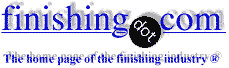
-----
Immersion gold plating vs. electroless gold plating
⇦ Tip: Readers want to learn from your situation;
so some readers skip abstract questions.
Q. Hello. I know electroplating well but I just saw a video about plating medium size pieces without using electricity. Not sure but from the video the material was copper and the plating result looked like gold plating. Any idea how? Thanks in advance.
amir kefa- tehran
April 24, 2022
A. Hi Amir. My guess is that it was simply a standard gold plating solution, which will immersion deposit onto copper without need for electricity. Any time you put a metal object into a plating solution, a battery is automatically formed between the metal of the substrate and the metal in the plating solution. If the metal in the plating solution is more noble than the metal of the substrate (and gold is more noble than copper), the "battery" is wired in the direction to cause deposition, and the plating solution will spontaneously plate out onto the substrate (this is a slight simplification because if the concentration is extremely low this may not happen).
If you can, please give us a URL for that video because we can only guess at what you saw and then try to answer with "ifs-ands-&-buts" :-)
Luck & Regards,
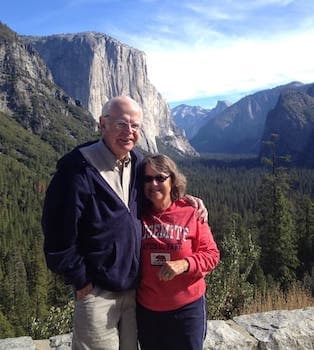
Ted Mooney, P.E. RET
Striving to live Aloha
(Ted can offer longterm or instant help)
finishing.com - Pine Beach, New Jersey
Thanks for the tip. I saved the video from instagram; I can send it to you via email
- tehran
July 9, 2022
A. Hi again, Amir. You can send it to mooney@finishing.com please, but we already know that it's possible to do immersion/replacement gold plating. The question isn't whether it can be done, it's whether the approach is applicable for your particular situation, but after your 2nd letter I still know nothing of your situation, and a 3rd letter with a video you saw won't help much :-) What substrate material are you trying to plate, and with what metal, and why (why does the part need this plating) ?
Luck & Regards,
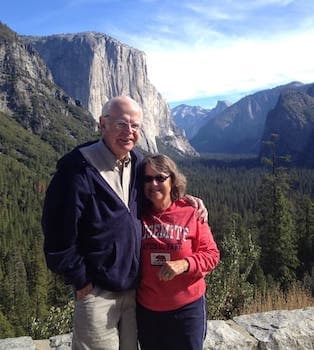
Ted Mooney, P.E. RET
Striving to live Aloha
(Ted can offer longterm or instant help)
finishing.com - Pine Beach, New Jersey
⇩ Related postings, oldest first ⇩
Q. Is there a substantive difference between electroless gold and immersion gold, and if so can you define this for me. I am not a finishing professional but I deal with components that mount to printed circuit boards.
Roger Williams- Missouri
2002
QUICKSTART:
"Immersion" in this context does not mean "dipping" as opposed to brushing or spraying. It carries a specialized meaning related to why the plating takes place, i.e., the driving mechanism, a chemical displacement process.
A. Hello, Roger.
By "electroless plating", industry professionals really mean "autocatalytic plating". So your question becomes what is the difference between chemical displacement plating operations/solutions and autocatalytic plating operations/solutions.
An immersion plating solution operates on the principal of displacement of the surface skin of the substrate by a more noble metal that is in solution. In science class, high school kids put iron nails in beakers of copper sulphate ⇦ on eBay or Amazon [affil link] and watch as the outermost layer of iron goes into solution and is replaced by copper ions coming out of solution.
There are several weaknesses to immersion plating. First, the thickness is limited to a few atoms: once the surface is covered by the new plating, the solution doesn't "see" the substrate anymore, so no more substrate atoms can dissolve, and consequently no more noble metal ions deposit. The second problem is that you can't immersion deposit a baser metal onto a more noble metal; for example, you can't immersion deposit copper onto gold, because the built in battery that drives immersion reactions is wired the opposite direction. Thirdly, immersion deposits can tend to exhibit poor adhesion; now I'm just guessing on the cause, but this might be related to the fact that the substrate is dissolving as the reaction proceeds, the newly deposited ions stand on feet of clay washing away below them.
Autocatalytic solutions are sort of "spring loaded" reactions which are driven by reducing agents in the solution, but which reduction reactions will only take place in the presence of a catalyst; but the metal being deposited is one of those catalysts. So you start the reaction either with electricity or by depositing onto a substrate which is also catalytic to the solution; then the reaction continues as long as the surface being plated remains in the solution, continuing to catalyze the reaction. Consequently the thickness can be much, much greater. Autocatalytic or "true electroless" gold plating is a relatively recent development whereas immersion plating was probably known to the ancients.
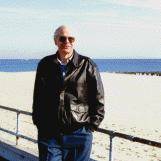
Ted Mooney, P.E.
Striving to live Aloha
(Ted can offer longterm or instant help)
finishing.com - Pine Beach, New Jersey
2002
Q. I am investigating moving to immersion silver from HASL surface finish for PWBs. I noticed Mr. Ted Mooney stated I.S. has poor adhesion. Would this be only in the as-plated state? After assembly with solder, the silver has alloyed into the joint and is no longer a layer, isn't it?
Thank you,
Lisa P Koland- Minneapolis, Minnesota
2003
A. Immersion plating processes do tend to have poorer adhesion than electroplating processes. This is perhaps because the plating process is not metered or controlled by an external electrical source; rather, atoms of the plating deposit on the substrate at the rate of their choosing, often not slowly building a solid crystal structure, but instantly converting from ions to metal of a powdery form. As previously mentioned, another possible reason may be that the substrate is dissolving; picture a gold atom which has just replaced a copper atom, and bonded well to it, when the underlying copper atom it has formed upon then dissolves away.
But sometimes the adhesion is adequate to the task. For example, virtually all plating onto aluminum begins with an immersion deposit of zinc. As for whether immersion silver will actually be an improvement over HASL, Lisa, sorry but the question is not within my experience; hopefully a more knowledgeable reader will reply.
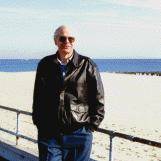
Ted Mooney, P.E.
Striving to live Aloha
(Ted can offer longterm or instant help)
finishing.com - Pine Beach, New Jersey
2003
A. I have been operating an immersion silver line as a finish for printed circuits for the past year or so and am unaware of any adhesion problems.
David Moyerprinted circuits manufacturing - St.Paul, Minnesota
February 11, 2008
by Reid & Goldie
-- hard to find & expensive; if you see a copy cheap, act fast!
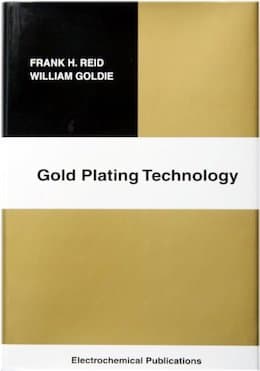
on eBay or Amazon
or AbeBooks
(affil link)
Hi David. Thanks for the feedback. Your response motivated me to look a little deeper ...
In Chapter 10, "Immersion Solutions" in Reid & Goldie's "Gold Plating Technology" .
there are several interesting pages devoted to predicting whether a particular immersion plating operation will produce adherent, bright, and continuous coatings on the base metal. One of the several factors is how close the two metals are to each other in half-cell voltages.
Regards,
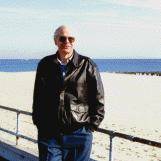
Ted Mooney, P.E.
Striving to live Aloha
(Ted can offer longterm or instant help)
finishing.com - Pine Beach, New Jersey
Q. I do copper electroforming of vegetal material (leaves, flowers) and then gold electroplate it directly over copper, with very poor results. I can't use nickel before gold plating as I produce anti-allergic jewels.
I guess my answer is going into the Electroless gold plating, directly over the copper electroformed organic object, if appropriate.
Would I need to do both steps? First do an immersion gold plating and then the autocatalytic process? Or is the autocatalytic one enough?
If so, many of my finishing quality problems would be solved.
Thanks for your comments and advise.
- Bogota, Colombia
March 5, 2009
A. Hi, Hernando. Gold directly on copper is theoretically not a good idea because they diffuse together. A better approach would be cobalt plating in lieu of nickel, or ideally white bronze plating in lieu of nickel. However, in non-critical and room temperature applications like jewelry plating, there is also a lot of evidence that this theoretical problem is often not a serious real-world problem.
Regards,
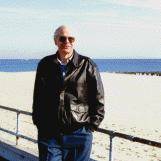
Ted Mooney, P.E.
Striving to live Aloha
(Ted can offer longterm or instant help)
finishing.com - Pine Beach, New Jersey
March 9, 2009
Q. Dear Ted: Thanks for your advise of March 9, 2009, but after years, my thinking is back to my original statement and I would like your consideration again. That is, go directly from copper base to gold, via gold by immersion and then, over it, electroless gold plating. Will it work? Is it technically feasible? Thanks again, but I still would like to change my technique.
Regards,
- Bogota, Colombia
December 15, 2011
A. Hi, Hernando.
There are proprietary immersion gold plating solutions designed for plating directly on copper, and there are autocatalytic gold baths, so it should be possible to do what you wish. But I don't know how well this two-layer gold process will adhere to your copper. Since the application is not critical, it's certainly worth a trial. But if I were you I would not sell millions until I verified the real-world durability of the product.
Regards,
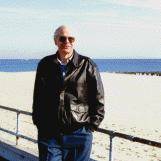
Ted Mooney, P.E.
Striving to live Aloha
(Ted can offer longterm or instant help)
finishing.com - Pine Beach, New Jersey
December 15, 2011
Q. Sir,
I want to know how to gold plate on a big article without current?
plating shop employee - Udaipur, India
April 12, 2011
A. Hi, Harish.
We appended your inquiry to a thread that explains the general situation. If you can describe the component that you wish to plate, including the environment it will see, why you want to plate it, and what it is made of, we can hopefully offer additional guidance. For decorative gold plating it is typical to nickel plate or white bronze plate under the gold as otherwise it may not be shiny. Gold leafing may be an alternative to gold plating without electricity. Good luck.
Regards,
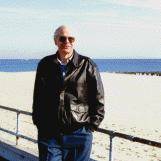
Ted Mooney, P.E.
Striving to live Aloha
(Ted can offer longterm or instant help)
finishing.com - Pine Beach, New Jersey
April 12, 2011
Q. Hi Mr Ted,
You said in your first response that:
"the thickness is limited to a few atoms: once the surface is covered by the new plating, the solution doesn't "see" the substrate anymore, so no more substrate atoms can dissolve, and consequently no more noble metal ions deposit"
I believe this statement to be correct. However, I have been experiencing thickness variations with immersion gold. (The process I'm using is ENEPIG). What do you think would account for the difference? What factor could possibly cause this when as you said, the solution wouldn't see the substrate anymore once everything is covered with plating?
Would appreciate your expert opinion. Thanks!
- Clark, Pampanga, Philippines
January 3, 2012
Hi Joel. If you look at the entry below from Shyam Sunder, he is suffering a 18:1 ratio from one side to the other :-(
I currate the site and make suggestions when my limited specific experience or my book knowledge permits ... but there are lots of processes I know little about and ENEPIG [electroless nickel - electroless palladium - immersion gold] is one of them. Any theory I raised, beyond the simple observation that these processes are not known for their stability, would only be a wild guess :-)
Regards,
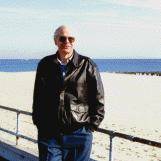
Ted Mooney, P.E.
Striving to live Aloha
(Ted can offer longterm or instant help)
finishing.com - Pine Beach, New Jersey
Q. I'm new and (hopefully) learning about gold plating as I want to start a local mobile business. Am I to understand from the opening question/answer in this thread there are three means to gold plate: autocatalytic plating, immersion plating and electroplating? If so what are the advantages/disadvantages particularly between autocatalytic and electroplating? I will be offering a decorative service, not industrial. Many thanks to all who answer.
David Caple- Heathfield, East Sussex, UK
February 28, 2012
A. Hi David.
A mobile business will in all likelihood be doing electroplating. It should be easiest and least expensive. It will work on the most substrates, the thickness will be easily controlled, and it will be easier to do alloy plating for different color, hardness, and karat. The only real disadvantage, and it may not apply to your mobile business, is that the thickness in any area is proportional to the current flowing to that spot (see Faraday's Law). This means that you can't practically plate the inside of small diameter tubes and, if doing tank plating, inside corners will have significantly less thickness than outside corners.
Autocatalytic gold plating is proprietary, relatively new, complex to keep operating properly, and limited. It is not a general purpose "jobber" solution, but something designed for specific purposes like plating of electronic circuits which it may be hard to bring electricity to.
Regards,
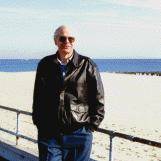
Ted Mooney, P.E.
Striving to live Aloha
(Ted can offer longterm or instant help)
finishing.com - Pine Beach, New Jersey
February , 2012
Q. Hi Ted and thanks ... yes I will be electroplating and will stick to that (and understand the basics of that process from school physics!). I also understand what I think you are describing as the immersion method where the component and solution effectively makes a battery which is 'lost' once a thin skin of plating forms on the item, but how does autocatalytic plating work?
Also because of the difficulties of getting into blind spots and corners with the electro process is there a case for using the immersion or autocatalytic process first to make sure the whole of the object is given a covering (albeit thin) and then using electroplating to build the thickness on the more accessible (more exposed) parts if desired?
David
- Heathfield, East Sussex, UK
February 28, 2012
A. Hi, again.
Before addressing auto-catalytic gold plating, let me speak about auto catalytic nickel plating first because it has been around for a long time, is widely used, very well understood, and offered by enough vendors that the general principle is not a trade secret.
The electroless nickel solution (auto-catalytic nickel solution) will contain nickel hypophoshite or nickel borohydride. Hyposphosphite and borohydride are powerful reducing agents, but they only work in the presence of a catalyst. The catalyst can be a steel surface, a zinc surface, or (importantly!) a nickel surface. The fact that a nickel surface is catalytic is why it is called autocatalytic rather than just catalytic. The plating doesn't stop when a very thin layer of nickel has been deposited, but it keeps going. Electroless nickel has some inherent problems: it can spontaneously plate out -- picture a spec of random nickel sticking on a tank wall and growing and growing and growing; and it gets exhausted or contaminated -- as the hypophosphite or borohydride reduces the nickel to metal, it gets oxidized to undesirable and not easily removed contaminants.
Back to auto-catalytic gold plating. This is a rather new technology, perhaps one or two suppliers, and far less understood. And who can afford to have gold autocatalytically plate out on a tank wall? In short, I don't know too much about it, you'd have to get a technical data sheet from a supplier (try Technic), but I seriously doubt that it will play a role in your jobber service. A more likely scenario would be to use electroless nickel for corrosion resistance and top it off with gold plating for color.
Regards,
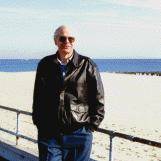
Ted Mooney, P.E.
Striving to live Aloha
(Ted can offer longterm or instant help)
finishing.com - Pine Beach, New Jersey
February 28, 2012
Q. I want to know in electroless gold deposition process on PCB's do we require filtering of solution and mechanical agitation? If yes kindly tell me how much is required. I want to deposit Gold about 2 micron thickness uniformly both sides.
Presently doing electroless Gold deposition by Sonex chemistry but there is a difference in thickness: one side getting 1.8 micron and other side getting 0.1 micron, while processing while doing mechanical agitation and filtering of solution. Kindly suggest me the process.
PCB manufacturing - India
July 25, 2012
Q. I have query on the immersion gold plating quality: how can we measure or monitor the plating quality? It is only the thickness is under monitoring? How about the Au density or surface morphology? Grain structure or surface lattice defect?
Thanks,
david
- Mal, Malaysia
May 14, 2015
A. Hello All
This paper can be interesting to illustrate this thread: "Non-Cyanide Electrolytes for Gold Plating".
If you aren't a Chemist it will be a little difficult to understand some terms but you can extract the essence and apply it to your requirements.
Best Regards
Armando
Chemist UCV
Dragus Chemical C.A - Caracas Vzla- Weston Florida
January 5, 2016
ENEPIG On Non PCB Surfaces
Q. Does anyone have any experience with ENEPIG finishes on non PCB surfaces? Typically ENEPIG, which is a highly wirebondable version of ENIG, is a PCB finish. I am experimenting with the idea of this finish on a non PCB surface and wanted to see if anyone had any experience doing this. My interest in this finish would be a more cost effective gold plating alternative. Typically the applications I deal with (electrolytic gold in the electronics industry) requires thicker gold than the 2 micro inch thickness of ENEPIG.
Thanks for the help. And by the way, please forgive my lack on knowledge on the topic as my background is not in plating, but mechanical engineering.
Engineer - San Jose, California
January 12, 2016
January 15, 2016
A. Electroless Nickel Electroless Palladium Immersion Gold finish for non-PCB (Printed Circuit Boards) applications as an inexpensive gold plating alternative? There is nothing inexpensive when you include Palladium and Gold on the same sentence. There is really nothing less expensive than electroless nickel followed by immersion gold out there.
lets explore the alternatives.
ECIG (Electroless Copper Immersion gold) is about as expensive as ENIG but with the caveat of copper diffusing into gold. A barrier like silver is recommended adding the extra cost of immersion silver. But ECISIG (Electroless Copper Immersion Silver Immersion Gold) would still be more affordable than ENIPIG.
What surfaces are you trying to gold plate? ABS plastics? Organic articles? Jewelry? Would be nice if you specified your needs.
Regards.
Marvin
- Managua, Nicaragua.
Q. Can I make plate Gold direct on to the ABS substrate. Please advice and help for necessary information. I would like to plate Gold direct on to the ABS substrate.
Sittikorn Rakjaisupplier/vendor - Bangkok , Thailand
February 13, 2018
Q.
Can I attach Gold directly on to the Polyurethane foam (PU foam) substrate? Please advice and help with necessary information. I would like to plate Gold directly onto the PU foam substrate use for catalysis chemistry reaction
- Ho Chi Minh, Vietnam
May 5, 2018
A. Hi. Plastics are non-conductive so you cannot plate gold directly onto them. You must metallize them first. Please see our FAQ about plating on organic materials. Good luck.
Regards,
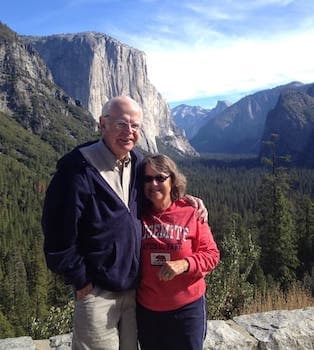
Ted Mooney, P.E. RET
Striving to live Aloha
(Ted can offer longterm or instant help)
finishing.com - Pine Beach, New Jersey
May 2018
Q, A, or Comment on THIS thread -or- Start a NEW Thread