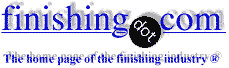
-----
Nickel plating zamac die castings for bathroom fixtures

Quickstart:
Zamac (Zinc - Aluminum - Magnesium - And - Kupfer, i.e., copper) is a family of alloys widely used for die casting. Zamac-3 is the most commonly plated one.
Zamac castings are difficult to plate for a number of reasons, including the castings often not being of sufficient quality. Please read on ...
Q. Hello,
We do Copper, Nickel and Chrome plating over Zamak-3 components specific to bathroom industry. Our customers need aesthetically superior products. Each component is divided in classification like A/B/C
⇦ huh? . Each have different tolerance for pit marks, for example B surface can have only 3-4 pit marks all over the surface.
To achieve this we do buffing after doing 40 mins of acid copper plating and then do Ni-Cr plating, in which rejection rate due to pitting may reach up to 18-30%. We want to reduce this over-processing and rejection rate.
Thank you for reading.
Management Employee - Aligarh, UP, India
May 6, 2025
A. Hi Shanu. You came here for answers, and you'll hopefully get them, but getting free help sometimes means putting up with a little bloviating first, which I'm prompted to do because I find tighter/laxer standards for A/B/C surfaces to sometimes be largely nonsense.
by Safranek & Brooman
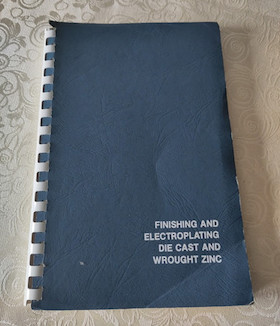
on eBay or Amazon
or AbeBooks
(affil link)
The explanation was that the customer was the special assistant to a V.P. of a major corporation; the V.P. had come up with the 'brilliant' idea of Ni-Cr plating these formerly powder coated parts for a silver anniversary edition ... so the parts had to be used to save his boss from looking foolish, although the quality of the castings was way too low for successful plating. As you can appreciate, the special assistant was soon calling the entire part a C surface, insisting that quality didn't matter, while the shop manager was deciding one by one which parts he would allow to be shipped 🙂
Luck & Regards,
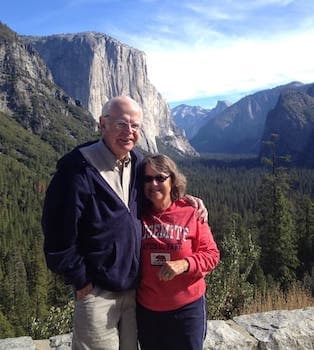
Ted Mooney, P.E. RET
Striving to live Aloha
(Ted can offer longterm or instant help)
finishing.com - Pine Beach, New Jersey
Q. Hi Ted,
First of all thank you for responding to my query in such a quick time, I do understand the need of quality casting to do good plating and also need to good surface finishing. And we are constantly working to improve it.
Trying to answer your questions in the best way I can
1) We try to maintain sufficient wetting agent and air agitation
2) Yes copper is pitted before buffing
3) Surface tension in Nickel tank is ___
4) No these are not gas pits, it does not have a tail.
Below information is from our internal discussion (we maybe completely wrong)
1) We think that after copper buffing we maybe just covering pits for the naked eyes, and they are still there, after nickel plating they become way more visible.
2) there is slight wavy formation over copper after copper buffing, our team is loading nickel tanks with too much organic in trying to provide leveling and hiding it. which in turn creates issues in the long turn.
- UP India
May 9, 2025
A. Shanu Garg
You have to run hull cell panel to duplicate the problem, Check Nickel bath pH, make sure it's within range, Make sure nickel solution surface tension is below 40 dynes. Using wetting agent to lower the surface tension.
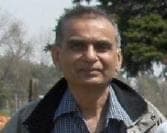
Popatbhai B. Patel
electroplating consultant - Roseville, Michigan
June 25, 2025
A. Shanu Garg,
The pits look likes round in shape. make sure no roughness instead of pits.
The nickel bath keeps surface tension <40 dyne/cm2, use wetting agent. Check boric acid concentration between 5-6 oz/gal
The chrome surface tension < 40 dyne/cm2.
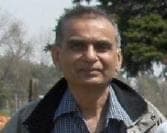
Popatbhai B. Patel
electroplating consultant - Roseville, Michigan
July 7, 2025
⇩ Related postings, oldest first ⇩
Q. Sir,
please let me have the process cycle for plating zinc die casting items with Nickel as I am making bathroom fittings with brass presently and want to shift to zinc die castings for reducing the cost of the product. Also let me know the implications involved in this process.
Thanking you, Kashinath.
Nishangi . Kashinathmaking bath room fittings. - Hyderabad, India
2003
A. Hi, Kashinath.
Ugh! Replacing brass with diecast for bathroom fixtures is a project I can't put my heart into :-(
I've always loved chrome plated brass because it ages so gracefully, and I hate diecast bathroom fixtures because, instead of aging gracefully like brass, they become pockmarked with crusty white volcanos. 🙂
Anyway, the essential elements of plating die castings are: assuring that 100% of the castings are plating quality (consistent finish, non porous, completely free of even the tiniest cold-shuts), then properly mechanically finished; your brass pretreatment cycle will need only minor adjustments; then cyanide copper plate; then acid copper plate; then nickel-chrome plate as at present.
Best of luck!
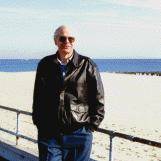
Ted Mooney, P.E.
Striving to live Aloha
(Ted can offer longterm or instant help)
finishing.com - Pine Beach, New Jersey
A. It is a very difficult task to use zinc-diecast components in the production of bathroom fittings. The quality of the castings will need to be very good to start with, and the plating quality will also have to be very good to survive the contact with water/humidity. Here in the U.K. we do not find the need to use an acid copper stage. I would suggest a copper cyanide plate of at least 12.5 microns (absolute minimum) and then a high corrosion resistant electroless nickel. This nickel should again be plated to an absolute minimum thickness of 12.5 microns. It will be quite an achievement though to compete with the quality of plated brass components!
Joseph Garnertrade platers - Corby, Northamptonshire, England, U.K.
Thanks for providing backup to my assessment, Joseph. I have seen older diecast parts used in bathrooms many times and they are always miserable and full of white mini-volcano pits. Yes, it's theoretically possible to plate the parts so well that nothing will happen to them for a fair amount of time. But the point will always come when the zinc is absolutely pit-ugly, whereas the brass would have aged gracefully, gradually revealing its smooth golden color through the thinning plating.
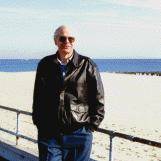
Ted Mooney, P.E.
Striving to live Aloha
(Ted can offer longterm or instant help)
finishing.com - Pine Beach, New Jersey
⇦ Tip: Readers want to learn from your situation;
so some readers skip abstract questions.
Q. Hi. Please, I want the whole process of nickel plating on zinc die castings. Thanks. I await your mail.
hussain iqbalengineering - lahore Punjab Pakistan
June 15, 2011
(affil links)
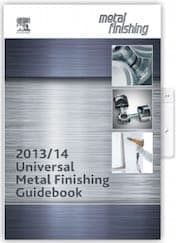
free pdf is currently available from academia.edu
A. Hi, cousin Hussain.
Please introduce yourself and your full situation. We've appended your question to a thread that will answer it if you are an experienced plater, but please see if a library or a company in your area can offer access to the Metal Finishing Guidebook ⇨
or the Electroplating Engineering Handbook to flesh out each of those broad process steps.
Myself and the other readers are always happy to help to try to steer a poster in the right direction, or to address a highly specific issue a poster is encountering, but we wouldn't want to mislead readers into believing that electroplating is an art & science that can be covered in a paragraph or two -- it will take you years to become a proficient plater of die castings.
Regards,
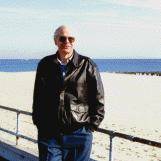
Ted Mooney, P.E.
Striving to live Aloha
(Ted can offer longterm or instant help)
finishing.com - Pine Beach, New Jersey
Nickel plating on zinc alloy (ZAMAK-5)
Q. Hi, I am a running a plating line on zamak alloy for a long time, but I am facing pitting while the surface is flat. How to remove the pitting.
The plating line includes ultrasonic cleaning, followed by cyanide copper and acid copper.
Please guide me on this.
Wish I had come here earlier. TIA.
- India
July 4, 2019
A. Hi Harit. Sorry, but I don't understand exactly what you mean by "while the surface is flat". Do you mean all surfaces on the component which is not curved? Or are you referring to the component's orientation in the plating tank (horizontal vs. vertical / top surface vs. bottom surface)? Successful plating of diecastings is difficult, and if we misunderstand the question, it's hard to be of much help, so please send photos and further explanation.
Have you carefully examined the surface before plating to insure absence of cold shuts
⇦ huh? ?
Please try to plate a Hull Cell
⇦ huh?
panel so you at least know the condition of the plating solution. Gas pits
⇦ huh? sound more likely on a flat surface than on rounded ones. Do you know the surface tension in the nickel plating bath? What do the pits look like under low magnification -- bright and hemispherical, or deep and ragged?
Regards,
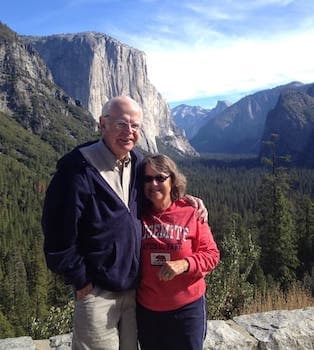
Ted Mooney, P.E. RET
Striving to live Aloha
(Ted can offer longterm or instant help)
finishing.com - Pine Beach, New Jersey
Q, A, or Comment on THIS thread -or- Start a NEW Thread