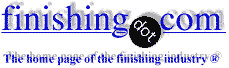
-----
pH is dropping/decreasing in nickel sulfamate plating bath
Q. I am using Nickel sulphamate bath to do heavy deposition on worn out shafts. I have just started the bath. I notice that the pH of the bath drops as the deposition takes place. I started out at 4.2 pH and after a day, the pH was down to 3.8. What can be the reason for this. Is it due to differences in the anode and cathode areas? Is there any other way to increase it (I don't want to add nickel carbonate as the quality of it is not good). The drop is pH is causing a problem to the deposit (it lifts off).
Nitin Kibe- Pune, India
2000
A. Most of the time it is caused by the anode going passive. This can be caused by not having enough Cl or Br in the solution (stay within recommended limits). My guess is that you are using electrolytic nickel instead of SD nickel, which is the optimum anode in this solution. If your pH is dropping, when it should be rising, your nickel content is probably slightly dropping also. Optimum anode to cathode ratio is about 1:1 to about 1:4^4:1 if I remember correctly.
- Navarre, Florida
2000
Q. I am using "S" nickel pellets. and the anode to cathode area ratio is around 1.25 I have not checked the nickel level in the solution. Should I have an optimum quantity of nickel sulphamate solution in the bath. I guess that I am using less quantity for higher current. Is there any thumbrule such as so many liters/amps of electrolyte should be there.
NItin Kibe [returning]- Pune, India
2000
A. I have to go along with everyone else on the S-Nickel. The S or SD refers to sulfur depolarised nickel. This anode material has a small amount of sulfur incorporated into the nickel when it is produced. The sulfur increases the activity of the nickel. SD nickel will dissolve in a plating bath containing little or no chlorides whereas regular nickel will not dissolve unless chlorides are present. Several nickel companies supply SD nickel. Of course nothing is free and SD nickel will produce slightly more anode residue because the sulfur does not dissolve in your bath and remains in the anode basket. Good Luck.
Don Piett- Thompson, Manitoba, Canada
2000
A. A normal sulfamate nickel tank will grow in nickel content because the anode is essentially 100% efficient while the cathode is 99+ % efficient. Why are you using pellets vs "S" rounds? They cost more and are normally used for tiny tanks of internal anodes. For anode area, you should only count the front half of the anode basket. The back half does not really do much. My last post I said an anode to cathode ratio of 1:1 to 1:4. My mistake! That should be 4:1. anything between 1 and 2 is optimum. What are you using for baskets? If you are not using a strike, you could be dragging in your caustic cleaner. This will cause some big problems with your plate adhesion as well as lowering the pH. Check your rinses.
James Watts- Navarre, Florida
2000
Q. Let me describe the tank. the cathode is a metal rod of Dia around 240 mm. The anode is Titanium mesh of dia 300 mm. the gap between electrodes is around 30 mm the anode is around 40 thick filled with "S" pellets. the depth of immersion is around 10% of the total cathode area.
From what James has said, the ratio of anode to cathode here works out to just over 1. Is that what causes the problem? I think I can experiment by masking the cathode so that the ration of anode to cathode is pushed higher. I am still plagued with this problem due to which I have to remove the solution after every load and treat it with nickel carbonate (plus dummying at low CD due to the treatment).
Nitin Kibe- Pune, India
2000
A. Hi Nitin.
I think it easier to get you a good answer if you tell us what amperage you use in the nickel solution. How is the titanium basket constructed. The titanium hook must have connection pressure. They must be turned around their axis, to get a good connection. If you have a bad connection you get more oxygen with the anode; they will passivate. Regards Anders S
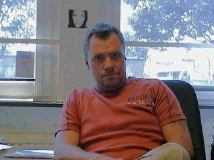
Anders Sundman
4th Generation Surface Engineering
Consultant - Arvika,
Sweden
2000
Q. The contacts of the anodes are bolted to the busbars. There is no heating at the interface. The cathode area is around 4 sq dm. the anode area is around 5 sq dm. The current passed is ramped up from 0 to 120 amps. The total time for the job is around 6 hours.
Nitin Kibe- Pune, India
2000
A. Nitin. I think the anodes get a bad connection with bolted titanium basket. Also the anode area is a little too small to the big cathode area you use in the nickel solution. I don't know if you have calculated with the size of the basket of titanium will give you. Regards Anders S
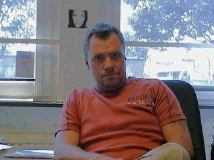
Anders Sundman
4th Generation Surface Engineering
Consultant - Arvika,
Sweden
2000
A. It's normal for the pH to increase over a long plate. We always started a little low, at about 3.8, and overnight it would go to 4.2 for example. Your experience is unusual, and it sounds like you are producing free H ions which will reduce the pH. This can be as said above due to insufficient anode area, and is definitely caused by high amperage and poor circulation leading to trains of bubbles of H2 from the baskets. We also found this problem when using a 'cleaning plate' using a titanium basket and plating constantly at about 4 A/SqM to remove trace CU and Fe. As this cleaning basket became empty the H2 went into solution, creating Hydrogen embrittlement of the plate, poor adhesion, compressive stress and anomalous deposits.
I concur, S rounds should be fine. If in doubt do a carbon treatment - the magic cure all!
Best of luck
- Melbourne,Vic, Australia
July 12, 2010
Multiple threads merged: please forgive chronology errors and repetition 🙂
What makes the pH drop in Nickel Sulphamate bath
2003Q. I have a small scale nickel sulfamate bath in which the pH generally goes down. I am aware that this should not be the case and I believe that it is closely connected to the root cause of all my problems. Some of the pH drop is connected to loss of water but this does not account for everything.
The 6 L bath is made up of:
2700 mL nickel sulfamate (80 g/L)
225 grams Boric Acid
18 grams sodium dodecyl sulphate, and DI water
The pH should be maintained at 4.0 and the bath is at 54 or 55 °C. I currently use nickel carbonate and sulfamic acid to adjust the pH. The bath is mechanically agitated and kept covered at all times. Plating is done at a constant current of 30 mA/cm^2. I use a C-12 activator and Wood's Strike prior to electroplating. The anode is nickel rounds in a titanium basket, in a cotton anode bag.
I am plating small steel rings (1" or 2" diameter), one or two at a time, and I am attempting to plate 4 mm onto them. The plating area is about 7.7 cm^2.
Until recently, I was using NaOH to increase the pH (and sulfuric acid to decrease) and I had problems with pitting... I was told that using NaOH contributed to the drop in pH as well as the pitting and to switch to nickel carbonate and sulfamic acid. I was not aware that adding nickel carbonate results in the formation of carbon dioxide (among other problems) and that plating should not continue immediately after addition of carbonate. This resulted in more pitting, but I am primarily concerned with why the pH goes down in the first place. Also, after the most recent attempt, my anode balls, which were new, were brown, which I suspect is related to adding the nickel carbonate.
I do not know what my anode/cathode efficiency is (what is a simple way to measure this?), but I do know that it is plating plenty of nickel even though it is pitting.
Any ideas?
Bianca McCarttUniversity of Kentucky - Lexington, Kentucky
A. Your pH absolutely should not drop. Are you using SD or electrolytic nickel anodes? You have called it rounds and balls. They are different--which one? I would not use cotton bags at this pH. Napped polypropylene or dynel cloth is the most common. You did not mention agitation or filtration -- it needs both. You really need to filter the solution overnight after an addition of nickel carbonate. Sulfuric acid is too harsh an acid to use for pH control. Sodium hydroxide will precipitate nickel out into a brown sludge. I have plated a lot larger things than you are in a 4 liter beaker without problems, so a larger tank would not help. Are you stirring the solution (at temperature) to get the boric acid redissolved? Otherwise it freezes out and goes to the bottom of your tank. I have a very strong feeling that you are not getting valid pH readings and are chasing your tail with adds in both directions. Please give an in depth description of exactly how you are taking the pH.
PS, a 4 mm build is a huge build on a tiny object.
James Watts- Navarre, Florida
2003
A. I know there will be people who disagree with my attitude towards nickel carbonate and sodium hydroxide, but I prefer to increase my bath pH with sodium hydroxide and NOT nickel carbonate. This is because nickel carbonate is a potential carcinogen (I think it is Class 1) and therefore very nasty to handle. On the other hand, sodium hydroxide is much safer and can be used with more accurate control. I do not see how adding an alkali such as NaOH can result in a drop in pH -- it goes against fundamental chemistry, but perhaps someone can shed some light on this hypothesis. Your problem of decreasing pH is interesting because if the bath is behaving itself it should not happen! All the basic rules say that when you electrodeposit a metal you may also deposit hydrogen -- nickel is no exception to this rule, so the pH should go up! Thank you for supplying so much information about your process; it helps everyone understand more about your problem.
I see you don't have any chloride in the electrolyte, so this could be a cause of the problem. If you are NOT using sulfur depolarised nickel anodes, you must have chloride in the bath to promote anodic depolarisation. If the anode doesn't dissolve, it will passivate and discharge oxygen and this will cause the bath pH to decrease. You mention the anode balls go brown and to me this indicates the nickel may well be passivating. Nickel sulphamate baths can be run without chloride present ONLY IF the anodes are sulfur depolarised. The advantage of doing this is that the lack of chloride reduces stress in the deposit. To be on the safe side, many sulphamate users use depolarised nickel, but also add up to 10 g/l NiCl2. If you want to decrease the bath pH use sulfamic acid ⇦ on eBay or Amazon [affil link] and not sulfuric acid; it is slightly more expensive but is better in this type of bath.
As far as pitting is concerned, it looks like your SDS is OK, so it could be due to insufficient agitation or bath contamination. I personally run nickel baths at 8-10 turnovers per hour, but accept this is high and often impracticable for larger volumes. This is through a filter but not through carbon. However, I would strongly advocate at least 3-4 turnovers per hour. Do a Hull Cell ⇦ huh? and check for metal contamination of the bath, as this can cause pitting. However, the pitting could also be due to the reduction in pH; as I said earlier, co-deposition of hydrogen can occur with nickel and this is most prevalent at low pH's. You do not say how low it gets, but looking at your figures I reckon you must be plating continuously for approaching 100 hours to get 4 mm of nickel down. I bet you don't continuously monitor the bath for that length of time, so it has plenty of opportunity to misbehave! With a bath of this size I would not advocate constant dosing as it is very difficult to set up and keep under control. I also note that pitting increased when you used nickel carbonate; this could be due to the carbonate not all dissolving as fast as you expected and you were actually co-depositing the solid carbonate particles with the nickel. Finally, anode and cathode efficiencies can be measured by good old Faraday's Laws; count the coulombs and weigh the metal lost and deposited - nickel is usually about 97-98% efficient cathodically and very similar, but slightly lower, anodically. Apologies for this rambling reply, but it brings up numerous points in which I have an interest.
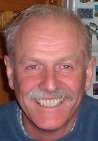
Trevor Crichton
R&D practical scientist
Chesham, Bucks, UK
2003
2003
Q. The anode I am using is Nickel Rounds "S" from Belmont Metals, Inc. I am not positive that my anode bags are cotton. They were custom made by Baker Bags, Inc and they may be napped polypropylene.
The bath is being stirred when the nickel carbonate is added and I do filter it prior to starting electroplating, but I did not realize that I would need to filter after any addition of nickel carbonate. What happens with the boric acid when nickel carbonate is added? Should I add more, and how much more should I add? I know that boric acid is intended to stabilize the pH, so it makes sense that it would need to be replenished if the pH had changed a lot.
I use an Orion 210 A pH meter with a temperature probe to monitor the pH. I usually calibrate it daily, when I take the pH. It takes about 180 hours to plate 4 mm and I have been plating 24 hours a day and only adjusting the pH once a day. The last attempt I made, the pH was dropping about 0.5-0.8 in 24 hours.
Currently I am trying to purify my existing baths per the high temperature/high pH treatment recommended by G. DiBari in his Electrodeposition of Nickel in Modern Electroplating. Unfortunately I cannot get the bath up to 66 °C per the instructions, only to 59 °C. Do you have any advice for purifying used baths? I intend to electrolytically purify using dummy cathodes as well.
When I get back to regular electroplating, how often should the bath be filtered during the process?
Thanks,
Bianca McCartt [returning]University of Kentucky - Lexington, Kentucky, USA
A. The pH lowering is an anode problem. As mentioned earlier, 100 ppm Cl is standard for Nickel Sulfamate baths -- or Bromide (some say this is better). Any sodium in any form should be avoided as it will increase the stress of the deposit. Working with nickel carbonate should be avoided at all cost as it is a very bad carcinogen and dusts very easily. (Lots of red tape, if you have this in house.) I'm sure if you keep your chloride level (or bromide) at 100 ppm you will never have to add anything to raise the pH. Use sulfamic acid to lower the pH; sulfuric acid is not an option. sulphates also add to the internal stress of the deposit.
Paul Eckerson- Lincoln, Nebraska
2003
A. I find that boric lowers our pH more than stabilizes it in our electroforming process. We place our boric in a napped bag and fill it or remove it based on our daily pH readings.
Jeff Bowling- Richmond, Indiana, USA
2003
A. One important factor should be highlighted: the sulphamate anion slowly hydrolyses in the electrolyte, ammonia
⇦ on
eBay or
Amazon [affil link] is formed, the rate of decomposition increases with decreasing pH and increasing temperature. Therefore the temperature in the bath should never exceed 70 °C or the pH<3.0. ammonia can cause hardening of the plated surface and the max. level is 1 g/L. If this level has been reached then the electrolyte cannot be recovered other than re-mixing a new electrolyte!
As known nickel chloride is not necessary to be added into S-nickel based bath system. However, when using high current density, it can exceed the passivation limit and nickel oxide form on S-nickel balls. If this happens, the side reaction can occur where water is oxidized to oxygen gas and protons, thereby the pH falls. In this case, you have to remove the S-nickel balls from the anode baskets and rinse with pure water, then allowing balls to stand in a solution of sulphamic acid (10% w/v in water) for several hours, which will etch off nickel oxide from balls. Rinsing the balls with water and return to the anode basket.
If pH dropping is caused by some contamination in your bath, you can try with cathode dummy plating with different current intervals until pH is increased, however, never using NaOH or other alkaline to increase pH.
- Sweden
November 7, 2008
Multiple threads merged: please forgive chronology errors and repetition 🙂
pH drop in Nickel Sulphamate installation
November 4, 2008Q. Dear all,
We had a sudden drop in the pH (from 4 to 3.2 roughly) on the Nickel Sulphamate bath, after 3 working days consecutive plating. We are working with S-Nickel anodes and prior to the plating, we've introduced a small amount of Nickel Chloride to prevent anodic corrosion on the anodes.
Theoretically, the pH should increase so I guess I'm having anodic corrosion anyway.
Should we increase the amount of chlorides on the bath?
Does anyone have an hint on this?
Thanks for your comments and best regards.
Paulo
Plating shop - Portugal
A. Hi, Paulo. Nickel chloride is added to promote anode corrosion, not to prevent it -- maybe there was a translation error.
Allow me to think out loud so that someone can correct me where I'm wrong: Electricity is applied to the plating tank and it causes nickel to oxidize and dissolve at the anode and to be reduced and deposit at the cathode. The process is very slightly less than 100 percent efficient, and some of the applied electricity can cause electrolysis of the water, with the production of some hydrogen gas at the cathode and/or some oxygen gas at the anode.
It is usual for the cathode efficiency to not be as high as the anode efficiency, meaning that slightly more nickel will be dissolved into solution than is plated out; charge balance will be maintained via more hydrogen being released at the cathode than oxygen released at the anode, with OH- consequently building up in the solution and the pH rising.
If the anode efficiency is low because the anodes aren't corroding, then oxygen is released at the anodes and the pH drops.
It sounds like you should either increase the Cl- or, maybe better, have more anode area?
Regards,
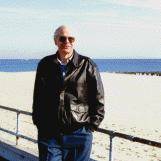
Ted Mooney, P.E.
Striving to live Aloha
(Ted can offer longterm or instant help)
finishing.com - Pine Beach, New Jersey
November 5, 2008
A. In a proper sulfamate nickel tank, the pH will rise! If the anode is not corroding properly, the pH will drop as in using an inert anode.
Check to see if you are using sulfur depolarized nickel anodes. If you are, empty the anode baskets, pressure wash the chips and activate. If you use any other acid than sulfamic, rinse the chips very well. Clean the baskets with a stiff brush/water and put on new anode bags. Reload the chips and dummy for several minutes.
Check all of the bath chemistries and adjust as required.
- Navarre, Florida
November 7, 2008
A. Firstly, chloride is added to nickel baths to promote anode dissolution, not inhibit it. Secondly, if you are using nickel sulphamate and S-nickel, in theory you do not need chloride, but as I have often said before, it is handy to promote some dissolution.
It is unusual for the pH to increase during plating, so it suggests something is wrong with the anodic reaction and I would think this is probably too smaller area, so increase the anode area. The anode and cathode areas should be approximately the same, give or take a factor of 2 or 3 - the anode should certainly not be an order of magnitude different to the cathode.
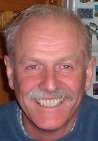
Trevor Crichton
R&D practical scientist
Chesham, Bucks, UK
November 8, 2008
November 11, 2008
Q. Dear Folks,
Thanks a lot for you comments!
You are completely right! Nickel-Chloride is inserted to promote anodic corrosion and not to prevent it!
I guess I meant that our anodes must be passivating (surface turning black) and the redox balance at the anode is retaining more Oxygen than what it was supposed to.
The area ratio Anode/ cathode must around 10:1 which I guess is more than enough but on the other hand it could be excess problem as well. What do you think?
I'll increase the chlorides a bit more and check out the result. I'll let you know.
Regards,
Paulo
- Portugal
A. I think that with an anode to cathode area ratio of 10 to 1 that your anodes are passivating. Take it down to 2 to 1 and clean and activate the anodes. You may need new anode bags also. Your problem should go away.
James Watts- Navarre, Florida
November 13, 2008
A. Jim,
I agree with your comment about too much anode area. I have an electroforming client who also has about 10 times more anode area than cathode area and he also frequently has passive anodes. Can you provide any references to back up what happens with too much anode area?
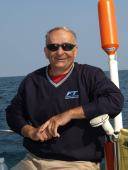
Pat Mentone
St Paul, Minnesota
November 24, 2008
A. Hi Pat,
Sorry, but I do not. Most of my knowledge is from operations sheets and literature. I also was able to pick the brains of some of the finest platers in the 80's at various conferences.
Most electroformers use a very low chloride content, so they have inferior anode corrosion to start with.
If they are using 2 x 6 baskets, see if they will switch to 2 x 3 or 1 x 4 baskets. If the anode to cathode distance is more than 4 inches, they should be able to remove at least some of the baskets with the same plate distribution and plate speed. It does require some common sense in the basket placement.
- Navarre, Florida
November 25, 2008
A. Just two thoughts on this problem :
1. there is no way to produce Oxygen at the anode if you have chloride in your electrolyte , first the chloride will be oxidized to chlorine. That means if your pH- drop is due to anodic passivation you should recognize a drop in your chloride concentration long before you see a pH drop.
2. Looking at the pourbaix diagram for nickel you will see that at pH 4 Nickel will only passivate at higher potentials. The bigger your anode area , the smaller the potential...
My guess would be , you are dragging something in your tank from the steps before, which is responsible for your pH drop.
- Lucerne Switzerland
December 2, 2008
CHECK YOUR BORIC ACID CONCENTRATION
BORIC ACID ACTS LIKE A BUFFER AND IF THE CONCENTRATION IS LOW YOU COULD HAVE BIG CHANGES IN pH.
Bnei Berak, Israel
December 6, 2008
A. I tend to agree with Ricardo - if you have a low boric acid content you will see a wide swing on bath pH. I would recommend a bath content of at least 30 g/l and probably 35 g/l. I have known one electroformer use 120 g/l boric acid, but they had to keep the bath hot the whole time to avoid crystallization of the boric acid - if this happens, you will have all sorts of problems getting it to redissolve.
Regarding the anode area; if it is too high the anodes will passivate and you will get gas discharges, so I would recommend an anode:cathode ratio of ideally about 2:1. It is important you use sulfur-depolarised nickel rounds as the anode and just measure the area of the anode basket and do not try making sophisticated calculations by taking into account the areas of the individual nickel rounds. Since you are using a nickel sulphamate bath, you do not need chloride present, as this is one of the major benefits of nickel sulphamate. However many platers still like to use a couple of grams per liter of chloride, just to make sure of good anode dissolution. If there is chloride present in the bath and the anode discharges gas, it will more likely be chlorine than oxygen. Any anodic discharge will tend to reduce the bath pH, so it should be avoided and the best way of doing that is to avoid passive anodes; active anodes also help keep the bath in balance with regard to nickel content. I would recommend that nickel sulphamate baths are operated at about pH 3.6-4.3 and ideally 3.8-4.2. If you use the plating conditions above, you should not see a significant amount of gassing
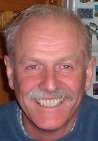
Trevor Crichton
R&D practical scientist
Chesham, Bucks, UK
December 14, 2008
December 15, 2008
A. Dear Paulo,
It does not take a Chemist to be an electroplater, but an understanding of basic Electrochemistry certainly helps.
An electroplater should at least understand the major anodic and cathodic reactions.
At a soluble Nickel anode the major reaction is the dissolution of the Nickel anode itself, and at the cathode it is the deposition of Nickel.
During Nickel plating, the pH rises as some Hydrogen ions are removed from the solution at the cathode and eventually escape as Hydrogen gas. This reduces the cathode efficiency to about 95%. Boric Acid in the solution ionizes to produce Hydrogen ions to compensate for the removal of Hydrogen ions, thus acting as a buffer.
If the pH is falling, most likely (unless acid is entering the solution from an outside source) the anode is not dissolving properly and Hydroxyl (OH-) ions are being discharged at the anode. Nickel Chloride is sometimes added to help dissolve the Nickel Anode, but this is not necessary if Sulfur activated Nickel Anodes are used. Nickel Chloride is not recommended as this can introduce stress into the Nickel deposits. Too much of an anode area could also contribute to the pH falling. An anode:cathode ratio of 1:1 to 2:1 is usually recommended. If your bath was working ok previously, then your Nickel anode might not be dissolving properly.
The following are some reasons why the Nickel anode might not be dissolving properly (usually accompanied by a rise in applied voltage):
i) Lose or corroded connections at the anode
ii) Lack of Nickel Chloride (if needed)
iii) Film formed on Nickel anode
There could be more reasons for the anode not dissolving properly. Recently, I had a problem with my bath pH falling. I observed the following:
i) Rise in applied voltage
ii) Brown film on anode.
iii) Brown discolored anode bag with sludge inside
iv) Corroded electrical contacts at the anode
I solved the problem by doing the following:
i) Replaced the anode bag
ii) Cleaned the anode in dilute Hydrochloric acid.
iii) Replaced the electrical contacts at the anode.
iv) Adjusted the pH with Nickel Carbonate
I hope I was able to help in some way.
- Danbury, Connecticut
A. Dear Maurice,
I do not think that OH- ions are dischargeable at the anode for it is not anodic reaction process. Was the pH reading taken near the surface of the Anode or from the bulk solution? A drop in the pH from 4 to about pH 3 should not cause a hydroxide discharge at the anode. I tend to agree with the Swedish gentleman that the drop in the bath's pH might be due to the plating bath's drag out either from the nearby poor rinsing acid solution. Alternatively, if the plating process is near a solid solution Heat treatment furnace operated environment, carbon emitted gas in the air could dissolve into the plating solution and decrease the acid value. Besides the evolved H2 gas on the cathode( H20 = OH- + H2), OH- ions ae a byproduct of cathodic reaction, that usually forms in the solution/ cathode diffusion interface. If a plating bath's pH begins to rise from 2.5 or less, the OH- ions begins to increase in the diffusion layer near the cathode surface. Higher and higher pH directly effect increases the formation of OH- ion barrier on the cathode/ solution interface, restricting possible diffusion of the active metal ions from migrating through to deposit on the cathode as pure alloyed or metal without inclusion of the brittle OH co-deposition. A plating bath of pH 3 at room or near room temperature should supply sufficient hydrogen ions (2H2O = O2 + 4H+ + 2e- ) near the anodic surface (anodic reaction) sufficient to help in the anodic dissolution and enhance the oxygen gas to de-sorbed off of the anode surface. If the anode surface is dirty with impurities including but not limited to organics/ inorganic such as chloride or metal impurities, the rate of the anodic dissolution may decreased and the rate of oxidation/anodic reaction slowed. Finally, if hydrogen bubbles on the cathode surface were not liberated due to low pH of the bath, then increase in the applied voltage to the cathode would be necessary to evolve the hydrogen gas to enhance the normal redox thermodynamic reaction of the plating process. When the reaction takes place, the hydrogen protons are consumed or liberated as gas on the cathode, a rise in the pH will be experienced until near depletion is reached, requiring buffering. Any one of the described phenomenon may have happened resulting in drop of the pH value observed, all things being equal.
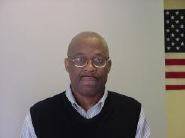
Bassey J. Udofot
Musgegon, Michigan
January 15, 2009
February 7, 2009
Dear all,
The Nickel sulphamate bath is working very smoothly now and we had no more pH drops since.
After reviewing a few of your suggestions, I came to prevent future problems by doing the following:
- ensure all anode basket are correctly connected to the power supply
- cleaned all anodes through hydrochloric acid
- adjusted anode/ cathode area ratio to 2:1
- ensured Boric Acid content at 30 g/l
Problem solved for now......
Thank you all for the valuable support.
Best regards,
- Portugal
Hi Paulo,
Great job !
Did you have to adjust the pH upwards by adding Nickel Carbonate?
Chao !
Maurice.
- Danbury, Connecticut USA
February 11, 2009
Hi Maurice!
Yes. The pH was adjusted by slowly adding Nickel Carbonate.
There were a few other options like NaOH and other proprietary solutions but I'd rather go for the most common one because of knowing its side effects.
Thank you for your support and best regards,
Paulo
- Portugal
February 13, 2009
August 22, 2014
Q. Hey all,
I was having a similar issue suddenly pop up so I did all the recommended things:
i) Replaced the anode bag
ii) Cleaned the anode in dilute Hydrochloric acid.
iii) Replaced the electrical contacts at the anode.
iv) Adjusted the pH with Nickel Carbonate
I am currently using S-nickel anodes and I don't see any film on the anode rounds and there is some black on the anode bag from nickel sulfide but not an excessive amount (a couple of quarter of a dollar sized black spots on the anode bag).
I did leach the anode bag in a pH 2.0 soap, sulfamic acid solution overnight. After replacing the anode bag I carbon filtered the solution for one day using the FloKing lab sized filter and pump.
I cleaned the electrical contacts (copper) with HCl and rinsed with water.
I used the bath once and the pH rose as, would be expected. I used the bath a second time and the pH suddenly dropped again.
I have a polypropylene anode bag filled with boric acid sitting in my bath.
Question, could my contacts have corroded again?
Could it be the anode to cathode ratio? What is the scientific basis for this being important. (I can only think of it affecting the electric field distribution.)
I am starting with a thin film of metal vacuum deposited OR liquid phase deposition of silver from a silver nitrate/ammonium hydroxide/dextrose solution (rinsed silver substrate before putting in bath).
I am ramping the current because I've observed that starting with my electroforming current causes delamination of the film.
I think that if I'm not ramping at a fast enough rate, the low current density is causing more electrolysis than nickel deposition to occur. Could this be the case? I want to have a final current density of 5 A/ft^2 starting with 0.72 A/ft^2.
One other thing I should mention is that I am trying to do a room temperature process because I am electroforming micron scale features off of a silver coated high coefficient of thermal expansion (310PPM/K) rubber and am concerned about thermal expansion.
laboratory - Cambridge, Massachusetts, USA
Ed. note: Closely related threads include --
- letter 9380, "pH adjustments for nickel sulfamate plating bath"
- letter 18637, "Nickel sulfamate pH is too low. How to raise?"
adv.
"The Sulfamate Nickel How-To Guide"
by David Crotty, PhD
& Robert Probert
published Oct. 2018
$89 plus shipping
Q, A, or Comment on THIS thread -or- Start a NEW Thread