloha
finishing.com - Pine Beach, New Jersey
Q. Dear sir,
We are facing pit mark , black patches on zn- Ni plating from last couple of months.
Please share with me your experience how to remove black patches from plating permanently.
Until the problem is solved, could you tell me about any rework able method available to remove black patches temporarily because percentage of rejection is 50%
Mangesh Taware [returning]employee - Pune, India
A. for black spots or pits on your alkaline Zn-Ni plated components, your Zn-Ni bath might be low in caustic -- this for me is the most common cause of blackness in the final product. So ensure you do a thorough bath analysis and check your level of Zn and caustic in your zinc nickel bath, then you can add a calculated amount of caustic or zincate concentrate. Also, ensure your pre-treatment process is effective,
I do hope this is helpful
Thanks,
Zik
- Osogbo, Osun State, Nigeria
Thanks Zik.
Regards,
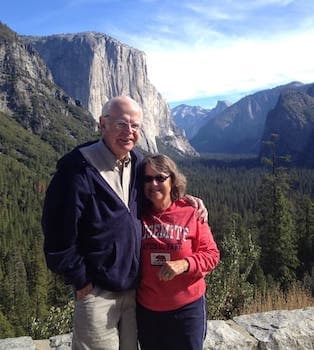
Ted Mooney, P.E. RET
Striving to live Aloha
finishing.com - Pine Beach, New Jersey
Thanks ZIK sir.
After checking all parameters, definitely will come back with you.
- Pune, Maharashtra, India
A. Kindly Check your Pre-treatment -- maybe acid pickle concentration is not in desired range.
Rahul Potphode- Pune, Maharastra, India
Q. I am seeing a similar situation with AISI1008 machined products displaying black spotting quite significantly.
Can anybody comment on whether this would impact on the integrity of the base metal?
- United Kingdom
November 7, 2018
Black spots/patches on Zinc Nickel Plated parts
Q. I am MN from India. One of my suppliers is exporting parts to Europe. These are machined parts made out of 16MnCr5. Zinc Nickel Plating is done on this part. After receipt of parts from Plating, the Machining supplier cleans part with Ultrasonic cleaning process and then dispatches parts to Europe.
When the parts reach by Air or Sea the customer can see black patches and spots on part and if they do SST on these parts white rust is observed within 60 hours.
- Satara, Maharashtra, India
November 15, 2019
A. Hi Mohan. Although there is a lot of discussion about black spots and patches on this thread, it is not clear to me why the 'machining supplier' cleans these plated parts. Are they assembled into something and then the whole assembly cleaned?
It is not a sure thing, but certainly possible, that the ultrasonic cleaning is harming the parts. Zinc nickel plating is invariably chromate conversion coated; the chromate is necessary, and it is certainly possible that an undefined cleaning solution in the ultrasonic cleaner is stripping the chromate. For example, thread 9406 says that you can remove the chromate conversion coating by immersion into alkaline cleaner or by boiling for 15 minutes.
Regards,
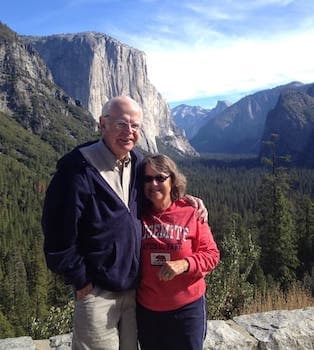
Ted Mooney, P.E. RET
Striving to live Aloha
finishing.com - Pine Beach, New Jersey
Q. There is Millipore requirement, and need to ensure no oil is present during dispatch. Also there is bore area where plating is not done and masking is done during plating other part of flange.
Also there is no 100% rejection. Black Spots are observed on 10% of lot.
- Satara, Maharashtra, India
A. Hi Mohan. Although there is only 10% rejection, you said they get white rust in 60 hours whereas a good chromate conversion coating should deter white rust for 96 hours minimum, and a 192-hour or 256-hour requirement is often expected.
Other readers are welcome to offer their takes, but my first guess remains that the ultrasonic cleaning is harming the chromate conversion coating ... and it should be very easy to test by simply putting some plated parts and some ultrasonic cleaned parts in a salt spray cabinet together and tracking what happens. Good luck.
Regards,
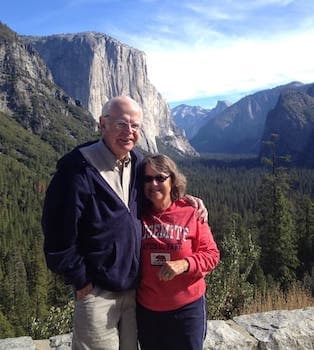
Ted Mooney, P.E. RET
Striving to live Aloha
finishing.com - Pine Beach, New Jersey
A. Hi Mr Mohan,
I don't think your plating guy is doing a very good job with the plating.
Please also check the water quality of the process line.
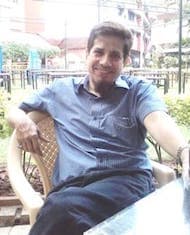
Khozem Vahaanwala
Saify Ind

Bengaluru, India
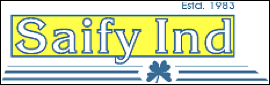
Passivation and polishing of Zinc Nickel plating
Q. I am renovating a MB 170S 1950 and zinc plating many parts like bolts and nuts. I dip the plated parts in nitric acid and finally in clear / blue passivation fluid and the result is satisfactory.
Then I have tried zinc-nickel plating for parts internal in the car that require higher surface finish, and here it is not going so well.
All steps are the same as zinc plating except the electrolyte and the anodes, all other fluids are the same.
1. The zinc-nickel plated part immediately turns black when I dip it in the nitric acid and the same happens if I just dip it in clear / blue passivation liquid. According to the instruction, a strong stream of bubbles should come when you dip it in the nitric acid but it does not happen.
2. It is excellent to polish the plated part and I get it very glossy, the layer of the plating seems to be of good thickness as I do not manage to polish it off and get down to the original material. But what happens to the different layers of surface treatment: am I polishing off the top protective layer and getting less protection?
- Östhammar, Sweden
February 12, 2020
Q. Hello everyone.
As a part of new investment, we started a demo line for our zinc-nickel alloy plating operations to test effects of parameters in a way that represents factual business circumstances.
However, by the end of day one we hit a huge road-bump.
In order to investigate the effect of zinc concentration on throwing speed, we diluted our trial bath to 7 g/L from our regular 8,5 g/L. I expected a significant rise in plating time. That being said our operation times increased more than three times. (1 hr for given thickness in normal operation, more than 3 hrs for demo-bath)
My question is, what am I missing? Did I underestimate Zn concentration's effect? Or Zn ratio started a "domino-effect" on other parameters that I can not observe easily? 7 g/L should still be acceptable but 3 hr for just one rack? It is by no means feasible!
Thanks in advance.
Platech Metal Plating Technology - Sakarya, Turkey
February 25, 2020
A.
Hi Serhat!
Did you dilute all the bath or only zinc content? Did you use the same water you use in the process or distilled water? Is it alkaline or acid zinc-nickel?
Zinc content of 7 g/l for an alkaline bath isn't a problem, you get more plating time but not triple. You should see if anything is off parameters in this "dilution". High nickel content (in relation with zinc) decreases your throwing power, too, so as a complex bath as it is, you need to watch all the parameters at once and not one to one.
Help me with the other data and we can solve this mystery!
Regards,
N. Ferraris S.A. - CaƱuelas, Buenos Aires, Argentina
![]() |
A. Hi, - New Delhi, India A. Hi. Asahi Aero Malaysia Sdn Bhd - Selangor, Malaysia |
Q. Hello team,
We are facing repetitive zinc nickel plating peel off issue from our customer during crimping process.
Requirement of Plating thickness is min 8 microns & nickel content is 12-16%.
Plating supplier claims plating thickness can't be maintained evenly on surface.
Base material is VS13111.
Regards,
Quality Assurance - Bangalore, Karnataka, India
March 17, 2020
Hi Raja. I give up :-)
Google finds me no pages with that spec number or alloy. Please tell us whose spec it is or exactly what the substrate is. Thanks.
Regards,
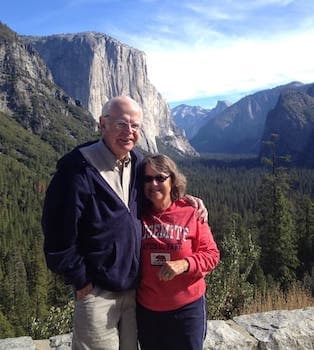
Ted Mooney, P.E. RET
Striving to live Aloha
finishing.com - Pine Beach, New Jersey
Q. Good day
I have some question about iron contamination in acid zinc nickel plating tank.
I suspect iron; I measured by colorimetric method and it's around 130 ppm.
what it's the best method to remove the iron from the solution, I Heard about the dummy plate with 90° cathodes and LCD and another says that use hydrogen peroxide.
Any in this forum have experience in that?
Thanks for your support.
- Querétaro, Mexico
December 11, 2020
Q. We have manufactured M6 screws and done zinc nickel alkaline based plating with 8 micron thickness and 85 / 15% composition with top coat. We have found 1000 Hrs SST in lab. We have packed screws in card board box and sent to customer but red rust found on screws as soon as it reached to customer in 14 days.
Please advice us how we can improve so that red rust should not appear. Please try to help us. Waiting for your advice
Amit & C.SamaniManufacturer of fasteners - Mumbai, India
September 23, 2021
A. Hi. If parts last 1000 hours (42 days) in an accelerated corrosion test, but the same parts don't survive 14 days when packed in boxes and shipped to your customer, it sounds like there are three possibilities:
1. The salt spray test results are extremely suspect, or
2. The parts were not dry when packed, or
3. Your cardboard boxes are high in sulfides or other materials that are causing rapid corrosion, or something about the transit conditions is extreme (tremendous vibration causing fretting of the coating, bold corrosive conditions in transit).
Take a few sample pieces and make sure they are absolutely dry, and seal them in polythene bags before throwing them in the carton with the other parts and see what your customer tells you about them. And leave one of those cardboard boxes on your own loading deck for the 14 days. This should not be hard to solve.
Luck & Regards,
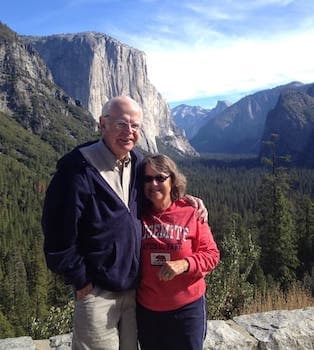
Ted Mooney, P.E. RET
Striving to live Aloha
finishing.com - Pine Beach, New Jersey
Q. Hello,
I have a problem with bolt (stick 110 length, 10 diameter, threads at each end). These bolts are hardened. I rack plate them. Surface treatment is Zn alloy (ZnNi). Sometimes I have a problem with black spots- diameter more than 5 to 5 mm (see photo). There is no thickness in black spots.
Stanislav Strmiska
- Czech Republic
February 17, 2022
A. Hi Stanislav. I'd vapor degrease a few if that is available to you, or otherwise let a few sit in the soak clean tank for an hour before continuing the processing and see what happens. I'd also scrub a few with pumice. It doesn't look to me like a problem that would develop in the plating tank, but earlier in the cycle.
Luck & Regards,
Ted Mooney, P.E. RET
Striving to live Aloha
finishing.com - Pine Beach, New Jersey
A. Hi Stanislav,
I don't have much experience with rack plating, but I do have some with hardened bolts and Zn-Ni plating. Do you use alkaline Zn-Ni? If you do, I suggest you make a flash plate in an acid plating (zinc or zinc-nickel if you can), bake for hydrogen embrittlement, and Zn-Ni plate after activating in caustic soda ⇦liquid caustic soda in bulk on
Amazon [affil link]
the previous plate. This is how we do if our customer allows us. If not, you only can put the parts in the plating tank and make an extended cycle, of 3 or 4 times the standard plating time, to make all the parts plate.
Hardened bolts make it difficult for alkaline baths. Additives to make hydrogen overpotential rise don't work and almost all the electrons go to hydrogen making on the surface of the parts you plate. So, thickness is very low and not even.
If you are making this with an acid plating process (doesn't seem the case because of the low brightness of the passivated parts), you REALLY should improve the previous cleaning as Ted mentioned.
Best wishes,
Daniel
Daniel Montañés
Process Engineering Manager - Cañuelas, Buenos
Q. I am facing line marks which is like minor burning on Zn-Ni plating which gets reduced by reducing the amps.
Can anyone suggest the causes?
Sathish kumar k- Chennai, Tamil Nadu, India
March 18, 2022
A. Hi. That doesn't look to me like a high current density area unless the parts are racked horizontally with that end facing the anodes.
How are the parts hung on the racks? Is the end with the line marks at the top when they are racked?
Luck & Regards,
Ted Mooney, P.E. RET
Striving to live Aloha
finishing.com - Pine Beach, New Jersey
Q. This is the position of part in rack line and I am facing issue issue in top and bottom of part.
- Chennai, Tamil Nadu, India
? Hi again. Maybe another reader will have a possible cause -- I don't see one. Any chance that those ends look suspicious before plating?
Luck & Regards,
Ted Mooney, P.E. RET
Striving to live Aloha
finishing.com - Pine Beach, New Jersey
Q. Hello everyone,
My name is Lamberto Carlini and I work in a galvanic for surface treatments in the aeronautical sector.
We are experiencing a problem in our Zinc Nickel process concerning the electrical contact points, I am attaching some photos. When checking the black areas with XRF, we find 0 deposit and a very high percentage of Ni (even >80%). I think the problem is related to the conductivity of the contact point.
Each charge we proceed with a stripping of the equipment in 15% hydrochloric acid and Ni remover.
The preparation cycle involves electrolytic degreasing, hydrochloric acid pickling, in the case of CRES parts we perform a strike of Ni, alkaline Zinc Nickel Zn about 8 g/l, Ni about 0.9 g/l, NaOH about 120 g/l.
The problem seems to be related to the stripping of plastic-coated stainless steel equipment, but any suggestions are welcome if anyone has different experiences, including different solutions for stripping.
Thank you
- Foligno, Umbria, Italia
January 18, 2023
? Wow! I've never seen such dramatic rack marks. I have no clue and am hoping to learn something from our readers.
Luck & Regards,
Ted Mooney, P.E. RET
Striving to live Aloha
finishing.com - Pine Beach, New Jersey
A. Hi Lamberto
1. Nice photos
2. It looks that many parts on the rack may require significant current. Sharp stainless steel tips of the rack are not good electrical contacts. Is there any chance that those tip-contacts just overheating (and it affects the plating conditions around them)?
Just my guess...
Good luck
- Winnipeg, CANADA
Good morning, after a few attempts we solved the problem by increasing the current density from 0.8 A / dmq to 1.1 A / dmq, the contact points did not give more problems. Thank you
- Foligno, Umbria, Italia
A. Hi Lamberto
1. Nice photos
2. It looks that many parts on the rack may require significant current. Sharp stainless steel tips of the rack are not good electrical contacts. Is there any chance that those tip-contacts just overheating (and it affects the plating conditions around them)?
Just my guess...
Good luck
- Winnipeg, CANADA
Hmm,
Alloy plating is always tricky, with one or both metals requiring complexing in order to allow deposition of both, and requiring that pretty rigid parameters be enforced. Somewhat counterintuitively, the contact points are the lowest current density spot on the part; still, the black deposits at the contact point when current is too low are quite surprising -- so thanks for sharing!
Luck & Regards,
Ted Mooney, P.E. RET
Striving to live Aloha
finishing.com - Pine Beach, New Jersey
Q. I have an issue with the Zn-Ni coating on the padbolts I am buying in. The spec calls for 8-14 micron of 12%-16% Ni, and I am getting 1 micron in some regions.
The padbolts are plated assembled and the low coating areas are behind the bolt on the plate. The bolt is about 8mm (5/16") in diameter and has about 2.5mm (3/32") of play above the plate.
I was wanting to know 2 things:
-What degree of reduction in thickness of coating could be expected? Is this a reasonable loss of coating thickness?
-To those coaters who have coated padbolts, were they generally assembled or assembled after coating?
For context, the reason they are coated assembled is to ensure the sizeable pinch would be protected.
- Ballarat, Australia
October 13, 2023

Q, A, or Comment on THIS thread -or- Start a NEW Thread