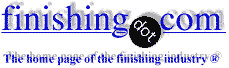
-----
Formula for polishing and buffing compounds
Quickstart:
Polishing and buffing is primarily a mechanical rather than a chemical process -- the abrasives in the compound do the work. Abrasives are of different materials depending upon the substrate which is being polished, and of different grit sizes because you can't get a fine finish with large grit (you'll continue scratching it), but can't polish in a reasonable time period with fine grit (no one digs the foundation for a skyscraper with a teaspoon).
Usually one starts with a grit rough enough to remove all prior scratches quickly; then a finer grit is used but which can remove all the scratches from step 1 in a reasonable time; then a still finer grit is used that can remove all the scratches from step 2 in a reasonable time, etc. Common practice is to sweep in one direction for steps 1, 3 and 5 (if applicable) and in the perpendicular direction for steps 2, 4, and 6 because this allows seeing that all scratches from the previous step have been removed before proceeding.
⇦ Tip: Readers want to learn from your situation;
so some readers skip abstract questions.
Q. Is there any additive to increase volume of binder? Or a direction to do that?
Matt GomezShop employee - Germany
January 18, 2022
⇦ Tip: Readers want to learn from your situation;
so some readers skip abstract questions.
Q. Can anybody tell me alternative to tripoli as it is expensive?
Shamim ahmed
Worker - Karachi Pakistan
January 26, 2022
A. Shamim: Calcined kaolin.
Alex Byarugaba- Kampala Uganda
July 12, 2022
⇩ Related postings, oldest first ⇩
Q. Hello,
I am a small business man from TN. I want to start a small scale of bars used for polishing and buffing stainless steel. I want to know the perfect formulation of chemicals used for polishing and buffing stainless steel and aluminium. Can you please say me the formula of chemicals used for the above process. I am awaiting your reply for opening my new polish material shop.
Thanks,
Vinod Rajpurohit- Madurai, TN, India
2002
(affil links)
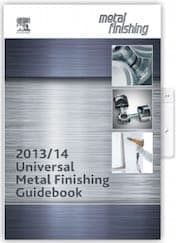
free pdf is currently available from academia.edu
A. Hi cousin Vinod. Please use internet advice from strangers as helpful little hints or for directing you towards authoritative sources. Never invest money based on it :-)
Please start by at least reading the "Buffing & Polishing" and "Buffing Wheels & Equipment" chapters in the Metal Finishing Guidebook ⇨
so you have an understanding of how to select abrasive materials and different abrasive sizes, and what the characteristics are of stainless steel and aluminum which will help guide those choices. Your customers are not likely to be able to polish & buff with a single type of bar, but will probably need a number of different grit sizes.
Because buffing compound bars are a commercial product rather than a home-brew affair, trade secrets are involved and you won't see much about their exact composition in technical articles or on the internet ... but I believe you will be able to find some introductory info in expired patents, and can then do further development efforts. Best of luck.
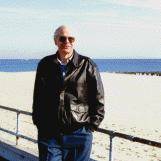
Ted Mooney, P.E.
Striving to live Aloha
(Ted can offer longterm or instant help)
finishing.com - Pine Beach, New Jersey
A. Not sure what you are looking for here. I suspect no one will give you the actual formulation of a buffing compound; however, it shouldn't be that hard either. The primary ingredient is normally an extremely fine aluminum oxide powder blended in some form of fatty compound. Compounds are formulated to work in or at a certain temperature range.

AF Kenton
retired business owner - Hatboro, Pennsylvania
Q. I want to know the composition of buffing compound for stainless steel, what its demand is all over the world, and what is its scope in future.
Reshmi [last name deleted for privacy by Editor]- Chennai, Tamil Nadu, India
February 13, 2013
A. Hi Reshmi. We added your inquiry to this thread about the composition of buffing compound. Marketing studies about current & future demand for product lines like this are generally offered in the $50,000 USD range, so I doubt that you'll receive any actionable info from your posting; but here it is, and best of luck.
Regards,
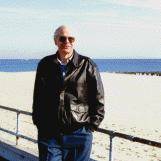
Ted Mooney, P.E.
Striving to live Aloha
(Ted can offer longterm or instant help)
finishing.com - Pine Beach, New Jersey
Q. I needed an expert's advice on polishing compounds.
If we use a freshly made compound and a compound which is comparatively older than the previous one, will the effect differ. Also wanted to know which bar should I use for cutting and pre polishing on stainless steel? We have a lot of options available but what should be the base of it?
- Mumbai, India
May 6, 2013
A. Hi Abhinav. Buffing compounds do have "shelf lives", probably mostly related to evaporation of solvents from the binders. The life after the package is opened is much shorter than while the packaging is still sealed.
What is really at "the base of it" is this: buffing and polishing is not something you can practically do with a single bar of compound for the same reason that you don't dig the foundation for a skyscraper with a tea spoon, nor try to put the coffee grounds in your percolator with a steam shovel. Too coarse an abrasive selection would mean you never stop putting substantial scratches into the workpiece, and too fine an abrasive would take forever and a day to do a heavy cut.
So you start with however coarse an abrasive you need to remove the largest and deepest grinding or handling scratches in a practical amount of time, and you end with however fine an abrasive you need for the degree of final buffing you seek. Frequently, two compounds are not enough and you need three or four stages -- sometimes even more.
You also must select abrasives that are hard enough to cut stainless steel and are iron-free (such as alumina and green chromic oxide) because the use of iron will make the stainless steel prone to rusting. This is mostly just book knowledge, so readers are welcome to expand upon it or correct me.
Regards,
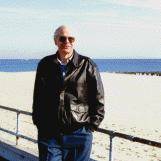
Ted Mooney, P.E.
Striving to live Aloha
(Ted can offer longterm or instant help)
finishing.com - Pine Beach, New Jersey
Thanks a lot Ted. The main issue with us always has been these compounds. This is one of the most important steps of plating and finishing industry but in our country it is the most overlooked upon since one has to all the dirty work.
Thanks a ton.
- Mumbai, India
May 11, 2013
Q. I wanted to know if there is any other alternative than aluminium oxide that can provide a better cutting result? Which mineral can be used to get a good result for removing initial heavy scratches from a stainless steel surface?
Abhinav Agarwal [returning]- Mumbai, India
January 31, 2014
A. There are a lot of other minerals out there that can abrade S.S.; however, normally aluminum oxide is the most common, the hardest and about the least expensive -- that is why it is used most. How are you going to use abrasive?

AF Kenton
retired business owner - Hatboro, Pennsylvania
Q. We do not know a good performing abrasive rather than aluminium oxide. Silica fades away very quickly which we do not use. I tried using a lot but currently unable to get the desired results. If you could suggest a few items, I could well try that. Plus what should be ratio of binders? Could you suggest us on that.
Abhinav Agarwal [returning]- Mumbai, India
September 18, 2014
A. If the media does not break down, it is not a good abrasive. That is why abrasive blast systems need to replace media periodically. If you want to try some hard crystal abrasive alternatives, you try garnet or zirconia.

AF Kenton
retired business owner - Hatboro, Pennsylvania
Q. Dear AF Kenton:
May you please tell me which is the abrasive and grain size to satin metals in a fantasy manufacturing shop?
Thank you.
- bogota, colombia
November 11, 2014
A. All abrasives media comes in different sizes. The larger the media size the coarser the surface finish. Hardness of the metal also affects the finish. Most satin metal finishes can be achieved with anywhere from 60-120 grit size media.

AF Kenton
retired business owner - Hatboro, Pennsylvania
Q.
Thank you Mr. kenton. Also I understand that to satin metals the solid abrasive compound should be greaseless. May you please tell me which greaseless binder should I use?
Thank you
- bogota colombia SA
A. Okay. Considered your question and think it is basically proprietary info that I do not have access too; however, I can give you a generic answer. Polishing compounds can be in a liquid or solid form. Naturally the less liquid the thicker the polish. When it comes to solid bars, most use a form of grease to bind rouge but you can use glue products.

AF Kenton
retired business owner - Hatboro, Pennsylvania
Q. Hi all,
Please help … What is the substitute of kerosene for metal finishing?
And why kerosene is even used after using polishing compounds?
hard chrome plating - New delhi, delhi - India
February 27, 2016
Color vs. Grit Size for Abrasives
Q. What is the significance of Color of abrasives? I've got 2 polishing compounds one Green and Red. Both these compounds have abrasive particles of same grit.
Amit KunchalManufacturer - Bangalore, India
October 15, 2016
A. Hi Amit. Although grit size is one important parameter for polishing, there is more to it than that, including what the abrasive is made of: aluminum oxide, emery, chromic oxide, tripoli, etc. It is possible that the green is made of chromic oxide (suitable for polishing stainless steel) and the red is emery not suitable for stainless because it induces rust. Even still, some manufacturers dye the abrasive bars to help you visually insure that it has all been removed before subsequent operations. If you tell us your situation, i.e., what you are trying to finish and what finish you need, it's possible that a reader will offer specific advice on which abrasives to use. Good luck.
Regards,
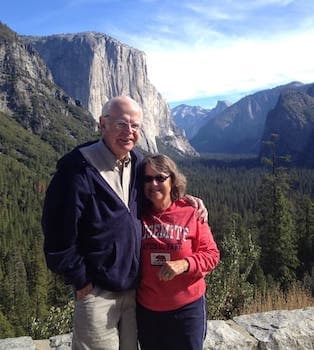
Ted Mooney, P.E. RET
Striving to live Aloha
(Ted can offer longterm or instant help)
finishing.com - Pine Beach, New Jersey
October 2016
Q. I have 2 polishing compounds.
Green made of Chrome Oxide.
Red made of Ferric Oxide.
Both have same grit size of 200.
Now if I use these 2 compounds on different metal surface such as:
1. Any white metal like Stainless Steel.
2. Any yellow metal like Copper.
What is the impact of color of compound?
What I understand that as grit size is same so polishing effect need to be similar.
Please comment.
- Bangalore, India
October 16, 2016
A. Amit,
I would not recommend using Ferric Oxide on stainless steel primarily to avoid contaminating a corrosion protected metal with ferric oxide. I haven't tested this, but simple mental evaluation for my own purposes is that it is something I would avoid. Chrome oxide is often times specifically used on stainless and therefore would be something I would go to for SS.
For copper, brass, bronze, zinc I would use brown Tripoli compound, although ferric oxide (red rouge) can be used and is on precious metals quite often and I'm sure would do a fine job on copper, brass, etc...
Both of what you have are very fine low cutting compounds and used normally for final finishing where polishing and low cutting is needed.
--Rama
- Woodinville, Washington USA
October 24, 2016
Q. I manufacture a compound using different oxides.
1. Yellow Ochre with 100 grit size.
2. Silica with 200 grit size.
I want to understand when we are mixing compound with different grit size, then what is the impact on finishing.
Will this compound behave more like compound with 100 grit size?
If yes, then what is the benefit of silica in compound?
Manufacturer - Bangalore, India
November 4, 2016
A. In regards to the last question about mixing. There is nothing gained by using 2 different grit sizes. You will not get more abrasion faster or smoother than using one or the other. You will get a measurement of the rougher abrasive but you may not get an even visual appearance of it.

AF Kenton
retired business owner - Hatboro, Pennsylvania
How does the grease content of Polishing Compound effect finishing?
Q. I see many different metal polishing compounds in market. Some are dry and some are oily. So how does the grease content in compound affect final finishing?
Amit Kunchal [returning]Manufacturer - Bangalore, India
December 5, 2016
A. Hi Amit, the previously mentioned article in the Metal Finishing Guidebook, which can be read right now at no cost, spends 8 pages explaining when and why to use solvent based vs. water based, liquid vs. solid, etc. Good luck.
Regards,
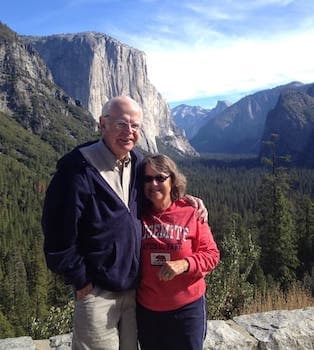
Ted Mooney, P.E. RET
Striving to live Aloha
(Ted can offer longterm or instant help)
finishing.com - Pine Beach, New Jersey
Looking for Technical Resources
Q I am manufacturer of metal polishing and buffing compound in India.
I am already manufacturing many different compounds with set formulation.
I really like to design new products for Indian market, but somehow due to lack of technical expertise, I am unable to do so.
I am looking for some consultants or some books on the same topic which can help me in designing new products.
Manufacturer - Bangalore, India
December 6, 2016
Q. I'm working in industrial workshop. I want to use polishing paste for steel sheets. Can you please tell me the formula of chemicals used for polishing paste?
Thanks
- tehran, iran
November 20, 2017
A. Hi cousin Sajad. As you can see, polishing is a whole technical discipline with some people devoting their entire careers to it. So please read this page and the free linked articles and try to fine tune your question with information such as what type of steel, what roughness it is when it gets to you, what roughness you want it to have at the conclusion of all your polishing and buffing steps, and what will be the next step (plating, painting, powder coating, galvanizing, oiling).
Is there a reason you can't just buy the already formulated polishing paste instead of having to buy all the individual commodity components? Thanks.
Regards,
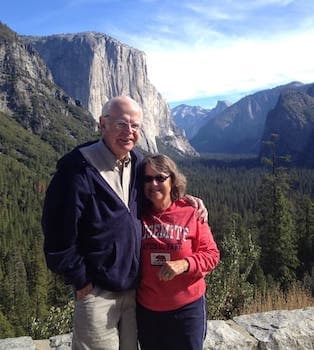
Ted Mooney, P.E. RET
Striving to live Aloha
(Ted can offer longterm or instant help)
finishing.com - Pine Beach, New Jersey
Q. Hi, I am in polishing compound manufacture; right know I am using green chrome, but it gives yellow shine.
I need a suggestion which chemical like green chrome can give blue shining.
manufacturing - nellore, andhra pradesh, India
November 21, 2017
Volck oil emulsifiers?
Q. Hi
Which emulsifier is used in Volck oil when diluting oil with water to make white-milky concentrated emulsion?
I am looking for an emulsifier agent that can make a milky emulsion canola oil in water?
Thanks.
student - iran
February 26, 2018
A. Making of polishing buffing bar a hot sell is any manufacturer's dream come true. For those who have succeeded are millionaires already. Because here no amount of marketing helps. Only the product speaks. The formula is very much required from the experienced. It's priceless!
Pavan dogra- Chennai, TN, India
A. I have been polishing metals for some time, and I make my own polishing compound. I have read a lot of patents and try almost everything. I have gotten Mirror-like finish in SS by using 700-800 g chrome oxide (green powder), 150 g paraffin, 150 g tallow stearine (or stearic acid
⇦ on
eBay or
Amazon [affil link] ). You can try fused alumina, but you need a particle size below 10 microns, otherwise you won't have a perfect bright mirror like surface.
Hope it helps you!
- Mariel, Artemisa, Cuba
January 5, 2019
Q. Hi
I need a way to Recycling of polishing soap that have broken down and are not useful. For this job, I liquify them with heat, and again format them to soap. But this reduces the quality of soap. So I want to know how can I up the quality of soap by adding something to the liquid?
Thanks.
stainless steel - sirjan, iran
February 4, 2019
April 2, 2019
Hi...
I want to do the business of metal polishing bar.
And don't know how to manufacture it, I know some ingredients. Can someone help me in this.
- Moradabad,UP, India
April 2019
(affil links)
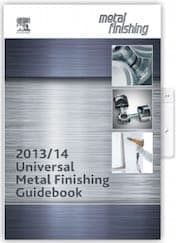
free pdf is currently available from academia.edu
A. Hi cousin Mohd. When you say you are you looking for someone to help, do you mean that you want to retain a consultant? If so, please post your inquiry as an RFQ so that we can share your contact info with the readers. Thanks.
If you are looking for free public help, did you follow the previous advice and read the two chapters in the online version of the Metal Finishing Guidebook as I suggested? Please download the book today because one of these days it probably won't be available anymore. If you have any specific questions, I think the readers will be happy to address them.
You might also try to obtain a hard copy of an earlier edition of that book because earlier editions have coverage by different authors so you will gain multiple perspectives. Good luck!
Regards,
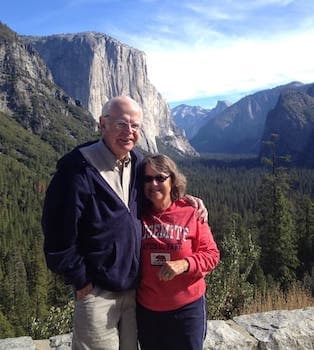
Ted Mooney, P.E. RET
Striving to live Aloha
(Ted can offer longterm or instant help)
finishing.com - Pine Beach, New Jersey
Q. Hi,
I am currently working in metal polish formulation.
I'm using about 5% of White Aluminium Oxide (200 mesh) and mixed with Silitin and found a lot of small scratches during polishing compared to silitin alone.
Is there any option how to reduce the scratches?
Amerseal Industrial Sdn Bhd - Kuantan, Pahang, Malaysia
April 4, 2019
A. Hi Nurul. I don't actually know how to formulate polishing pastes, but I do know that the purpose of the abrasive is to 'scratch' the surfaces. The problem might be that the mesh/grit size is too low for the fineness of the finish you are trying to offer.
Regards,
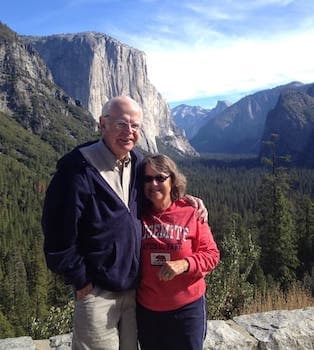
Ted Mooney, P.E. RET
Striving to live Aloha
(Ted can offer longterm or instant help)
finishing.com - Pine Beach, New Jersey
A. Hi, Nurul and other readers,
I'm not from the polishing or metal finishing industry. My comments are at best, general in this respect. Exact formulations, as had been mentioned here and elsewhere by Ted as well as others, are proprietary or Trade Secrets. As such, the exact form, particle sizes or the precise weight percentage of individual components within a product shall not be made known to the public on any SDS/MSDS of any manufacturer.
The basic abrasive most commonly used for stainless steel polishing is green chromic oxide. It's normally uncommon to find it as the sole abrasive in any commercial compounds for such applications. A fair amount of aluminum oxide, whatever the forms, are normally incorporated as well. In addition, depending on the products from different suppliers, fillers and other property modifiers such as calcium carbonate, silica (both amorphous and crystalline forms), kaolinite, etc are usually present.
The binders can be solid or semi-pasty at room temperatures. These usually are petroleum-based waxes and some fatty acids.
Hard alumina particles passing a 200 mesh sieve approximates 74 microns, which is not too different from what is found for the finer portion of hydraulic cement powders. These are suitable for removing deeper scratches, not for buffing to a mirror finish. You'll need softer materials which should crumble during polishing if that's the only size range available. The combination wouldn't be suitable for hard metals such as chrome-based alloys, which requires very fine, hard materials such as chromic oxide powders. These do not interact with the base metal to produce undesirable discolorations on such surfaces. As mentioned, polishing involves several stages from coarsest for scratch removal to the finest for the finish.
- Negeri Sembilan, Malaysia
Terrific explanation, Mark! Thanks!
Regards,
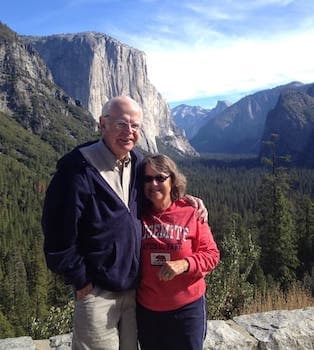
Ted Mooney, P.E. RET
Striving to live Aloha
(Ted can offer longterm or instant help)
finishing.com - Pine Beach, New Jersey
Q. Hi I am a piddler which means I do little projects. I am doing wood burning and it is recommended to use green polishing compound to clean the tips. I was looking for the compounds in green polishing compound to see how I can salvage a dry green polishing compound but the posts don't say exact ingredients of polishing compound so now I ask. How can you soften a very hard green polishing compound? The one I have is sort of dried out. Thank for any help.
Connie McCollum- Seneca, South Carolina USA
August 20, 2019
A. Hi Connie. Sorry it's dried up on you, but you'll never find exactly what solvents were in it. Kerosene might or might not loosen it up, but do that only outside because of extreme flammability, of course, and be mindful that a hot woodburning tip can therefore be trouble.
I would suggest, instead, getting some new green compound (it's quite cheap) and keeping it in a tightly sealed jar or wrapping it with saran wrap.
Regards,
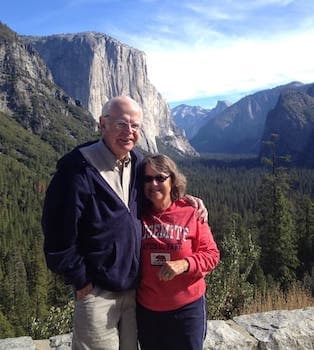
Ted Mooney, P.E. RET
Striving to live Aloha
(Ted can offer longterm or instant help)
finishing.com - Pine Beach, New Jersey
August 2019
Hello from Connie McCollum. Thank you for your quick response to my question. I will go buy some more to prevent any problems. That was my first time visiting this site and I'm very impressed with the knowledge of the people who ask questions and the responses given. Again thank you.
- Seneca, South Carolina USA
August 23, 2019
Looking for Animal Free Polishing Compounds
Q. Most of the Alumina Paste products contain animal products, most often part of the grease binder. Are there products that are free of animal products that could be used to polish Stainless Steel?
Jerry LyonsSales guy for Manufacturer of SS products doing some research on his own - Cincinnati, Ohio USA
October 14, 2019
February 27, 2021
Ed. note: Please, please, pretty please,
No abstract questions!
Q. Need formula to make solid and liquid polishing compound for metal polishing.
Rajeev Mohta- FARIDABAD, INDIA
Q. I want to make green buffing compound for aluminium buffing. The main thing to remove scratches from aluminium and get mirror finish, please give me the formula to make this compound.
Anto o.R- kerala India
March 12, 2021
A. Try archive .org website -- there you can find many download free old chemical formulas handbooks. (https://archive.org/details/in.ernet.dli.2015.198912?q=metal+polish)
Hope it helps and good luck!
- Cerovski vrh Croatia
March 16, 2021
November 22, 2021
I have just manufactured a polishing compound and my product quality is the same as polishing compound which are in market but I have a question:
1. by the same weight my volume product is lower than market one, do you have any suggestion in order to increasing the volume?
student - england
A. Hi. If I were you I'd probably just label mine as "super concentrated", but you can look up the directions for whipped butter and see if simply whipping yours lets it keep the air in suspension to lighten it.
Luck & Regards,
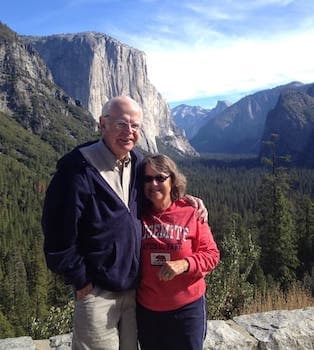
Ted Mooney, P.E. RET
Striving to live Aloha
(Ted can offer longterm or instant help)
finishing.com - Pine Beach, New Jersey
November 2021
Q, A, or Comment on THIS thread -or- Start a NEW Thread