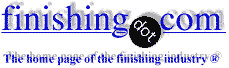
-----
Electroplating with copper sulphate for science project
Q. I am an IB student struggling to provide a satisfactory explanation for the results of my IA experiment.
In the experiment, I aimed to explore how changes in electrolyte concentration would affect the electroplating rate. I electroplated copper on copper using copper sulfate (CuSO4)
⇦ on
eBay or
Amazon [affil link] as an electrolyte with concentrations of 0.2, 0.4, 0.6, 0.8, 1.0, 1.2 M. I measured the mass of the cathode before and after electroplating with 0.6A DC current and 5V for 5 minutes. The mass change average from 8 trials were around 0.02g for the 0.2M, increasing almost linearly to 0.05g at 1.0 M, but then decreasing significantly to 0.03g at 1.2M. i also did a few test trails for 1.4 M, and electroplating barely happened.
I used 2.5*5 cm 99% pure copper strips for both the cathode and anode (the type labs provide for electrolytic cell experiments), and the CuSO4 was dissolved in distilled water.
The anode became steadily smaller as the reaction progressed, but some of it turned yellow, green, or black, with some crystal-like patterns appearing on the strip after electroplating. I suspect this is because of impurities, but apparently, only Cu(CN)2 and Cu(Hg(SCN)4) have this color. I do not know where these impurities may have come from.
Theoretically, according to Faraday's law, the changes in concentration should not affect the rate of electrolysis, but this experiment demonstrated otherwise. Is there any possible explanation for this deviation, and the change of trends at 1.0M? Could this be due to a difference in conductivity of the solution? then why does the rate decrease at 1.2M?
Thank you so much!
PS: this is a quite urgent situation, every idea helps even if it may not be completely correct (these ideas show reflection and they can earn me points).
Student - California
December 24, 2023
A. Hi Tiffany,
I would suggest rechecking the voltage and current because A = V / R and you should not be able to hold both the current and the voltage constant with solutions of varying conductivity unless you are introducing another variable.
Your voltage is high for a beaker [beakers on
eBay
or
Amazon [affil link] plating experiment.
The "efficiency" of acid copper sulphate plating should be close to 100% at reasonable currents and voltages. But there should be sulfuric acid in the solution for proper plating (maybe that's not allowed in school).
What may be happening is that you are plating at a faster rate than the low concentration solutions can handle, so most of your Faraday's Law current is going to the liberation of hydrogen rather than the deposition of copper, and as you increase the concentration you are moving towards a more reasonable plating rate, and plating more while generating less hydrogen gas (you should be able to see the bubbles if you're generating lots of it).
As for the lower deposition rate at higher concentration it may well be "anode polarization" -- what happens in this case is the copper sulphate concentration gets too high very close to the anode and it interferes with normal ion transport and conductivity.
Luck & Regards,
Ted Mooney, P.E. RET
Striving to live Aloha
(Ted is available for instant or longterm help)
finishing.com - Pine Beach, New Jersey
Q. Thank you so much for your answer!
Here are some follow-ups.
I actually only controlled the current (for easier calculations). I used a device called a Vernier constant current system
⇦ on
eBay], and I turned the current up to the highest at 0.6A. The device says that the voltage should be around 5V, although I did not measure it. I understand that the voltage may fluctuate a little.
Just wondering, what is the ideal voltage if I am using a 250 ml solution in a beaker [beakers on
eBay
or
Amazon [affil link] to electroplate? And how does a high voltage affect the electroplating rate?
Also, there were no observable air bubbles coming from either the cathode nor anode :(, unfortunately. I sanded the copper and immersed it in 5% acetic acid for 30 seconds to remove copper oxides before drying it and using the copper strip as the cathode. I also used a copper wire to hold the cathode and make it fully immersed in the solution, might this have affected the results?
Thank you so much!
- California
December 26, 2023
A. Hi again. Based on your questions, here is what I'd like you to think about --
Current (amperage) is actually the measure of how many electrons you are pumping through your power supply and copper wiring per unit of time. One way of viewing Faraday's Law is that each of those electrons you are pumping must be matched by an atom getting stripped of its electrons, migrating through the solution over to the cathode, and recapturing its electrons. So for each two electrons you move, you reduce one atom of Copper on the anode to a Cu++ ion, it migrates to the cathode, re-captures those two electrons and becomes an atom of copper on the cathode.
So, if you hold the current and time constant, the amount of copper you deposit should remain constant regardless of concentration, voltage, temperature, or anything else ... EXCEPT ... Faraday's Law doesn't actually say how much copper must deposit, it says how much ionic transfer must occur. Any difference is accounted for by some other ionic activity, and the one that matters in electroplating is the liberation of hydrogen gas from water. If there are not sufficient Cu++ ions at the cathode to accept all the electrons you are pumping there, what will happen is that water will split into hydrogen gas and hydroxide ions to make up the deficit:
2 H2O + 2e- ⇨ H2(gas) + 2 OH-
i.e., 2 'excess' electrons will split two molecules of water into one atom of hydrogen gas and two ions of hydroxide.
Usually, operating under proper conditions, copper plating is nearly 100% efficient (nearly 100% of the electricity deposits copper, and very little is 'wasted' generating hydrogen gas. But under poor deposition conditions, a significant amount can be wasted, and your experiment seems to be doing that: demonstrating the waste or inefficiency.
The above should make you realize that voltage is not actually a control factor here. What an electroplater actually tries to do is to keep the current low enough that s/he gets essentially 100% efficiency. What I can tell you about your voltage is that 5 v is higher than appropriate for a 250 ml beaker. Even at 1-1/2 volts I think you generate significant hydrogen. My guess is that your Vernier power supply
⇦ on
eBay] is only putting out something like 2 volts to maintain the 0.6A.
(affil links)
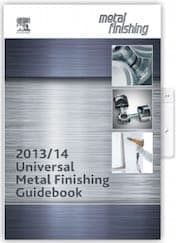
free pdf is currently available from academia.edu
The Metal Finishing Guidebook is available on line for free and has a subchapter on copper sulphate plating baths, as well as all sorts of charts you will find helpful. Congratulations on doing the experiment right -- recording your results then trying to understand them. Many students try to understand what they ought to obtain first, which invariably convinces them to perform junk science, talking themselves into discounting their results or altering them to get the results they were "supposed to get" :-)
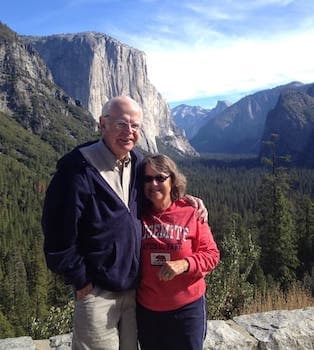
Ted Mooney, P.E. RET
Striving to live Aloha
(Ted is available for instant or longterm help)
finishing.com - Pine Beach, New Jersey
Q. Sorry, I forgot to mention that I did not put H2SO4 into the copper sulfate, would this have limited the conductivity of the solution and thus affected the electroplating rate? Because the conductivity of CuSO4 does increase with concentration, which corresponds with the increase in electroplating rate.
Also, the copper that I plated out had a matte surface with a pinkish color. It turns to the normal red-brown copper color after I sand it. Is this normal?
Thank you so much!
- California
December 26, 2023
Regards,
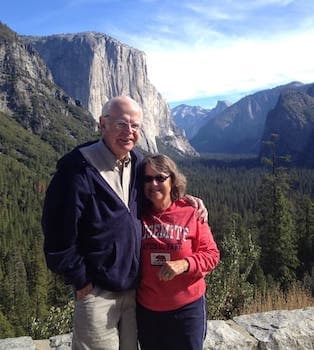
Ted Mooney, P.E. RET
Striving to live Aloha
(Ted is available for instant or longterm help)
finishing.com - Pine Beach, New Jersey
Q. Hello,
I am doing the exact same experiment for my IB chem IA (how concentration affects copper plating mass) and had a question that is not necessarily related to the outlier in the data, but more for my background as I make final touches. I am not 100% sure what the half reactions occurring are, because every source says something different and my teacher wasn't totally sure either. I am using a copper strip for the anode and a graphite rod as the cathode.
I know reduction would be Cu2+ + 2e- --> Cu, but is oxidation the reverse of that as solid copper from the anode replenishes the ions, or would it be the oxidation of sulfate in the CuSO4 solution? I was confused by this because I thought sulfate couldn't oxidize, but this is the second half reaction my teacher was suggesting.
Unfortunately I'm in a similar situation to Tiffany in that I need to turn this document in as soon as possible so any help is greatly appreciated!!
- Virginia
February 24, 2024
A. Hi Colleen,
It's unfortunate that students do this particular experiment -- correlating copper deposition quantity to copper concentration -- because there is actually no dependable relationship :-(
Demonstrating the truth of Faraday's Law would probably be a better experiment.
But yes, the main half call reaction at the cathode is reduction per your equation. The undesired half-cell reaction which occurs to a more limited extent is 2H2O + 2e- --> H2^ + 20H-
And the main half cell reaction at the anode is the reverse, i.e., Cu - 2e- --> Cu2+. The undesired half-cell reaction which occurs to a more limited extent is 2H20 - 4e- --> 02^ + 4H+
Luck & Regards,
Ted Mooney, P.E. RET
Striving to live Aloha
(Ted is available for instant or longterm help)
finishing.com - Pine Beach, New Jersey
⇩ Related postings, oldest first ⇩
Q. Hello,
I am a freshman student in an honors chemistry class. I have conducted an electroplating experiment that tested the effect of different amounts of copper sulphate ⇦ on eBay or Amazon [affil link] in the bath(g) on the change in mass of a nickel from before it was plated to after it was plated with copper. I had 100 trials total. The four amounts of copper sulphate tested were 5 g, 10 g, 15 g, and 20 g dissolved in 150 mL of water. From the results I gathered my data showed that there is virtually no difference in how much copper was plated on the nickel despite the different amounts that were used. I am now writing my lab report and my teacher wants me to find out why there was no difference between in the change of the mass of the nickels. My experiment obviously showed that the amount of copper sulphate in the plating bath has no effect on how much the nickel is plated but I really need to know why.
I am sorry if this is a stupid question, but I am not very familiar with this site and do not know if it has already been answered elsewhere, and I don't have a lot of time. I appreciate any help you can give me. Thank you and please respond as soon as you can.
Melissa A [last name deleted for privacy by Editor]student - Columbia, Missouri, United States
2004
A. Not a stupid question at all, Melissa. You are very industrious to plate 100 samples, good for you, and your results are exactly correct! Here is what happens--
The copper ions are sitting in solution, doing essentially nothing until you apply electricity. Then, when you apply electricity and a copper ion is touching your nickel cathode, two electrons flow into it reducing it from a Cu++ ion to a Cu0 metal atom. So the amount of copper deposited is proportional to the number of electrons that flowed, i.e., the coulombs or ampere-seconds, NOT the copper concentration. This is Faraday's Law, and we're very happy you demonstrated it so well.
There is, however, a second reaction that occurs to a much lesser degree. Those two electrons can sometimes instead be wasted in the liberation of hydrogen from water,
2H2O + 2e- => H2 + 2OH-.
If 100 percent of your electricity goes into depositing copper, the process is said to be operating at 100 percent efficiency. If 10 percent of the electricity goes into liberating hydrogen from water, the process is operating at 90 percent efficiency. At high copper concentrations and reasonable current, like you used, copper plating is close to 100 percent efficient because it is much easier to reduce copper than hydrogen; but if you lower the copper concentration way down, the efficiency will drop off. You can understand this by remembering that I started by saying "a copper ion is touching your nickel cathode". Suppose that the concentration is so low that at a given instant no copper ions are near or touching the cathode? The electricity still needs to flow, and will do so by liberating hydrogen from the water.
You did a great experiment and demonstrated Faraday's Law -- with the great 'control' of showing that copper concentration within reasonable limits has no effect on plating rate! (but had you run another trial with a greatly reduced copper concentration, you might have seen the reduced efficiency that results from too little copper in solution).
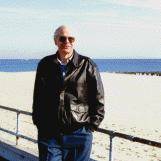
Ted Mooney, P.E.
Striving to live Aloha
(Ted is available for instant or longterm help)
finishing.com - Pine Beach, New Jersey
Q. I am helping my 7th grade child with a science project that involves ECD of copper using different concentrations of copper sulphate solution. At higher concentrations it went pretty well and he observed nicely deposited copper formations. At successively lower concentrations there seemed to be increased bubbling (presumably electrolysis of water?) but also the deposits were black. Is this an optical property of the deposited copper, CuO or something else?
Thanks,
Dan
hobbyist - Northport, New York, US
February 1, 2009
A. Hi, Dan. The black deposit you are seeing is called "burning" or "smut", and I can tell you basically what it is, but it's hard to put a fine point on it in terms of percentages, because it is the result of a process that is out of control and therefore erratic and unpredictable. One component of it is a very finely deposited copper powder (if powders are fine enough they tend to look black because the tiny balls bounce light away at skew angles instead of reflecting it back.
It is caused, as previously mentioned, by trying to plate at a higher current than the solution can sustain. The electricity must take two paths to complete the circuit, electrons flow through the copper wire, while positively charged copper ions flow through the solution. If there isn't enough copper in the solution to sustain the current you are passing through the wire, the instant a copper ion reaches the cathode it is instantly reduced to a spec of powder instead of slowly growing a proper grain structure. Additionally, water is hydrolyzed into hydrogen and oxygen to try to carry the current.
It is possible to successfully plate copper with a low concentration of copper in the solution, but you must plate at a very low voltage and consequently slower so the small concentration of copper ions is sufficient to match the electrons you are passing through the wire. Good luck.
Regards,
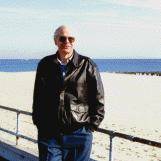
Ted Mooney, P.E.
Striving to live Aloha
(Ted is available for instant or longterm help)
finishing.com - Pine Beach, New Jersey
Q. My name is Aditi and I'm doing a chemistry project on Electrolysis. I'm in the ninth grade. I'm plating a steel rod with copper from a CuSO4 solution. I want to know what reactions take place and whether the SO4 ions will rush to the other electrode.
Aditi L.Student - Pune, Maharashtra, India
March 16, 2010
A. Hi Aditi. Sorry, but your experiment will not be successful because electroplating copper onto a steel rod is a problem. Copper is more noble than steel, so copper will deposit onto the rod without any electricity applied. As for the reaction involved, the copper sulphate ionizes into Cu++ and SO4- -, and the Cu++ ions migrate over to the steel surface. When they reach it, they "steal" electrons from the steel because they are more noble than the steel is. Thus the copper ions become neutralized and deposit as copper metal onto the rod, while simultaneously the iron (steel) atoms lose their electrons and ionize into solution. When the steel surface is completely covered with copper metal, the reaction will stop.
However, if you apply electricity at that point, you can make it continue. You'll pump electrons to the cathode, where they will continue to reduce Cu++ ions to copper metal, and the electrons you pulled from the anode will cause the copper atoms of the anode to dissolve into solution as Cu++ ions.
Regards,
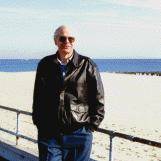
Ted Mooney, P.E.
Striving to live Aloha
(Ted is available for instant or longterm help)
finishing.com - Pine Beach, New Jersey
Need very heavy copper plating on top of nickel plating
Q. Dear sir. I run a small electronics company (mostly power electronics) and we need to have a thick copper plate applied to a nickel plated spring clip and a nickel (or gold) plated magnet. The cladding must be a minimum of .32mm but we prefer .4mm [ed note: 0.016"] thick. I have contacted every plater in the country (Guatemala) -- they do not "experiment" so we are on our own.
Our need is estimated to be 2000 clips and 1500 magnets per year. Also we are somewhat space limited -- a process that requires ten different baths even if it is less costly would not be as suitable as one that requires less space but is more costly. Any suggestions or advice would be greatly appreciated.
Sincerely ,
Field Effect Transistor Co. - Teculutan , Zacapa , Guatemala
January 10, 2019
Ed. note: This RFQ is outdated, but technical replies are welcome, and readers are encouraged to post their own RFQs. But no public commercial suggestions please ( huh? why?).
A. Hi Robert. 3500 parts per year is only 15-20 per working day, so your production needs are not far beyond an experimental laboratory. But the only practical way to get the copper on them is probably electroplating, and these thicknesses are in the range of usual electroforming thicknesses and will likely require a plating time of almost a full day.
Before plating, the parts will require electrocleaning, rinsing, acid dip neutralization, rinsing, Wood's Nickel Striking, and rinsing before the copper plating. A possible alternative for less space is sandblasting followed by rinsing and Woods's Nickel Striking.
The plating is thick enough that maybe, depending on the shape of the parts, you can rely on a shrink-wrap cohesion effect more than adhesion to keep the copper attached to the parts. So maybe you can just sandblast the parts, rinse off the dust, and quickly start copper plating without the strike. (Must the nickel plating be retained?)
Years ago I was involved with the re-plating of the ironwork of Philadelphia city hall's William Penn clock tower; the original plating (acid copper plating directly onto iron & steel) was in the same general thickness range as you are contemplating and worked for many decades ... but once it became perforated there was rapid horrible undercutting corrosion because there was zero adhesion.
Regards,
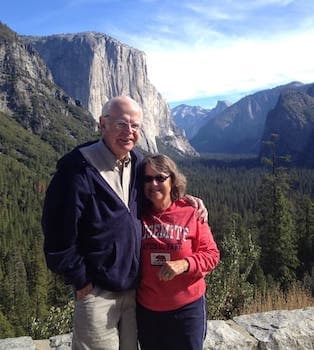
Ted Mooney, P.E. RET
Striving to live Aloha
(Ted is available for instant or longterm help)
finishing.com - Pine Beach, New Jersey
Q. Thank you mister Mooney for your advice ... it sounds like it is doable. You asked if the nickel is necessary -- no, I just mentioned it because it was there, but I believe good adhesion is necessary because of flexing and the high amps that will be passing through the part.
I do have a few follow up questions if you don't mind --
1. in this application sand blasting is unacceptable due to the stress risers it would leave (it is a spring) but we have bead blasting, hot caustic soda bath ⇦liquid caustic soda in bulk on
Amazon [affil link]
, hot ferric chloride
⇦ on
eBay or
Amazon [affil link] bath (with or without 5% nitric acid ) would any of these do what the sand blasting was intended to do?
2. after the Wood's Nickel Strike you say to copper plate , but a quick search of the internet turns up at least a dozen different copper plating methods, does it matter which one I choose? (many chemicals are not available here , for example we make our own ferric chloride, so having several choices is a good thing from a chemical availability aspect).
Thank you in Advance.
Sincerely,
Field Effect Transistor Co. - Teculutan Zacapa Guatemala
A. Hi again Robert. If at all possible you should be buying your plating solutions from a reputable plating process provider. If that is impossible, then you need to at least build a good plating library so you can research the matter.
Old nickel plating is difficult to activate for good adhesion even with a Wood's Nickel Strike. And chemically removing it without proprietaries or creating an environmental mess with nitric acid is difficult; blasting is better. Personally I would guess the best procedure for good adhesion on springs with old nickel plating would be to blast the old nickel off, then either nickel strike or cyanide copper strike, then acid copper plate.
But you don't build a plating plant based on theory. You need to try these things before you build a plant to do them.
Regards,
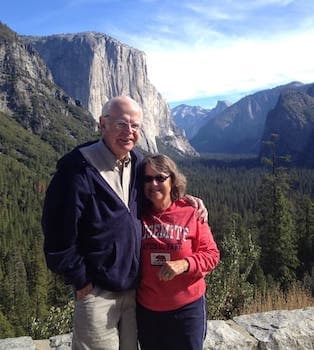
Ted Mooney, P.E. RET
Striving to live Aloha
(Ted is available for instant or longterm help)
finishing.com - Pine Beach, New Jersey
Q. Hi - for a 6th grade science experiment we are copper plating US 5 cent (Nickel) coins in a 500 CuSO4 solution with 9v battery and increasing amounts of sulfuric acid - the problem is our weighing scale has a d=0.1 g and we are not seeing any more than 0.1 grams or at best 0.2 g for the highest acid levels - but we can clearly see that the Copper is pushed onto the coin and the alligator clip - are we saturating the coin ? Does copper deposit stop after the first level of coating? How can we show the gradients of acidity vs Copper deposited if we are "over plating"?
Anand VenugopalStudent - San Jose, California
January 5, 2020
"Hands-on" learning is fun, maybe try a ...
Precision Electronic Scale
on
eBay
or
Amazon
(affil link)
A. Hi Anand. Sorry to have to say this but, unfortunately, your experiment is a poor one. First, the variable that you are varying (acid concentration) is far removed from the heart of the matter of what electroplating is really about as a science. Secondly your constants (like 9V battery) are poorly chosen (9V is WAY too much; 3 V is more than enough, probably too much). Thirdly, a scale which is incapable of measuring what you are need to measure really isn't much use. Apologies :-(
Please see our paper "Faraday's Law of Electrolysis for Plating" which explains what the science of electroplating is really about. If you read and understand it, I think you will immediately rethink your experiment and figure out a better way to structure it. Good luck.
Regards,
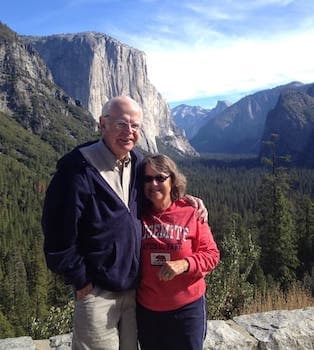
Ted Mooney, P.E. RET
Striving to live Aloha
(Ted is available for instant or longterm help)
finishing.com - Pine Beach, New Jersey
Q. Hello,
My son wants to validate the atomic mass unit of copper through a copper electroplating experiment. Passing a known amount of current for a given time (ampere-seconds) and measuring the mass of copper deposited, and then using the principle behind Faraday's law, he wants to calculate what he finds the atomic mass unit of copper to be :-) experimentally and check whether it is indeed 63.5. He is estimating that if he can get 3 gms of copper deposited through passing a current of 1.25 Amps for 6 hours (using a low-cost DC power supply), he may be able to get some calculations he can work with. We already have a scale that can measure to 0.01g so he may plan to do 2-3 trials.
I am writing to you since it is unclear how much electrolyte he should use and what would be best way for him to measure the amount of copper deposited. He was planning to use an iron electrode (4 inch long bar, 12g) and a copper electrode (4 inch long bar, 12 g) from a science experiment tools store.
Thank you in advance for your guidance!
Kiran
- San Jose, California
December 2, 2020
A. Hi Kiran, that's an ambitious science project! I didn't carefully check your numbers, but they look about 2X too high. Remember that in acid copper sulphate, the oxidation state/valence of the copper is +2, which means you need to move 2 electrons through the power supply and wiring, not 1, for each ion of copper you want to transfer from anode to cathode through the solution.
But don't use an iron cathode because copper, being more noble than iron, will spontaneously deposit a thin layer on it without electricity, slightly changing the data. I would suggest just using two copper electrodes and carefully measuring the weight of both, and the weight of the solution before and after the experiment (if the solution & beaker aren't too heavy for your scale), which will offer checks and balances against measurement errors. In the unlikely event that the total of the three changes, he'll have another thing to consider & report -- that some of the weight might have evaporated as water or turned to hydrogen and floated off :-)
I don't know the surface area of those 4 inch long bars, and you probably only want to submerge 3 to 3-1/2 inches in the solution, because you won't want the connection submerged in the solution and possibly corrupting the situation. But I wouldn't suggest trying to plate at more than about 10 amps/square foot maximum, so I think the 1.25 Amps is probably high. Shooting for less copper deposited or plating for 12 or 24 hours might be better.
A beaker [beakers on eBay or Amazon [affil link] of 300-500 mL would be ideal because he can also record and track the solution level, to see if some was lost to evaporation or hydrogen. I'd get the beaker first and see how much solution corresponds to a 3 to 3-1/2" level (but obviously less than 300-500 mL).
With the before & after weight of the anode, the before & after weight of the cathode, the before & after weight of the solution, the ampere-hours of electricity, and the before & after solution level he should have outstanding data for his terrific experiment.
Luck & Regards,
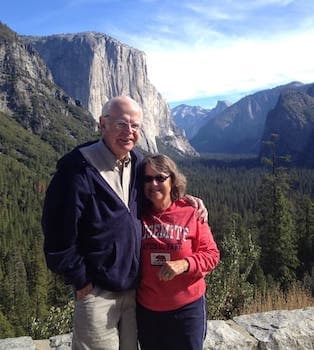
Ted Mooney, P.E. RET
Striving to live Aloha
(Ted is available for instant or longterm help)
finishing.com - Pine Beach, New Jersey
Q. Hello, Mr. Mooney,
Thank you so much for your terrific guidance on my son's project. He is very grateful. I have ordered the DC supply, glass beaker set [beakers on
eBay
or
Amazon [affil link] with various sizes, and copper electrodes for him. I have a few follow-up questions.
1. For making the electrolyte, is it ok to buy copper sulphate
⇦ on
eBay or
Amazon [affil link] crystals or powder and mixing with water? or is it better to buy pre-made copper sulphate electrolyte. If it is the former, then how many gms would be best to order.
2. Based on 10 amps/sq.foot recommendation, my son converted this guidance to amp/sq.inch and for plating both sides of roughly 3 sq.inch of his electrode, he is thinking 0.5 Amps. He will run this for a longer time (12 hours). I got him a couple extra electrodes in case his first run doesn't work out ;-)
3. Can you pls validate if our understanding of the scientific principle is correct: When electricity is passed, the copper cations Cu2+ from the copper sulphate solution will go to the copper cathode and deposit as metallic copper, while the sulphate anions (SO4) 2- will go to copper anode and combine with the copper and leach out more CuSO4 back into the electrolyte (replenishing the copper ions). This process keeps going on as electricity is passed. We will lose some electrolyte as you mentioned to evaporation. Is our understanding correct?
4. So for his calculations: the total mass of copper deposited will be increase in weight of the copper cathode. I'm wondering how does the decrease in weight of copper anode and any changes to the electrolyte factor in his calculations for mass of copper deposited.
Thank you so very much for your continued guidance!
- San Jose California
A. Hi again Kiran. I have never actually done the experiment, but:
1. When people talk about buying or using copper sulphate, they usually actually mean copper sulphate pentahydrate, CuSO4·5H20. This is the blue crystals or powders you generally see. It is quite soluble, so he should be able to readily dissolve it in water. The advantage of using crystals or powder over buying a liquid is that you'll know how much actual copper sulphate you have, whereas if you buy a liquid then you'll have to trust the percentage from the label to know how much copper sulphate you have versus water.
A standard copper plating bath is about 210 grams per liter but you can operate at much lower concentration, and you may not be able to dissolve quite that much anyway, so buying 100 grams for a 300-500 mL beaker should be more than enough. You're also supposed to have about 30 grams per liter of sulfuric acid in your plating bath, but you didn't tell us how old your son is so I don't know if that's appropriate. You may want to just use vinegar
⇦in bulk on
eBay
or
Amazon [affil link] instead. In that case, I'd probably use about 1 part vinegar to 4 parts water (200 grams per liter).
2. 0.5 Amp sounds okay to me.
3. Your understanding is correct, but you don't really even have to worry about the sulphate to understand it: when your power supply strips two electrons from the anode and pushes them through the copper wiring to the cathode, what used to be an atom of Cu0 on the anode has now been turned into a Cu+2 ion in solution. It will migrate over to the cathode where it re-meets those 2 electrons and becomes an atom of copper again.
4. The anode weight and solution weight don't factor into his calculation for the weight gain at the cathode; that's a free-standing measurement; sorry for confusing/misleading you ...
But, just as one atom of copper should deposit on the cathode for each 2 electrons transferred, one atom of copper should be removed from the anode. So the weight loss from the anode should match the weight gain on the cathode -- just a built-in check.
My suggestion about weighing the solution and watching for evaporation was probably overkill, I only mentioned it because if the weight gain of the cathode doesn't match the weight loss from the anode, the only explanation is that there is either more or less copper dissolved in the solution at the end of the test than at the beginning; probably just skip that and weigh the anode and cathode before and after rather than going nuts with data :-)
Luck & Regards,
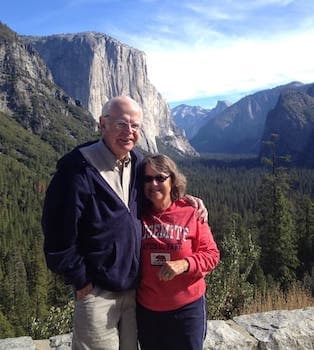
Ted Mooney, P.E. RET
Striving to live Aloha
(Ted is available for instant or longterm help)
finishing.com - Pine Beach, New Jersey
A. Please do not forget the 2 most important ingredients of the experiment: safety glasses ⇦ on eBay or Amazon [affil link] and gloves ⇦ on eBay or Amazon [affil link] .
Leon Gusak- Winnipeg, Canada
Thank you Mr. Mooney so very much for such detailed guidance!
I think my son now has ample clarity to embark on his experiment.
Per Leon's advice, I will be sure to ensure he keeps his safety gloves and glasses at all times ;-)
- San Jose, California
Q, A, or Comment on THIS thread -or- Start a NEW Thread