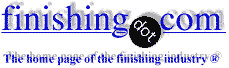
-----
Plating Cost Calculations and Comparisons
⇦ Tip: Readers want to learn from your situation;
so some readers skip abstract questions.
@Ajay Raina:HOW TO CALCULATE PLATING COST?
AMAN VERMAEMPLOYEE - AGRA, India
March 30, 2022
A. Hi Aman. Ajay already tried to answer that question, as did other contributors to this thread. But his posting was from 13 years ago, so I don't know if we can reach him about your followup.
But while we're working on that, please give us the details of the particular item you would like to know the plating cost of: size, sketch, material of substrate, what type of plating, monthly volume, etc., and give us a fighting chance ...
... because a summer internship, let alone a forum posting, would fall short of answering the general question of how to estimate plating costs. Estimators probably average several years of plating experience; I knew one fellow who was a plating foreman for ten years before he moved up to the estimator position for his plating company :-)
We can certainly try to help you with one specific part though! Thanks!
Luck & Regards,
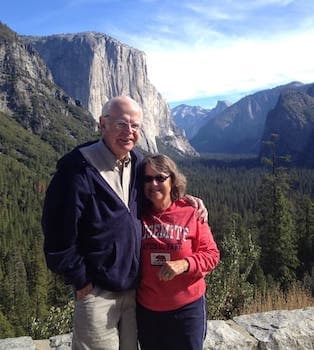
Ted Mooney, P.E. RET
Striving to live Aloha
(Ted can offer longterm or instant help)
finishing.com - Pine Beach, New Jersey
Q. Mandar, Hi good afternoon.
Can you help me to find this article? I am really interested.
Metal Finishing "Good Days and Bad Days", Part IV, Cost and pricing, by Milton Weiner.
- Matamoros, Mexico
April 30, 2023
A. Hi Abdias.
Mandar's posting was from 2000 and he probably isn't reachable. Metal Finishing magazine closed almost 10 years ago, so this will be hard to find. And ScienceDirect does not list this particular article, indicating that it was probably from before 1995 and isn't digitized anywhere. If you can find a library that has the issues of Metal Finishing from 1995 on back, you might find it.
Luck & Regards,
Ted Mooney, P.E. RET
Striving to live Aloha
(Ted can offer longterm or instant help)
finishing.com - Pine Beach, New Jersey
Q. Bad luck. Mr. Mooney, do you know of another article that will help me on costing/calculation for plating?
Regards!
- Matamoros, Mexico
May 3, 2023
A. Hi. Sorry but I don't, and I've never seen an estimating book or training course. If you want a price on a particular part, you can send it out for quotes, of course.
As in most industries, labor cost is usually a major driver; and if the work is processed on a major automated plating line, amortization of equipment may be another. The cost of the chemistry can vary from nearly insignificant in the case of highly customized zinc plating, to fairly substantial in the case of processes such as high production volume electroless nickel plating.
I knew one plating shop which required their estimators to have 10 years experience as a plating foreman before they were trusted to offer quotations because it can be a job with great responsibility & accountability.
But if you introduce yourself and your situation and a more specific question, with typical substrate materials, typical plating finishes, and production volumes, the readers may be able to offer at least some general guidelines.
Luck & Regards,
Ted Mooney, P.E. RET
Striving to live Aloha
(Ted can offer longterm or instant help)
finishing.com - Pine Beach, New Jersey
⇩ Related postings, oldest first ⇩
Q. Our client is an electroplater that will install a line to do "silver electroplating" and we are helping him to find the costs involved. It will be a new operation and we need to find the plating time per piece and the bath's size. I found a good deal of information at The Technical University of Denmark's web site but I am having trouble understanding the way to calculate the time per piece. Apparently it involves the use of fixed bath's sizes. I need an expert's help with this problem and any other advise that he/she can provide.
Alberto Dominguez- San Juan, Puerto Rico, USA
2000
A. There are manual calculations by which you can get the answers you need (one of the equations involves Faraday's law). There is also software. Either way, you need to think seriously about paying an equipment manufacturer or a consultant to help you get GOOD answers.
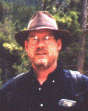
Bill Vins
microwave & cable assemblies - Mesa (what a place-a), Arizona
A. You may order a publication by Metal Finishing "Good Days and Bad Days", Part IV, Cost and pricing, by Milton Weiner. It is very useful and costs only about $10.
Mandar Sunthankar- Fort Collins, Colorado
Ed. update: Elsevier closed down Metal Finishing in 2013, and they do not seem to offer this article behind their paywall. We don't see it on line anywhere. You would need to find a library which has it. The Surface Finishers Educational Association has it, New Brunswick Plating probably does, or try worldcat.org.
A. THE AREA CALCULATION OF ARTICLE TO BE ELECTROPLATED IS REQUIRED TO BY THE READER. WHICH IS THE AREA TO BE TAKEN FOR COST CALCULATION
MUKUL VAIDYA- PUNE, MAHATASHTRA, INDIA
Multiple threads merged: please forgive chronology errors and repetition 🙂
Q. Hello,
I am a technical writer at an engineering company. My assignment is to write a comparison of plating methods, specifically the following: electro-deposited, plasma spray coating, electro-less, hard anodizing, carburizing, and PVD/CVD. I have found plenty of background material on the web, including this site. However, the last criteria requested was a relative cost comparison of these techniques, for example, anodizing is less expensive than electro-less. I realize there are many factors that affect the cost of plating, but could anyone propose a simple hierarchy of cost for these six methods?
Thanks,
Susan Wolverton- Foothill Ranch, California, USA
2003
A. Hi Susan. As you probably realize, Susan, these processes not only perform different functions but apply to different substrates. For example, anodizing applies to aluminum and not steel whereas carburizing applies to steel and not aluminum.
Further, often the processes go together. A part that is to be carburized--for example, a gear--is first selectively copper electroplated to prevent hardening in the bore area. 'Lifetime' finishes and some 'gold' finishes employ a PVD topcoat on top of electro-deposited platings. Plasma spray coating may be cost competitive with the highest quality heavy chrome plating it competes against, but could be 100 times the cost of zinc plating.
I suppose I would rank them, cheapest first, as plating (in turn ranging from zinc as cheapest through chrome plating as most expensive, hard anodizing, carburizing, electroless plating, PVD/CVD, plasma spray coating. But again, there are electroplatings that cost a lot more than hard anodizing, carburizing, or electroless plating. And there are PVD/CVD coatings that cost more than plasma spray. And probably another half-dozen "Ifs-&-and-Buts", too :-)
Best of luck,
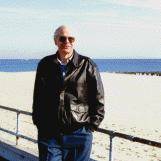
Ted Mooney, P.E.
Striving to live Aloha
(Ted can offer longterm or instant help)
finishing.com - Pine Beach, New Jersey
Q. I am looking for alternative ways assign prices to parts we plate. We currently use only part weight and use a price per pound. I thought maybe surface area plated might be more of an accurate measurement. I appreciate any thoughts.
Steve Van CleveSales Engineer - Moberly, Missouri, USA
March 6, 2009
A. Hi, Steve. Although surface area is usually a better parameter than weight, it's still not good enough. The starting point is usually to determine what a few specific parts cost you to plate -- raw materials, labor, overhead, return allowance, etc. -- and then work on figuring out why part A requires 2.7 times as much labor as part B, but half the chemicals cost of part C, etc., so that you can then estimate the cost of plating part Z.
It's not easy, but you can start by figuring out what it costs you to plate the parts you presently plate.
Our advice to buyers is usually to get several competitive quotes because pricing is quite complicated. Advising a plating shop how to price stuff is very difficult :-( ... one shop I know of requires 10 years experience as a plating foreman before they can be promoted to estimator! Ballpark estimates are obviously easier than shaving a bid to the penny, but it is extremely difficult to accurately and competitively quote against shops whose estimators were plating foremen for 10 years.
Regards,
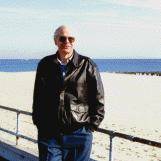
Ted Mooney, P.E.
Striving to live Aloha
(Ted can offer longterm or instant help)
finishing.com - Pine Beach, New Jersey
Q. Within electroless nickel, cad, and any other similar plating for the sole purpose of protection against the elements, how would the cost comparison match up?
Loren Coffin- Elmira, Oregon, US
November 15, 2012
A. Hi Loren.
Years ago, before it became an environmental albatross, cadmium plating could be cost competitive with zinc plating in some circumstances, but no longer. Electroless nickel is much more expensive than zinc plating.
Zinc plating is the least expensive plating for corrosion protection. Some of the zinc alloy platings like zinc-iron, zinc-cobalt, and zinc-nickel may not be too much more expensive than plain zinc plating, and may exhibit sufficient extra corrosion protection as to be as inexpensive on a functional scale. Good luck.
Regards,
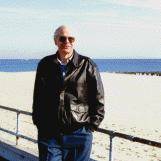
Ted Mooney, P.E.
Striving to live Aloha
(Ted can offer longterm or instant help)
finishing.com - Pine Beach, New Jersey
A. "Within electroless nickel, cad, and any other similar plating for the sole purpose of protection against the elements, how would the cost comparison match up?"
A. Good question. It does not depend only on the coating type, but also whether the coating is uniformly sealed or microcracked, etc.
For thin coatings a 2-3% Phosphorous Nickel could be the best, but it needs to be without any pinholes and such. The cost is higher. It can, however, be used on microminiature components, where it is very uniformly applied. It can also cover non-conductive surfaces if pretreated with a catalyst.
If you can afford adding 10-20 microns, then Zn-Ni plating, sealed with trivalent chromium and some varnish on top. Much cheaper too.
Cadmium is (WAS, luckily, cancer cad) a uniform type of coating, much like copper, it is malleable, plastic and wears off with friction in many cases.
Zinc plating or dipping in molten zinc is the classic, cheap and easy. If covered with special paint layers afterwards, provides good protection for many years, but compared to Zn-Ni is much softer and less corrosion resistant. (150HV hardness compared to 400HV hardness)
There is also phosphating in boiling alkaline bath which provides an even, black surface, after which the steel or iron component is oiled and thus corrosion protected. A very simple and very, very cheap method.
Thus, it depends on the aggressivity of the environment in question. If you expect salt, see the blue zincate or even gold-plated air conditioning exchangers. Zinc alone is good, but put it into seawater and see it vanish. Thus, any plating will use further modifiers, sealers, varnishes, etc. that assure the plating wasn't in vain. And that cost more. 10% more or 400% more. Depends. Thicker coatings: more protection. More sealers: more protection. More passivators: more protection.
Very thick Zinc-Nickel plating, plus a lot of post-processing can exceed the cost of a very thin nickel (on some substrates), but then Zinc plating can do 20-ton blocks, while electroless nickel is best suited for tabletop usage due to bath costs and limited life of the bath.
Thus, for huge volume applications, coatings and plating with the cheapest and lowest cost (and lowest risk during operation) raw materials will be used, but in very small parts, even some expensive coats or plating may be very cost effective due to some other properties (Aesthetic, etc.)
If you really need to be protected against the elements, you can even apply many layers of metals (if you must avoid paints), which could be NiP (electroless Nickel-phosphorus) as the base layer, then sealed and then over plated with 5 or 10 or even 15 micrometers of gold, for example. When properly executed and with Cobalt as the additive in gold plating, such corrosion protection would be amazing, even if wasteful financially.
Many times it is not just the nominal metals plated, it is the whole process and the resulting surface, plus organic or inorganic passivating compound over that surface.
Imagine you have a 10-micrometer thick copper plating, that is absolutely even and 100% copper. Copper alone can corrode, but slowly and very uniformly. This coating would be in some applications superior to cracked surface of untreated electroless nickel, which, by itself does not corrode or dissolve in water, but the unsealed surface would let water and air to the steel surface below and slowly start pitting corrosion holes. The copper, after wearing off, would more likely start the corrosion over the whole surface at once.
Many factors, such as, corrosion in what environment are you protecting against, or, if there are any other design constraints (protecting for 10 years, 20, 100, 1000 or only 5?) need to be considered, as the protections work in a different manner.
Zinc coating is "sacrificial", that is, any attempted corrosion will corrode the zinc. Gold plating (or nickel, etc.) is purely a barrier coating, aiming to prevent oxygen and other factors from the environment to the surface you are trying to protect.
Thus, cost-effective depends on: desired result, design environment, yearly volume, availability, planned lifetime, risk, etc.
Metal blackening by phosphating is the very cheapest. Very simple, allows huge parts, cars, etc.
Zinc is cheapest. But a zinc plating that protects better will cost 3x as much.
Zinc-Nickel great. Better hardness and anti-corrosion properties. Also added cost. If you plan on long term and rough conditions, it will be more effective than Zinc.
The rest is likely more cost effective for marine environments, where the required thickness of everything is much higher.
The "cost effective" also changes with the atmosphere: Hydrogen sulfide? sulfur dioxide? Risk of abrasive damage? Frequent changing temperatures? Exhaust products? Manipulation of the plated surface after expedition? Any other mechanical strain? Is the environment alkaline, acidic, neutral? What kind of dissolved salts? Any electric potential driving the corrosion?
Each of the corrosion protection mechanism has different weak points upon which it fails to protect, and each of the plating and sealing processes has a slightly (or completely) different properties in this manner.
That all affects the calculation of what will be cost effective, sometimes disabling some of the options.
- Vienna, (The Coffee City), Austria
A. Jane D. Stanton has written a comprehensive overview, but even that may not answer your question. If you ask a specific question, and provide some facts yourself, you will get a simpler and more easily understood answer.
What items do your wish to protect?
What are they made of?
What are the service conditions?
How long do you want them to last?
How many are there?
There's a world of difference between a million of an item which will be used indoors, in a clean environment and needs to last for two years against one which:
Is a zinc die casting, made fifty at a time, and which must withstand twenty years on the front of a truck which is driven 100K miles a year on salted roads.
Item #1 might cost pennies to finish, and item #2 tens of dollars.
Your question is akin to asking a physician: "I have a pain in my belly. How long do I have to live?"
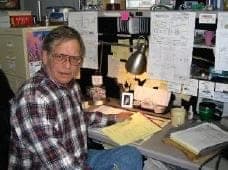
Jeffrey Holmes, CEF
Spartanburg, South Carolina
Q. Dear All,
May I know how the plating cost being calculated out ?
Other than knowing the dimension and difficulty of the parts on the cost calculation, will like to know what other factors that cause the price being quoted ?
Thanks,
- SINGAPORE
April 2, 2020
A. Hi Stephanie.
We appended your inquiry to one of dozens of threads we have about cost calculations for plating.
If this page does not already contain the info you seek, please search the site for the type of plating you need (zinc, nickel, chrome, etc.), the general type of part (threaded hardware, reel-to-reel electronics, large individual parts), and maybe the substrate material ... or re-post with details. Also, please tell us where you fit into the supply chain, as that impacts how to best answer. Thanks.
Regards,
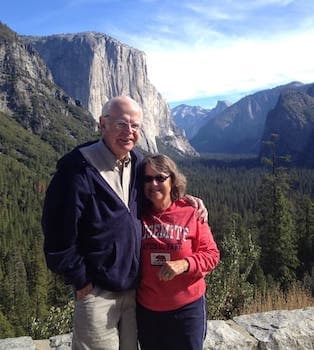
Ted Mooney, P.E. RET
Striving to live Aloha
(Ted can offer longterm or instant help)
finishing.com - Pine Beach, New Jersey
⇦ Tip: Readers want to learn from your situation;
so some readers skip abstract questions.
Q. Dear Sir,
How to calculate the generic cost of hard chroming a cylindrical shaft given the OD is 60 mm & Length is 600 mm,
when we need to do 200 microns on the surface?
- Sharjah UAE
January 21, 2022
A. Hi Taher. From your question it sounds like you are a buyer, not an employee of a plating shop.
Unfortunately, I think any answers offered and any calculations you engage in will just be lost motion; I think all you can realistically do is try to get multiple quotations.
Luck & Regards,
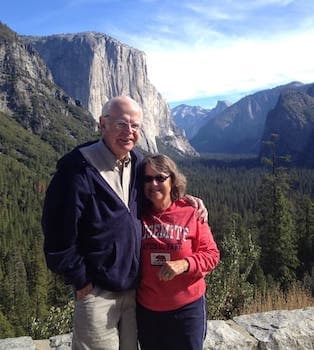
Ted Mooney, P.E. RET
Striving to live Aloha
(Ted can offer longterm or instant help)
finishing.com - Pine Beach, New Jersey
A. Hi Taher,
It may be a nice comparison how much the Chrome as a metal costs, relatively to the plating cost: 60mm x 600mm x Pi x 0.2mm x 7.19 g/cm3 = 162.6 grams of Chromium.
At bulk metal price it will be approximately $1-2.
To this huge cost of the metal you should add just a "little" for: cleaning, fixturing, masking, 10-20 hours of plating, HE bake (if required), maintaining and analyzing the Chrome bath, grinding (as 200 micron most likely will need grinding), testing, and few other things that I may forget. So, depending on a shop, requirements, and volumes -- it can be anywhere between few tens to few hundred dollars.
Thank you for the nice question.
- Winnipeg, Canada
• Thread 25603 about Zinc Plating
• Thread 43852 about Nickel Plating
• Thread 53013 about Gold, Silver & Jewelry Plating
• Thread 42981 about General Issues
Q, A, or Comment on THIS thread -or- Start a NEW Thread