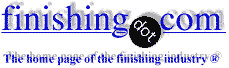
-----
Lead (Pb) in Hot Dip Galvanizing

⇦ Tip: Readers want to learn from your situation;
so some readers skip abstract questions.
Office worker - KOREA
April 7, 2025
![]() |
A. Hi Lee, Q. Even after looking up a lot of information, it is explained that the maximum solubility of lead in hot-dip galvanizing is about 1.2~1.6% and that lead exceeding that amount is deposited at the bottom of the kettle. Office worker - KOREA April 7, 2025 |
A. Hi again.
Now it's become interesting. Thanks!
Luck & Regards,
Ted Mooney, P.E. RET
Striving to live Aloha
(Ted can offer longterm or instant help)
finishing.com - Pine Beach, New Jersey
The limit of solubility of Pb in Zn is about 1.1- 1.2%. Any more Pb added to the kettle sinks (due to much higher density) to the bottom of the kettle as liquid Pb and sits under the dross.
If you are getting an analysis of 2% then either the sampling method or the analysis is suspected to be wrong. Was the sample representative of the whole? Could contamination have happened?
What was the analysis method?
Liquid Pb under the dross should not exceed about 50 mm. The reason is that the dross floating on top of it would be higher in the kettle, even higher than the dross protection insulation in the furnace outside the kettle. If the zinc locally gets overheated due to dross being on the inside at a higher level, the heat cannot dissipate and the heat circulate in the zinc.
Zinc is continually dissolving the kettle. Normally at about 2 mm/year of kettle (at 450 °C), but raise the temp to 550C and that rate increases to about 10 mm/day.
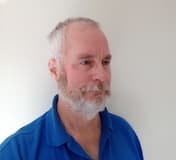
Geoff Crowley, galvanizing consultant
Crithwood Ltd.

Bathgate, Scotland, UK
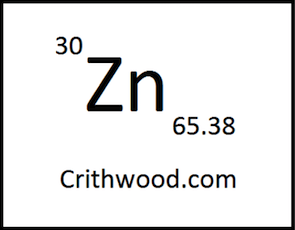
⇩ Related postings, oldest first ⇩
What is the purpose of lead in hot dip galvanizing?
for Engineers, Shops, Specifiers
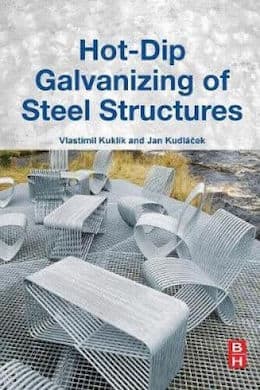
avail from eBay, AbeBooks, or Amazon
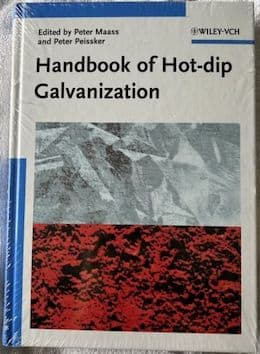
avail from eBay, AbeBooks, or Amazon
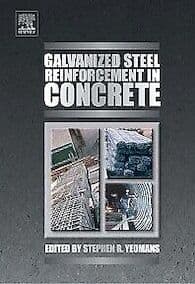
avail from eBay, AbeBooks, or Amazon
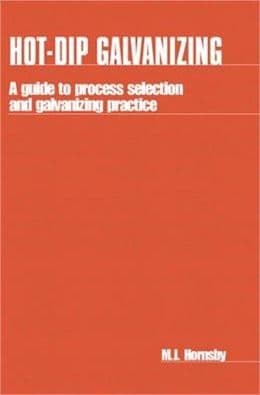
avail from eBay, AbeBooks, or Amazon
avail from Amazon
"User's Guide to Hot Dip Galvanizing for Corrosion Protection in Atmospheric Service" by NACE (1997 only rarely avail.)
avail from AbeBooks, or Amazon
(as an Amazon Associate & eBay Partner, we earn from qualifying purchases)
Q. In hot dip galvanising, why do we use a low level of lead along with Zinc with other metal composition in metal pot, and what is the basic function of lead in hot dip galvanising?
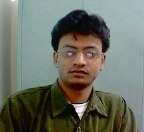
Vipin Jain
galvanised steel manufacturing - Biratnagar, Morang, Nepal
2003
A. Hot-dip Galvanizing is based on alloying Iron with zinc. Traces of iron introduced into the zinc kettle(carry-over with the material to be galvanized from wet pre-treatment, from the steel zinc-kettle-wall and the material to be galvanized will alloy with the zinc too, thus forming zinc-iron alloy particles called dross. This dross is some heavier than the zinc and will slightly sink to bottom of the kettle. Lead has two functions: 1. dissolved lead in the zinc-melt has influence on the fluidity of the zinc and will help dross particles sink to the bottom - floating dross particles will cause roughness on the material to be galvanized(bad quality) 2. The lead layer on the bottom of the kettle will prevent dross will be stuck to the iron kettle-bottom and makes it possible to remove the dross from the bottom of the kettle, because lead is heavier than the dross and will not alloy with the dross and zinc - so dross floats on the lead-layer.
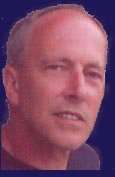
Dolf van den Berg
- Leusden, The Netherlands
2003
A. DEAR SIR,
IN HOT DIP GALVANIZING, PURE LEAD CHARGES IN POT SAVE THE LIFE OF POT, LEAD BEHAVES AS A CUSHION EFFECT.
- bombay, India
September 13, 2009
What can be substituted for lead?
Q. In my previous question, I asked, why we use low level of lead in zinc kettle, and I got a satisfactory answer. Now will anyone please tell me, can we use another metal in place of lead in zinc kettle for such functionality in the galvanising process.
Regards,
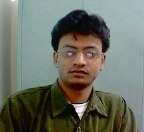
Vipin Jain [returning]
galvanised steel manufacturing - Biratnagar, Morang, Nepal
2003
A. Coming back on your second question I don't know the reason why you'd like to change lead for something else, but in Scandinavia lead will be forbidden for environmental reasons.
Bismuth or Tin could be elements to replace the function of dissolved lead. These elements cause a high fluidity of the zinc and a good wetting of the steel. De-drossing of the kettle is hardly a problem. Cominco Canada made investigations adding Bismuth to Zinc for hot-dip galvanizing.
Regards,
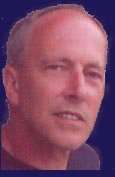
Dolf van den Berg
- Leusden, The Netherlands
2003
Q. SIR-
I WANT TO KNOW - HOW TO REFINE THE LEAD FROM THE BOTTOM LAYER OF LEAD USED IN HOT DIP GALVANISING TANK? I.E., ZINC BASED LEAD, CONTAINS DROSS ALSO? AND WHAT WILL BE THE RECOVERY EFFICIENCY?
- HYDERABAD, India
2006
What is ideal lead percentage?
Q. So what would be the ideal amount of Lead to charge in a Zinc bath (lead layer thickness or % zinc)?
Jaydip Atodaria- Harare, Zimbabwe
October 19, 2010
A. Hi, Jaydip. Environmentalists think the ideal amount is zero :-)
You can search the site for "lead-free" galvanizing. Good luck.
Regards,
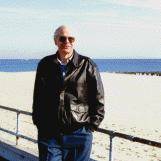
Ted Mooney, P.E.
Striving to live Aloha
(Ted can offer longterm or instant help)
finishing.com - Pine Beach, New Jersey
Q. Dear Sir,
Thanks for your reply. Our problem is we have a zinc tank 10x1.0x1.5m deep which leaked and we are in the process of changing the kettle. From the pot wear it seems it wore out due to dross. Will adding a layer of lead increase the effectiveness of drossing? Then in that case we need to know when charging the new bath how much lead should be added?
Thanking you.
- Harare, Zimbabwe
A. Sorry Jaydip, I can't answer that. But if you patiently search the site, similar subjects have been discussed at length by true experts several times. Good luck!
Regards,
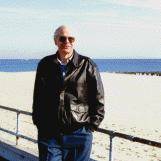
Ted Mooney, P.E.
Striving to live Aloha
(Ted can offer longterm or instant help)
finishing.com - Pine Beach, New Jersey
A. Lead ideal amount is 1.3%.
Khizer Abbas- Pakistan
May 3, 2012
How to lower the Lead content in the zinc kettle
Q. Hi,
We have a content of 0.11% Pb in our zinc kettle.
Due to new restrictions, we have to lower our Pb content to 0.05% Pb
Are there any other ways to lower the Pb content, then pump out zinc and replace it with new SHG zinc?
- Sweden
June 18, 2013
A. Its interesting that someone is forcing you to reduce Pb content. Can you say why they want that?
I think you could perhaps pump the Pb rich Zn off the floor of the tank and so reduce it that way. If you get the free Pb out, and then only replace with Zn without Pb, then it must come down. At about 1% Pb in solution, you probably have some free Pb on the bottom. Getting that out first would help.
Is there a time limit by which you must do this? If not, I think you could get it down in 6 months or so without a complete pumpout. But I'm guessing this, I don't know of anyone trying it.
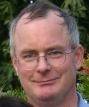
Geoff Crowley
Crithwood Ltd.
Westfield, Scotland, UK
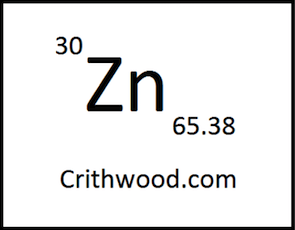
July 2, 2013
A. Sirs:
Lead solubility in zinc depends on temperature:
800 °F 1.0% Lead (Pb)
820 °F 1.2% Lead
840 °F 1.4% Lead
860 °F 1.6% Lead
Calculation to determine lead content in zinc as it is used and replaced by SHG zinc:
(Fraction Changed/Day)Raised to Power,Days Times Orig. Pb%
Example:
500,000 pounds zinc in kettle.
5,000 pounds zinc consumed each work day.
0.11% Lead Original Lead percent.
(500,000-5,000)/500,000 = 0.9900
(0.99)Raised to power 20 days times 0.11% equals 0.090% Pb
(0.99)Raised to power 60 days times 0.11% equals 0.060% Pb
(0.99)Raised to power 80 days times 0.11% equals 0.049% Pb
Notes: "days" are work days. Use "x raised to power y" on scientific calculator. Thus put in 0.99 hit enter and then put in 20 (days) then hit "=" Then multiply by 0.11. At 0.11% lead there would be no benefit to pump from the kettle bottom. Be sure to use "brightener bar (10% Al 90% Zn) that DOES NOT CONTAIN LEAD.
The real issue here is that zinc with no additives does not work as well as zinc with lead. I am working on this issue just now with excellent success and no need for lead.
Regards,
Galvanizing Consultant - Hot Springs, South Dakota, USA
July 5, 2013
A. On our last kettle pump out, which started with a dissolved Pb content at 1.0%, the Pb content of the bottom zinc was about 80% and we got 2 ingots out like that.
So while the theory might say its not worthwhile, the practical experience suggests that a significant reduction might be possible way to hasten the dilution process.
We have not used the technique to take Pb out, but have taken Pb out as an unintended consequence.
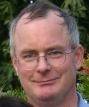
Geoff Crowley
Crithwood Ltd.
Westfield, Scotland, UK
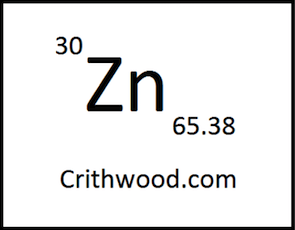
July 8, 2013
Geoff,
In your case with 1% lead, you obviously had liquid lead under the dross. In the other case with only 0.11% lead it is obvious that there is no liquid lead under the dross.
Regards,
Galvanizing Consultant - Hot Springs, South Dakota, USA
July 10, 2013
A. Apologies: I mis-read the Pb level in the original post.
Yes, reducing from 0.11 to under 0.05% is another matter entirely.
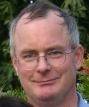
Geoff Crowley
Crithwood Ltd.
Westfield, Scotland, UK
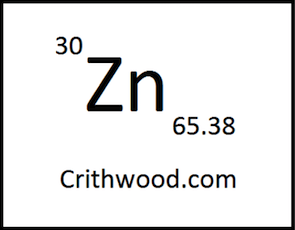
July 16, 2013
Q. Dear sir,
I want to know can I ingot lead at continue my production? And your answer is no, so when I can use lead ingot at kettle?
Different colour created in my kettle this type problem created. I think that this type problem created after ingot lead during continue production. What you say about this sir?
- Vadodara, Gujarat, India
December 20, 2013
A. Hi Kadva. Apologies but I don't understand your question. Hopefully someone who is more familiar with this may understand what you are trying to ask.
Regards,
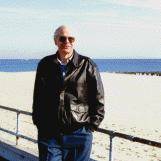
Ted Mooney, P.E.
Striving to live Aloha
(Ted can offer longterm or instant help)
finishing.com - Pine Beach, New Jersey
December 20, 2013
Q. Dear sir,
Thank you for your reply.
Sir, I mean can I add lead into the pot while continuing my galvanizing production?
- Vadodara, Gujarat, India
December 20, 2013
Q. Dear experts,
How to reduce the lead percentage in bath, from 0.2%
- Jeddah KSA
March 28, 2016
Q. How and what % to use Lead in new zinc kettle for long life of kettle?
SUPRABHAT BANERJEE- Jaipur, India
April 11, 2016
A. Dear Mr. Suprabhat,
It is advisable to add lead after 10 days of complete melt out of ZINC in new kettle. Do not operate with more than 50 mm of lead in bottom of kettle.
- Vadodara, India
August 12, 2016
Q. In our Hot Dip Continuous Galvanizing line, we are using Tin/Antimony for Spangles apart from Lead, we want to stop adding the Tin in the Zinc bath, what would be effect whether brightness would be affected or spangle formation. As per my knowledge, Lead & Antimony are main elements which forms the spangles on the Galvanized surface. If not what is the actual role of Tin in Zinc bath composition.
Kantilal P. TrivediQuality Head-Cold rolling & Galvanizing of Steel - Baroda, Gujarat, India
April 15, 2016
A. DEAR KANTILAL
TIN AFFECTS GLOSSINESS OF THE SURFACE. THERE IS NO SPANGLE CREATION BY ADDING THE TIN. YOU CAN USE LEAD AND ANTIMONY FOR SPANGLE.
REGARDS,
- ANGUL, ODISHA, India
August 18, 2016
Q. Dear sir,
We are adding 2 kg (0.1%) of lead to our 2MT hot dip galvanizing pot. Our regular coating production is 6-7 MT per day of SGI casting. Our coating quality also okay and castings also passed after 6 dip test in copper sulphate
⇦ on
eBay or
Amazon [affil link] solution. I want to know whether 0.1% lead addition daily is correct or not.
- Abu road, Rajasthan, India
January 7, 2019
A. Sirs: Tin in the zinc is known to cause the galvanized steel to crack. In the USA a stressed steel bridge was destroyed by tin. In the UK a stadium had its roof support structures crack due to tin in the zinc. Too much bismuth causes white rust.
Lead in the zinc increases the reactivity of malleable cast iron and produces coating that side off the castings. In Ireland only one galvanizer is lead-free and it is known for good galvanizing of castings.
Lead in the zinc does not protect the kettle.
Regards,
Galvanizing Consultant - Hot Springs, South Dakota, USA
January 8, 2019
A. Concerning lead in the kettle.
Pb has maximum solubility in Zn at about 1.2% at 450 °C. Further additions than this just accumulates on the kettle bottom as it is the most dense among Zn, dross and Pb.
Zeta dross crystals are not very dense compared to Zn, and the addition of Pb causes them to sink as they combine with Pb in solution, become heavier and sink. More floating dross is found in Pb-free kettles than those with 0.6% Pb or more.
Pb-free is rare (as in 0%) as much Zn supplied has some Pb in it; the ores are found together in nature, so they end up being processed together, and only by active separation is "pure" Zn made.
Pilling (perhaps worlds premier kettle maker) in their book "Galvanizing Kettles - recommendations for the user" recommend having minimum 0.6% Pb.
Sn in the melt is another matter. Rather than actually CAUSE cracking, it aggravates an existing problem. The most recent extensive research on this shows that the galvanizing isn't the cause of the cracking, even in Sn containing melts, but it reveals and exaggerates cracks that are there in the first place but undetected.
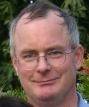
Geoff Crowley
Crithwood Ltd.
Westfield, Scotland, UK
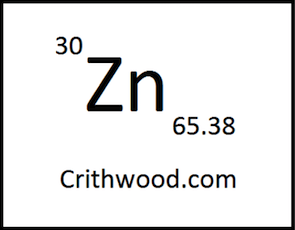
January 9, 2019
![]() |
A. Geoff, In the USA the only prime Western producer (e.g. 1% lead) tried to switch to electrolytic zinc (e.g., near 0% lead) but technology did not work properly. In the old days, I liked lead in the zinc and there are certainly some advantages, but now I like lead-free better. I believe the top half-inch of zinc in the kettle is "special." In the old days floating dross was common on Monday mornings. We have found ways around this and floating dross for my clients is virtually zero. Does Pilling give any reason for recommending above 0.6% lead? Galvanizing Consultant - Hot Springs, South Dakota, USA January 10, 2019 Q. Sir, Thanks for the reply, Some things are clarified, however still my doubt of 0.1% Lead addition in molten zinc is correct or not? - Aburoad, Rajasthan, India |
Lead in Galvanizing: SEM and Melt Analysis gave very different answers
Q. Hi My Dear,
Please Guide Me: I'm Galvanizer, One of our customers after testing the SEM method found 4.30% lead and 1.82% aluminum in galvanize Coating , while melt analysis at the time of galvanizing with a spectrometric method (Quantimetric Method) gave 0.0001% aluminum and 0.95% lead.
Measures:
1- Is the conclusion of coating quality consistent with the test results based on the SEM method? And whether the subscriber can refer to the components using SEM method?
2- Is the melt analysis test sufficient in principle for the coating quality according to ASTM B9 & ASTM A123?
technical Manager - Tehran, Iran
August 26, 2019
Ed. note: We believe "ASTM B9" is a typo, Shahriar.
A. Dear Shahriar,
It would be extremely easy to have a melt with content 0.95% lead and find areas on an SEM analysis that would show 4.30% lead - this is because EDS/EDX is only a localised measurement, even before you take in all the potential error sources. It is not a bulk measurement of composition, and therefore I do not think it is suitable for this testing. I would be very surprised if any of the relevant standards mentioned it.
Atomic absorption spectrometry
⇦ on
eBay
or
Amazon [affil link] to ASTM E536 is suitable for both aluminium and lead in zinc and is referenced in ASTM B6-23 (Standard Specification for Zinc)
- Gloucestershire, UK
September 3, 2019
Q. Is there any substitute for charging lead alloy in continuous galvanizing? How lead-free zinc coating is initiated?
Hitesh Poshtiwalaemployee - Surat , Gujarat, India
September 6, 2023
Q, A, or Comment on THIS thread -or- Start a NEW Thread