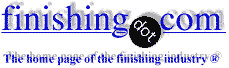
-----
Copper pyrophosphate plating bath Q&A's
Quickstart (no readers left behind):
Although copper plating can be done with a very simple & effective copper sulphate "bright acid copper" process, this can' t be used directly on steel, aluminum, or zinc components because copper is more 'noble' than those metals and will spontaneously "immersion deposit" on them, with poor adhesion.
The traditional answer is to do an initial copper strike in a cyanide copper plating bath. But cyanide is a very dangerous and highly regulated material. One alternative is to use a copper pyrophosphate, or other proprietary non-cyanide copper plating process.
Q. I would like to contact someone who uses pyrophosphate copper process on regular basis. I'm particularly interested in Enthone-OMI's "CUPRAL" and Canning's "SUPER PYROBRITE" because only these two companies offer that technology on my domestic market.
Thank you
Adam Wittmanngalwanotechnika - Poznan, Poland
1998
A. Dear Adam
For a critical job it was necessary to use copper pyrophosphate and no supplier offered that in India. So I formulated the bath from off shelf chemicals, and converting ortho phosphate to pyro phosphate. If you want to go to those root levels, I can dig up my notes.
Yashawant Devalelectroplaters - Pune, Mah., India
Current efficiency of copper pyrophosphate plating
Q. I have a question regarding current efficiency of copper pyrophosphate bath. From literature, the efficiency should be 100%. I got a commercial bath and tried to measure its current efficiency using a pre-weighed copper foil. The c.d. was 20 mA/cm2. The temp of the bath was 50 °C. From the weight difference before and after plating, the calculated efficiency was only 74%. If this number were true, I would see bubbles out from the cathode. I did several tests and got same results. I can not figure out what the problem is. I also tested the current efficiency of one commercial acid copper bath using the same method. The result was close 100%. Any suggestions would be appreciated.
by N. Kanani
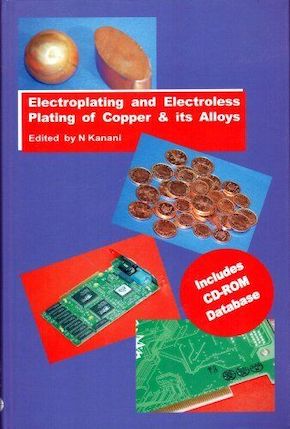
on eBay or Amazon
or AbeBooks
(affil link)
- Torrance, California, USA
2000
A. 74% is actually pretty good for Pyro.
"Current efficiency" includes two terms. Anode efficiency and Cathode efficiency. Instead of Hydrogen at the cathode you may see Oxygen at the anode.
For good operation you should see neither.
In many solutions (Electroless Copper comes to mind) gases like Hydrogen can bump around in solution for a while before bubbles begin to form.
PWBs - Alberta Canada
2004
A. We, too, have recently checked the cathode efficiency of a pyrophosphate copper bath, and found it to be close to 80%. We are also noticing an increase in the specific gravity of the solution, that may indicate that the copper concentration in it is rising due to the difference between the anode (presumably 100%) and cathode efficiencies.
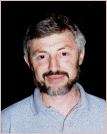

"PlaterB" Berl Stein
NiCoForm, Inc.

Rochester, New York
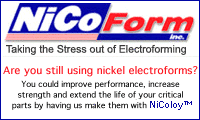
December 9, 2010
Q. We are plating aluminum parts (nickel, acid copper, nickel, chrome) . We use only non-cyanide baths. We plate zinc parts and for that reason we made up a pyrophosphate copper bath. (pH=8,5 ; Temp=55 grad C ; I=1 A/dm2 ; P2O7:Cu=7:1). At the beginning everything was great. We were doing pyrophosphate copper strike then acid copper. After 3 months, when we plated in the pyrophosphate copper bath, the copper layer falls off the zinc (layer has micro holes). In the acid copper bath under the layer rise blisters. Maybe in the bath is too much orthophosphates? How to remove it? Could you help me solve this problem. Any suggestions would be greatly appreciated.
Waldemar TomankiewiczMetal finishing - Cracow, Malopolska, Poland
2003
A. Hi Waldermar,
To lower the ortophosphite content is only one way to do it that's is to discarded to reduce its concentration in the solution. If you have a high contamination of zinc that will show by producing brassy looking deposit and should be dummied out at medium current density.
Regards,
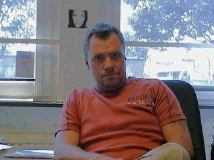
Anders Sundman
4th Generation Surface Engineering
Consultant - Arvika,
Sweden
Q. What chemicals can we use to lower the pH of the copper pyrophosphate plating bath? Is Polyphosphoric acid ok?
Steven AngStudent - Singapore
2003
A. We don't use the term polyphosphoric. If it means pyrophosphoric, is O.K.
Guillermo MarrufoMonterrey, NL, Mexico
Copper pyrophosphate or non-cyanide copper as heat treatment maskant
Q. I am looking for information about non-cyanide copper plating for use as a heat treat maskant and / or info on a an alternative non-hazardous maskant for heat treat applications (i.e., selective carburization, nitriding). Anyone who can help or point me in the right direction would be greatly appreciated.
Thanks,
helicopters - Haltom City, Texas
2003
A. Copper pyrophosphate and proprietary baths are probably the only cyanide-free approaches.
adv.
Finishing.com's supporting advertiser EPI / Electrochemical Products Inc. [a finishing.com supporting advertiser] is one supplier.
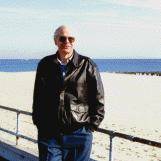
Ted Mooney, P.E.
Striving to live Aloha
finishing.com - Pine Beach, New Jersey
A. Pyrophosphate copper :
copper pyrophosphate.......... 110 gm
potassium pyrophosphate...... 400 gm
citric acid
⇦ on
eBay
or
Amazon [affil links] .................. 10 gm
water........................1 lit
pH 8,5 -temp.50 C, 5 A/dm2
Tartaric copper (19.century):
add copper carbonate
⇦ on
eBay
or
Amazon [affil links]
to solution of potassium tartrate( 100 gm/lit.water), until some carbonate remained undissolved, then add potassium carbonate to pH 10
- Cerovski vrh Croatia
A. A variety of alkaline non-cyanide copper baths are available from suppliers. Each manufacturer has baths with different properties in plating or waste treatment. Pyrophosphate baths are outdated technology unless you are trying for a "home brew".
Gene Packmanprocess supplier - Great Neck, New York
A. You can use ceramic or enamel coating [as heat treatment maskant].
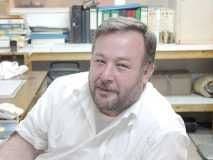
Khair Shishani
aircraft maintenance - Al Ain, UAE
Q. Hi!
I would like to ask how to maintain pH on a PyroCopper Bath? Our pH trend is increasing everyday and right now we are using Sulfuric Acid to decrease its pH. Experts said that pH of this bath should be decreasing in the long run...But why is it that every day pH is still increasing on our side? What are the possible causes?
Our pH parameter is 8.2 - 9.2...usual pH everyday reach 9.3 to 9.5.
Thanks ahead.
Diana Fe Espinosa
Philippines
plating service employee - Philippines
November 4, 2011
A. Hi Diana,
pH increase could be due to hydrolysis of water at cathode instead of copper ions reduce to copper metal:
2e-
2H2O ------> H2 (hydrogen gas) + 2OH-
You may verify cathode efficiency by:
1. Observe if significant gassing around cathode;
2. Observe if bath solution copper concentration is climbing up (anode dissolution more than cathode plate out);
3. Perform weight gain test to compare actual copper deposit weight vs. theoretical weight under Faradays Law.
Other than that, drag in of alkaline species may be a reason as well.
Regards,
David
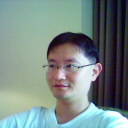
David Shiu
- Singapore
A. Hi,
In the early days of Copper Pyrophosphate plating, we used and recommended "Tetraphosphoric acid". It was made by mixing water and phosphorus pentoxide to give a polyphosphoric containing 4 P atoms - H6 P4 O13. In reality it contained a mixture of polyphosphates with an average P of 4. It worked very well and rapidly became pyrophosphate (P2) in the plating bath.
We soon abandoned it in favour of of the cheaper and readily available sulfuric acid. In moderate quantities sulphate has no adverse effects. Ultimately it begins to lower the maximum current density as it adds to viscosity of the bath.
Your rate of pH rise is too high and the question you should have asked is how to prevent it. pH rises in pyro baths because of excessive anode area. There are several drawbacks, the need to add acid being one of them. Others are:
1) lowering of the optimum P207:Cu ratio
2) If you are using brightener, it will precipitate on the sludge which forms on the anodes at LCD.
Controlling anode area is the is key to running a copper pyro bath. The pH should slowly rise, say 0.2 - 0.3 units per week. There are also disadvantages with falling pH.
My advice is to get the anode area down to meet the above condition. When the anode current density is correct, the anodes should have a clean, pink or slightly dusty appearance. Anode CD too low gives a brown sludge and too high, a bright electropolished appearance.
Well, there's some advice - whether you want it or not!
Harry
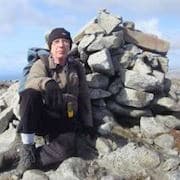
Harry Parkes
- Birmingham, UK
? Is the volume of your acid solution staying constant?
Scott Hope- Chicago, Illinois, USA
A. I run a Copper Pyrophosphate Plating Bath. It's small, about 150 gallons. My additives (with each load) is a brightener and ammonium hydroxide. Both of these items have a higher pH than my bath. So with each load, my bath pH increases. However my DI water is a bit of a lower pH to my bath, and so this tends to even out. Once a week I usually add a solution of 10% Sulfuric Acid to 90% DI Water. This solution is generally (for my bath) made up in a 3L bottle and poured into our sump tank. This generally drops the pH from 8.9 (which is the highest I will allow it to go), to 8.6. I sometimes have to add 2 x 3L bottles, depending on my concentration amounts.
Hope this helps.
- Camarillo, California
A. TO LOWER pH USE POLYPHOSPHORIC ACID (THE TERM POLY PHOSPHORIC ACID REF. TO CONC. GRADES OF PHOSPHORIC ACID ABOVE 95%). TO RAISE pH USE 10% POTASSIUM HYDROXIDE.
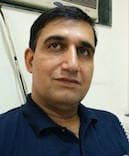
Ajay Raina
Ludhiana, Punjab, India
What chemical is used to lower pH of copper pyrophosphate bath
Q. I am running into a problem where my records (copper blanks) are getting a pattern of tiny dots all over them as if pits are trying to form but are then covered up by the brightener/leveler (py-61-H) during plating. I noticed that the anodes are getting a dark brown to black film on them.
I read a lot of posts about how this black film is normal in acid copper plating but have not been able to find information if this is normal in pyrophosphate copper plating.
The rest of my process is the same so I'm not sure what is causing the film or if this is related to the little dots of roughness all over the blanks.
Is there something I should be doing to eliminate this film? My anodes usually have a light colored film on them.
Thanks
Ben
- LA, California
June 5, 2012
A. Hi Ben.
We appended your inquiry to this thread because Harry Parkes' response of November 10, 2011 seems to directly answer your question. Good luck.
Regards,
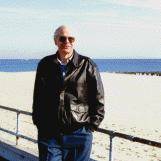
Ted Mooney, P.E.
Striving to live Aloha
finishing.com - Pine Beach, New Jersey
A. I would suggest taking a look at your part while it is being plated if possible. Find out at what step of the process these dots are occurring and if they are occurring consistently in the same area at the same part of the process.
From what you said, it appears that your part goes in not cleaned fully as the dots appear at the beginning and are covered up by your brightener? (If I understand you correctly).
Items to check would be:
1. Are there dots before the part goes in? Can you check with a scope before putting it in the bath?
2. If they are not there, look at the part as it goes through the process and see at which point the dots start appearing and narrow that problem down
3. Are you using a consistent substrate? If you were not getting dots before, but are getting dots now, did you change the type of substrate you were using?
4. It looks like you could have a chemical imbalance, possibly too much of one thing, too little of another? Can you have it analyzed by a lab?
5. Are you putting in too much additive (PT61H or Ammonia) or too little of it?
That's my two cents on the subject.
- Juarez, Mexico
How to remove iron from copper pyrophosphate plating bath
Q. How do I go about removing iron from a copper pyro electroplating bath?
Kory Rodenhiser- Bridgewater,NS, Canada
August 19, 2014
A. I don't think that there is a practical method to remove iron from a copper pyrophosphate bath. In many years of involvement with copper pyro I can't recall a problem cause by iron. Except that it is important to allow sufficient potassium pyrophosphate to complex the iron as well as the copper. Think in terms of total metal: pyrophosphate rather than just copper.
May I ask what problems you have?
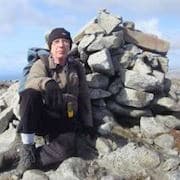
Harry Parkes
- Birmingham, UK
Q. Copper Pyrophosphate Delaminating from Strike
Hi Everyone, I am having some difficulties with my copper pyrophosphate automated copper plating line. The parts plated are high grade aerospace materials.
On around 10% of the components that are plated using the line we are witnessing separation between the strike and plate layers on the components after they have been stoved at 195 °C for 2 hours.
We have tried disposing of all of the rinsing baths between the strike bath and the plating baths as well as replacing the sulfuric acid dip we use prior to plating but there are still issues with plate peeling from the strike. We most recently tried replacing the strike bath this weekend just gone but we have still had problems. We have also given all of our tooling and plating stations a good thorough clean on all contact points.
There is no consistent pattern on day of the week, tooling used, size of component, plating bath the parts have gone in. Although certain part numbers do seem to be more consistently affected. Has anyone got nay suggestions for anything else I can try to get to the root cause of the problem?
Thanks,
Andrew
Andrew Amor
- Yeovil, England
April 15, 2021
A. Sounds like the copper is getting passive and you need to activate the surface. You should look at a mild copper etch after the copper and before the next plating solution.
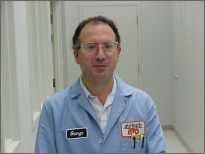
George Shahin
Atotech - Rock Hill, South Carolina
Hi George,
Thank you for the advise. We do currently use a sulfuric acid dip between striking and plating which has always historically worked successfully.
As an update we were able to isolate the problem as being caused by our internal plating anodes. We are currently trying to work out what about them is causing this to take place as they have been recently calibrated.
Thanks,
Andrew
- Yeovil England
Readers may also be interested in these related threads:
• Topic #540/61 "Copper Pyrophosphate Plating: Orthophosphate & potassium pyrophosphate in bath"
• Topic #353/61 "Non-cyanide copper strike/plating process problems & solutions"
Q, A, or Comment on THIS thread -or- Start a NEW Thread