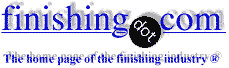
-----
Electrical conduction properties of nickel plating
October 13, 2021
Q. Hello, we are a company working in RF / medical field.
I'd like to know which is the electrical behavior of an electroless nickel (or copper, or silver) plated layer on the surface of a stainless steel tube.
In case of nickel, for example, the resulting layer is not pure nickel but a sort of nickel/phosphorus alloy (if my understanding is correct).
So the electrical conductivity of such material is less than the one of pure nickel. How much?
I posed the question for nickel because i've seen that electroless nickel deposition is very common, and the performances in terms of RF attenuation should be enough good using nickel. But I could consider also electroless copper or silver plating, giving even better results if the electrical conductivity of the deposited layer is the same of the one of pure metal.
I cannot use electroplating because it's not recommended for this case (too complex setup, too expensive)
Thanks in advance for anyone who can help me.
- Sesto Fiorentino (Florence, Italy)
A. Hi Vasco. We have appended your question to a thread where Sjamp VanEsch has already answered your question about the conductivity of electroless nickel.
But you should be very cautious about your early decisions, so you might want to consider retaining a plating consultant if you will be doing a lot of plating. Here are some issues I'd be concerned about:
• getting sufficient adhesion if you cannot use electroplating might be a problem because a Wood's Nickel Strike (an electrolytic process) is the standard way of getting good adhesion on stainless steel.
• electroless nickel is much more expensive than electrolytic nickel; if the parts are small & few, you may be able to ignore this, but in general you never switch from electrolytic nickel to electroless nickel to save money :-)
• when the complexity of electrolytic nickel concerns you, you need to know that electroless nickel has plenty of its own complexities :-)
You might want to get plating shops to quote on these parts before you install a system of your own, so you know what will be a reasonable expenditure for an in-house system. Good luck!
Luck & Regards,
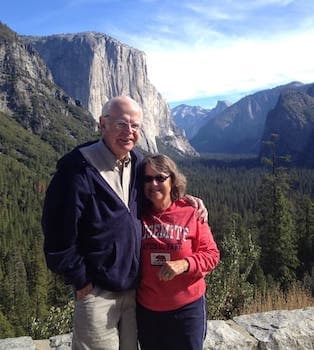
Ted Mooney, P.E. RET
Striving to live Aloha
(Ted can offer longterm or instant help)
finishing.com - Pine Beach, New Jersey
October 2021
Mr. Mooney, thank you for your reply and sorry, I did not see the reported thread. Sorry for my poor English.
Q. The plating should be performed "inside" a stainless tube with about 2 mm bore.
My post was concerning electroless nickel because I read another thread in this very interesting site (www.finishing.com/402/43.shtml) in which it's shown that it's impractical to perform electrolytic deposition in this case, because of too complex setup: an electrode, inside the tube and insulated from it, is needed in order to evenly distribute the electric current and the solution has to be pumped inside the tube.
The conclusion in this thread was that electroless plating would be better for this case.
Starting from ideal copper which has σ = 5.8e7, nickel is about 4 times worse while stainless steel 304 is about 50 times worse. with 3% P it would become 16 times worse. The gain w.r.t. steel is not so high.
I need to assess if this gain has enough usefulness to justify this process step.
RF engineer - Sesto Fiorentino (Florence, Italy)
October 14, 2021
Vasco,
Electroless nickel would be the best to plate inside of this tube. You are correct in that regard. However, for electroless nickel to adhere to stainless steel, you must first plate with a nickel strike. This is an electroplating process and a very inefficient one at that.
Unless someone else has a better idea about how to gain adhesion with electroless nickel over stainless in a 2mm diameter tube, I would suggest a different material for your tube.
Why does your tube need to be stainless? If you use a carbon steel tube and plate the inside and outside of it, would that work instead? The part would then have a similar look to stainless steel. Carbon steel also conducts current better than stainless. It could be a "win-win" if you switched to a carbon steel tube that would not require a nickel strike before the electroless nickel plating.
Plating Manager - Hammond Louisiana
⇩ Related postings, oldest first ⇩
Q. Is there a difference in electrical conductive properties between bright nickel plating and electroless nickel plating? I have been using electroless nickel plated beryllium copper for an electrical contact and am finding less than optimal conductivity. Is there another type of plating that would provide good corrosion resistance and better conduction?
Kjersha Wanlass- Berkeley, California, USA
2003
A. Dear Mr Wanlass,
There is a difference in electrical conductivity properties. The specific resistance of electroless nickel with 6-7% P is about 50-70 micro-ohm-cm, in general the more phosphorus the more resistance. For example 3% P gives a resistance of about 30 micro-ohm-cm, 8-9% P gives a resistance of about 90-110 micro-ohm-cm. Heat treatment can lower the resistance a lot. Also the amount and kind of additives in the plating bath influences the electrical resistivity.
The specific resistance of bright nickel is about 12-19 micro-ohm-cm, depending of what kind of bath(chloride,sulphate) and what additives are used. Pure nickel, plated out of a bath without any organic additives,has a specific resistance of about 7-8 micro-ohm-cm. Plating silver over nickel or NiP gives excellent electrical properties and provides good corrosion resistance.
Kind regards,
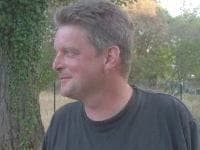
Sjamp van Esch
- Eindhoven, The Netherlands
2003
Q. I have electrical contact between mild steel to mild steel blocks, diameter 300 mm. The current flowing is 600 A TRMS, AC (50 Hz). I need to know what plating is best in this scenario. Also, will plating lower the contact resistance, as plating introduces two more contacts in principle as steel to steel contact becomes steel to nickel to nickel to steel after plating. Please clear these doubts.
Sanjay Patelresearch student, high temperature sintering applications - Surat, Gujarat, India
December 15, 2012
A. Hello Sanjay. Two different types of resistances are involved in contact applications: the internal resistance of the metals, and the contact resistance where the two surfaces are touching, which is high because of dirt and oxides on the surfaces, and incomplete contact.
When two steel surfaces contact each other out in the open air, there is high resistance because of the rust, dirt, and rough surfaces which the electricity must traverse. When two nickel plated surfaces contact each other, the resistance is much lower because the nickel surface is smoother and the oxide film is much thinner. When steel is electroplated with nickel, there is true metallurgical joining of the two surfaces, and very low resistance at that joint. So you will find lower resistance and a much more satisfactory contact by nickel plating the steel surfaces.
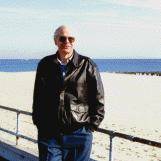
Ted Mooney, P.E.
Striving to live Aloha
(Ted can offer longterm or instant help)
finishing.com - Pine Beach, New Jersey
December 20, 2012
⇦ Tip: Readers want to learn from your situation;
so some readers skip abstract questions.
Q. Hello,
Please reply to below:
1 can brass and steel be nickel and then silver electroless plated?
2 is this a good electrical contact for 220 volt ac 0.07 amp current flow, for just resistive load?
3 what contact pressure is required for this load?
Thanks
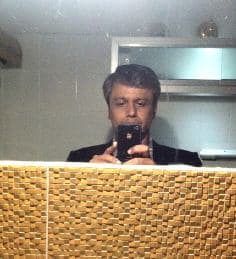
Waseem Muggo
- Lahore, Pakistan
⇦ Tip: Readers want to learn from your situation;
so some readers skip abstract questions.
Q. Please reply as:
1 nickel plating and then silver plating by electrolysis [ed. note: electroless?]
2 what is pressure required for contact for 220 volt 0.70 amp resistive load?
3 is max surface area of contact better than minimum?
- Lahore, Punjab, Pakistan
June 29, 2013
Hi cousin Waseem. The answer to question 1 from June 28th is yes; I can't answer the others from that date.
I think question 1 from June 29th is asking whether nickel plating followed by silver plating can be done electrolytically, and yes it. Again I can't answer question 2.
Question number 3 is probably not really answerable. On a microscopic scale, the smaller contact may actually have more area in contact: knife edge contacts are often used for better contact even though the contact area is small, and 'wiping' contacts are often employed where flat contacts are used. So minimum may be best for contact, but the area of brass or steel carrying the current may be more important.
As you see, nobody has responded despite this page being viewed thousands of times. It usually will work better if you can engage readers in conversation by introducing yourself, explaining what it is you are working on, and why these questions have come up. Nobody likes 'flash card quizzes', and nobody likes publicly announcing "I don't know", which they'll have to say even if they know the answer to 5 of your questions but not all 6 :-)
Regards,
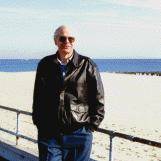
Ted Mooney, P.E.
Striving to live Aloha
(Ted can offer longterm or instant help)
finishing.com - Pine Beach, New Jersey
June 5, 2019
Q. I am an automotive switch engineer and I am trying to piece together Hardness and Resistivity info for the various types of nickel plating. I am looking for Resistivity of Sulfamate Nickel and semi-bright nickel. This is what I have so far:
Watts 130-200 HV 7-8 micro ohm cm
Sulfamate 170-230 HV ??resistivity??
Semi-bright 300-400 HV ??resistivity??
Watts w/brightener 600-800 Hv 12-19 micro ohm cm
Low Phos 620-720 HV 30 micro ohm cm
Mid Phos 550-620 HV 65 micro ohm cm
High Phos 500-550 HV 120 micro ohm cm
Contact Resistance is a function of resistivity and the area of contact which is related to Hardness
BCS-ABS (former TRW Automotive) - Oxford, Michigan, USA
by William Safranek
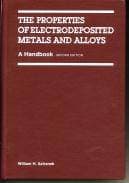
on eBay or Amazon
or AbeBooks
(affil link)
A. Hi Allen. Safranek includes a 75-page chapter on the properties of electroplated nickel.
Regards,
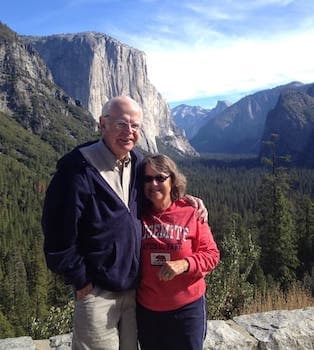
Ted Mooney, P.E. RET
Striving to live Aloha
(Ted can offer longterm or instant help)
finishing.com - Pine Beach, New Jersey
A. If you are looking for wear resistance of nickel plating you may consider using an electroless nickel plate.
Isaac BrownTechnical Sales Rep - Cleveland, OH
July 30, 2019
Q, A, or Comment on THIS thread -or- Start a NEW Thread