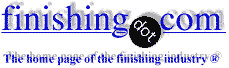
-----
Reduce paint thickness in Cathodic Electrodeposition (CED) system?
⇦ Tip: Readers want to learn from your situation;
so some readers skip abstract questions.
Q. Solvent name for reducing the pH of electrophoretic bath.
Mohd Farman[Moradabad] UP [India]
January 30, 2024
Q. How Voltage, Current & Resistance are true in CED coating (V=IR)?
Supinder SharmaEmployee - Gujarat
May 25, 2024
A. Hi Supinder,
Ohm's Law (V=IR) is always true, but it's often easier to visualize when rearranged as "I = V/R", i.e. the current that will flow through the system is equal to the voltage you put on the system divided by the resistance of the system. If you want to double the current flow you need to double the voltage, or cut the resistance in half.
But I don't really understand the question ... more words please.
Luck & Regards,
Ted Mooney, P.E. RET
Striving to live Aloha
(Ted can offer longterm or instant help)
finishing.com - Pine Beach, New Jersey
Q. I agree about this V=IR , but voltage I applied and current amp output delivered I want how to measure resistance in our CED bath for understanding.
Supinder Sharma- Gujarat
May 28, 2024
Multiple threads merged: please forgive chronology errors and repetition 🙂
2003
Q. I'm working on a cathodic electrodeposition (CED) project. Currently I'm getting paint thickness in the range of 25-32 microns.I want to reduce this thickness up to 18-20 microns.
ACRONYMS:
NVM = non-volatile material
CED bath parameters : pH 5.90-6.10 Conductivity 960 micro Siemens. Temp 28-30 °C NVM(% solids) 9.43 % P/B (pigment binder ratio) 0.10 Voltage 160 V Anolyte conductivity 2500 micro Siemens I have five ways to reduce the thickness:
a. By reducing the bath conductivity
b. By reducing the anolyte conductivity.
c. By reducing the NVM.
d By reducing the voltage/current.
e. By reducing the dipping time in CED bath.
I can't reduce the dipping time in bath as I have some restriction. I can't reduce the anolyte conductivity as on reducing this fungus/bacterial growth is taking place. I can't reduce the NVM as it is already on lower side (standard is 12-14 %). My bath conductivity is already on lower side but still thickness is not coming low. I'm operating at 140 V though my standard is of 250-300 V. Please suggest how I can reduce the thickness.
Manish C [last name deleted for privacy by Editor]- New Delhi, New Delhi, India
![]() |
ACRONYMS: A. Manish, Please check the pH is per your supplier's standard. Please check that the conductivity conforms to prescribed levels per supplier data sheet. Are you running an Ultrafilter and replacing the discharged permeate with DI water of 5 micro Siemens conductivity? Are the solids as prescribed? Since we do not have an idea of the proprietary process you are using, some of these suggestions may validate the process. Hope this helps. Regards, ![]() Asif Nurie [deceased] - New Delhi, India With deep regret we sadly advise that Asif passed away on Jan 24, 2016 A. I have used electrophoretic paint in the past and found that the thickness of the cathodic electrodeposit could be controlled by either the temperature or the voltage. Changing the bath chemistry is not a wise way to proceed because you are altering an established system and unless you know exactly what you are doing, you will cause a lot of future problems. The deposition thickness is related to the bath temperature, so by reducing this and keeping all other properties constant you will reduce the thickness. The systems I have worked on are quiet sensitive to temperature, so only modest changes will alter the thickness. Alternatively, reduce the voltage; this will also reduce the thickness. I do not know what you mean by operating at 140 V although the "standard is 250-300 V", so perhaps you can elucidate. Finally, if these two changes do not reduce the thickness to your needs, you have to reduce the processing time. Assuming your system is similar to the one I have used, there is no point in reducing the current because this automatically reduces to a very low value as the deposit thickens. ![]() Trevor Crichton R&D practical scientist Chesham, Bucks, UK 2003 |
by Electrocoat Association
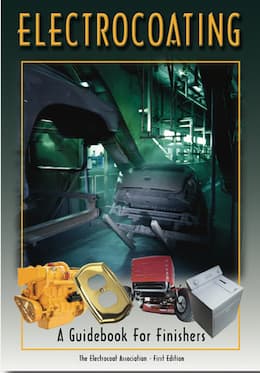
on eBay or Amazon
or AbeBooks
(affil link)
Dear Asif,
Thanks for your valuable suggestions. I'm running an ultrafiltration unit and also using DI water of < 5 microsiemens conductivity. pH is in the supplier's range(5.10-6.10), but still I'm not able to reduce the thickness. I'm working with the latest CED technology . Our system is the latest one. We have four ways to reduce the thickness in CED system and which I have described in my previous query and I have tried all except reduction in dipping time. I can't go for this option. I hope that you will further give your valuable suggestions to me.
Thanking you.
Dear Trevor,
Thanks for your valuable suggestions. Yes I am using the same system that you are using there. I am using the latest CED system which is used everywhere in this world. So assume that it's the same as you have. Yes it's true that standard voltage requirement is 230-250 volts but I'm operating at 160 V because I thought it will help me in reducing the thickness. It's also true that my trial can damage our system and can create future problems but I love to do trial because without trial we cannot come to a conclusion.
As far as temperature is concerned our standard is 28-30° C. and I have reduced it to 27 from 30 but still the thickness is coming high and I am surprised that at lower voltage (140 V), low NVM(9.41 %) and low conductivity (960 ms), I am getting high thickness (26-32 microns). Let me reduce the temperature to 25 °C. and then see what happens. Thanks again for your suggestion.
Regards,
Manish C [returning]- New Delhi, India
A. If you are unable to control the thickness, the problem may lie elsewhere. You need to check if the voltage displayed is the same as the voltage applied on the component.
Gurvin SinghMohali, Punjab, India
2003
2003
A. Dear friend,
In my opinion may the conductivity of ED bath is too low. Because I have the opposite problems from you. Since I want to raise the thickness (now is about 20 micron) but the only difference parameter was conductivity of ED Bath whereas too high in mine.
The data parameter from my process are :
1.NV 14.67%
2.Coating voltage is 140 V (range 80 to 160 V)
3.pH is 6.25 (range from 5.9 to 6.3)
4.Conductivity is about 1545 micro Siemens/cm. (standard is 1100 to
1400).
5.Ratio F1 to F2 is 1:10
I also used the latest technology of ED Paint, which is Acrylic CED-Lead Free
Henry S [last name deleted for privacy by Editor]- Jakarta, Indonesia
2007
A. Dear Mr.Manish,
I understand your problem.
ACRONYMS:
DFT = dry film thickness
You want to control the outer DFT without disturbing any line condition.
In this case you can cover the anode cells simply with the PVC pipe of good quality (Quality in the sense of Good Chemical Resistance).
After doing this definitely you will get reduction of 6 to 8 µ DFT.
Your throw power will not affect after doing this (Kindly check up with the paint supplier).
regards,
paints - Pune
by Bruggemann & Rach
on eBay or Amazon
or AbeBooks
(affil link)
A. Dear Manish,
One other way of reducing the DFT of your EDP is in choosing mineral fillers with a very fine particle size, good dispersion properties and good flow properties. It often happens that due to cost reasons, producers change the mineral filler included in the original formulation to a cheaper grade locally available. In this case, many properties of the EDP - including the DFT - are getting worse.
Especially the dispersion behavior of the fillers affect the DFT very much. If the filler is not dispersed properly, you will find agglomerates that are actually much larger than the original particle size of the filler. Also the flow properties are affected negatively by a bad dispersion.
There are only very few mineral fillers that are working properly in EDP systems, one I know is called Sillitin.
Best Regards
Christian
- Neuburg, Germany
May 23, 2008
A. Dear Manish,
I feel sorry to say that the CED you are using have very low rupture limit. Generally rupture limit of CED is more the equal to 350 volt. Nobody can help you; just change the paint supplier.
- Lahore Pakistan
June 29, 2008
A. Dear Manish
Please check the Solvent level of the bath and co relate with the production trend You may be feeding the bath in the higher rate , that means your bath will be fresh and that's why you are getting high DFT.
This is the same problem I observed in my line . I reduced Solvent level.Drained permeate at regular frequency to Keep the DFT and Finish in good condition.
Thanks
Srinivasan
- Chennai, India
March 9, 2009
A. Dear
Please check the applied voltage which is shown by the rectifier & increase the bath conductivity ,reducing the bath temp.
thanks,
- Gurgao, India
December 10, 2008
A. You did not write about the number of anode cells and type of anode cells. However, reduce the number of anodes, or cover the membrane from bottom side.
DINESH MAURYA- jamshedpur, India
April 9, 2009
December 11, 2009
A. How to reduce Dry Film Thickness?: there are several way to reduce DFT --
1. Decrease applied voltage.
2. Increase of MeQ (milliequivalents) value by adding pH adjuster.
3. Purge of permeate to reduce solvent content.
4. For CED line that have high turn over set MeQ value in maximum specification.
5. Increase conductivity of anolyte tank, it will up MeQ value.
Regards
- Bekasi, Indonesia
A. Dear Manish,
You please reduce your anode no. or Reduce solvent level is only way to reduce DFT. You should must ask your supplier for that. If you will use Sixth generation CED Paint Your problem will resolve.
Ankush shukla- Ghaziabad, India
May 20, 2010
A. Dear Manish,
Please check calibration of displays & DFT meter etc, then change any variable one by one and note the impact/ results. The change should be economical, not increase the wastage of energy or material. Following steps may help you to overcome this problem:
1: Conductivity of Anolyte seems to be very high as 2500 micro Siemens; decrease gradually as 2400-2300-2200.......
2: Reduce the solvent percentage;
3: Although it may not possible to reduce the dip time in your system but my suggestion is to reduce the dip time any way; will save the cost & energy and also help to reduce the ED thickness.
4: The concentration of electrodes are higher than dipped body area. Reduce the electrode quantity and increase the distance in between the electrodes.
Hope you will post the result of successful measure you have taken so far.
Regards,
- Karachi, Pakistan
August 5, 2010
A. Dear Manish,
At such parameters still you are getting high DFT, so please check Anode:Cathode it around 1:4 if it's less than this then increase it with isolating/disconnecting some anode.
- Pune, India
September 25, 2010
October 31, 2010
A. Dear Manish
You should check these points to reduce the DFT of your component.
1)What is the Anode : cathode ratio
2) You should cover the bottom portion of anode with pvc .
3) You should increase the P/b Ratio of your system.
4) you should check the Actual current and voltage and ramp up time for your system.
Regards
Ravi
- Bareilly, Uttar Pradesh, India
A. Dear,
Please note how much time taken to reach maximum DFT, then after cut down the half of the deposition time without changing any bath parameter. you will get lower DFT if not cut it another half. Generally, DFT depends upon deposition time, voltage, micelle size and surface charge ratio.
- sivassa, India
January 19, 2011
A. Dear all,
To reduce dry film thickness we must concentrate on voltage (280-320), process time (120-130 secs), pH (5.8 to 6.0), conductivity(1200-1600), Meq-24to28, NVM-18 to 22, anolyte conductivity- 500 to 700, voltage rampup time has been separated to 3 stages (10,5,5), hold on (30,25,55), solvent%- 1 to 2
- Chennai, India
May 29, 2012
A. Dear Manish,
Increase the P/B ratio and change the permeate water (25% permeate in two days time and do this step in four times).
- Chennai, Kanchipuram, India
July 29, 2013
A. Dear Mr. Manish,
Please check the Bacteria contamination or growth in CED bath, bacteria growth can lead to higher deposition.
- Jamshedpur, Jharkhand
July 16, 2014
A. Mr.Manish,
I understand your parameters and I suggest you reduce the pH to 5.70 from 5.90~6.10 for reducing thickness ... because pH range is 5.10 to 6.10. So you can maintain pH within 5.50~5.70. It helps to reduce the thickness of the component. I tried many times and got results: low pH can build low DFT.
- Chennai,Tamilnadu, India
April 2, 2015
A. Please check the solvent level (flow controller) of the tank and circulation rate for smooth CED coating and bubble free.
Ajay Kumar singhForce motors Ltd - Indore MP India
March 17, 2017
2005
Q. Hello sirs I humbly feel that it's really a great time to interact with you wizards. In our CED process, we are encountering a major paint problem poor E'coat deposition (dipping process) defect in the sill outer panel of the car body because of "rust" in the non-coverage area of coating. This is not occurring in the sill outer panels we use which are provided with wax holes.
I'm really baffled whether the problem is with the process parameter settings or the mechanical alignment or settings. The process parameters settings we use in our CED process are :
%NVM = 18.7
pH = 5.94
CONDUCTIVITY = 1827 uS
P/B RATIO = 0.16-0.25
BATH TEMPERATURE = 30.7° C
APPLIED VOLTAGE = INLET POINT = 0 V
OUTLET VOLTAGE = 100 V
MAIN BUS = 235 V
CURRENT = INLET = 0/350 amps
MAIN = 950 amps
When we change the inlet voltage, paint defect "hash marks" start appearing in the car bodies. We are planning to increase the %NVM or the inlet voltage -- WILL IT SOLVE THE PROBLEM?
Generously give me your valuable suggestions .
Looking forward with great regards ,
- Chennai, India
Q. I WANT INFORMATION ABOUT CED COATING. I WANT CED COATING CHEAPER THAN POWDER COATING
YASEER charoliaplating shop - MUMBAI INDIA
March 17, 2011
Q. Dear sir,
How to increase MEQ if bath pH is already lower side?
- Greater noida
February 27, 2012
Q. I am a technician at a factory in Shah Alam. I run the factory's CED process. I have a problem with the quality of the paint. Each item of the CED process is bubbled on the surface of part. Why did it happen?
Khairul Abidin Mohamed- Shah Alam, Selangor Darul Ehsan, Malaysia
March 1, 2012
A. Check suction of circulating pumps after shutting the pumps.
See if there is any leakage.
- Nasik, Maharashtra, India
June 7, 2012
Q. I have been given a project to optimize the DFT of e coat. I need to know the exact chemistry behind e-coating plus how much it varies according to the pH, NVM. I know how it varies I just want to know how much it varies. For example, at 21% nvm at my current bath conditions I'm getting about 19 microns and for 18% I'm getting 16 microns DFT. Please help ASAP.
Harsh Bhatiapaint shop, prod. - Pune, Maharashtra
July 10, 2012
Q. I have recently been given to work on DFT optimization of paints in top coat line and on CED DFT optimization. Please suggest me any ideas on how to proceed with this project?
Vikrant Patnaik- Ahmedabad, India
September 14, 2012
Q. What will be effect of higher DFT on CED coated part (40-45 micron against specification of 18-22 micron) on product quality?
Application : Wheel rims
Coating: CED + Top coat (white /silver)
- Bhoapl, India
April 11, 2013
A. It leads to peeling off.
Vijay Bhadwaj- Ludhiana, Punjab, India
May 20, 2013
Q. Hi, I wanted to have input from you all ED experts out there!
We have a car production line with different models, surface area of which differs.
End result is that the largest body gets the required DFT with voltage of 360V, however our challenge is to optimize the energy requirement for all models. We are thinking of a Variable Voltage Rectifier, i.e., to vary the voltage to meet required DFT for DIFFERENT surface areas.
Is having this system a good idea? Can you share some more ideas of optimizing for different models? THANKS.
- Lahore, Pakistan
May 23, 2013
A. The voltage can be controlled automatically so that the DFT remains the same even when the surface area changes.
Gurvin SinghMohali, Punjab, India
July 29, 2013
Q. Hi, I have a cathodic electrodeposition painting system for painting motorcycle frames and other fabricated items. But now I am getting some coarse and nonuniform film on the part. Film thickness is not uniform and on some flat surfaces the film is coarse like deep orange peel. Thickness in some places is 25 microns and some places 70-100 microns. Condition of CED bath and other stages are almost the same as when no problems occur. What may be the cause of this problem and what is the remedy?
Please do a favor to me by giving me the proper solution to this problem.
Thank you.
- Gazipore, Dhaka, Bangladesh
December 20, 2013
A. To reduce the thickness of the coated film you have to add hydrogen peroxide to the bath in the range of 1-10%; it acts as a hydrogen scavenger. Hydrogen gas evolves making defect in the deposited film like pits and makes the surface non uniformly covered -- the problem is in the hydrogen gas evolved, you can use other scavengers like nitroethane.
I think this is the method to get uniform and reduced thickness.
Thanks
- cairo egypt
February 23, 2016
January 23, 2014
Q.
The data parameter from my process are :
1. NV 14.54% range 13-15
2. Coating voltage is 140 V (range 130 to 300 V)
3. pH is 6.33 (range from 5.8 to 6.4)
4. Conductivity is about 1630 micro Siemens/cm. (standard is 1100 to 1600).
5. Ratio F1 to F2 is 1:10
6. MEQ 32.7 range is 28-32
7. Solvent content 1.2 range 1.1-1.4
I found abnormal surface finish now like sagging is occur and in some point no paint is adhere to the metal. also in some area DFT is abnormally high. what to do now ?
More clearly I want to know:
1. how can I reduce conductivity of ED chemical and
2. how can I reduce pH or ED if it goes higher than the range?
3. how can I reduce MEQ ?
I also used the latest technology of ED Paint, which is Acrylic CED-Lead Free
- Dhaka, Bangladesh
A. Welded area usually having spatters and gloss bleed. It will not allow CED coating/paint to stick to the surface over a period of time rust formation will happen.
It is very important to clean the weld spatters & gloss bleed before any paint coating.
For reducing ED coating (CED DFT) you may reduce the bath temperature to less than 25 (22 - 25) & voltage (140-180)
- Mysore, Karnataka & India
August 24, 2016
Q. What is the effect found on surface when pH value of bath increases or decreases?
Suman K Singh- Jamshedpur, Jharkhand, INDIA
July 25, 2016
by Electrocoat Association
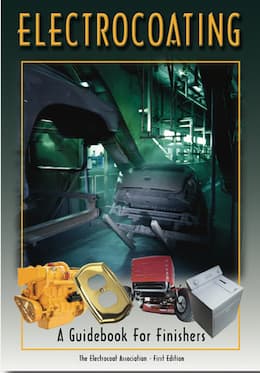
on eBay or Amazon
or AbeBooks
(affil link)
A. Hi Suman. "Handbook of Electropainting Technology" has at least 6 sub-chapters devoted to pH; I don't have a copy of "Electrocoating -- A Guidebook", but good books on the subject are best when you are interested in the abstract science of a subject. Vendors might be able to meet with you as well to discuss such general topics as well.
This forum handles highly specific shop problems well, as you can see, but there probably isn't much that people can do for you in a forum of this type to help with abstract theoretical discussion.
If you are having a specific problem, please carefully detail it (i.e., use more words in your question than you want in the answer), and I'm pretty sure the readers can help. Good luck!
Regards,
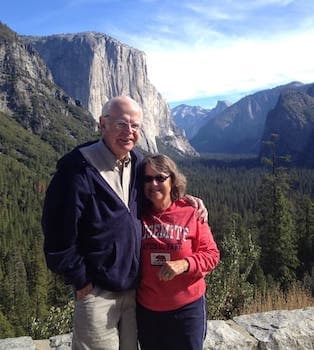
Ted Mooney, P.E. RET
Striving to live Aloha
(Ted can offer longterm or instant help)
finishing.com - Pine Beach, New Jersey
July 2016
Q. Hello sir,
I am rohit singh. Currently I am starting of career in CED coating so please suggest me best book, or if can be possible you provide me related material.
Thanks,
Regards,
- gurgaon, haryana, India
December 9, 2016
A. Hi Rohit. The two that I just mentioned to Suman are the only books I know of; I've only read the one. Good luck.
Regards,
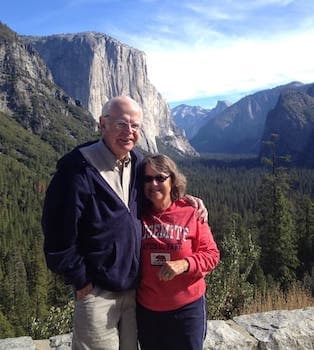
Ted Mooney, P.E. RET
Striving to live Aloha
(Ted can offer longterm or instant help)
finishing.com - Pine Beach, New Jersey
Q. Sir, I am working on CED machine. On the finished product I get a thickness up to 80 mm, but only 15-20 is acceptable. So what to do for this?
Rohit kumar- faridabad,haryana, India
September 9, 2017
A. Hi cousin Rohit. This page is about how to reduce the thickness of CED coatings. There have been some explicit & repeated suggestions, so please try your best to cast your question in terms of the suggestions that have been offered and commenting on the proposed solutions. Thanks!
Regards,
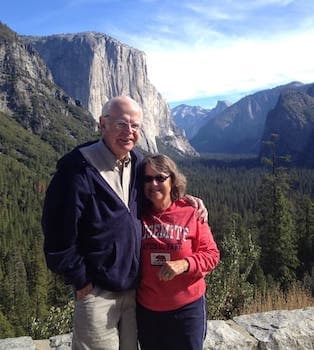
Ted Mooney, P.E. RET
Striving to live Aloha
(Ted can offer longterm or instant help)
finishing.com - Pine Beach, New Jersey
November 2017
Q. Running Cathodic epoxy e-coat line. My paint thickness is through the roof. I have turned down our rectifier and still no better results.
Jason Daire- Jackson, Michigan United States
April 25, 2018
Q. Hello friends
Please can you help me for CED coating DFT because currently I'm facing DFT problem. I'm getting high DFT 18/20 micron, as per required DFT 16 micron. So please suggest to me CED bath parameters is temp. 32 and NVM is 14.63, CED bath pH is 5.9. And anolyte conductivity is 1400, and CED bath level is 18/20. Rectifier is 200 V.
Best regards
Student - Jamesdpur, India
September 26, 2018
December 15, 2018
A. Hello jason , Hello amit,
I think you both have same problem with excess throwing; I think three ways we can decrease the DFT:
1) Decrease paint solids
2) By Decrease in pH (5.5- 5.6)
3) Addition of solvent which reduces the viscosity of tank
So by this way we can control on DFT
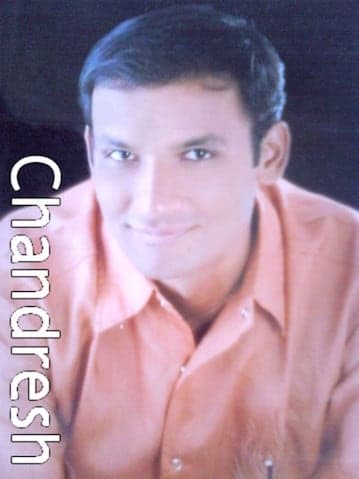
Chandresh Varsani
- RAJKOT, Gujarat, India
August 18, 2020
⇦ Tip: Readers want to learn from your situation;
so some readers skip abstract questions.
Can we reduce the acrylic DFT from 25 to 20? Or how much DFT can be kept of a CED coating at the lower side, on which all the Quality properties are right? (Current Spec is 25-30 Micron).
Sunil kumar- Haridwar Uttrakhand
A. Hi Sunil. I don't think your concern was actually about UV resistance, so we moved your posting off of the thread where you posted it, and onto this page which is about controlling thickness, and which already offers many suggestions. It sounds like 20 to 25 micron thickness is generally readily achievable.
But if the spec says 25 to 30 microns why are you anxious to change it? What is the substrate material and its surface roughness? A thickness which is sufficient for a polished substrate may not be satisfactorily pore-free on some rough surfaces. What follows the CED? -- Powder Coating? What precedes it -- a reliable zinc phosphate? Thanks!
Luck & Regards,
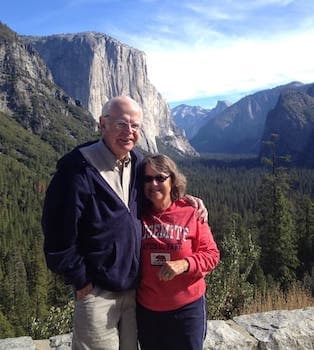
Ted Mooney, P.E. RET
Striving to live Aloha
(Ted can offer longterm or instant help)
finishing.com - Pine Beach, New Jersey
August 2020
by Bruggemann & Rach
on eBay or Amazon
or AbeBooks
(affil link)
Q. Dear Sir, I'm the PTED line Operator.
Sir I want to know how I can reduce thickness of CED paint.
Current pH = 5.8 to 5.96 while std. pH = 5.8 to 6.20
Anolyte conductivity is 800 to 810; sometimes it's 790 to 800 wile standard of anolyte conductivity 700 to 1200.
And also bath conductivity is also low as compared to before. Current bath conductivity 1550 to 1580 while temp is 28 to 28.8 while std temperature of ED is 28 to 30 while voltage is setting on 270 to 290.
First we worked on 290 voltage but now we reduce voltage to 270 to reduce thickness, but still not achieving from 40 to 25.
How can I reduce thickness? Kindly suggest ... I'll be waiting for your reply.
- Pakistan Karachi
A. Dear sir,.
Please check the solvent content in bath, if it high ,
By reducing the solvent content in the bath DFT also will reduce
- Hindupur, Aandra pradesh
May 31, 2021
May 2021
Thanks Sudhakar! Five previous writers offered the same relationship: "lower solvent = lower DFT". It's a bit counter-intuitive because higher solvent does means lower viscosity as one responder noted ... but competing forces overwhelm that effect as confirmed by graphs in the previously mentioned W. Machu Handbook of Electropainting Technology.
Luck & Regards,
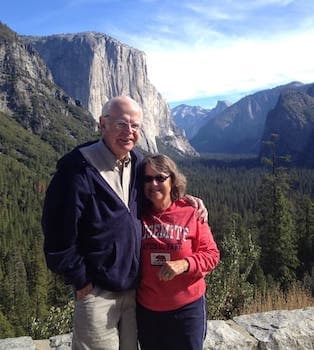
Ted Mooney, P.E. RET
Striving to live Aloha
(Ted can offer longterm or instant help)
finishing.com - Pine Beach, New Jersey
A. You can reduce your thickness, by eliminating the solvent level from the bath.
Just drain the UF permeate 2-3 times your thickness automatically drops. If you have so many constraints.
Employee - Pakistan
December 30, 2021
Q, A, or Comment on THIS thread -or- Start a NEW Thread