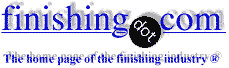
-----
Prevention and removal of white rust on galvanizing

Q. Dear sir,
How to reduce white rust in wire galvanizing whatever we are not using dichromate, normally Quench only.
- Abu dhabi, uae
January 1, 2022
A. Hi Mohd Tariq. Your question answers itself :-)
It sounds very difficult to re-wind wire to insure that it is absolutely dry, free of capillary action areas, and that all the wire has good exposure to the atmosphere. It seems like eschewing the traditional specific step designed to reduce white rusting is problematic.
Perhaps there is a galvanizing consultant out there who has some alternate ideas towards reducing white rust, but you will probably have to start by supplying a lot of technical details about exactly what you are doing.
Luck & Regards,
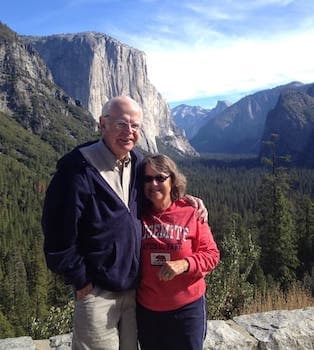
Ted Mooney, P.E. RET
Striving to live Aloha
(Ted is available for instant or longterm help)
finishing.com - Pine Beach, New Jersey
January 2022
A. As to Wire galvanizing, white rust can happen at previous treatment process and after galvanizing. Need more information to analyze if rust happened before galvanizing. After galvanizing there is a quenching process. There are two potential causes for your issue.
1. Quenching too long time and wire brings water when packing.
2. Quenching water: Quenching water should be softened and clean.
FYI.
Integrated supplier of Galvanizing - Shanghai
February 12, 2022
⇩ Related postings, oldest first ⇩
Q. Dear Sirs,
My question is ; If the hot deep galvanised surface of material has white rust, how can we clean or remove the surface of it? And What can be the actual reason of the white rust on galvanised surface?
Best Regards,
Ms, Mechanical Engineer - Sarýseki , Ýskenderun, Turkey
2003
A. White rust consists of zinc-corrosion-products and will grow when fresh galvanized material is stored or transported in a way that condensed water can act upon the zinc-layer without ventilation. When the effect is not that serious, white rust can be brushed off with a soft brush. (it often looks serious because white rust has a large volume - You can measure the zinc layer after brushing off to see if it is serious) Take care for ventilation after brushing.
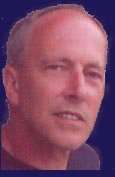
Dolf van den Berg
- Leusden, The Netherlands
2003
A. Dip all galvanizing in a weak Cr solution to passivate after galv. Dipping hot also cools the work for quicker cleaning access. Gives good protection for 2-4 months from white rust. The energy removed from the steel to the passivate solution can be recovered for heating acid to make faster pickling.
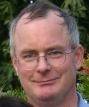
Geoff Crowley
Crithwood Ltd.
Westfield, Scotland, UK
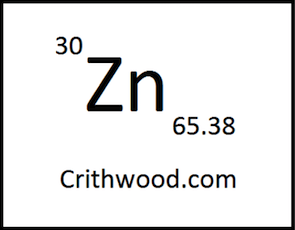
2003
Q. We have some galvanized coils after months now it is rusted (white rust)
How can I deal with this coils ( paint-clean...)
Thank you.
employee - Egypt
2007
Q. I am a galvanizing engineer working for a big MNC for the past 4 years. I want to know if white rust could be avoided. Our plant is situated in a coastal area , does the salty air accelerates white rust formation? How can this be controlled ? Is there any passivation treatment for the same?
ARUN KUMARPLATING SHOP EMPLOYEE - PONDICHERRY, India
December 29, 2008
by Kuklik & Kudlacek
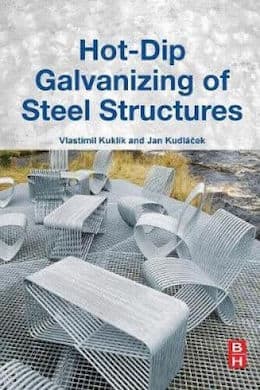
on eBay or Amazon
or AbeBooks
(affil link)
A. Post galvanizing passivation avoids the formation of white rust for a while. (perhaps 6 weeks)
But the options for effective passivation are not so attractive. The best performing include chromate systems which are unattractive from a Health and Environment perspective.
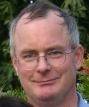
Geoff Crowley
Crithwood Ltd.
Westfield, Scotland, UK
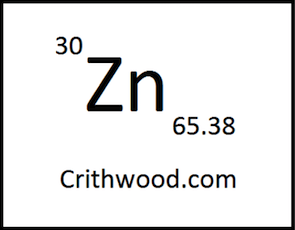
December 31, 2008
January 3, 2009
A. Sir:
With hex chrome the pH must be kept within narrow limits to give good results. There is an additive for hex chrome quench that gives a perfectly clear coating. The usual effective hex chrome is a few hundred ppm in Cr+6.
Some galvanizers think they can control white rust by:
(1) Use the "dry" kettle method.
(2) Not use a quench.
(3) Use the quench water to make-up for evaporation losses in the hot flux solution and then add only tap water to the quench.
(4) Not allow the galvanized product to get rained on for 2 to 4 days.
(5) Keep the aluminum content of the zinc at or below 0.001%.
(6) Not use bismuth or tin in the zinc or at least limit their use.
(7) Clean the quench water when it contains a cloudy precipitate.
Regards,
Galvanizing Consultant - Hot Springs, South Dakota, USA
A. This posting relates to this letter and 56143.
In November of 2010, I started my new NiftyGalv process at a plant having 0.1% bismuth in the zinc. During that first trip, I saw virtually no white rust even though it rained about one-third the time I was there. This plant has a relatively warm climate with some air pollution. The galvanized product is not water quenched and goes immediately outside. During my second trip in January of 2011, I again saw virtually no white rust even though it rained.
Yesterday (Feb. 2012), I spoke with the owner and he stated that white rust has been substantially reduced in the last year. I asked him to quantify his "substantially reduced" statement. I asked: "On a scale from 1 (virtually no white rust) to 10 (severe white rust) what were you a year ago and what are you now?" His answer was: "A year ago I was a 6 or 7 and now I am a 0 or 1." The question is: Did NiftyGalv reduce white rust or did the lowering of the bismuth (from 0.1% to 0.02%; no bismuth was added in the last 16 months) reduce the white rust? Because it took 16 months to achieve less white rust, NiftyGalv appears not to be the cause of less white rust. Rather, lowering the bismuth appears to lower the white rust. Without bismuth, lead, or NiftyGalv the galvanizing results are poor. Because lead is toxic its use is not recommended and galvanizers in the USA are phasing it out of their zinc.
My seeing little or no white rust during my two trips is likely due to the lack of unique combined conditions causing white rust. The owner, however, is there every day and he mentioned a year ago during certain night rain events he knew he would arrive at the plant with chalky white all over the product. During the present rain season (now) that chalky white has not reappeared.
Other metals in the zinc that can cause white rust or early corrosion include: too much aluminum, tin, copper, and magnesium.
Galvanizing Consultant - Hot Springs, South Dakota, USA
February 2, 2012
Q. Galvanized iron wire usually has a galvanizing surface in order to prevent rusting or corrosion. Galvanization can protect galvanized wire underneath from rusting, but after a long time galvanization itself also can rust or corrosion. This will be a white rust instead of a typical red rust. If the corrosion is continued to develop, the underneath galvanized wire may begin to rust. So how to clean corrosion from galvanized wire and improve galvanized iron wire's service life.
Joy LiuShijiazhuang city, China
April 1, 2012
A. Sir:
Normally zinc corrodes about 20 times slower than steel. Unfortunately in recent times the addition of bismuth and perhaps tin accelerates white rust formation. Thus if you could provide zinc bath analysis perhaps this question could be addressed. Excess aluminum in the zinc can likely cause white rust.
Also if a quench is used and becomes contaminated (e.g. in a few 1,000 ppm) then this dirty quench will cause white rusting. A simple conductivity meter can determine the level of quench water contamination. Alternatively even putting the quench water into a glass bottle and observing coloration or cloudiness could be useful.
Regards,
Galvanizing Consultant - Hot Springs, South Dakota, USA
by NACE
[only rarely available]
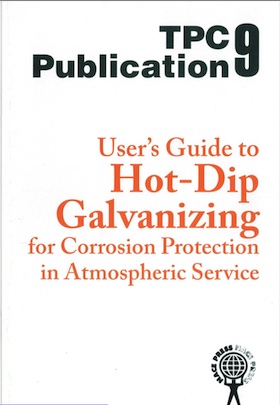
on eBay or Amazon
or AbeBooks
(affil link)
Q. Dear Sir,
May I ask what contaminates the quenching water, and causes white rust / reduced brightness? Is it the residue from flux (ZnCl2 and NH4Cl)? The Zinc ash?
Regards,
- Selangor, Malaysia
April 20, 2012
A. Sir:
You are correct the dissolved material is zinc chloride and ammonium chloride from the flux. The undissolved material is likely zinc oxide. My new process causes the burned flux/ash to not stick to the galvanized product so I need to inform users of this technology to change out their quench tank. In a year or so we can see if the dissolved materials in the quench is less than the usual 5,000 ppm.
Regards,
Galvanizing Consultant - Hot Springs, South Dakota, USA
April 27, 2012
Dear Dr Thomas,
Thank you for sharing your knowledge with us.
Regards,
- Selangor, Malaysia
Q. What is the reason behind white rust? Please brief all and give also solutions.
Johur Ahmed Roneysteel - Chittagong, Bangladesh
August 26, 2013
A. Hi Johur. We appended your inquiry to a thread which hopefully answered it for you. If not, please try to detail your actual situation so we can get down to specifics.
This forum is a great way to get advice for highly specific real-world situations, but books might be better if you're seeking insights into broad general concepts. Good luck.
Regards,
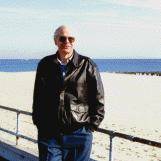
Ted Mooney, P.E.
Striving to live Aloha
(Ted is available for instant or longterm help)
finishing.com - Pine Beach, New Jersey
August 2013
Do phosphide fumigants cause galvanizing to white rust?
Q. Dear All,
I have situation of complete white rust on the zinc coating, even though the galvanized surfaces are exposed to open atmosphere. But it seems that the galvanized surfaces are exposed to aluminum phosphide fumigation. Could this aluminum fumigation be the cause of this white rust.
Please share your thoughts.
Regards
Sathish
- United Arab Emirates
June 20, 2014
A. Hi Sathish. I found your question interesting, so I did some googling of aluminum phosphide fumigation and discovered that it evolves phosphine gas, which is highly corrosive to noble metals, but maybe not to galvanizing. I also learned that the "wheat pills" used for the process often contain chemicals which evolve ammonia ⇦ on eBay or Amazon [affil link] to limit the explosivity of the phosphine gas. So thanks for the interesting question. But I have no real clue as to the answer :-(
Hopefully someone experienced with galvanized silos will know right offhand the effect of the phosphide fumigants on it.
Regards,
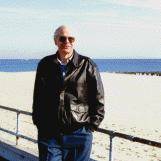
Ted Mooney, P.E.
Striving to live Aloha
(Ted is available for instant or longterm help)
finishing.com - Pine Beach, New Jersey
A. This fumigation has NO EFFECT on galvanized surface.
Dalela, Umesh Chandra- Abu Dhabi, UAE
July 3, 2014
A. Sir:
I presume the fumigation is done in a sea bound container? Aluminum Phosphide in wheat pills is used here on the prairie to kill prairie dogs. As I remember one puts the pills into the hole, covers with dirt, and then adds water. Thus in a container one may put the pills in a dish, adds water and close the container. Take note that phosgene is extremely toxic.
Under proper conditions (e.g. moisture/sea salt), I certainly expect much white rust. I once had a case of extreme white rust in a container which contained tartaric acid
⇦ on
eBay
or
Amazon [affil link] (perhaps from a previous shipment).
I do not know if phosgene alone may or may not cause white rust.
Regards,
Galvanizing Consultant - Hot Springs, South Dakota, USA
July 3, 2014
November 25, 2015
Q. We are facing issues of white rust on the parts once they reach the customer overseas.
I am attaching some pictures of parts that have observed white rust once they are received by our customer in the US.
These parts are put in a box, the boxes are then placed in a pallet and the pallet is stretch wrapped and sealed. How can this occur and how can we address this?
Larger parts are directly placed in pallets and then stretch wrapped.
- Delhi, India
![]() |
A. The image shows classic white rust, sometimes also called "wet storage stain". The clues are in that second name. ![]() Geoff Crowley Crithwood Ltd. Westfield, Scotland, UK ![]() November 28, 2015 A. First of all, what you are seeing is white rust caused by water, almost certainly in a confined system. It can be removed by a weak acid or a very weak solution of a strong acid, followed by rinsing. Naval Jelly is used frequently for such applications. It is phosphoric acid-based, so it leaves a thin film of zinc phosphate on the surface. ![]() Tom Rochester CTO - Jackson, Michigan, USA Plating Systems & Technologies, Inc. ![]() ![]() December 2, 2015 |
A. It's not so much that the EU require trivalent chromates, they seem intent to ban all chromates, from 2017.
We have tried many non-chrome passivates and not found one that works yet. Our test is simple. Freshly galvanize some test plates, about 4-5 for each chemical under test. Passivate with the material being tested. Now stack the plates flat to flat, in a pile and leave this out in the weather for a couple of weeks. It must rain several times (not hard here in Scotland), and dry at least once.
Some tested so-called passivates make a worse job than water.
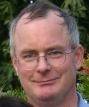
Geoff Crowley
Crithwood Ltd.
Westfield, Scotland, UK
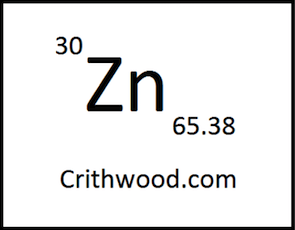
December 3, 2015
A Guide to process Selection & Galvanizing Practice"
by M. J. Hornsby
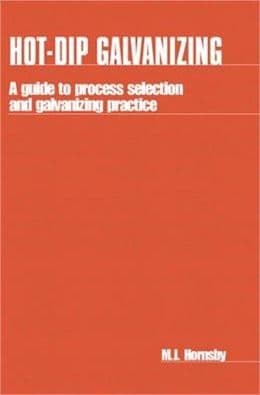
on eBay or Amazon
or AbeBooks
(affil link)
Q. What should be added in galvanizing kettle with lead to prevent or lessen white rust formation? We are facing problem of rapid white rust after galvanization.
Armaghan Rauf- Lahore, Pakistan
February 25, 2016
Hi Armaghan. As you see, we added your query to a long and detailed thread on the subject. Please review it and follow up if you have remaining questions. Thanks!
Regards,
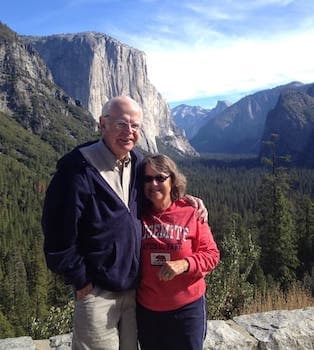
Ted Mooney, P.E. RET
Striving to live Aloha
(Ted is available for instant or longterm help)
finishing.com - Pine Beach, New Jersey
Q. For Geoff Crowley
We are looking at non-chromate quenches as well and were wondering if you had any updated information or results on viable alternatives.
QC, Canada
July 19, 2017
Hi cousin Angelo! Please try to preface your question by telling us what your company is learning so far. Thanks!
Regards,
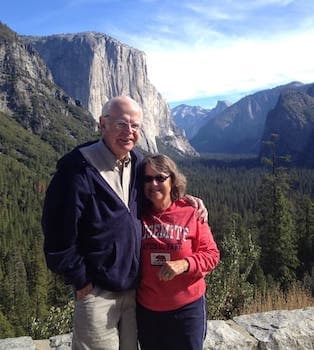
Ted Mooney, P.E. RET
Striving to live Aloha
(Ted is available for instant or longterm help)
finishing.com - Pine Beach, New Jersey
July 2017
![]() |
Q. Ted, I am afraid I am strictly here seeking knowledge. I am new to the industry. I know our technical department is working on trying to eliminate chromates from the quench process. I am looking for information that can help them in terms of alternative materials. I am not sure if this is the right forum for that. Hopefully someone can point me in the right direction. Angelo P. [returning]QC, Canada July 21, 2017
We'd like for your technical department to SHARE in this exchange of info, even if it's only: "We've read that ...", or "We've found an article that claims ...", or "We tried ... ", or "We're not sure, but we think ..." If regular helpers like Geoff find instead that this public forum is devolving into a unidirectional technology transfer where he not only shares his company's hard-won knowledge with his international competitors, but they come back requesting a progress report on what he has learned, while being unwilling to offer anything whatsoever in return, we surely won't be able to expect his or anyone's continuing help :-( I didn't think we were asking much, but I went back and removed your name, company name & city as it's our intent to share aloha, not to try to embarrass. Regards and stay well, ![]() Ted Mooney, P.E. RET Striving to live Aloha (Ted is available for instant or longterm help) finishing.com - Pine Beach, New Jersey July 2017 |
A. Sir:
At one time I thought that calcium chloride in the flux (from hard water, or contaminated flux) was a cause of white rust. Now I am investigating aluminum chloride in the flux as a source of white rust.
To reduce white rust, I recommend a metallic aluminum level in the molten zinc to be no higher than 0.0005%.
Regards,
Galvanizing Consultant - Hot Springs, South Dakota
July 23, 2017
Q. Hi, I am Niranjan Kumar From FOWLER WESTRUP India PVT LTD.
WE Have Found the White rust/Stain On Galvanized Sheets. I have read the comments, Some of them suggested to clean the surface with vinegar
⇦in bulk on
eBay
or
Amazon [affil link] , I think it is one of the good suggestions. But in the view of preventive action, shall we use more galvanized Coating thickness sheet (means 120 gsm or More GSM sheet can protect from moisturized condition)? Please suggest if this idea works or not?
FOWLER WESTRUP India PVT LTD - Malur,Karnataka, India
September 16, 2017
A. In my experience there is no proven alternative to chrome trioxide passivation to help delay white rust if the process is also a quench from hot steel. There are alternatives for treating cold or cool, but they don't work with hot steel straight out fo the zinc. All galvanizing will get white rust is stored wet and touching each other. It can be prevented totally by either keeping the galv steel dry, or separating it from each other by at least an inch (25mm).
Adjusting the thickness of the coating doesn't solve this issue.
The chromate passivation doesn't give everlasting protection, but at the right strength and temperature (these factors are interdependent), it will delay the onset for 6-8 weeks. That's usually long enough to get the material put into service wherever it is to end up.
Weak acids can be used carefully to clean white rusted steel, and citric acid
⇦ on
eBay
or
Amazon [affil link] works best in my experience. There are some proprietary brand liquids to use for this purpose in the UK, but they're essentially citric acid and detergent.
I agree with Tom (above) that excess aluminium dissolved in the zinc makes matters worse, but I'd say about <0.001% as a limit. Certainly above that level there's a bigger problem.
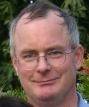
Geoff Crowley
Crithwood Ltd.
Westfield, Scotland, UK
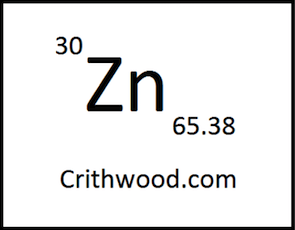
September 20, 2017
A. Hello,
I've found that alkali metal silicate based compositions ('water glass'
⇦ on
eBay or
Amazon [affil link]
) are effective in white rust inhibition of hot dip galvanized steel.
In case of quenching too-hot galvanized steel(~450 °C) in silicate containing quenching water, gloss reduction problem was happened because of too much deposition of silicate compounds. But there is no problem under 300 °C.
So I think that it will be possible to apply if there is another quenching tank.
Process : Hot dip galvanizing -> quench in water -> passivation in silicate containing water.
- Pohang, Gyeongbuk, South Korea
December 13, 2017
A. Sir:
Sodium or potassium silicate are also known as water glass. What happens when it rains? Water glass is fully soluble in water. I believe this has been tried before without good results.
Regards,
Galvanizing Consultant - Hot Springs, South Dakota
December 21, 2017
December 26, 2017
Hello, Dr. Thomas H. Cook.
You are right. Sodium or potassium silicate are water soluble, so it is not easy to get water resistant silicate layers for good corrosion protection.
However, water resistant silicate layer can be obtained with heating (losing water molecules in silicate layer) and additive.
I think that hot galvanized steel surface is helpful to form water resistant layer. And as you know, silicate layer is hydrophillic, so it is susceptible to water penetration. More water resistant layer can be obtained by converting hydrophillic layers to hydrophobic ones with additive (potassium methyl siliconate).
Refer to my journal paper "Synergistic effect of potassium metal siliconate on silicate conversion coating for corrosion protection of galvanized steel"
by Jaekyu Min, Ji Hoon Park, Hong-Kyun Sohn, Jong Myung Park.
And also, in my experience, the other additives (phosphorous and titanium complex) are helpful to increase corrosion protection.
- Pohang, Gyeongbuk, South Korea
Q. Sir:
What is the reference to your journal article? Is this treatment commercial? How many tanks are involved, and what is the cost?
Regards,
Galvanizing Consultant - Hot Springs South Dakota USA
December 26, 2017
----
Ed. note: We hope Jaekyu returns to answer those questions. His article was in Journal of Industrial & Engineering Chemistry, Vol. 18, Issue 2, March 2012. It seems it can only be reached through an Elsevier paywall, which would exclude most readers of this free public forum from participating in a discussion of it; we're not printing the URL, but you can find it by searching by article title with Google :-)
December 27, 2017
Thank you for your interest.
1. "What is the reference to your journal article?"
- I'm sorry I'm not good at English. I don't know exact meaning of the question. Do you mean the reference journal?
I can't find a way to upload the file, so I will send my journal article to you by email (mooney@finishing.com)
2. Is this treatment commercial?
- I have tried to commercialize, but there are no needs in Korea yet. If anyone want to apply this passivation treatment, I can provide the information.
3. How many tanks are involved?
- Passivation treatment needs just one water tank which contains silicate compound and additives. But it should be cooled down (under 300 °C) before passivation treatment. So it needs another cooling (quenching) tank or cooling system.
And also, you can apply the treatment by spraying after water quenching.
4. What is the cost?
- As you know, alkali metal silicate compounds are very cheap materials compared to other Cr-free alternatives (Ce, Mo, Zr, Ti and so on). I don't know exact prices of chemical compounds in your country. In case of Korea, the price of raw materials for concentrated passivation solution may be about 0.6~0.8 dollar per kg. Although the ability of corrosion protection depends on concentration of passivation solution and process conditions, in my experience, it needs about 1~3wt% concentration in order to obtain the effect equal to chromate passivation.
Chemipia Co. - Pohang, Gyeongbuk, South Korea
Q. I have galvanized sheet steel (4'x8') stacked in 5000 lb bundles.
Is it possible to attach a sacrificial anode (e.g., magnesium based?) to the bundle to minimize/prevent white rust?
Ideally, this material is stored in a temp/moisture controlled environment.
However, I would like to store the material in an uncontrolled, covered environment and ideally store outside without cover.
- Fargo, North Dakota, USA
March 2, 2018
A. Practically if the Hot dip galvanised material has been passivated by proper dichromating you can stack it in the open.
Vishal AgarwalINDANA STEEL PVT LTD - Mumbai, Maharashtra, India
March 19, 2018
Q. Hi. We are having huge issues with white rust on our galvanised products. This only shows once we have etch coat primed with thinners based oxide primer and painted with acrylic paint on the galvanised steel fencing. My question is: how do we remove the white rust on the painted product?
Deirdre
- Cape Town, South Africa
March 31, 2018
A. You can remove white rust off galvanized steel using a weak citric acid solution.
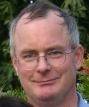
Geoff Crowley
Crithwood Ltd.
Westfield, Scotland, UK
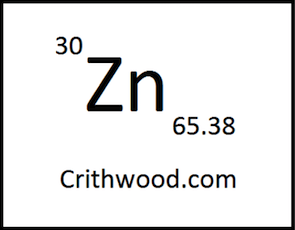
May 4, 2018
Q. Dear Sir,
We are a manufacturer of Guardrails and faced with white rust after hot-dip-galvanizing of our product.
We learned of Chromate Passivation at quenching tank that will prevent white rust. What chemical should we add to the quenching tank to avoid these white rust.
Prestar, Guardrail manufacturer - Selangor, Malaysia.
June 14, 2019
A. Dear Mr Toh,
After Hot Dip Galvanizing the zinc forms a hard layer of Zinc Carbonate that is a corrosion inhibitor.
I would like to believe that the natural carbonate layer formation will be long term durable vis à vis a chromate layer.
Guys here too use proprietary chromate dips after galvanizing to make the blue look pretty. Choose what works for your business.
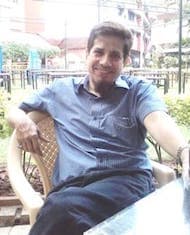
Khozem Vahaanwala
Saify Ind

Bengaluru, India
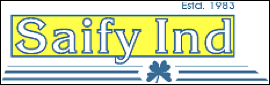
June 15, 2019
June 24, 2021
Q. Hello!
A Builder is asking me to figure out some problems they are having with some old Zinc Cladding on an abandoned housing estate. They would like to restore the original appearance of the Zinc. We have some spare cladding for experiments.
Here is a photo of the problem.
That suggested a mild acid - but I would like to hear what the people on the famous Finishing.com have to say since I don't know much about Zinc.
Thank you! All suggestions appreciated. The Internaut
- Cork, Ireland
Tip: This forum was created to help build camaraderie through sharing tips, opinions, pics & personalities.
The operator & those readers who want that might not engage with anonymous posters.
A. Hi, TA. My bet is on a very mild case of white rust, but you could try a salt remover first.
I'm not sure what makes those soffits prone to white rust, maybe just the fact that they're not ventilated, probably attract condensation, and are out of the sun, perhaps keeping them wet too much of the time.
Tom Rochester suggests that naval jelly (phosphoric acid treatment) may be the best approach for white rust, and he's probably right, but if the resulting appearance doesn't meet your builder's desires, sulfamic acid ⇦ on eBay or Amazon [affil link] (an ingredient in many copper cleaners) might leave no residue and generate an appearance more to his liking.
Luck & Regards,
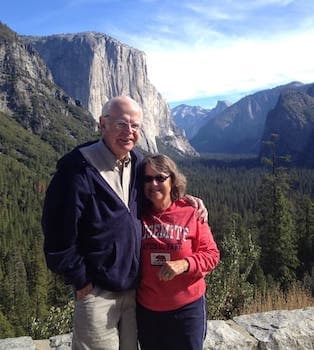
Ted Mooney, P.E. RET
Striving to live Aloha
(Ted is available for instant or longterm help)
finishing.com - Pine Beach, New Jersey
June 2021
Q, A, or Comment on THIS thread -or- Start a NEW Thread