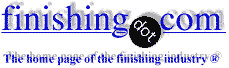
-----
Electropolishing 420 SS Stainless
Q. I am looking for information on how to electro-polish 400 series stainless steel. I make knives as a hobby and would like further info on chemicals and amounts of current needed. I have attempted a couple of acids under current but I have not been able to get good result. Thank You,
Gary Hamilton- Brenham, Texas USA
2002
Q. DEAR SIR,
I WANT TO DO ELECTRO POLISHING ON STAINLESS STEEL 420 GRADE STRIPS PRODUCT KNOWN AS RIDERLESS HEALD'S USED IN TEXTILE WEAVING THE THICKNESS OF PRODUCT IS 0.30 MM, WIDTH IS 5.50 MM & LENGTH IS 280 MM TO 410 MM.
PLEASE GUIDE IN THE ABOVE MATTER.
MR. ASHOK M. NAIR-MAHARASHTRA, INDIA
2002
A. Hello, Gary_, Ashok. Most of the "must have" metal finishing books include good chapters on electropolishing of stainless steel, including the Metal Finishing Guidebook, ASM's Metals Handbook, Vol. 5., but especially the Electroplating Engineering Handbook ⇦ this on eBay, AbeBooks, or Amazon [affil links] , which has a great chapter on the subject. Take a look at it and formulate some questions. Good luck!
Good luck.
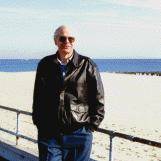
Ted Mooney, P.E.
Striving to live Aloha
finishing.com - Pine Beach, New Jersey
A. Proprietary electropolishing processes for SS400 series are available in India.
Ramesh Khare- Mumbai, India
Q. We have lost our recipes for our electropolisher. Can someone help me with some recipes for 316 grade stainless 420 grade stainless.
Many thanks,
BOB LYESURGICAL INSTRUMENT MANUFACTURER - SYDNEY, NSW, AUSTRALIA
2003
A. Hi, Bob. There are many different recipes, most based on sulfuric acid or a mix of phosphoric and sulfuric acid. The Electroplating Engineering Handbook ⇦ this on eBay, AbeBooks, or Amazon [affil links] has an excellent chapter on electropolishing, and includes some recipes you could try. But as implied by Ramesh's reply, you best strategy at this point might well be to contact a vendor of proprietary electropolishing solutions who can offer experience and testing to get you running again. It often requires not just a recipe but hand-holding as well :-)
Good luck.
Regards,
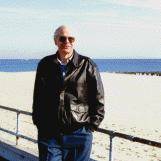
Ted Mooney, P.E.
Striving to live Aloha
finishing.com - Pine Beach, New Jersey
Multiple threads merged: please forgive chronology errors and repetition 🙂
Q. I am a student of V.J.T.I.
I need information about electropolishing SS420. It's required for my M-Tech final year project.
Kindly reply the same at the earliest.
Regards,
9th Edition, Vol. 5
"Surface Cleaning, Finishing & Coating"
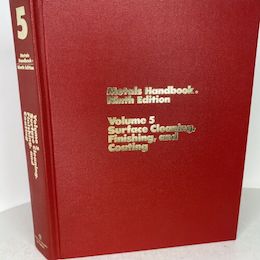
on eBay or Amazon
or AbeBooks
(affil link)
V.J.T.I., MUMBAI - MUMBAI, MAHARASHTRA, INDIA
2006
A. From your university library or a local library, try to get a copy of the Electroplating Engineering Handbook ⇦ this on eBay, AbeBooks, or Amazon [affil links] , Mahesh. It has a chapter of electropolishing of stainless steel which will tell you what you need to know. If that book is for any reason unavailable, other treatments of the subject (although not quite as good) can be found in the ASM Metals Handbook Vol. 5 or the Metal Finishing Guidebook. Good luck.
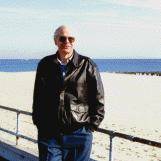
Ted Mooney, P.E.
Striving to live Aloha
finishing.com - Pine Beach, New Jersey
Q. I am getting a matte finish after electropolishing my 420SS parts. The parts are heat treated to Rc50. Any ideas why it would not be bright and shiny?
Steve Waszakprogram manager - Oceanside, California
December 14, 2009
and Chemical Polishing
of Metals in
Research and Industry"
by W.J. Tegart
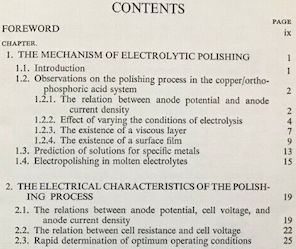
on eBay or Amazon
or AbeBooks
(affil link)
A. Hi, Steve. Etching is sometimes the result of insufficient current density or excess water in the electropolishing solution.
But it isn't clear to me whether you are doing this electropolishing in-house vs. contracting it out; nor whether this is a problem which has just recently developed in your long-established proven process vs. whether you haven't yet successfully electropolished anything. But if you can flesh out your situation I am confident that the readers will have good next steps for you!
Regards,
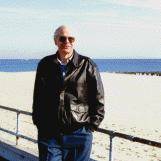
Ted Mooney, P.E.
Striving to live Aloha
finishing.com - Pine Beach, New Jersey
A. Steve, 420 stainless steel is not the easiest of stainlesses to electropolish - in fact all 400 series are quite a problem! The basic formulations for stainless steels are based on sulfuric acid and orthophosphoric acid, but these are generally not very successful with 400 series, so extra additives such as hydroacetic acid ⇦ on eBay or Amazon [affil links] and/or aryl sulphonic acids are used. You may get best results if you talk to your supply house, as they may well have a suitable solution.
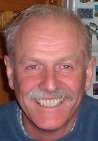
Trevor Crichton
R&D practical scientist
Chesham, Bucks, UK
adv.
Stainless steel 420 and other 400-series steels can easily be polished in Universal electrolyte. We have installed such 1000 gal tank in March in one American shop. They have not replaced electrolyte yet and use it mostly for 420 series, although aluminum, copper, nickel and other metals can be polished in this tank also.
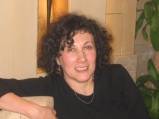
Anna Berkovich
Russamer Lab

Pittsburgh, Pennsylvania
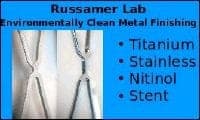
A. Apologies Anna, I am aware of your non-acid saline based electrolytes for stainless steel, but unfortunately I have no first hand experience of them. My response was based on the conventional phosphoric acid-sulfuric acid mixes, where 400 series steels do present major problems. I believe that your systems may well be the answer to many prayers.
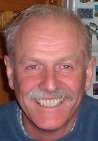
Trevor Crichton
R&D practical scientist
Chesham, Bucks, UK
![]() |
Q. Anna, you mentioned a universal polish for copper. Does it also serve as an anti tarnish on the copper? ![]() ![]() Sara Michaeli Tel-Aviv-Yafo, Israel December 24, 2009 A. Sara, ![]() Anna Berkovich Russamer Lab ![]() Pittsburgh, Pennsylvania ![]() |
We outsource the electropolishing service. Many thanks for the feedback received.
- Oceanside, California, USA
December 29, 2009
Electropolishing of free-machining 420F Stainless Steel
Q. We manufacture a variety of medical parts, some of which are electropolished. Most alloys respond very well but we have had a few problems with free machining 420F coming back with a very dull and etched surface. Upon speaking to the electropolisher I found out that after the first run the parts were a dark brown color. The second trip through the process got rid of the brown but left the etched surface.
They think it is because of the free machining agent (sulfur or selenium), and supporting that theory is the fact that the etching is more pronounced on surfaces that intersect the grain of the bar that the parts were made from. If that is the case, why would the problem be so intermittent? 95% of the time everything is fine.
Any help would be very appreciated.
Owner - Bloomington, Indiana, USA
July 1, 2010
A. Two possibilities.There may be minute differences in the alloy, even in the same bar. Most probable is the difference in the grain structure because of a slight difference in the hardening / annealing cycle.
James Watts- Navarre, Florida
![]() |
A. The explanation usually is: higher carbon content of the stainless steel from the supplier. Conventional electrolyte cannot handle electropolishing of stainless steel with higher carbon in its chemical composition. ![]() Anna Berkovich Russamer Lab ![]() Pittsburgh, Pennsylvania ![]() A. Mike, |
Thanks for the responses. It sounds like the problem could be any of a number of things.
I looked at the cert. file for the material lot that the parts came from. Carbon was .35%, sulfur was .20%. Both are well within tolerance. I don't know about the heat treatment as there is no info for that. I did find out that that there was no alkaline pre-treatment prior to EP.
The strange thing about this is we have run other lots from the same bar with no problem at all.
Mike Kiser [returning]
Owner - Bloomington, Indiana, USA
A. Dear Sir,
SS 420F has very good corrosive resistance, so this used in aircraft. This is hardened material having chemical composition as Chromium 12.5%, Nickel .20%, Manganese .50%, Carbon .22%, Silicon .50%, Iron Balance -- this is suitable for polishing. Side by you is due to electrolyte, temperature failure, and passivation due to local polarity changes.
- Madurai, Tamil Nadu, India.
Multiple threads merged: please forgive chronology errors and repetition 🙂
Q. I used to electropolish 304 stainless steel parts, but I received one made of 420SS with the same operating conditions as 304. I obtained a dull appearance and etched surface.
The question is what are the parameters to take in to account to be successful in that case?
Thanks in advance
Daniel
- Bucaramanga, Santander, Colombia
April 17, 2012
A. 420 is not the best for electropolishing. Use the same conditions as for 304, make sure specific gravity is high enough, no excess water, shorten polishing time, keep bath temp 120-130 °F, current density at least 150 ASF. The best you can hope for is semi-bright and smooth.
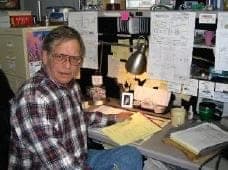
Jeffrey Holmes, CEF
Spartanburg, South Carolina
A. It may be a case of bath composition. If you are using a phosphoric/sulfuric based mix, the phosphoric acid may be too high. 300 series will work over a wide range of ratios. But, 400 series work best with a ratio of about 50:50. If you are operating at around 60 °C (140 °F) then you may have to raise the temperature to around 85 °C (185 °F) to get the brightest results.
One of the disadvantages of such a bath is that the minimum current density to obtain polishing (rather that etching) will have to be increased. Also, 400 series may start to dissolve chemically. Unless the chemical attack is only slight, it may be necessary to raise to initial current density to start the polishing action.
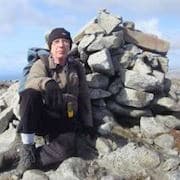
Harry Parkes
- Birmingham, UK
A. I agree with Harry Parkes suggestions and would like to suggest that to avoid low current density areas during the electropolishing process, multiple connections are made and special focus made on "difficult areas" where you may get lower current densities.
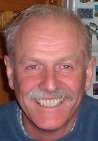
Trevor Crichton
R&D practical scientist
Chesham, Bucks, UK
April 25, 2012
Sorry for the delay!!
I was running samples.
Thanks, it worked fine, I obtained a satin finish, a very good shine, and sometimes not the same but acceptable.
The delay was because I did not want to write that I was not able to do it, or to say that I surrendered.
Thanks to Mr. Trevor, Mr. Parkes and Mr. Jeffrey!!
At the beginning it did not work --
I raised the temperature but changed the solution on a small bath, but the result was grey dull appearance. So I added an alcohol and lowered the temperature.
I suspect the problem was that the bath was very small so the bath got a very high temperature just before starting to work and the metal got etched by the solution.
- Bucaramanga, Santander, Colombia
Q. What are the additives other than phosphoric/sulfuric based for electropolishing of Steel 400 series?
Matineh AtrianR&D expert seeking optimum parameters - Isfahan, Iran
May 25, 2019
A. Hi Matineh. We appended your inquiry to a thread where Trevor has offered a general answer regarding the additives. If that is not sufficient a search of the technical literature at surfacequery.com, or possibly even scholar.google.com might possibly find some published results. Good luck.
Regards,
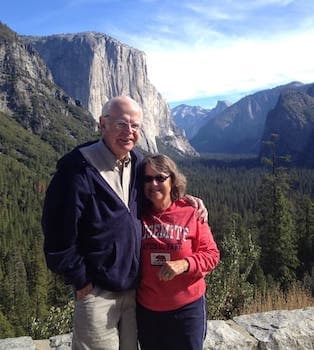
Ted Mooney, P.E. RET
Striving to live Aloha
finishing.com - Pine Beach, New Jersey
Want near-mirror polishing on SS 420
Q. Hi guys, I would like to know the condition to have polished surface near to mirror -- I mean what voltage, what anode and cathode, what electrolyte for stainless steel 420? Shape of workpiece is similar to Iphone 5.
alireza tatelectropolish - tehran, iran
January 10, 2020

Q, A, or Comment on THIS thread -or- Start a NEW Thread