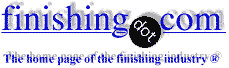
-----
Spray chroming with silver nitrate

Q. Hi Marvin, I'm using only reducer R. What is sensitizer, and what is the chemical used and when should be it used.
Saravanan kumaran- Chennai, Tamilnadu, India
January 3, 2023
A. Hi Saravan. We'll try to alert Marvin to your question, but he previously answered that question here. Marvin has done yeomen work helping everyone with this, so please study the whole thread because it's already very long, and repeating stuff will only make it longer & more confusing :-)
Luck & Regards,
Ted Mooney, P.E. RET
Striving to live Aloha
(Ted can offer longterm or instant help)
finishing.com - Pine Beach, New Jersey
Q. Hi, sorry to pick up a old tread
Can anyone tell me (in a dumb down way / no chemistry knowledge) how to make the fluids to "spray chrome" with silver? I have a few veteran cars, and it would be a Nice cheap way to upgrade the look of a few parts
Hope someone can help..
Beat regards from denmark.
/Brian
- Denmark
October 10, 2024
A. Hi Brian.
The normal procedure, even for those who are chemists, is to start by buying the process package from suppliers who sell them with instructions, and perhaps the needed optional equipment like 2-head sprays guns, etc.
Most people would not attempt to formulate even house paint or enamel for the interior trim in their house or an old car, let alone a system of highly compatible primer, sensitizer, 2-component silvering layer, and topcoat. Still, on-line patent searches are so easy today that you could see what can be learned that way.
Luck & Regards,
Ted Mooney, P.E. RET
Striving to live Aloha
(Ted can offer longterm or instant help)
finishing.com - Pine Beach, New Jersey
⇩ Related postings, oldest first ⇩
Q. I'm associated with trading of building materials in Dubai. I wanted to know if it's possible to metallize the surface of polystyrene with silver and the procedure for it ... any help in this regard will be highly appreciated
Ahmed Jawwad Aliattractive building materials - UAE
2006
A. Yes, it is possible to metallize polystyrene but there are many severe limitations & handling restrictions. What are the dimensions of the items you are trying to metallize and what will be the specific end use? We need more information before describing a proper process. Thanks.
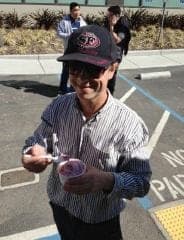
Blake Kneedler
Feather Hollow Eng. - Stockton, California
A. Dear Ahmed,
Silver tends to get dark after a while, depending on the air, moisture, and temperature. Thin layers of silver already become ugly after a week.
Silver is not a suitable metal for your plans.
It is much better to use a more stable metal; like gold.
- The Netherlands
A. Polystyrene can be coated with silver and there are many ways of doing it. The problem comes in making it stick. The simplest way is to use polystyrene with about 5% butadiene in it and then etch the copolymer prior to electroless metallising. Alternatively you can use plasma etching to prepare the surface. The best way to do deposit the silver is by silver spray - the old silver mirror process. However, you need to provide more information about what you intend to do and its final end-use.
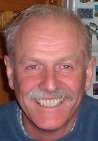
Trevor Crichton
R&D practical scientist
Chesham, Bucks, UK
Q. Dear sirs
I recently came across a company in the course of my business that had sprayed a silver nitrate solution onto a piece of styrene having first primed with a PU filler. They then used an activator (Acid) which resulted in a superb chrome finish that was then washed over with distilled water before application of a finish coat of a clear PU lacquer. My question is have you come across this process and if so do you have an idea on how to achieve this. I have been trying for several months to find out more information on this process. The whole procedure was done with a conventional spray gun.
Yours sincerely,
- Birmingham, West Midlands, UK
2003
A. Hi, Trevor,
This sounds like "two-part silvering" wherein silver nitrate and a reducing agent are simultaneously sprayed onto a surface to reduce a silver film onto it. You can probably research the technology successfully by searching for "Brashear process". Good luck.
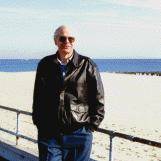
Ted Mooney, P.E.
Striving to live Aloha
(Ted can offer longterm or instant help)
finishing.com - Pine Beach, New Jersey
A. I have recently got training and bought the system from a company in Shenzhen in China. The process is very simple. Just need the Silver Nitrate mixed with distilled water. Add 100 g Silver Nitrate in 20 Liters of distilled water called solution A; and make Solution B by mixing ammonia ⇦ on eBay or Amazon [affil link] in distilled water 1:20 and spray with a twin nozzle gun.
Base coat is PU, Spray chemicals named K and S wet-on-wet then A+B; and over coat can be PU or UV. You can make silver, gold and any metallic colour. The technology, spray machine and materials are available for sale in China.
Masood Tariq- Lahore, Pakistan
August 19, 2009
Q. I want to know about silver spray plating technology by 5-gun machine. I read your article but I do not understand "S" wet on wet chemical. Kindly send me info on S chemical.
zarrar ahmadplating shop - Delhi, India
April 22, 2011
A. Hi Zarrar,
There are many suppliers of chrome-look paints, including the advertisers who make this site possible and who are shown in the banner at the top of the page. You can correspond directly with them if you wish.
But this discussion has mixed together a generic discussion of spray finish silvering, with specific instructions from one particular Chinese brand, so it is getting confusing. It sounds like parts K and S of that particular system together comprise a two-pack base coat before the silvering. "Wet-on-wet" simply means that one part is sprayed first, and then the second part is sprayed on before the first part has completely dried.
Regards,
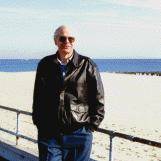
Ted Mooney, P.E.
Striving to live Aloha
(Ted can offer longterm or instant help)
finishing.com - Pine Beach, New Jersey
Q. I want to know what is the k and s, which is used in the silver spray plating?
plating shop - baroda
June 14, 2011
A. Hi, Ankit. Masood explained what k and s meant to him, which I tried to clarify for Zarrar.
It's always difficult to know what shorthand or slang someone is referring to without the complete context.
Still, I'd go with Masood's explanation that they are letters assigned to the two components of a polyurethane base coat by their Chinese manufacturer. You can learn more about this from the wikipedia entry on polyurethanes at en.wikipedia.org/wiki/Polyurethane, or by googling for "two-component wet-on-wet polyurethane". Good luck.
Regards,
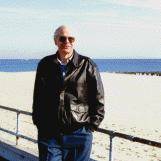
Ted Mooney, P.E.
Striving to live Aloha
(Ted can offer longterm or instant help)
finishing.com - Pine Beach, New Jersey
Q. Hi,
Can you please give me some information on tin II chloride dihydrate perfect mixture? Because I'm so sure my mixture on this is having problems. The silver reaction is very slow, yellowish, non stick. My mixture is 5 g/L tin, 10 mL HCl and D.I. water.
Please help.
Thanks
- Malaysia, penang
August 7, 2016
A. Hi Andy. Sorry, I do not even know whether tin II chloride dihydrate is a good reducing agent for this particular silvering operation or not.
Regards,
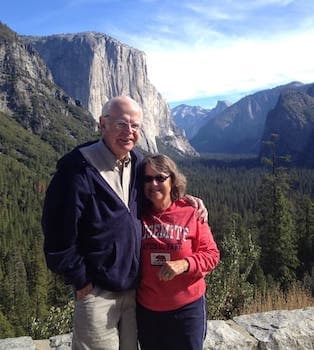
Ted Mooney, P.E. RET
Striving to live Aloha
(Ted can offer longterm or instant help)
finishing.com - Pine Beach, New Jersey
A. Hi Andy
Any chloride or hydrochloric acid will react with silver nitrate to give a precipitate of silver chloride. It is a standard test for chlorides.
Reducing silver nitrate to produce a silver deposit requires handling strong and potentially hazardous chemicals.
If you do not fully understand the chemistry it would be better to find an alternative process.
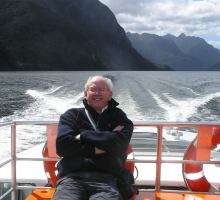
Geoff Smith
Hampshire, England
Hi Mr.Geoff,
Thanks for your information. I have successfully found out the problems and at the same time success my formula by using tin II chloride dihydrate and HCl.
Once again, thanks guys
- Malaysia penang
Q. Hi,
I have a question.
1. How to make my silvering chrome looks whiter and shine?
2. What is the name of chemical when spray on it for easy to blow off the water?
thanks
- Malaysia penang
August 18, 2016
Hi Andy.
2. Either isopropyl alcohol or mild detergents like sodium lauryl sulphate can improve rinsing.
Regards,
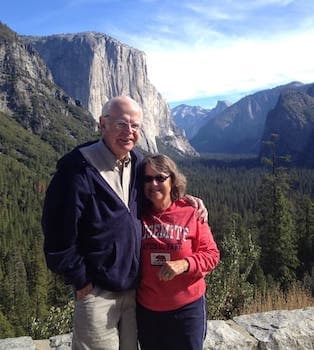
Ted Mooney, P.E. RET
Striving to live Aloha
(Ted can offer longterm or instant help)
finishing.com - Pine Beach, New Jersey
A. Tin II Chloride in this process or any Spray Silvering process is to seed the non conductive surface with an active metal that will make the reduced silver stick to it and form the silver mirror, it's prepared by mixing about 5 grams of Tin II Chloride with 25 ml of HCl then adding about 1 L of deionized Water (DI Water); after the piece has been degreased, and its surface tension has been lowered (wetting agent) the sensitizer will be sprayed and allowed to seed the surface for at least one minute but no more than 3 minutes.
Some call it sensitizer or Activator, I have used Zinc Chloride (zinc oxide
⇦ on
eBay or
Amazon [affil link]
+ HCl) and Magnesium Chloride (salts from the pharmacy) and they have worked just as good.
- Managua, Nicaragua
Q. Hi,
Thanks for the information.
And how to make silver look like white platinum gold after the silver been done? Any idea what to add in the silver?
Thanks
- Malaysia pg
September 27, 2016
A. Hi Andy. Companies like G.J. Nikolas [a finishing.com supporting advertiser] offer tinted topcoats like you seem to be talking about. If you want to do your own tinting of topcoats you probably have to do some reading on paint formulation.
Regards,
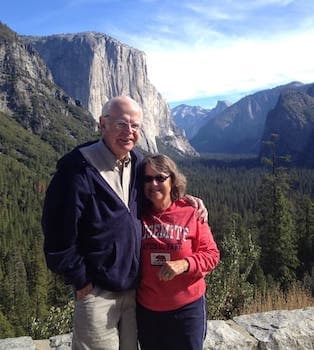
Ted Mooney, P.E. RET
Striving to live Aloha
(Ted can offer longterm or instant help)
finishing.com - Pine Beach, New Jersey
Q. Hi,
Can you please teach/show me the steps/how to re-spray on chrome without removing the faulty chrome?
(Example: peel off touched by finger after spray or some area not turning into chrome).
Thanks
- Malaysia, Penang
January 16, 2017
A. If the Silvering did not go well (many reasons for that), what I do is use dilute ferric chloride
⇦ on
eBay or
Amazon [affil link] , clean very well and start again.
But if this happened after the silvering has been clear coat it, then you must wait for the clear to fully cure and start from that as a base.
- Managua, Nicaragua.
Thanks a lot.
- Malaysia, Penang
January 22, 2017
Q. I have few questions to ask regarding silvering:-
1. How long I can leave the item after silvering without spraying top coat?
2. How long I need to wait to spray top coat after silvering (best results)?
3. Now I'm using Brashear Process preparation solution. On this formulation, there is a (Reverse solution) wrote there. And this is the only step I didn't use it. Is this important for the whole formula? Why and for?
Thanks
- Malaysia, Penang
March 4, 2017
!! Hi,
Anyone please help me. URGENT.
What can I do when too much ammonia added into silvering solution?
Now when I spray out the solution it's completely smelling of ammonia.
Help please.
Thanks
- Malaysia, Penang
March 7, 2017
A. The most you can wait is two hours, but if you can force dry the piece and then allow for about 15 minutes to cool down, that will be best or one hour air dry.
As for too much ammonia, I am afraid that you just need to use what you have, that is why when experimenting I always try to use the least silver nitrate as I can because its quite expensive, the only steps I know are, Mix 3 grams of Silver Nitrate on about 500 ml of Di water, then add about 3 grams of sodium hydroxide, then just enough ammonia to completely dissolve the silver hydroxide complex, some book references advise to leave a very small amount of the hydroxide at the bottom, just enough to see it, that will guarantee that you are not using too much ammonia.
Marvin Sevilla- Managua Nicaragua
Q. Hi Marvin,
Thanks for the top coat information.
Regarding to what you say on my mistake, I don't really understand what you mean on this ("As for too much ammonia, I am afraid that you just need to use what you have").
As what I mean on my question is, I already made a mistake when mixing the solution. What do I need to do to save/undo my failure solution? It's really wasting money if I pour the solution away and this solution is 4L not 1L.
Thanks.
- Malaysia, Penang
March 9, 2017
A. I am afraid that you would need to work with what you have now (should be able to silver without any issues, just need to use breathing protection). So far there is no way to remedy this without using more silver nitrate to compensate for the extra Ammonia.
Marvin Sevilla- Managua Nicaragua
Hi Marvin,
I already understand what you mean. I will try it later.
Thanks a lot.
- Penang, Malaysia
March 10, 2017
Q. Hi sir,
Need help. We want to know activator name (applied before silver solution) or how to make it.
handicraft - Delhi, India
March 12, 2017
![]() ![]() |
Hi Sameer. Apologies, but you posted stuff with 3 variations of your name on several different threads and I didn't know they were from the same person, and didn't always comprehend them. I now understand, so we're posting all of it together now. Sorry for the delay! Regards, ![]() Ted Mooney, P.E. RET Striving to live Aloha (Ted can offer longterm or instant help) finishing.com - Pine Beach, New Jersey Q. Dear sir, ![]() Q. Hi team, Q. Hi team, handicraft - Delhi, India |
A. To understand the nature of your current issues (water not staying on item and water beading/bubble) we must understand the nature and history of the type of metal coating that you are trying to attempt. The basis of what we call today "Spray On Chrome" dates back to 1835 German chemist Justus von Liebig, the reduction of Silver Nitrate to elemental Silver and deposited into a glass sheet; that was the start of the Silvering Mirrors history, and that is exactly what this process (spray on chrome) really is, creating a front surface mirror; and we do that by re-creating a glass like surface (PU gloss coating) on other dielectric surfaces (non conductive articles like plastic, wood, resin).
The issue is that glass is a very unique surface and it has a very low surface tension, and when properly cleaned the water (and chemicals in it) will completely cover the surface ... but Automotive/Industrial coatings like PU have a very high water surface tension, and no matter how much you clean the surface the water will just bead and will not stay on.
So how do most people get around that constraint? I personally use a proprietary wetting agent that lowers the surface tension and makes the surface behave like glass; others use Flame/plasma treatment to lower the surface tension (I personally don't use it because I don't like to play with fire while working with expensive articles).
Please watch this instructional videos I made on the subject.
Pre wetting agent high water tension:
Post wetting agent low water tension:
When you see videos of pros using just the sensitizer and it appears to flow it is because they use expensive proprietary silvering chemicals and the sensitizer already comes with wetting agent. Another interesting thing is that right after they silver the piece, they use a chemical to counter the wetting agent effect; they do this so the water beads and is extracted much faster and better using forced air. I personally don't use this and just force dry the piece the best I can.
Marvin Sevilla- Managua, Nicaragua
Wow, quite an exposition, Marvin. Thanks!
Regards,
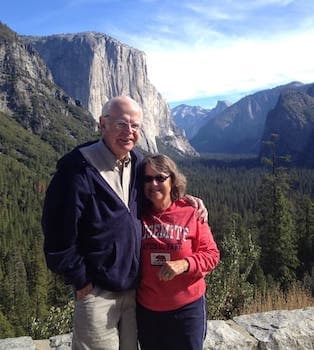
Ted Mooney, P.E. RET
Striving to live Aloha
(Ted can offer longterm or instant help)
finishing.com - Pine Beach, New Jersey
Q. Hi sir,
Thanks for reply, I am really thankful to you.
I have 2 other problems as well.
a) Suggest name of activator to do silver plating (what is to be added into water to make activator)?
b) Suggest us the name of how can make good reducer from glucose (composition)?
- Delhi, India
March 13, 2017
A. Sameer haque, for your question of "Need help. We want to know activator name (applied before silver solution) or how to make it." :-
1. Tin II Chloride in this process or any Spray Silvering process is to seed the non conductive surface with an active metal that will make the reduced silver stick to it and form the silver mirror; it's prepared by mixing about 5 grams of Tin II Chloride with 25 ml of HCl then adding about 1 L of deionized Water (DI Water); after the piece has been degreased, and its surface tension has been lowered (wetting agent) the sensitizer will be sprayed and allowed to seed the surface for at least one minute but no more than 3 minutes.
(This solution formula is from Marvin. You can just follow this formula to use or if you think you want to try to make it better, it's all on your own. Good Luck.)
2. Any super high gloss base coat will do. Just need to keep the pieces after spray base coat for 12 hours then only can spray on silver (p/s: make sure the place to store it is clean and oil free in Air.)
GOOD LUCK
Thanks a lot to all people that are giving away information. This forum is perfect for all :)
- Malaysia, Penang
March 18, 2017
Q. HI,
NEED ADVICE FROM YOU GUYS. I FEEL TO CHANGE ONE OF THE CHEMICALS FOR SILVERING SOLUTION AND I DON'T KNOW CAN IT WORK OR NOT?
NOW I'M USING THIS CHEMICAL:-
AGNO3 + NH3 + KOH.
CAN I CHANGE IT TO THIS:-
AGNO3 + NH4Cl + KOH =??
NH3 IS REALLY TOO SMELLY AND QUITE HARMFUL IF ACCIDENTALLY DRINK IT. FOR NH4CI NOT SO HARMFUL. AND IT WORKS IF I USE NH4Cl?
THANKS
- Malaysia, Penang
![]() |
A. Many if not all of the chemicals in the Silvering process are quite dangerous if swallowed. I do not suggest changing Ammonium hydroxide with Ammonium chloride, it will not work at all, you will most likely be precipitating insoluble Silver Chloride instead of creating Silver hydroxide, the basic process has not changed in nearly 200 years, there has been many improvements, but most of them made towards the reducer and sensitizer, but the base of the process is the silver ammonia complex, and there is no changing that. Marvin Sevilla- Managua Nicaragua A. I am not sure why posts have not been posted yet, I gave an extended reply, but this time I will just go ahead and say that no, you cannot use Ammonium Chloride instead of Ammonium Hydroxide, the reaction between Ammonium Chloride and Silver Nitrate is insoluble Silver Chloride and Ammonium Nitrate, the process have been the same for nearly 200 years and while ammonia can be toxic, most of the other chemicals can be quite harmful if swallowed. Marvin Sevilla- Managua Nicaragua ---- |
Q. Hi Marvin,
Oops... I already bought ammonium chloride. Anyway, to make 1 L high grade ammonium hydroxide by using ammonium chloride?
And thanks a lot for the information.
- Malaysia, Penang
March 20, 2017
A. I am afraid you will need to get Ammonium Hydroxide, I suggest you use reagent grade chemicals and don't even try to make your own if are serious about this as a business, otherwise you will be plagued by inconsistent results. This process is very complex as it is and by trying to make your own chemicals you will just bring more Variables to it; that is why big businesses just purchase the chemicals from vendors that can guarantee consistent results and give tech support ... but I understand where you're coming from because I tried that myself with okay results.
Marvin Sevilla- Managua, Nicaragua
Q. Hi Marvin,
But I already brought ammonium chloride (1kg) bottle. Nothing I can do on it? Is wasting money if I just throw into bin. I try to refer in youtube (How to make ammonia hydroxide from ammonium chloride). It's just seen very simple to make ammonia solution. But I need to diluted into 1 L and dilute again into 500 mL.
Anyways to know how many grams of ammonium chloride and KOH needed to use to process 1 L
Thanks for the earlier answer.
- Malaysia, Penang
Hi Andy. I applaud Marvin's yeoman efforts on this thread, where he has replied to your continuing requests for help 10 separate times already! The amount of time he has given you personally is way beyond generous ... and I don't think we should now be asking him to spend his time detailing a procedure for doing exactly what he has very clearly told us not to do :-)
I suggest that you follow youtube instructions or the many student pages available about how to make ammonia gas from ammonium chloride. If students can do it, surely you can do it without insisting upon dragging Marvin by the heels where he has already told us twice that he does not want to go :-)
Best of luck. Regards,
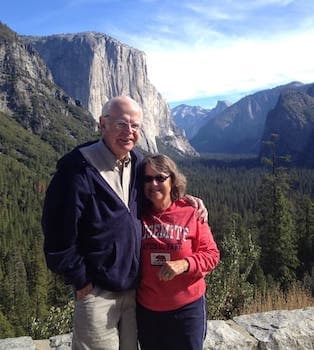
Ted Mooney, P.E. RET
Striving to live Aloha
(Ted can offer longterm or instant help)
finishing.com - Pine Beach, New Jersey
A. Mr. Ted, I've been there and done that, believing I could make every component of the system myself, only to hit a brick wall. It's time consuming, results are never guaranteed and inconsistent. It was a learning experience because I am not a chemist, but I got to learn many things; I am very grateful for the learned experience, but it's not for everyone to take upon themselves.
Now I order the most complex chemicals like silvering/reducing solution/wetting agent from the least expensive provider in the USA; I pay to bring them to Nicaragua, and while the profit margins are not as large as home made chemicals with 95% quality and accuracy, you can't put a price on dependability, quality assurance and tech support from a trusted vendor.
Marvin Sevilla- Managua Nicaragua
(You're on the 1st page of this topic) Next page >
Q, A, or Comment on THIS thread -or- Start a NEW Thread