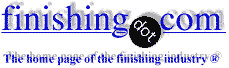
-----
Blackening formulas for steel and cast iron
Q. Finding sodium nitrite here is difficult, will the caustic soda ⇦liquid caustic soda in bulk on Amazon [affil link] /sodium nitrate ⇦ on Amazon [affil link] only solution work? Or is sodium nitrite essential?
Warthog RawboneHobby blacksmith - Midvaal South africa
December 13, 2021
A. Try any old-school blackening formula for blackening steel (50 gms ferric chloride ⇦ on eBay or Amazon [affil link] / 1 lit water, brown finish boil it in water for 30 minutes, repeat it at least 3 times). tannic acid ⇦ on eBay or Amazon [affil link] / phosphoric acid mix can be used too (20 gms tannic acid ⇦ on eBay or Amazon [affil link] /15 mll phosphoric acid/ 1 lit water). Hope it helps and good luck!
Goran Budija- Cerovski vrh Croatia
A. According to old D.Fishlocks book on metal coloring you can use sodium hydroxide and sodium nitrate ⇦ on Amazon [affil link] formula. Sodium hydroxide ... 1200-1500 gms sodium nitrate ... 30 gms water 1 lit.,5-30 minutes immersion, boiling solution (140-150 °C). Hope it helps and good luck!
Goran Budija- Cerovski vrh Croatia
Q. Can Potassium Nitrate (KNO3) be substituted? I read an article that suggested Sodium Hydroxide (NaOH) and Potassium Nitrate (KNO3) work very well and are the most commonly available, but no information about the ratio of either per gallon of water. Any thoughts?
Brett Pruitt- Marshall, Texas
December 29, 2022
A. Expired US patent US2817610A is good source of information on that subject.Hope it helps and good luck!
Goran Budija- Cerovski vrh Croatia
⇩ Related postings, oldest first ⇩
(affil links)
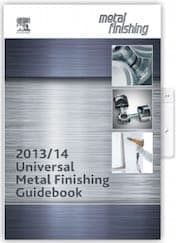
free pdf is currently available from academia.edu
Q. Dear sirs I would like to know more about the blacking process for steel and cast iron.I tried to find some specialized literature about this process in technical books, but unfortunately I didn't have success. Therefore I ask to my FINISHING.COM's colleague please if could some one help and indicate me, where I will be able to find details about this subject. Thanks in advance for the assistance, Best regards
ricardo bastos- sao paulo, Brazil
1999
A. Dear Mr. Ricardo B.,
Blackening on steel can be achieved by oxidation process using sodium hydroxide along with oxidising agents such as sodium nitrite and sodium nitrate. A typical formula for blackening on steel is given below. 1. sodium hydroxide (caustic soda ⇦liquid caustic soda in bulk on Amazon [affil link] ) - 625 gms/litre 2. Sodium nitrite - 100 gms/lit 3. Sodium Nitrate - 25 gms/litre Here the temperature should be around 140 °C to get uniform blackening. with best regards, ramesh.
ramesh varadhan- Chennai, India
![]() |
A. Answer to letter of Ricardo Bastos: There is really not much information about blacking of steels and cast iron available. All I can add is that it is simple and at everyone's site possible by means of a new blacking at room temperature. You need no costly apparatus and have no harmful chemicals-no heating-up-no exhaust-no environmental problems. It is as easy as dipping parts into paint. Klaus S [last name deleted for privacy by Editor]- WIESBADEN - Germany
![]() Ted Mooney, P.E. Striving to live Aloha (Ted can offer longterm or instant help) finishing.com - Pine Beach, New Jersey |
Q. Mr.RAMESH, I understand that a catalyst is being added at the time of blackening by some. Any idea? Also dipping in blue colored oil seems to deepen the color...any comments?
ramajayam- Bangalore, Karnataka, India
Q. DEAR METAL FINISHING FRIENDS, I came to know that recently blackening of metals also can be done at room temp. If, any one has a basic idea about this? Please give me an idea or let me know where it can be found in metal finishing. My advance thanks to You.
JANARTHANA RAJA- CHENNAI, India
1999
A. Hi, Janarthana. There are proprietary blackening solutions that operate at room temperature available from suppliers like EPI / Electrochemical Products Inc. [a finishing.com supporting advertiser], Heatbath, and several others. Some if not all are based on deposition of selenium compounds. We have an FAQ about black oxide and cold blackening.
However, the best of the proprietaries, after decades of trial-and-error and gradual improvement, are still inferior to hot blackening in my personal opinion. So I would not propose a non-proprietary cold blackening process because the likely quality of the finish would likely be very low. I'd say stick to hot blackening or purchase a proprietary room temperature bath. Good luck!
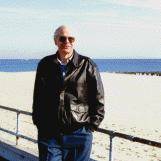
Ted Mooney, P.E.
Striving to live Aloha
(Ted can offer longterm or instant help)
finishing.com - Pine Beach, New Jersey
Q. Dear sir,
I have completed my B.E degree and started an industry in Bangalore, I deal with the blackening of the materials.
I'm posing some problems for getting the material blackened, i.e., the customers supply, the raw material after heat treatment and there are some scalings, dust, residual oil (metaquench etc.)
So please suggest me that what all acid washes and at what concentrations I have to do so that I will be able to remove all these oils, soot, scaling etc.,and I can give a better quality to the customers.
With regards,
N.Yatish Kumar- Bangalore, Karnataka, India
March 6, 2009
A. Phosphoric acid
sean manvw- Baltimore Maryland
A. Hi. I appreciate Sean's answer and help, but I don't think phosphoric acid is up to this job :-)
I think you'll need hot alkaline cleaning followed by rinsing and a dip in HCl.
Regards,
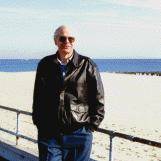
Ted Mooney, P.E.
Striving to live Aloha
(Ted can offer longterm or instant help)
finishing.com - Pine Beach, New Jersey
Q. Dear sir,
After blacking operation, is there any changes in material properties (hardness, dimensions, smoothness)? Please give good suggestion. After heat treatment, blacking is suitable for steel?
Regards
- Hyderabad,AP
July 30, 2009
A. Hi, Rajendar. In most cases black oxiding will have no meaningful effect on hardness, dimensions, or smoothness. Some hardened components like rifle barrels are blackened.
But we can give you a more accurate and useful answer if you are able to describe the details of your own particular situation; there are a dozen "ifs, ands, and buts" which apply to the general case, but probably not to your case. Good luck.
Regards,
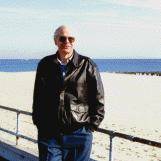
Ted Mooney, P.E.
Striving to live Aloha
(Ted can offer longterm or instant help)
finishing.com - Pine Beach, New Jersey
Q. Sir please tell me all chemicals mixed in water, like you say caustic 625 gm/ltr
Vikas girdhar- Amritsar Punjab India
March 26, 2018
by Biestek & Weber
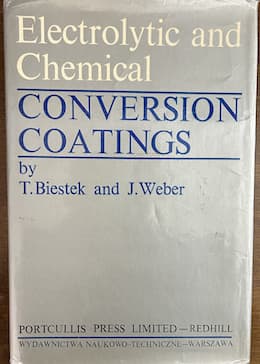
on Amazon
on AbeBooks
(affil link)
A. Hi Vikas. Ramesh Varadhan advised us "caustic 625 gm/ltr", but also to add sodium nitrite 100 gms and sodium nitrate 25 gms per liter of water.
In the 1998 Metal Finishing Guidebook, Nat Hall suggests caustic 80 oz/gal, potassium nitrite 30 oz/gal, and potassium nitrate 20 oz/gal. Biestek & Weber's "Conversion Coatings" .
offers five more variations, and a very good treatment about how the background chemistry works. One of their formulas is 650-700 gm/ltr caustic, 30-35 gms/ltr NaNO3, 16-18 gms/liter NaNO2, 18-20 gms/ltr NaCl.
I'm confident that any of these formulas will work, and that small variations are highly unlikely to be the main cause of any difficulties which you are encountering. Reprinting variations in formulas from textbooks is probably less useful than people describing their own situation and letting us try to help them with it :-)
Good luck, regards,
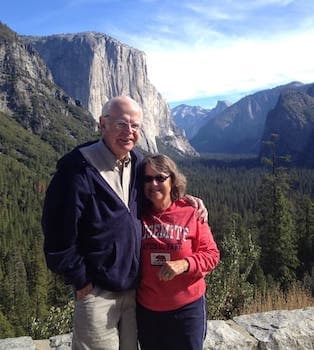
Ted Mooney, P.E. RET
Striving to live Aloha
(Ted can offer longterm or instant help)
finishing.com - Pine Beach, New Jersey
Q. I tried an experiment with electro-blackening of steel, 4140 or an alloy near enough. I started with a solution of sodium hydroxide and sodium nitrate and was able to achieve a medium brown finish. Unfortunately my chemical knowledge is only what I acquired in high school and a qualitative Analysis class in my freshman year of college... Quite a few years ago.
Is anyone aware of an electrolytic process to generate the Fe3O4, black coating?
I recently ran a across a cold blue process using Hydrogen Peroxide and Sodium Chloride (a saturated solution in the H2O2) where you develop the red rust (ferric oxide I believe) which is then converted to Fe3O4 in a hot water bath. The question on this process centers around the Sodium Chloride: is this the best salt to add to the peroxide solution, and if so what does the chloride ion contribute to the oxidation process?
Thanks for your time
- Waukesha, Wisconsin USA
April 7, 2018
A. Probably oldest electroblackening process for iron and steel is Becquerels process (1861). He used a solution of iron-II-oxide in ammonia. According to Fishlock 400 gm NaOH/ 1 lit water solution can be used (50-100A/sq.ft.,120 °C temp, 10-30 minutes. Object= anode. Hope it helps and good luck!
Goran Budija- Cerovski vrh Croatia
Thanks for the information Goran. I will give this a try.
Q. The cold blue/slow rust method that is used to blue/blacken steel is a desirable process. For home users it is quite safe compared to the industrial caustic hot blue, so it has both importance and relevance for me.
I have rephrased the second part of my earlier question for clarity.
I recently ran a across a cold blue or slow rust method using Hydrogen Peroxide and Sodium Chloride added to saturation in H2O2).
This solution is used to rapidly develop the red rust Fe2O3 which is then converted to Fe3O4 in a hot water bath.
My question on this process centers around the Sodium Chloride: Is this the best salt to add to the peroxide solution, and if so what does the chloride ion contribute to the oxidation process? Is this analogous to rust on iron that is 'caused' by HCl fumes? The fact that the HCl causes rust to form is obvious, what is less obvious is the chlorine/oxygen relationship. Obviously this is a layman's perspective, but it's all I have...
Thanks for your time
CIW LLC - Waukesha Wisconsin USA
April 11, 2018
A. According to Angiers' book Firearm Bluing and Browning there are very many formulas and many of them are based on use of more or less toxic components (mercury compounds, antimony compounds, potassium bichromate, nitric acid). If compared with that type of compounds, sodium chloride is harmless but still effective. Hope it helps and good luck!
Goran Budija- Zagreb,Croatia
Q. cont'd I'm looking to get a little chemistry education. I don't have a problem using the H2O2/NaCl solution to obtain the results I want, I'm trying to understand the chemistry.
What purpose does the chlorine ion serve in the chemistry of the H2O2 solutions' reaction that forms the Fe2O3?
Put another way, would this reaction still result in the formation of Fe2O3 without the NaCl? Is it a catalyst? Are there intermediate products that contribute to the reaction?
Thanks
- Waukesha Wisconsin USA
A. The best answer to my secondary question regarding the reason for the NaCl dissolved in hydrogen peroxide seems to have been found on Reddit":
In reality, the H2O2 scavenges an electron from the Fe in the steel, electrons prefer to travel in salt water (which is why salt water conducts electricity). The electron jumps to the H2O2 forming H2O and O- which immediately grabs the Fe2+/Fe3+ to form iron oxide. In the absence of NaCl, the electrons struggle to make it to the H2O2 because they are scavenged by the H+ ions in the water (which is why you would see bubbling in the absence of salt, but not a lot of action)"
My commentary which relates to firearms coatings:
The blacking conversion (from red to black) is accomplished in a boiling water tank using the same process that has been used to form the classical 'cold rust' seen on many old firearms that post date the 'browning' era but pre-date the 'hot blue' using a high temperature saturated NaO/NaNO3 solution.
Thanks for the input.
- Waukesha, Wisconsin USA
A. My company has used the supersaturated aqueous solution of sodium hydroxide to blacken antique steel and cast iron hardware, such as sash pulleys for many years. Without any other additives, it works very well. Quite a durable finish.
Boil for 20 minutes, approx. 280 °F. We use a gas burner on a stand OUTSIDE. And handle very carefully, with protective clothing and face protection. Water being added can erupt as it superheats beneath the surface.
- City of Orange, NJ
Q. Hi Peter, that is very interesting about heating a super saturated solution outside. I just wondered what was the vessel you used to heat the solution in? Thanks. Chris
Chris Baxter- UK, Wales
April 20, 2023
A. Any steel pot will do. Deeper is better. Reasonably thick. Don't use a thin steel can. Use tongs with thick rubber gloves and goggles to put steel objects into the pot
Peter Triestman- City of Orange, NJ
April 29, 2023
Q, A, or Comment on THIS thread -or- Start a NEW Thread