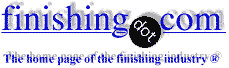
-----
Alkaline zinc plating speed (allowable current density)

Q. Need to formula for 1 micron thickness increase.
Then carbonate increased in plating bath any issue came from part thickness or other parameters.
Which type of parameters involved to improve thickness.
Qualit - Chennai
October 13, 2023
A. Hi SATHYARAJ. More words please :-)
Your posting has a few typos which I don't know how to correct because there is not enough context. But it sounds like you are presently doing zinc plating and you want to increase its thickness by 1µ
Zinc plating can range from 5µ to 25µ in thickness per ASTM B633, so an increase of 1µ is a minimal change, probably only requiring a small increase in plating time rather than a change to the solution chemistry.
Luck & Regards,
Ted Mooney, P.E. RET
Striving to live Aloha
(Ted can offer longterm or instant help)
finishing.com - Pine Beach, New Jersey
⇩ Related postings, oldest first ⇩
for Shops, Specifiers & Engineers
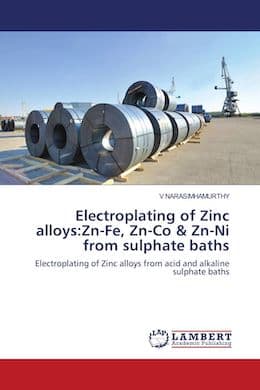
from eBay, AbeBooks, or Amazon
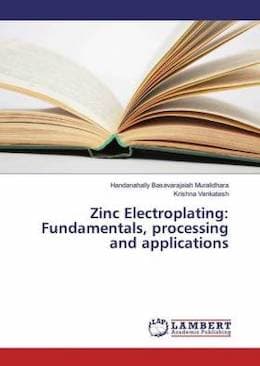
from eBay, AbeBooks, or Amazon
"Alkaline non-cyanide zinc plating with reuse of recovered chemicals" by Jacqueline M. Peden (1994)
from (U.S. EPA)
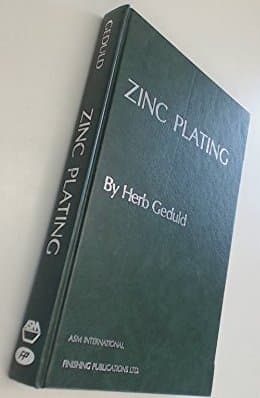
from eBay, AbeBooks, or Amazon
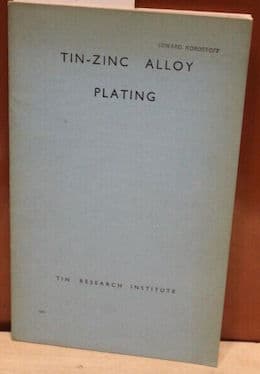
from eBay, or AbeBooks
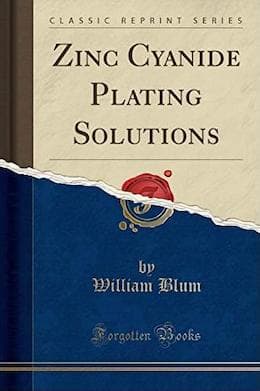
from eBay, AbeBooks, or Amazon
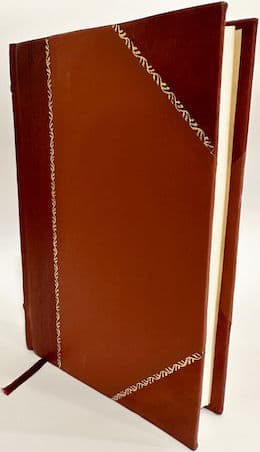
from eBay, AbeBooks, or Amazon
(as an Amazon Associate & eBay Partner, we earn from qualifying purchases)
Q. Amps per square Ft? We have metal product electroplated after forming. My question is in regards to zinc plating. Is there a target amps per square ft. that is required to obtain a nominal coating thickness of .0005"? If so should I be able to calculate surface area by the particular parts we mfg. and determine an appropriate lot size to obtain the nominal thickness required? Thanks for any input.
Joe Comptonaccess hardware - Honeoye Falls, New York
2004
A. If you look in the plating process supplier's technical data sheet or a plating book like the Metal Finishing Guidebook you will sort of find your answer, but you won't like it because it will probably say something like 4-60/ASF, and the range will be too broad to help you much. About 20 ASF is probably typical/average, but even that won't quite answer your question, and might somewhat mislead you.
The real way to look at it is that no production plating shop anywhere is going to plate slower than they have to, at a lower production rate, so what usually controls the ASF is not what plating thickness they are shooting for, but what ASF they can successfully plate at. So, what you are looking for is whether 20 ASF, or somewhat less or somewhat more, is the ASF they must limit themselves to. Then you can divide the available amperage of the rectifier by that number, and that's how many square feet you can plate in one load. Also, you can then assume some efficiency (which might be 95 percent for acid zinc, 50 percent for cyanide zinc, and somewhere in between for alkaline non-cyanide) and then apply Faraday's Law to see how long it will take to get .0005" at 20 (or whatever) ASF. The Metal Finishing Guidebook has a handy chart in the back which combines Faraday's Law with the various conversion factors and tells you how many amp-hours per square foot to get .001" thickness at 100 percent efficiency.
For zinc it's 14.3, so you need 7.15 for .0005". Say 80 percent efficiency (which is low for acid zinc but very high for alkaline), then you need 8.94 amp-hours per square foot. If you can plate at 20 ASF, that's a plating time of 27 minutes. I don't think that's terribly far off for acid zinc but very optimistic for alkaline, but hopefully a practicing zinc plater will correct me.
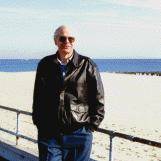
Ted Mooney, P.E.
Striving to live Aloha
(Ted can offer longterm or instant help)
finishing.com - Pine Beach, New Jersey
A. Dead on target Mr Mooney. We generally decide upon ASF depending on the part configuration. The part that has obtuse angles sticking out are better suited to lesser currents as low as 10 ASF and longer plating times, and dead flat parts can be plated with currents as high as 40 asf with reasonably uniform plating thickness.
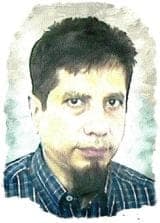
Khozem Vahaanwala
Saify Ind

Bengaluru, Karnataka, India
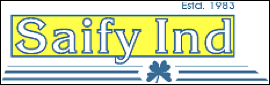
Q. What is the upper voltage limit for NAZ NaOH baths (rack plate)? Chemical data sheets and CEF literature both state a max of 6 volts. But I cannot seem to find much information about the harm or risks for running higher voltage?
I am trying to find all ways to maximize our bath's through-put. We use steel anodes with a separate zinc regeneration tank. Curiously, we already operate in the 6-7 volt range, our main loads are 120-150 sq ft, and at this voltage we achieve 8-10 ASF. Thickness requirement for these loads is .0003" minimum. Due to mechanical issues (hoists), our current plating time is 45 minutes. This same line used to run at a 36-minute plating rate. We are in the process of upgrading our hoists, I am just preparing for the plating bath to be the new "choke-point".
Metal finishing - Lincoln, Nebraska USA
January 17, 2020
A. Hi Bruce. What does 'NAZ' mean? Obviously, the ideal situation is when the design is such that everything "chokes" simultaneously -- i.e., you have the appropriate number of plating cells and the appropriate hoist capacity, that you still have enough cleaning time & acid dip time, sufficient drain time, a non-wasteful time-motion diagram, enough load/unload time, etc. How many plating cells do you have, and is the time-motion diagram such that all are full, or is one always empty ('put & take' programming)?
I am familiar with amperage limits, not voltage limits for plating processes; I've personally never heard of it. Rather, there are ASF limits beyond which the plating burns, based on, as our knowledgable colleague Kozeem notes, the shape of the parts and other factors. Electroplating is definitely a science, but unfortunately that doesn't mean that our knowledge is sufficient that every answer can be mathematically derived from first principles. You currently plate at 8 to 10 ASF for 45 minutes and you used to successfully plate for only 36 minutes, so you must have been plating at:
45/36 X (8 to 10), or 10 to 12.5 ASF
Platers plate at as high a current density as they can without burning. I would guess, but it's only a guess, that you can probably plate at a higher current density than 10 to 12.5 ASF ... but, as Kozem says current density might be limited to 10 ASF or might be as high as 40 ASF depending on part shape, and I can't challenge those numbers.
Regards,
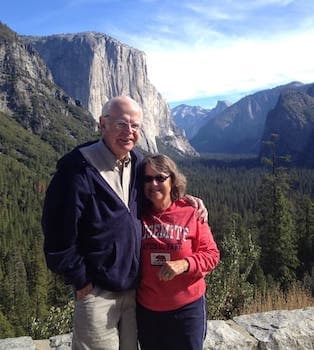
Ted Mooney, P.E. RET
Striving to live Aloha
(Ted can offer longterm or instant help)
finishing.com - Pine Beach, New Jersey
Q. My apologies, NAZ (Non-cyanide Alkaline Zinc). I was taught years ago that gains in plating speed drop off above 6-7 volts in an alkaline bath, wasting energy, and potentially slowing the plating speed. Is this incorrect? I've posed this same question to our chemical supplier, they are researching this as well. We have three plating cells, all of which remain full the entire cycle. We just checked sodium carbonates, they are at 45 g/L, which surprises me since we have never treated for carbonates. I appreciate the feedback!
Bruce Brady [returning]Metal finishing - Lincoln, Nebraska USA
January 21, 2020
A. Hi again. We agree on the fact that attempting to plate at beyond some certain empirically determined plating speed doesn't work properly because it generates too much hydrogen and/or burns the plating. I personally have just never heard of this plating speed issue expressed in terms of voltage rather than current density, so I can't comment -- although others hopefully will.
Working from the "Electrochemical Equivalents" chart in the MFG, it takes 14.3 ASF for 60 minutes to deposit .001" of zinc at 100% efficiency. Your efficiency could be 75%, but probably a bit lower, so 14.3/.75 = 19 ASF for 60 minutes to deposit .001" or 5.7 ASF for 60 minutes to deposit 0.0003". So at 10 ASF it will take about 34 minutes.
With 3 plating cells at 5 loads per hour you'd get about 35 minutes of plating time. If, with the new hoist, you can plate 7 loads per hour, that would be about 24 minutes of plating time and would require successful plating at 14 ASF. That assumes plating thickness is uniform, which it never is, so you'll actually need a bit more to reach a minimum thickness. Without seeing the parts, let alone actual experience with them, I can only guess, but I think it will work :-)
Of course, 7 loads per hour is not a lot, but you'd probably need additional plating cells to get beyond it.
Regards,
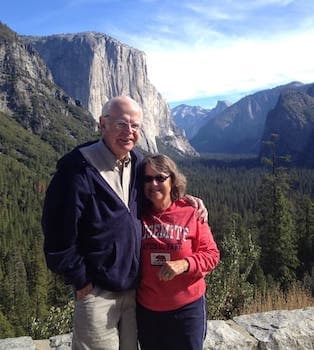
Ted Mooney, P.E. RET
Striving to live Aloha
(Ted can offer longterm or instant help)
finishing.com - Pine Beach, New Jersey
Q. Hi ! I am a mechanical engineer working in electroplating industry.
Wanted to know that whether we can produce Minimum 13 micron zinc coating following alkaline zinc rack plating in less than 30 minutes or not .
Rectifier capacity and zinc metal concentration can be made available as per requirement .
Looking for your support.
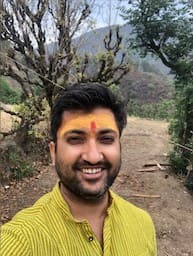
Rahul Bhatt
- Faridabad Haryana
February 14, 2022
A. Hi Rahul. It sounds maybe just barely feasible if by 'minimum 13 micron' you mean an "average thickness" of not less than 13 microns, but not if you mean "at least 13 microns everywhere" on the part. According to the "Electrochemical Equivalents" appendix in the Metal Finishing Guidebook, at 100% efficiency, 14.3 Amp-hours/ft2 will deposit a thickness of 0.001", so 7.32 Amp-hours/ft2 would deposit 13 microns average thickness. But the efficiency of alkaline zinc plating is only about 40% to 90%, and probably toward the lower end of that range when you want to plate at high current density. So more than 60% efficiency sounds unlikely to me, which brings you back up to, say, 12.2.Amp-hours/ft2 to deposit 13 microns, or 24.4 Amps/ft2 to do it in a half hour. Khozem's comments on this thread will help clarify whether 24.4 Amps/ft2 is feasible for your parts.
Luck & Regards,
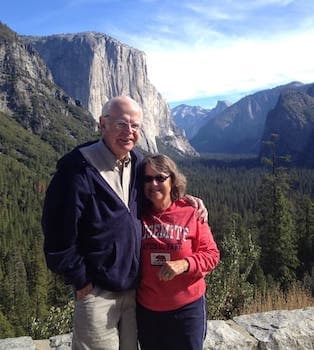
Ted Mooney, P.E. RET
Striving to live Aloha
(Ted can offer longterm or instant help)
finishing.com - Pine Beach, New Jersey
Q. Thanks very much for your earlier response !
I have few questions I mean to present:
1. On what circumstances Efficiency of bath is varying & how can we keep it an optimum return level?
2. If we can plate in a varying current density ranges, can we vary the concentration of Zinc metal in the bath as well? If yes, what is the range suggested ?
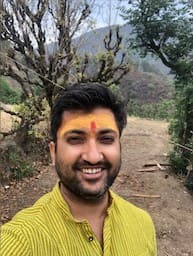
Rahul Bhatt [returning]
- Faridabad, Haryana, India
March 6, 2022
A. Hi again. Generally, plating shops use proprietary processes.
I.e., rather than each individual shop starting back in 1955 again and developing their own process across a period of decades, we buy the processes from suppliers who have done the research & development and offer a technical data sheet and periodic analysis and assistance to make sure their bath is operating under the optimum conditions -- not just for efficiency, but in all aspects.
Remember that everything is inter-related variables rather than independent variables when it comes to satisfactory plating. Increasing the concentration should increase the efficiency, but it obviously increases dragout and waste treatment costs, as well as causing other less obvious problems. Plus, although plating is a science, it involves a large amount of empirical knowledge in addition to theoretical knowledge based on first principles. Finally, production plating must be an equilibrium process -- you can't optimize it to plate one load of work, but must assure that when you finish processing a load of work, the zinc concentration and other parameters in the bath must be the same as when you started processing the load.
You can read textbooks, like the Geduld or Muralidhara & Venkatesh books suggested further up the page, and try to do some optimization -- but the usual approach these days is to buy a proprietary process and follow the supplier's technical data sheet rather than ad libbing or being forced to do your own R&D. :-)
Luck & Regards,
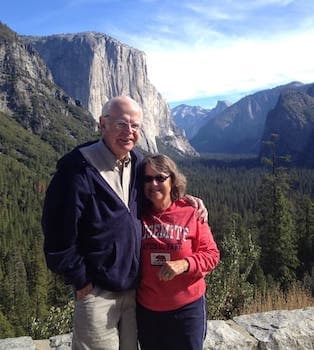
Ted Mooney, P.E. RET
Striving to live Aloha
(Ted can offer longterm or instant help)
finishing.com - Pine Beach, New Jersey
A. To give an example, Alkaline non cyanide zinc bath. I use in the range of 12-18 grams of zinc during a 20 minute run at current density of 20 ASF, running the zinc level at the higher end of the recommended range and bath temp of 25-30 °C, rack plating.
Boris Siljanoski- Australia
January 24, 2024
Q. As you said 40 ASF for plating is it for one side or 40 ASF Both sides of metal.
A kalim- Bangalore, India
June 5, 2022
A. Hi Kalim. ASF means amperes per square foot; it refers to the total surface area of the components; so, yes, it's 40X the total surface area, which includes both sides if you're talking about flat sheets which have two sides.
But please introduce yourself and the situation you are encountering. Not only because it makes the page more interesting than dry requests for clarification of grammar & arithmetic, but because it is very easy to misinterpret things when you give readers no opportunity to critique your thinking. For example, Khozem said 40 ASF was possible in some limited circumstances; he certainly did not mean that it's standard or the normal situation or easy. So how you intend to use that 40 ASF information that you gleaned here would be interesting to those readers who have not been able to do satisfactory plating at 40 ASF :-)
Luck & Regards,
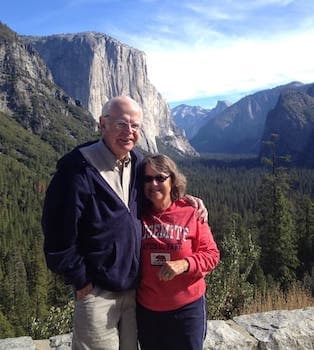
Ted Mooney, P.E. RET
Striving to live Aloha
(Ted can offer longterm or instant help)
finishing.com - Pine Beach, New Jersey
Q. Plating time is it too high in alkaline non-cyanide zinc plating?
I am electroplating 6x6 inch cold rolled Steel panel in non-cyanide alkaline zinc plating of 7 litre bath. I am facing the problem of very high plating time. I got only 3 micron in 30 min at 2.9 amp/dm2. My surface area is 2.32 dm2. I also observe that anodes become black during electroplating. Please suggest solution.
- New Delhi, India
July 31, 2022
(affil links)
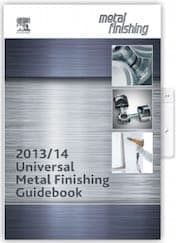
free pdf is currently available from academia.edu
A. Hi ABHISHEK. Unless the back side of that plate is reliably masked, your surface area is 4.64 dm2 (0.5 ft2), not 2.32 dm2. Are you sure you are plating at 2.9 amp/dm2 (27 ASF) , i.e., 13 Amps total, or might you be plating at half that rate?
From the Electrochemical Equivalents table in the Metal Finishing Guidebook:
At 100% efficiency, zinc will plate 0.001" per 14.3 Amp hours per square foot. You are applying 27.3 ASF for 1/2 hours so you would get 0.00095 inches or 24 microns. At an efficiency of 40% it would be 9.6 microns in 30 minutes.
Please get back to us with conformation of your surface area and current density and something about your plating solution (a proper proprietary or a home-brew zincate solution). Trying to guess the cause of a problem from very limited data is difficult, but if that data is actually wrong it can become unworkable :-)
Luck & Regards,
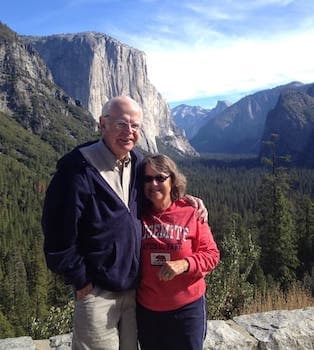
Ted Mooney, P.E. RET
Striving to live Aloha
(Ted can offer longterm or instant help)
finishing.com - Pine Beach, New Jersey
A. To give an example, Alkaline non cyanide zinc bath. I use in the range of 12-18 grams of zinc during a 20 minute run at current density of 20 ASF, running the zinc level at the higher end of the recommended range and bath temp of 25-30 °C, rack plating.
Boris Siljanoski- Australia
January 24, 2024
Q, A, or Comment on THIS thread -or- Start a NEW Thread