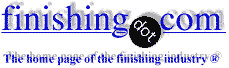

this text gets replaced with bannerText
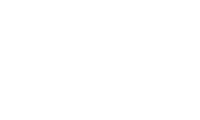
Jump to elated thread:
• or continue with -----:
Stripping tin plating from copper
Q. Hello All,
My name is Jayden. I am a new process engineer for a PCB shop in California. My question is how could I control the normality of stripping solution to be in spec. I have a difficult time troubleshooting the tin resist stripper issue. The normality is always at a higher value than the vendor recommendation of 4 ml/l.
The chemical solution used to strip the panel is TSN-3000 nitric acid through ChemCut-CC8000 stripping systems. A dosing controller based on panel count is applied and adjusted at 5 panels per 30 seconds. I have tried many ways to fix the problem such as cleaning the tank, cleaning the spray nozzles, adjusting the conveyor speed based on the weight loss, keeping the spray pressure at 30 PSI and bath temperature at 85 °F, dumping and remaking a new bath, adjusting the dosing controller. When changing a new bath, the specific gravity and normality of solution are in spec for 2 days, but increasingly out of spec as 4.3 ml/l for normality after all.
I really get stuck in solving the issue, so please help to support me in overcoming this headache problem.
I greatly appreciate your help.
- San Jose-California
January 24, 2022
? How are you measuring/calculating the normality? If it's based on the specific gravity of the solution, the calculated values are going to rise as tin enters the solution.
Joshua MeisnerProcess Engineer - Flushing, New York
⇩ Related postings, oldest first ⇩
Q. Any information on stripping bright acid tin deposits from pure copper. Have tried MSA and MSA peroxide, but very slow. Any ideas gratefully received
Tom Kinsman- Burnley, Lancashire, UK
2000
A. You might try this: 120 g/l NaOH, make the part anodic at 6 VDC. You can vary the temperature to control the rate, but be aware that if you go too hot the copper might be attacked.
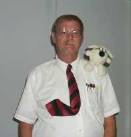
James Totter, CEF
- Tallahassee, Florida
A. Hot Concentrated HCl. I thought tin was very difficult to dissolve, but this works a treat!
Ian Brookeuniversity - Glasgow, Scotland
A. Tom, My favorite stripper for tin off copper is a 50-50 mixture of Nitric and Muriatic Acids. You have to be extremely careful, and use exhaust ventilation, as it will fume like crazy. Also you have to be really careful with it or it will boil from the top of the container. Be sure to wear an apron ⇦ on eBay or Amazon [affil link] and face shield ⇦ on eBay or Amazon [affil link] . It does not leave any noticeable etching and is really fast.
Phil Pace- Tulsa, Oklahoma
A. Tom, we found that a mixture of 4-6 oz/gal of Ammonium Bifluoride and 10% by volume of Hydrogen Peroxide works well.
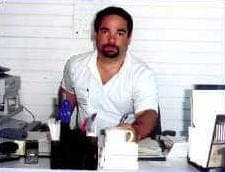
Jim Conner
Mabank, Texas USA
Q. Nowadays, our stripping chemical uses fluoboric acid to strip Tin from Copper and alloy material. Copper material can be stripped many times.
But this acid dissolves tin and also alloy material so it cannot be used to strip more than once. Do you have an idea what chemical can strip tin from alloy 42 material without dissolving the alloy material ?
Thank you
electronics - Lobam, Riau Island, Indonesia
2003
A. Try an alkaline strip. Makeup a strip with 6-8 oz/gal strip aid with 10-12 oz/gal caustic soda ⇦liquid caustic soda in bulk on Amazon [affil link] . Temperature 120-160 F.
Mark C. Reppa- Plymouth, Michigan
A. Another alkaline approach is to use caustic soda ⇦liquid caustic soda in bulk on Amazon [affil link] 100 g/l Sodium chlorite 50 g/l at 90-100 °C Parts will be covered with a brown oxide which can be removed with HCl.
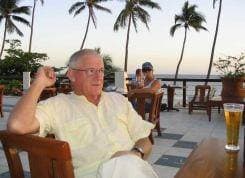
Geoffrey Whitelaw
- Port Melbourne, Australia
Q. Hi
I am trying to find a method of removing tin plating from spade crimp connectors. Reason is that we are trying to make calibration-grade voltage measurements, and there is enough thermal voltage between copper and tin to be the dominant error.
The base metal of crimped spade connectors is electrolytic copper -- which is great. Just need to get the tin plating off - including down the hole that the wire goes during crimping.
Any suggestions how to do this would be really appreciated.
Thanks and regards
Craig Sawyers- Oxford, Oxfordshire, UK
2004
A. Use a hot solution (70 °C) of 2N sodium hydroxide ⇦ on Amazon [affil link] . This will chemically dissolve the tin. However, if the tin plating has been heated, the tin will migrate into the copper to form an intermetallic. This is much more difficult to remove, but it may be possible if the tin plated copper is anodically polarised in the hot alkali. If not you may need to use an acid stripper.
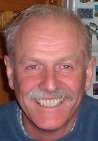
Trevor Crichton
R&D practical scientist
Chesham, Bucks, UK
A. Try 25% sulfuric acid plus 8 oz./gal copper sulphate.
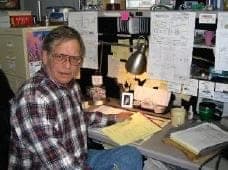
Jeffrey Holmes, CEF
Spartanburg, South Carolina
A. Following up on Trevor's advice I think you would need an oxidant added to this caustic solution if you have any thickness.
Suggest sodium chlorite (ite) say 50 g/l.
There will be an oxide film on the surface which can be removed with HCl.
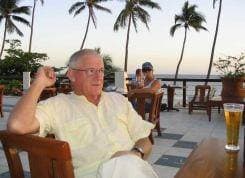
Geoffrey Whitelaw
- Port Melbourne, Australia
A. Geoff's recommendation of adding chlorite to sodium hydroxide is indeed worthwhile; it will certainly increase the dissolution rate of tin and will probably attack any intermetallic alloy. However, it is a very powerful oxidising agent and I do not know what it will do the substrate. I know that using electrolytic alkaline chlorite for detinning tin cans can result in the formation of ferrite ions from the iron. Using just sodium hydroxide will dissolve all the tin, albeit slowly, but it will not attack the substrate.
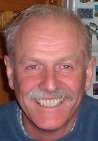
Trevor Crichton
R&D practical scientist
Chesham, Bucks, UK
2004
Q. Hi, I have been using TL-105 from Enthone. I use it to remove Tin/lead without destroying the Cu beneath.
Now, Enthone does not sells the product anymore. Do you know who sells it? Or if the TL-106 may be used?
I thank you in advance for your answer.
Kind regards,
- Porto, Portugal
May 21, 2013
A. Hello Sofia,
I would contact the supplier of the TL-106 to make sure this product would fit your needs. If not, there are many suppliers that have tin and tin - lead stripping solutions. I am not at liberty to give you a specific supplier, as it conflicts with this site's editorial standards.
Process Engineer - Mesa, Arizona, USA
A. Tom,
There are many formulations available (see Metal Finishing Guidebook). To retain the bright copper finish, you will require a stripper which contains an etch inhibitor. You can get information on product availability from any supplier.
Regards,
Mark Chasse- State College, Pennsylvania, USA
Hi. The stripping formulation info that Mark refers to is in the 2006 Edition of the Metal Finishing Guidebook, but not in the 2014 Edition -- as new articles come, old articles must go. Sorry, I don't know the most recent edition where it is still available.
Regards,
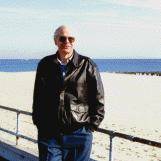
Ted Mooney, P.E.
Striving to live Aloha
(Ted can offer longterm or instant help)
finishing.com - Pine Beach, New Jersey
February 2014
Q. Regarding: "... Ammonium Bifluoride and 10% by volume of Hydrogen Peroxide works well.",
What is the concentration of hydrogen peroxide?
- 6 of october, giza, egypt
October 20, 2014
Q. I'm also looking for a way to strip Sn. The base could be copper, brass or Nickel. We currently use Peroxide and ammonium bifluoride but were exploring other options to be able to run the waste through our waste treatment system (we can't currently treat the peroxide). I'm looking for something that would be fairly fast and efficient and preferably not attack the base. Any thoughts?
Chad Stott- Indianapolis, Indiana
May 12, 2020
A. Hi Chad.
MSA, NaOH used anodically, hot HCl, 50-50 HNO3-HCl, strong NaOH used with or without chlorite added, proprietary strippers, and trying the bifluoride without the peroxide have been suggested. Trying one/some of them is probably the next step, unless you'd prefer to try to treat the peroxide (I think it decomposes fairly quickly especially at warmer temperatures
Good luck!
Luck & Regards,
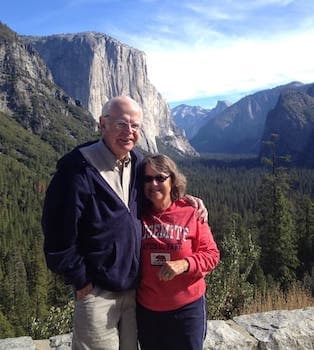
Ted Mooney, P.E. RET
Striving to live Aloha
(Ted can offer longterm or instant help)
finishing.com - Pine Beach, New Jersey
Recovering tin from electroplating sludges
Q. Hello,
We are trying a couple of methods for tin recovery from some electroplating sludge but so far it's not working very well. We are trying to determine the metal/Tin content in the sludge. I've dried it and tried smelting it in a furnace and have gotten some tin but there is still a lot of dry powder/chunky material left behind after the furnace. We've tried heating to over 1600 °F but it doesn't seem to make a difference. Is there a better way to determine the tin content of this sludge? Any help would be greatly appreciated.
- Indianapolis, Indiana
July 16, 2020
A. Hi Chad. I see some good technical articles on that:
www.sciencedirect.com/science/article/abs/pii/092134499190006A
www.researchgate.net/publication/248231667_Tin_recovery_from_an_electroplating_sludge
www.techno-preneur.net/technology/new-technologies/metallurgytechnique/tinplating_industry.html
and some patents:
patents.google.com/patent/US6110349A/en
patents.google.com/patent/CN104630826A/en
for recovery of tin from electroplating sludges but they generally seem to assume that the tin was precipitated separate from the other metals, or is at least the major constituent; other materials in your sludge interfere with the recoverability of the tin.
I'm not a chemist, but I don't think trying to smelt an electroplating sludge is either the best way to recover the metal values nor the way to analyze for them. I think dissolving the tin in the sludge to ionic form is key to both.
Another thing to think about is that tin is not generally regulated in your effluent, and that means it may make more sense to remove & recover the bulk of the tin by ion exchange, electrolytic recovery, or evaporation, rather than precipitating it only to have to redissolve it.
While we await help from someone who is knowledgeable in tin analysis, a material balance may help you estimate the tin content of the sludge. Is electroplating of the tin, or stripping of the tin the major source? You might also search the site with the term "tin recovery", where vacuum evaporation and electrolytic recovery are discussed.
Luck & Regards,
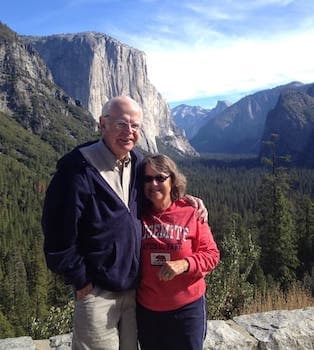
Ted Mooney, P.E. RET
Striving to live Aloha
(Ted can offer longterm or instant help)
finishing.com - Pine Beach, New Jersey
A. It would help to know more about the process that generates the tin-bearing waste to see if there is a way to either recover or minimize it at the source.
I have not done this but heard of one company that re-dissolved the tin from the sludge with hot sodium hydroxide, oxidized it to +4 tin to make an alkaline stannate bath. This can be electroplated using SS anodes to recover the tin.
- Cleveland Heights, Ohio
Q, A, or Comment on THIS thread -or- Start a NEW Thread