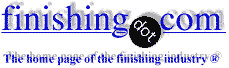
-----
Lead in hot dip galvanising
Q. What is the role of Lead / titanium in the Bath? And can we replace the lead with titanium in bath ? If yes then what will be the impact of having no lead inside zinc bath ?
What is the reason of the spangle formation on strips?
- Bhubaneswar Odisha, India
March 3, 2021
A. Hi Joyoti. We added your question to one of several threads we already had on lead in galvanizing (although I am not familiar with titanium additions to the bath). See thread 38207 for some input regarding spangle, or search the site for lots of threads related to lead and to spangle.
Luck & Regards,
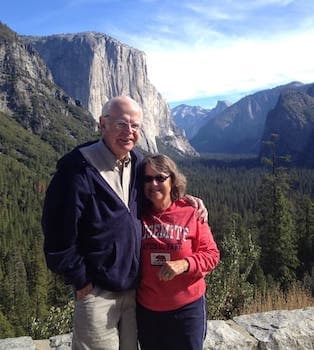
Ted Mooney, P.E. RET
Striving to live Aloha
(Ted can offer longterm or instant help)
finishing.com - Pine Beach, New Jersey
March 2021
⇩ Related postings, oldest first ⇩
2003
Q. Dear Sir,
As a consultant on environmental matters, I have been asked to address the question - "why is some lead added to hot dip galvanising baths?" So far I have received three answers
1) to protect the bottom of steel baths used to hold the molten zinc against corrosion through Zn/Fe alloy formation;
2) to give a "sparkle" to the finished galvanised work;
3) to "wet" the steel so that the final zinc coat is strongly adhering to the steel.
Could someone please enlighten me as to which of these is correct? Also, is it possible to perform hot dip galvanising without the necessity of adding lead to the bath?
Hope you can help,
- Canberra, ACT, AUSTRALIA
A. Not all Hot dip galvanizers use lead in their zinc. You can contact ILZRO (the International Lead Zinc Research Organization) for reasons why some Galvanizers use lead. Type in the letters to search and it will come up.
M. Stroia- Canton, Ohio
2003
A. In "Test for Lead in Hot-Dip Galvanizing Zinc", by Thomas H. Cook and Mohammed Arif, Metal Finishing (USA) October 1991, pages 29 to 31, Dr. Cook gives a test for lead in HDG and describes briefly the reasons for the use of lead in the bath.
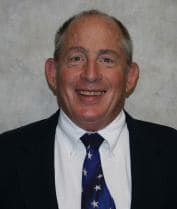
Tom Rochester
CTO - Jackson, Michigan, USA
Plating Systems & Technologies, Inc.

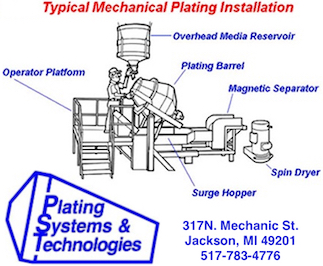
2003
Multiple threads merged: please forgive chronology errors and repetition 🙂
How much lead needed to start up a new galvanizing kettle?
Q. When starting up a new zinc kettle for the first time, how much percentage lead needs to be added into the molten zinc?
Ahmed Shariffmanager - Saudi Arabia
September 14, 2010
A. Dear Mr. Ahmad;
Do you run a continuous Galvanizing line or Hot Dip one?
Why do you want to use Lead in the Kettle? Antimony is better.
Regards,
- Amman, Jordan
September 15, 2010
A. Sir:
In the USA lead is being eliminated from hot dip galvanizing, state by state due to the toxic nature of lead. There is technology available that enables lead-free zinc to work as well or better than leaded zinc for hot dip galvanizing. At this point I would NEVER recommend adding lead to a galvanizing bath.
It is true that antimony improves the results in hot dip galvanizing, however if one "strips" the zinc coating containing antimony the gas stibine (SbH3) is formed which is highly toxic and has caused deaths in hot dip galvanizing.
There are non-traditional ways to reduce the surface tension and the reactivity (of Sandlin Curve reactive steels), which enable excellent results in lead free zinc in hot dip galvanizing baths.
Regards,
Galvanizing Consultant - Hot Springs, South Dakota, USA
September 15, 2010
The hype about lead creeping round the world seems to be getting out of hand. Yes, Pb is toxic, but entrapped in the zinc, at the typical levels that galvanizing exhibits seems trivial. Is there any reputable research to show that this has any adverse health effects?
Many substances are toxic at some concentrations / exposures, (like water, oxygen, etc.) but that doesn't mean they should be banned.
Most zinc is found (in ore form) along with lead, and so has some in it as refined (depending on the process).
Addition to a galvanizing kettle isn't often necessary, but sometimes it's a cost effective means of solving specific problems.
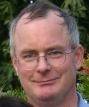
Geoff Crowley
Crithwood Ltd.
Westfield, Scotland, UK
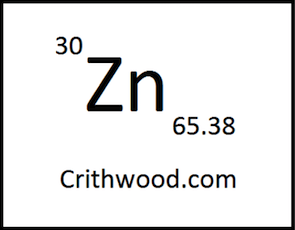
September 17, 2010
A. Geoff,
I know of three cases in which the galvanizing employee who "worked" the dry ash on the kettle exceeded the limit on lead in his air sampling equipment. In these cases the lead in the zinc was about 1% and the lead in the dry ash was about 5%. I know this because I personally tested the lead in zinc and ash. Two of these companies now use MZR machines and two of the three use lead-free zinc.
In the USA, it is my understanding that the most strict state is California. I believe that anything that is toxic or can cause cancer must be labeled. I have seen many of these labels even here in South Dakota (a long way from California). Thus for a galvanizer to sell product in California containing 1% lead, each piece would have to be labeled. I believe that all the California galvanizers use lead-free zinc. There seems to be several other states with pending legislation regarding lead.
On the internet there is a story of a woman that ate wild pig and ingested one lead shot gun pellet, resulting in elevated lead in her blood. She nearly died. After an operation in which the pellet was removed she made a full recovery.
In North Dakota (USA) a hunting group gave wild game (deer) to food pantries for low income folks. The state tested and found elevated lead levels in folks eating this donated wild game. As a result, North Dakota condemned several hundred thousand pounds of deer. The source of the lead was found to be shattered lead bullets.
In my youth I thought nothing of putting slit lead shot on my fishing line by biting down using my teeth. I also once melted lead in my parents' basement to make fishing weights. I overheated the lead and became terribly ill.
Apparently shot gun pellets are now produced in steel and rifle bullets are now produced in copper. Indeed times are changing.
With proper technology, converting from leaded to lead-free galvanizing can be done seamlessly and with an excellent result.
Regards,
Galvanizing Consultant - Hot Springs, South Dakota, USA
It's a long way from eating 100% lead, to touching/using galvanized steel where there was 1% Pb dissolved in the melt.
EU seems no different though in heading in the direction of reducing risk to the extent that prevents industry.
I'm sure that converting to lead-free galv is "seamless" as you said.
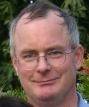
Geoff Crowley
Crithwood Ltd.
Westfield, Scotland, UK
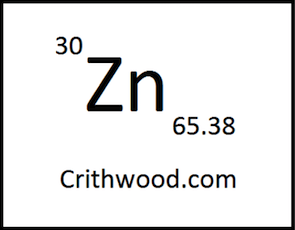
September 24, 2010
September 25, 2010
Q. Geoff,
Your response to conversion from leaded to lead-free galvanizing was the exact opposite of what I expected. Have you ever galvanized with virtually no lead in your zinc? If so, what were your results?
Regards,
Galvanizing Consultant - Hot Springs, South Dakota, USA
A. It's possible to galvanize with "lead free" (I have, but not here), but there doesn't seem to be any evidence that the typical levels of lead in galv melt have caused any health issues with users of galvanized products.
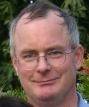
Geoff Crowley
Crithwood Ltd.
Westfield, Scotland, UK
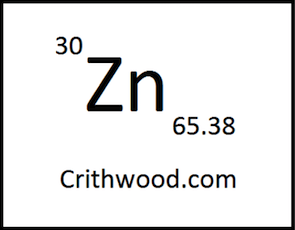
September 29, 2010
Hi, Geoff.
I'm not sure what standard of evidence we should apply to determine whether something like lead in galvanizing is or is not dangerous; with the Reach standards, I'm sure we'll be hearing more of that. But I do agree with the concept that we should not eliminate materials of construction based on fuzzy ideological grounds. Truthfully, every recent time there has been a plane crash my first impulse was to ask whether cadmium, chrome, or lead were omitted from critical parts on ideological grounds. I do not believe that inferior materials & processes with a protocol of more frequent inspection is really a proper substitute for more robust materials & processes.
Regards,
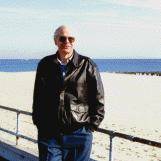
Ted Mooney, P.E.
Striving to live Aloha
(Ted can offer longterm or instant help)
finishing.com - Pine Beach, New Jersey
September 29, 2010
A. Geoff,
My experiences are that lead-free galvanizing is difficult, expensive, and gives a lower quality product. In the USA, due to its toxic nature and environmental restrictions, lead is being eliminated in hot dip galvanizing. Conventionally bismuth and nickel are being used in place of lead. Nickel is "on the environmental radar" in some states in the USA because it is known to cause cancer. To compound these problems, more and more steel in the USA is becoming more reactive toward zinc, causing grey, thick zinc coatings that may not adhere well to the steel. There are unconventional methods to galvanize without lead, nickel, or bismuth.
Ted,
Your point is well taken about safety versus environmental or economic considerations. Several years ago tin was used in hot dip galvanizing. The reason for its use was primarily economic. Increasing the tin content in the zinc caused a lowing of zinc consumption per ton galvanized. During this time, I received many telephone calls from galvanizers asking why their steel was cracking and why their hanging steel wires were breaking. Over time it was determined that above about 0.3% tin was causing the cracking of stressed steel products. Several lawsuits were successful on galvanizers and on at least one zinc company promoting the use of tin. I was concerned about safety issues and sent two letters to ASTM requesting they consider a maximum on tin in hot dip galvanizing. I received no response from ASTM.
Items affected by this tin cracking included: A stressed steel bridge, an overhead highway sign, large diameter steel pilings to support a building in a wet area, a soccer stadium roof support structure, steel scaffolding, large diameter pipe that peeled like a banana and other unreported structural products. It was a difficult time for hot dip galvanizers.
Regards,
Galvanizing Consultant - Hot Springs, South Dakota, USA
October 13, 2010
Sirs:
California proposition 65 (1987) has a list of about 200 reproductive toxicity and/or cancer causing agents. To market in California may require appropriate labels. California also has a "safe harbor" daily dosage for these agents. For lead the "safe harbor" daily dosage is 0.5 micro-grams/day. For a one ounce (28.35 grams) fishing sinker 50,700,000 "safe harbor" daily doses could come from the fishing sinker (28.35 g / 0.0000005 g/day = 50,700,000 days). This is 155,342 YEARS
THIS IS MORE THAN 2,000 LIFETIMES (FOR LEAD).
For nickel (sometimes used in lead-free hot dip zinc galvanizing) the "safe harbor" daily dosage is 0.8 micro-grams/day. Thus it would take 97,089 YEARS to use up one ounce of nickel for daily "safe harbor" doses.
As a kid I used to melt lead in my parents basement and make fishing sinkers. I sold the one ounce sinkers at three for ten cents. Once I over heated the lead and became quite ill.
Times are changing.
Regards,
Galvanizing Consultant - Hot Springs, South Dakota, USA
Hi, Dr. Cook. Thanks for the calculation but I don't quite know the moral. . . Is it that California was not long ago the nation's wealthiest and best-positioned state but drove themselves to bankruptcy through lunacy?
You melted lead in the confines of a basement as a child, and did it wrong, but are still here to talk about it decades later. And I collected mercury from the trash behind the drugstore to play with it numerous times, played with asbestos, lit paper bags of magnesium shavings, and used carbon tetrachloride regularly for everything from reading watermarks as a stamp collector to cleaning the the white vinyl in my convertible.
It's good that we've reduced the permitted exposures to these things, but I'm mortified by extremism, not grateful for it.
Our present course is so laughably penny-wise & pound-foolish that I'm astounded at our blindness. We know exactly how to finish things like lawn furniture so they will easily last 15-20 years or more. But we harass the finishers who use the necessary ounce of phosphate, instead of the ones who don't! With the result that everywhere I look now I see garbage metal that lasts 2-3 seasons or less before rusting to uselessness ... so we have to mine ore to replace it; ship the ore to a smelter; smelt it and roll the steel; ship it to the fabricator; fabricate it, finish it, package it; ship it to a retailer -- only to ship it all to a landfill a half dozen times in the 20 year period instead of once! Countless tons of wasted metal, transportation, energy, packaging ... wasted chances and wrecked economy ... and we have the hubris to be proud that we saved the earth from an ounce of phosphate -- at the cost of tons of unsustainable waste :-)
Regards,
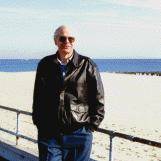
Ted Mooney, P.E.
Striving to live Aloha
(Ted can offer longterm or instant help)
finishing.com - Pine Beach, New Jersey
Layer between zinc and lead in our hot dip galvanizing tank
December 4, 2010Q. Dear everybody
I am working as manager of planning in an organisation doing hot
dip galvanizing. We are facing problem of complete dipping of lattice
steel structure in our zinc bath. This structure is 21' long. Its
lower end is about 24" square and upper end is 12". From
upper end it dips 16' but remaining 5' floated; this is first time in
my career. Complete dip is possible if we hard pressure on both legs
of the structure at lower end. We also noticed that there is a layer
between lead and zinc about 1' from bottom of zinc bath. Anybody have
solution of this issue and want to know about layer formation. I shall
be very grateful. Our zinc is 99.995% pure. We also are using lead and
aluminium. Dr. Cook, you were here in year 1989 or 90.
RESPONSIBLE TO CONTROL PRODUCTION - LAHORE, PAKISTAN
December 7, 2010
A. Sir,
Perhaps you have a large dross build-up and the obstruction is giving you difficulty in sinking the towers into the molten zinc?
Regards,
Galvanizing Consultant - Hot Springs, South Dakota, USA
A. Failure of steel items to sink in zinc can only really be one of two problems.
1. Air not vented causing buoyancy (and high risk of explosion)
2. Obstruction in bath. This could be another piece of steel (not uncommon for a wire to break and a piece to fall in, causing obstruction), or dross. Your comment about a "layer" between zinc and lead suggests this. I've seen dross to 300 mm deep in a kettle, and heard of it being 1000 mm deep (half the kettle's depth). Such dross levels introduce severe risk of kettle wall erosion and subsequent zinc leakage (disaster!)
How often do you dross in terms of drossing/time and drossing/tonne galvanized?
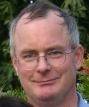
Geoff Crowley
Crithwood Ltd.
Westfield, Scotland, UK
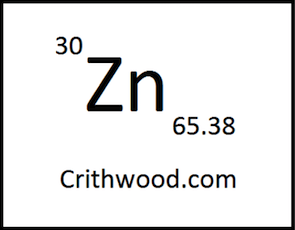
December 9, 2010
Multiple threads merged: please forgive chronology errors and repetition 🙂
Q. Dear Sir, Could you please help to share the information of the usage rate of EZDA and lead in hot dip galvanising production? Currently, our benchmarking is 0.50 kg per 1Mt production output for EZDA & also 0.50 kg per 1Mt production output for lead under normal production running. Is this correct? TQ, From SB Yeo, Malaysia
Yeo Seng BoonProduction - Malaysia
April 26, 2012
? What is the real reason that some people do not like lead in galvanizing?
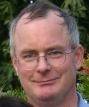
Geoff Crowley
Crithwood Ltd.
Westfield, Scotland, UK
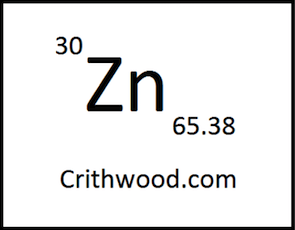
April 27, 2012
May 1, 2012
A. Lead is very toxic and has poisoned humans since ancient times.
Regards,
Galvanizing Consultant - Hot Springs, South Dakota, USA
May 4, 2012
opinion! That lead is toxic is an oversimplification.
Oxygen can be toxic, so can water. In fact most compounds can be toxic, but not at all concentrations, all exposures.
Concentration and exposure are all important.
People don't normally eat galvanizing.
The concentration of Pb in Zn is very low (typically <1%)
So where is the risk located in galvanizing? In the process or the product? At what stages, uses? And to who?
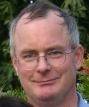
Geoff Crowley
Crithwood Ltd.
Westfield, Scotland, UK
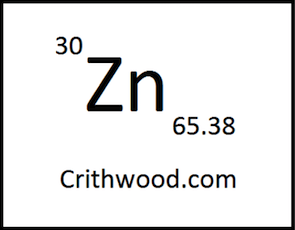
May 12, 2012
opinion! Geoff,
You are industrialist. Your position seems to be-- "Nothing is toxic so why should anyone worry."
For the actual workers in the plant, who work 8 to 12 hours/day for 250 days/year the toxic nature of these heavy metals can express health problems. Check the Health and Safety section of finishing.com.
Just as lead in the bones of ancient Romans show significant lead poisoning, which may well have led to the fall of the Roman Empire, we should learn from the past.
The "safe harbor" dose as defined in California is a few tenths micrograms/day for lead. Thus a one-ounce fishing sinker is sufficient for daily doses for an individual for 130,000 years. Although California "guidelines" according to Proposition 65 seem harsh, there are real reasons for these guidelines. Irrespective, these guidelines are what they are.
Regards,
Galvanizing Consultant - Hot Springs, South Dakota, USA
opinion! Hi, Dr. Cook.
I don't think it's fair to characterize or attempt to assign motives to other people's statements, but I am interested to hear the evidence for the possibility that lead poisoning led to the fall of the Roman Empire. The evidence would have to be fairly convincing before I'd offer it much credence, since the Roman Empire is only one of hundreds of powerful empires throughout history, and every single one fell.
All galvanized and zinc plated hardware seems to labeled with Prop. 65 warnings, whether it contains lead or not -- which seems to achieve exactly the opposite of what you would like to see. We should reduce the use of and our exposure to toxic substances; but in teaching safety classes and in other instances, I've personally seen, time and again, the danger that over-aggressive warnings have placed people in. We seem to have totally forgotten today the story of "The Boy Who Cried Wolf".
Regards,
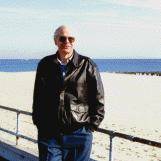
Ted Mooney, P.E.
Striving to live Aloha
(Ted can offer longterm or instant help)
finishing.com - Pine Beach, New Jersey
May 14, 2012
opinion! I don't deny being an industrialist, but the health and safety of those that enable industry (and I too spend a lot of time inside galvanizing plants), is very important.
But that needs to be based on good information. Information is presented in many ways these days, some of them not helpful to those that need it, and not helpful to those that rely on good decisions being taken, based on that information.
To just state that lead is toxic with no qualifiers about dose, concentration, exposure etc isn't very helpful, and could, without qualification be misleading.
I'm still searching for good information that shows that Pb in Zn for galvanizing, at the levels often used (<1%, >0.5%) is a hazard for either those exposed daily to the kettle, or to the consumers of galvanized products.
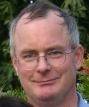
Geoff Crowley
Crithwood Ltd.
Westfield, Scotland, UK
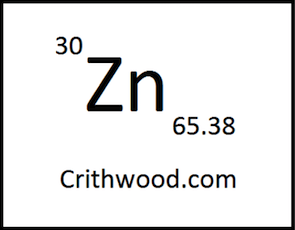
May 15, 2012
May 17, 2012
A. Geoff,
In the USA, the NIOSH Pocket Guide to Chemical Hazards September 2007 lists the LEAD Exposure Limits for NIOSH REL as: TWA 0.050 mg/M3 and the OSHA PEL TWA as: 0.050 mg/M3.
This pocket guide also lists several symptoms of lead poisoning.
About 35 years ago a galvanizer "working" the dry ash had an air sampler attached to his belt and a tube near his mouth. The lead result of the test was 0.058 mg/m3. Blood testing showed elevated lead levels. Lead in the zinc was about 1% and lead in the flux was 374 ppm. The galvanizing plant stopped working dry ash at an annual loss of $400,000/year. They now have a machine to recover zinc from the dry ash.
In my own testing of baghouse dust, out of seven samples, the three highest readings for lead were: 0.72%, 1.03%, and 1.26% (All of these were for "dry" kettle operations.) In contrast, the lead for "wet" kettle operations were all below 0.01%.
The aluminum levels in these baghouse samples were all about 100 times greater than the aluminum in the zinc bath. Thus aluminum oxidizes on the zinc surface and is trapped out as aluminum oxide. Thus, of all the aluminum added, 95% shows up in the skimmings and only 5% is in the zinc coating on the steel. This shows why aluminum must be added to the kettle zinc on a daily basis.
In separate testing of dry ash the lead percentages are commonly between 2% and 5% in zinc baths with around 1% lead. Thus lead likely oxidizes on the zinc surface and is trapped out as lead oxide powder. The fact that high lead levels are found in the baghouse dust shows that the lead must be airborne to be trapped in the baghouse.
At one time I was a lead advocate for galvanizing. Indeed the increased fluidity, and decreased surface tension of the zinc melt is quite improved. In addition there is some evidence that drossing is easier.
Nowadays I have changed my position about lead because I now know that some nasty ash sticks to the steel in leaded kettles. This surprised me very much. Testing of this nasty ash showed it to be about 50% zinc chloride, 0.25% iron and 0.50% manganese (likely from manganese in the flux, coming from the steel). In kettles without lead this nasty sticking ash does not form. Since OSHA is regulatory in the USA it is important to find alternatives for lead in hot dip galvanizing. Indeed there are excellent methods to galvanize without lead.
I do not have data showing that any end user of galvanizing has been harmed by lead in the zinc. There was a lawsuit in California regarding a watering can galvanized by an out of state galvanizer who had lead in his zinc. There were no proposition 65 labels on the cans. According to my source, the lawsuit was settled out of court for a few thousand dollars.
Regards,
Galvanizing Consultant - Hot Springs, South Dakota, USA
Thomas,
That's good useful information, thanks.
I have some other sources also coming, and can assess the risk more quantitatively now.
I think that the sources of exposure are well controlled, so there doesn't seem a panic to make sudden changes, but the whole risk needs to be evaluated properly.
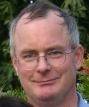
Geoff Crowley
Crithwood Ltd.
Westfield, Scotland, UK
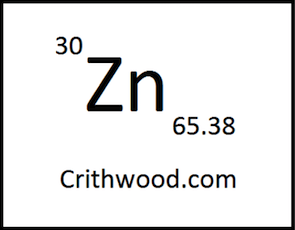
May 17, 2012
September 21, 2012
Q. Dear Sir,
What is the best addition ratio for lead in galvanizing pot?
Based on what lead is add into kettle pot? either:
1)During drossing
2)Output (tonnage)
How should percent of lead should be maintained in kettle pot?
For flux solution, what is formula to maintain it?
Thanks/ Regards
- Rawang, Selangor, Malaysia
![]() |
A. Dear PJ; galvanizing - Ankara, TURKEY September 25, 2012 September 25, 2012 A. Sir: Galvanizing Consultant - Hot Springs, South Dakota, USA "Internet advertising price-demand curve: Infinite demand at zero cost / zero demand at infinitesimal cost", Thomas J. Pullizzi (co-founder of finishing.com), 1995.
Regards, ![]() Ted Mooney, P.E. Striving to live Aloha (Ted can offer longterm or instant help) finishing.com - Pine Beach, New Jersey |
A. There is a variety of information about lead in galv zinc. Some good, some a bit misleading (in both directions).
1% Pb dissolved seems a very common level to run in much of Europe.
Many running Pb free experience problems with fluidity, and colour. Some have experienced dross issues on kettle floors. (Pb is often used to float the dross off the kettle floor)
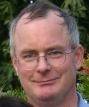
Geoff Crowley
Crithwood Ltd.
Westfield, Scotland, UK
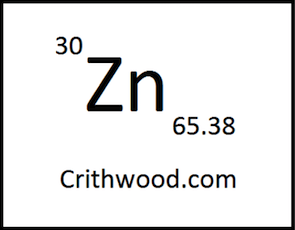
October 4, 2012
October 11, 2012
Q. Dear Sir,
Currently we are using Korea special high grade zinc jumbo block (Zn: 99.995% min)
The Chemical composition of these blocks are:
1)Zn 99.996
2)Al <0.0001
3)Cd <0.0001
4)Cu 0.0006
5)Fe 0.0003
6)Pb 0.002
7)Sn <0.0001
I have few questions:
1)Is there any proof show that-usage of zinc can cause "white rust " to the product.
2)What is the chemical composition for quality zinc block?
Thanks.
galvanizing - Rawang, Selangor, Malaysia
A. Sir:
By using this SHG zinc as you receive it, I would expect great difficulty in skimming the molten zinc surface and having the zinc stay liquid long enough to withdraw the steel. I would also expect dull grey coatings (a bit brighter if aluminum is a added). The zinc surface is also likely to have both dross pimples and numerous smaller pimples on the product. Zinc usage is likely to be 25% higher than it could easily be.
Regards,
Galvanizing Consultant - Hot Springs, South Dakota, USA
Q. I am going to start a new galvanizing plant. My kettle capacity is 150 MT of Zinc. How much lead must I put in the kettle before firing? And what grade of lead to use?
Shabbir Qureshi- Jubail ,North Province, Saudi Arabia
December 24, 2013
A. Sir,
If you wish to use lead in your zinc then add between 1% to 1.5% lead by weight of the zinc in your kettle.
I do not like lead in the zinc for a number of reasons, one of which is that leaded zinc attacks cast iron excessively and some of the zinc coating falls off into the molten zinc.
I now have 28 kettles using my process with excellent results all using no lead.
Regards,
Galvanizing Consultant - Hot Springs, South Dakota, USA
December 26, 2013
Q. Hi,
I want to know if we remove lead from the galvanizing dip, what will be the result on final product? How will it effect the surface quality of HDG?
Thanks
- UAE, Dubai
January 27, 2014
A. Hi Mina. Your question is the subject of this thread, as well as letters 38207, "Minimize/maximize spangle in hot dip galvanizing", 24568, and "Lead (Pb) in Hot Dip Galvanizing". The topic is not easily dispatched in a paragraph or two, and invariably you don't simply remove the lead, you do some other things as well. But we'll see if any knowledgeable galvanizers can respond to you. Good luck.
Regards,
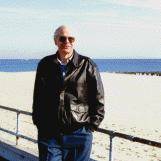
Ted Mooney, P.E.
Striving to live Aloha
(Ted can offer longterm or instant help)
finishing.com - Pine Beach, New Jersey
January 28, 2014
A. Dear Mina,
We use lead in our coil galvanising continuous line in Iran; we add lead just for increasing the size of spangles on sheets and coils.
R&D Center - Qazvin, Iran
January 30, 2014
Q. Sir,
My kettle capacity is 181 MT. Zinc
How much lead in kettle?
Tata Projects Ltd. - Nagpur.Maharastra , India.
October 19, 2019
A. Sir: In the USA lead is now almost never used in the zinc anymore. Bismuth at 0.03% in the zinc has replaced the lead. There are other ways to make up for not having lead.
Regards,
Galvanizing Consultant - Hot Springs SD USA
October 29, 2019
Q. Does anyone know of a published investigation/risk assessment for Lead emissions to air from hot dip galvanizing?
Peter JohnsEnvironmental Assessment - Perth Western Australia
October 25, 2019
Q, A, or Comment on THIS thread -or- Start a NEW Thread