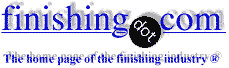
-----
Chromate Conversion vs Anodizing
Q1. What is the difference between anodizing and Chromate plating in terms of electrical conductivity?
Q2. Is there any visual way to differentiate between the two?
- Thailand
2002
A. Hi Juraine,
Anodizing is an electrolytically formed coating of aluminum oxide and it is totally non-conductive. Chromate is an immersion process which affords some corrosion protection but less than anodizing. Chromate by itself is almost totally non-conductive, however, when applied according to our MIL-C-5541, Class III is conductive. There is a lot of controversy regarding "contact resistance". With any chromate coating if you push the probe hard enough it will cut through the soft chromate film and make contact.
Chromate is yellow or clear, the clear being better conductivity. Anodizing is hard and clear (unless dyed).
Chromate will scratch with your fingernail. You cannot scratch anodizing with your fingernail.
Get back to me if this is not enough information.
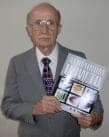
Robert H Probert
Robert H Probert Technical Services

Garner, North Carolina
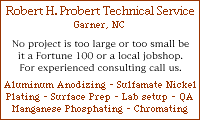
2002
Q. I'm new to this business, and was hoping someone could give me a quick overview of why chromate converting is a recommended process as a paint primer? Why is anodizing not?
Thanks,
Process engineer - Tucson, Arizona
2006
A. Patricia,
I think it comes down to a simple commercial decision. Chromate conversion coating is a simple immersion process and, in relative terms, is quick to do.
Anodising will give good paint adhesion but is an electrolytic process, takes longer, sometimes involves special jigging and can involve increased hazards (chromic acid mists for MIL-A-8625 / MIL-PRF-8625
[⇦ this spec on DLA] type I anodising).
If cost is no object to you I would always go for type I anodising as a key for paint. If costs need to be considered then chromate conversion coating is the answer.
Aerospace - Yeovil, Somerset, UK
2006
A. Chromating is the norm for paint base due to it being an immersion process as opposed to a longer, more expensive electrolytic process such as anodize. Anodize is also frowned upon in the aerospace industry, for example, as it lowers the fatigue strength of the aluminum. The thicker the anodic layer, the more degrading to the overall fatigue strength - this is why the thinnest, Type I, chromic anodize is widely used in the aerospace field.
adv.
If you have specific question, please E-mail me!

Milt Stevenson, Jr.
Syracuse, New York
2006
A. The main difference between anodizing and chromate conversion coating is the electrical conductivity of the finishes. Anodizing is non-conductive while chromate conversion coating gives an electrically conductive coating.
Reha Aktas- Tulsa, Oklahoma
2006
A. Reha,
I would be very careful with that statement. In accordance with MIL-DTL-5541
[⇦ this spec on DLA] only class 3 coatings should be used for electrical continuity.
As the thickness of chromate conversion increases so does the electrical resistance, so much so that a class 1A coating, to all intents and purposes, can be considered non-electrically conductive. The only way to get electrical conductivity with this coating is by breaching the coating.
Aerospace - Yeovil, Somerset, UK
2006
A. Chromating process is losing popularity as it is detrimental for environment. There are non-chromate products tested and recommended to replace chromate products.
Timur Ulucakaluminum extrusions & finishing - Istanbul, Turkey
2006
May 1, 2016
A. Chromate Conversion and Anodisation Both are Passivation processes on aluminium.(both are corrosion resistant coatings, both increase paint adhesion for aluminium due to formation of pores.)
In Chromatisation the Workpiece is dipped in a Hot Bath so that a layer of conductive Cr2O3 is formed on the job.
Whereas in Anodisation a layer of non conductive Al2O3 is formed through Method of Electrolytic passivation... passage of current in a bath with aluminium as anode.
Chromatisation is generally much cheaper then anodisation.
The process you should follow should depend on the application of your product.
Say if you need a low bonding resistance between two mating parts so as to provide a better conductive path, then you should go for Chromatisation (preferably Trivalent).
If you need abrasion /wear resistance, or say you are designing a heat sink for a system, you should go for anodisation and black dye.
avionics - Delhi, India
Q. How to get electrical conductivity on aluminium after anodizing or from other coating?
I have a sample from customer where his anodized aluminium is conductive with 10^3. But when I did anodizing on aluminium it's not conductive. its only ESD with 10^10.
Can anyone advise me how I can get electrical conductivity after anodizing on aluminium? What kind of anodized?
Does e-coating(what kind?), Chromate, Alodine and Iridite get the electrical conductivity? But it must not have any banned substances on the finishing.
Thanks in advance.
- Jakarta, Indonesia
October 17, 2016
A. Hi Andrew. Aluminum can be chromate conversion coated with trivalent (no hexavalent chrome) per MIL-DTL-5541 [⇦ this spec on DLA], Type II, Class 3. Good luck.
It is also possible to do conductive anodizing (see thread 7297), but this is quite a bot more complicated and expensive.
Regards,
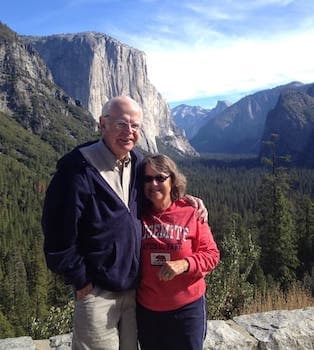
Ted Mooney, P.E. RET
Striving to live Aloha
finishing.com - Pine Beach, New Jersey
October 2016
Q. What is typical electrical contact resistance values in micro-ohms for chromatized (Type I class 3) Al alloy. Why does it increase upon corrosion tests?
Deepashri NageLarsen & Toubro - Mumbai, Maharashtra, India
January 10, 2019
A. Hi Deepashri. Per MIL-DTL-5541 rev. F:
Presumably the corrosion test is partially successful in corroding the finish so that its surface conductance is not as reliably low. Good luck.
Regards,
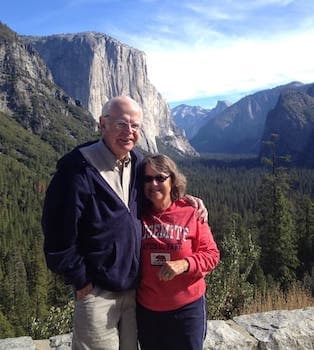
Ted Mooney, P.E. RET
Striving to live Aloha
finishing.com - Pine Beach, New Jersey
Q. Thanks Ted, for your reply. However, I was expecting typical values based on the inherent film formed.
Irrespective of the measuring device, method etc. Does the measurement area under consideration affect the values?
- Mumbai, Maharashtra, India
January 11, 2019
A. Hi again Dr. Nage. Apparently the authors of MIL-DTL-5541 do not believe that such values are "irrespective of the measuring device, method, etc." as you might wish, but are highly dependent upon it. I personally have never seen the test done and know little about it, but we have several threads about it on the site ...
Please search the site with the term "chromate conductivity test" (google prohibits us from pre-loading search terms into the custom search engine) ...
Or post the method you are using, the type of parts you are testing, and the results you have been getting, and you'll probably draw enthusiastic response. But after 30 years of postings, 60,000 questions and a quarter million replies, abstract questions seem to no longer draw much reader interest. Good luck.
Regards,
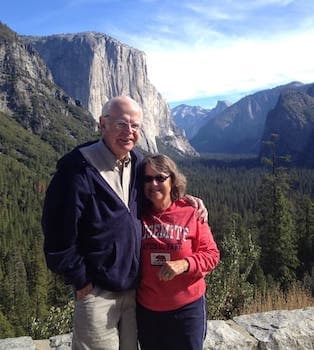
Ted Mooney, P.E. RET
Striving to live Aloha
finishing.com - Pine Beach, New Jersey
January 2019
⇦ Tip: Readers want to learn from your situation;
so some readers skip abstract questions.
Which coating is best for aluminium, anodizing vs. chromating
Arun kumar- Tamil Nadu
December 19, 2019
? Hi Arun. They have wildly different thermal conductivity and electrical conductivity, totally different hardness and abrasion resistance, differing paintability, appearance, cost, and corrosion resistance. We can either refer you to many long chapters in textbooks (there's a lot to it), or you can tell us your situation and we can probably answer which is preferable and why in a paragraph or two. Get back to us please.
Regards,
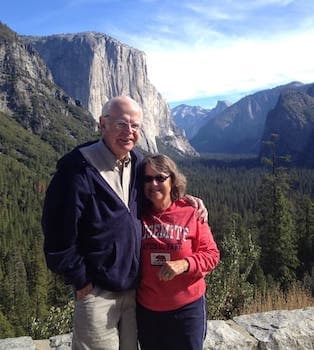
Ted Mooney, P.E. RET
Striving to live Aloha
finishing.com - Pine Beach, New Jersey
December 2019
Q, A, or Comment on THIS thread -or- Start a NEW Thread