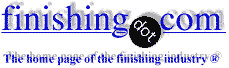
-----
Coloring stainless steel (anodizing)
Current questions and answers:
Q. Hello
Please tell me procedure of coloring 38 swg round stainless steel wire, 304 grade. I want to produce a permanent color on stainless steel wire, that will not fade away for a longer duration. Any help in this regard is highly appreciated.
Thanks and regards
- Delhi, India
April 7, 2021
A. Hi Kuldeep. If a gold color is satisfactory, a titanium nitride coating applied by PVD, as you see on drills in a hardware store, is probably the most durable. Otherwise, give us more exacting input about your needs for more exacting output :-)
Luck & Regards,
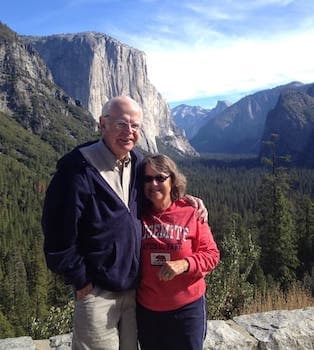
Ted Mooney, P.E. RET
Striving to live Aloha
(Ted can offer longterm or instant help)
finishing.com - Pine Beach, New Jersey
April 2021
Q. Sir, thank you for your reply. Kindly explain the procedure of PVD coating on ss wire, 304 grade, 0.15mm thickness. I want to gold color the stainless steel wire. Kindly provide in detail the method of PVD coating and material required for same. Thanks and regards.
Kuldeep Mittal- Delhi shalimar bagh, India [returning]
April 10, 2021
A. Hi Kuldeep. I doubt that anyone can offer you the "in detail" info you are looking for in the short format appropriate for a public forum ... I think you will need to contact suppliers of PVD machines.
I am not familiar enough with the process to tell you much except that PVD stands for 'physical vapor deposition', a process where your wire would be put into a vacuum chamber, sometimes partially back-filled with inert gas, along with 'targets' of titanium-bearing material; then heat would vaporize the titanium or other materials and, usually assisted with some sort of bias voltage, the materials solidify onto your wire as a titanium nitride or similar gold-colored hard coating. Whether the wire can best be handled as a coil or in continuous fashion, passing through some manner of vacuum seals is unfortunately beyond my experience :-)
But I do know that titanium nitride PVD coating of stainless steel materials is widely done, and that titanium nitride coated, gold-colored stainless steel building panels are a commodity item.
Luck & Regards,
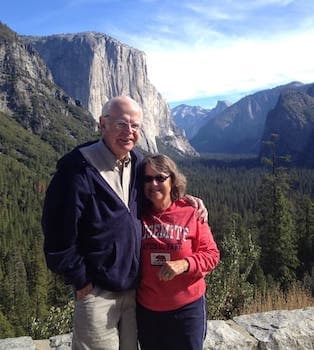
Ted Mooney, P.E. RET
Striving to live Aloha
(Ted can offer longterm or instant help)
finishing.com - Pine Beach, New Jersey
April 2021
Thank you very much sir for all your valuable information.
Thanks and regards
- Delhi shalimar bagh, India
April 12, 2021
May 12, 2021
Q. My name is Alan Pryde and I am the General Manager of a manufacturing facility in Hamilton, Ontario.
We use stainless steel wire in diameter from .014" - .028", I would like to colour coat the wire for identification purposes.
The coating cannot be a plastic or PVC as the product is subject to high heat of approximately 400 - 500° F.
The coating should be scratch resistant, UV resistant, and able to withstand the above heat.
Two part question:
1.0 What process can used to apply this coating
2.0 We would like to purchase equipment to do this in house
3.0 If the equipment purchase is not viable, what companies can do this?
The wire comes to us in 50 lb spool.
Thank you
- Hamilton Ontario
Hi Alan,
adv.
Please get back to me directly to admin@russamer.com
I need the SS alloy type. We can do multiple color anodized for 400-series SS, like 420, 430, 440; limited colors for 302. 304 alloy, and no colors for 316.
The process is color anodizing. We never did continuous anodizing for SS, mostly worked with color coding surgical instruments. If testing goes well, we can supply the process to your shop.
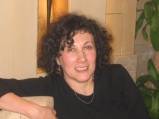
Anna Berkovich
Russamer Lab

Pittsburgh, Pennsylvania
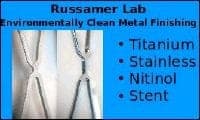
⇩ Related postings, oldest first ⇩
Q. Can someone please direct me into achieving coloring stainless steel (anodizing). I need to know what equipment to use and how to go about processing it. Thank you in advance.
Yours truly,
- Delta, BC, Canada
2002
A. Stainless steel does not anodize like Ti or niobium, it is called inco-colouring and is usually done with heat and moisture. Oven heating at a certain temperature with a certain amount of humidity will colour stainless steel.
Jeff Swayze- Kelowna, B.C.
2002
Q. Jeff,
Regarding Inco-colouring of stainless steel, how colorfast is the application for exterior applications? Thanks, Mike
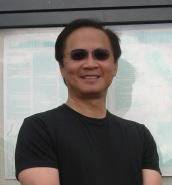
Michael Liu Taylor
specialty stainless steel distributor - Dallas, Texas
2002
A. Well, the layer of colouring on the stainless steel is approximately 20-30 angstroms thick (the usual thickness of chromium oxide on most well passivated stainless), so if the parts are not abraded or in contact with corrosive environments, the colouring should remain intact. Perhaps if you used a clear aftercoat, the colouring will be protected from environmental damage. Which grade of stainless are you referring to, and what is the application? Will the parts be ornamental , or will they be handled regularly? Your results will be dependent on your application, as the colouring can easily be abraded, or etched away in relatively corrosive atmospheres.
Good luck!
- Kelowna, B.C., Canada
A. The coloring is completely lightfast because no pigments are involved; it's a diffraction (interference) coloration caused by the light reflecting off the surface of the clear chrome oxide coating and off the surface of the part below the coating. The coating is a partial wavelength thick, which causes the interference.
For that reason, though, I doubt that you can clearcoat it without losing most of the color, because that adds a second transparent layer, probably too thick for partial-wavelength interference. Good luck.
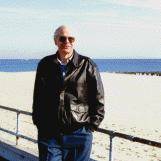
Ted Mooney, P.E.
Striving to live Aloha
(Ted can offer longterm or instant help)
finishing.com - Pine Beach, New Jersey
A. Actually, there is a proprietary method sold by one of the advertisers at this site. Look for Prismatic Stainless Steel [from B&M Finishers, a finishing.com supporting advertiser]. Color is jet black.
James Watts- Navarre, Florida
2002
2002
DEFINITION:
"Inco process" and "Inco coloring" have quickly become slang, especially with the International Nickel Company no longer in existence to clarify their intentions.
While Jeff says the "Inco process" refers to electroless oxidation, and the Products Finishing article seems to imply the same, the European S.S. Development Assoc. says that the term refers to the electrolytic (anodizing) process.
Thus, the term should probably only be used in a specification with care & precision or it may result in a contract dispute :-)
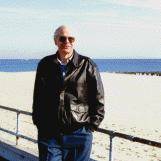
Ted Mooney, P.E.
Striving to live Aloha
(Ted can offer longterm or instant help)
finishing.com - Pine Beach, New Jersey
A. A coating on stainless steel may be achieved by an electro-chemical process, which creates a super-thin layer of chrome oxide. However, coloring 17-4 stainless steel is somewhat unpredictable, and better results may appear on 304 and 316 stainless steels. In theory, this procedure works best when the metal has been electropolished and demagnetized. In my experience, I have gotten different results, varying from drastic variation of tonalities from sample to sample (from brown to fainted black), to unevenness hues on one piece.
Instead, would black-oxide work for your application?
- Avilla, Indiana
2002
Q. Clinton Tharp, would you share your process and chemicals with me. I just want to color code 302 stainless steel pins, 22 gauge, 21 gauge and 20 gauge that are 3/4 inch long. So my pot or volume required is minimal and since my volumes are very small, it is not worth going outside for the process.
Mike Dalton- Skokie, Illinois, USA
June 13, 2011
Q. Please let me know what process is used to colour 304 stainless. Can I do it myself?
Theunis Pretoriusknives - Kempton Park, Gauteng, South Africa
May 13, 2008
Q. I WANT TO GIVE BROWN COLOR ON STAINLESS STEEL 304 BY DIPPING INTO A CHEMICAL (BY CURRENT OR WITHOUT CURRENT). PLEASE ALSO TELL ME , WHAT OTHER COLORS CAN BE OBTAINED ON STAINLESS STEEL BY DIPPING INTO SOME CHEMICALS.
REGARDS
- Gujranwala, Pakistan
January 24, 2012
Q. Most people are talking about using only 18SWG thick SS 304 or 316 material. Can this be done on 202 grade material which is 24SWG thick?
Visweswaran Manickam- Trichy, India
April 27, 2012
April 14, 2014
Q. Hello, I have a slight problem and would appreciate some help
I have been asked as a degree project to color some steel accessories (small pieces used for clothes).
After some research I have found that the steel in question is most likely stainless steel although I don't know what family exactly. I saw that it could be colored by adding a layer of chromium oxide by passivating it.
Now I used different baths and this is what I got so far :
. nitric acid 20% --> stainless steel goes yellow then dissolves if exposed any longer
. nitric acid 20% + sodium dichromate (3oz/gal) --> same result as above
. citric acid
⇦ on
eBay
or
Amazon [affil link] 10oz/w --> stainless steel goes tin pink but doesn't dissolve
So I want to ask, am I going in the right direction? And what am I doing wrong because I want to have other colors?
Thank you for your time
student - Korba, Tunisia
A. Hi Medhat. A first principle for science experiments is that they must be replicable. Nothing has been learned if they are not. So a science student should not be trying to develop a treatment process for an unknown material. You must find out what stainless you have :-)
Austenitic stainless steel is much more suitable for coloration than martensitic, so start by verifying that your sample is non-magnetic if you have no other clues. I don't have hands-on experience with this stuff, but we've linked to a Products Finishing artice about it. I have also read that you can do an anodic treatment to get the chromic oxide for better coloring, and that cathodic post-treatments are used for hardening the coating. While the finest treatments have surely been the result of extensive proprietary development, your experimentation can take you further than it has so far. Good luck!
An outstanding paper on all sorts of stainless coloration is Colouring Stainless Steel" by the European Stainless Steel Development Association.
Good luck and Regards,
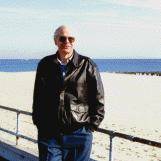
Ted Mooney, P.E.
Striving to live Aloha
(Ted can offer longterm or instant help)
finishing.com - Pine Beach, New Jersey
April 2014
Q. Which of these PVD (Physical Vapour Deposition) or Electroless (Inco process) is the best process for colouring of Stainless steel?
N Narasimha- Bangalore, Karnataka & India
June 11, 2018
A. Hi Narasimha. Many different methods would not be available if one were "best" of course. You need to describe the application, including what kind of coloring effect you are looking for, before anyone can explain the important advantages & disadvantages for that particular case.
But, in general, the previously referenced "Coloring Stainless Steel" white paper from the European Stainless Steel Development Association says about the electroless immersion process described in the illustrated "Products Finishing" article that "the coloured film obtained in this way proved too soft and porous to give adequate wear and abrasion resistance", and it references a study on it. It also explains why only corrosion-resistant stainless should be used for the electrolytic coloring process (anodizing), type 304 or better.
It may be worthwhile to mention that things can get 'color' from two very different sources. The first is from pigments or other "real" colors. If a child draws a rainbow with crayons or water paints they are putting pigments and "real" color onto the paper. But the child can put a rainbow-colored pattern onto a mud-puddle by applying a single drop of uncolored oil. That color is not "real", but is interference or diffraction colorization. Part of the light hitting the puddle reflects off the top of the oil, and part of it travels an additional partial wavelength through the oil and reflects off the surface of the water. The two portions of reflected light are out of phase by the thickness of the oil at that point, which amplifies some colors and cancels out others. Some PVD coatings have "true" coloration: titanium nitride coatings have a true gold color to them, whereas other PVD coatings and electrolytic colorization are actually transparent and get their color from diffraction. So if you want varying rainbow coloration like an oil slick, or you like the colors to change when viewed from different angles, either transparent PVD coatings or transparent electrolytic coatings can do it; but if you demand that the color not change when viewed from different angles and under different lighting conditions solid colors like titanium nitride PVD or electrolytically deposited brass or gold may be better and will generally be thicker and more abrasion resistant.
Regards,
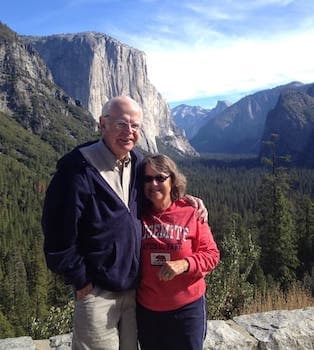
Ted Mooney, P.E. RET
Striving to live Aloha
(Ted can offer longterm or instant help)
finishing.com - Pine Beach, New Jersey
June 2018
Q. The application is for "316L stainless steel watch case" and required colors are Gold, Rose Gold, Dark Silver (lighter than Gun metal) and black(matte). Which is the best process for coloring this application?
N Naraimha [returning]- Bangalore, Karnataka & India
June 13, 2018
A. Hi again. Probably PVD. Good luck.
Regards,
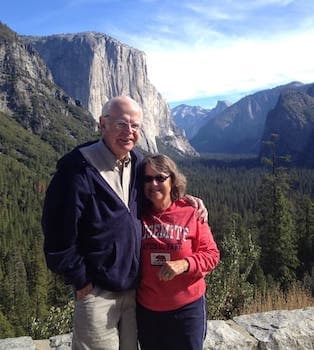
Ted Mooney, P.E. RET
Striving to live Aloha
(Ted can offer longterm or instant help)
finishing.com - Pine Beach, New Jersey
June 2018
----
Ed. note: Additional threads about coloring/anodizing of stainless steel include topics 1383, 21437, and 24520.
Q, A, or Comment on THIS thread -or- Start a NEW Thread