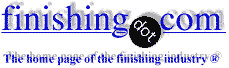
-----
Surface Activation for Phosphating. Grain Size Issues
Q. Good morning Sir, I'm from Pune, India. We are in process of developing a component in Manganese Phosphating. We are struggling to get consistent layer of Phosphate. If we grit blast the surface (even fine blasting), the phosphating is achieved -- which I believe means, the surface is not active enough. We have degreased the parts with various methods so as to eliminate the possibility of failure owing to ineffective cleaning.
Please guide us. We are using Nihon Parkerising products. They are good for other parts. However we are struggling with this one. The chemistry of target component is Carbon 0.38-0.43%, Chromium 0.8-1.1%, Moly 0.15-0.25%, Manganese 0.75-1.0%, Silicon 0.15-0.3%. It is AISI 4140 steel.Kindly guide us. Regards,
- PUNE, Maharashtra, India
July 28, 2022
A. This can be handled effectively by electrolytic phosphating process.
Prakash Hegde- Bangalore, India
December 21, 2022
⇦ Tip: Readers want to learn from your situation;
so some readers skip abstract questions.
Q. Hello, I am trying to optimize our parkerize process and I noticed that our activation bath is at room temperature while most parkerized process I see in the internet have heated their activation baths. I would like to know how does the activation temperature affects parkerization?
Vince GoIntern - Philippines
August 15, 2022
⇩ Related postings, oldest first ⇩
⇦ Tip: Readers want to learn from your situation;
so some readers skip abstract questions.
Q. In zinc phosphating what is importance of activation? What is chemical composition of activators ? How can it maintained ?
Vishwas M.painting shop - Indore, India
2002
A. Surface Activation chemicals activate the metal to obtain fine crystalline structure during phosphate coating which will increase corrosion resistance and adhesion properties. Crystalline structure less than 10 Microns always preferable.If we are not using activation rinse, the phosphate crystal size may be large and results in voids in Phosphate coating (Gap between structure will be large). Corrosion will take place at the voids.
Basically it is a Titanium based weak alkali chemical.
pH and Alkalinity are the parameters to be maintained daily.
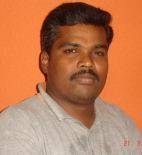
P.M.Saravanan
paint shop manager
Chennai, Tamilnadu, India
2007
⇦ Tip: Readers want to learn from your situation;
so some readers skip abstract questions.
Q. @Saravanan,
Can you explain in detail about surface Activation process in pt line?
Employee - Bangalore, India
March 2, 2022
A. Hi nivedha.
T.S.N. Sankara Narayanan offers quite a bit of detail below.
If you are a supplier trying to develop your own titanium activation solution, patent DE 10 2008 054 407 B4 looks like a good start (https://patents.google.com/patent/DE102008054407B4/en?q=titanium+activation+phosphating&oq=titanium+activation+phosphating).
Saravanan's posting was from 15 years ago so I'm afraid he is unlikely to see it. Please introduce yourself and your situation that motivates you to find his reply insufficient so we can move in the direction you need. Do you not yet have a titanium-based activation process in your PT line, or you do have one but it is not accomplishing what Saravanan says it should? Or do you lack the technical data sheets from the solution supplier to operate it? Or are you a chemical distributor trying to find a supplier of this process, or a student writing a thesis?
Luck & Regards,
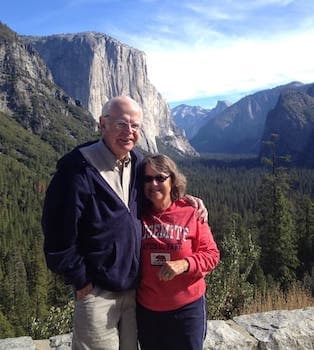
Ted Mooney, P.E. RET
Striving to live Aloha
(Ted can offer longterm or instant help)
finishing.com - Pine Beach, New Jersey
Very low pH in activation bath
Q. Sir,
We are operating tri-cationic phosphating. Our surface activation bath is deviating from the spec. in total alkalinity. It is very low in the range of 1.2-1.5 against 1.8-2.2. I will be grateful to know the reason.
babu sankar- hosur,tamilnadu
2003
A. I would recommend that you control the bath using the following significant characteristics Total Titanium/Filterable Titanium and pH. If the pH/alkalinity is falling then you need to:
1) Check the water used to replenish the bath. You may need to use de-mineralised water if the town water is suspect.
2) Phosphate solution may be spraying back due to misdirected entry sprays or along the conveyor shroud. This will reduce the pH and cause greater problems if not fixed. You should also demand that your chemical supplier investigate the problem as you may be using the wrong product for your conditions.
Good Luck,
David Hall- Melbourne, Australia
Q. We are facing same issue although we are using good quality DI water & also there is no phosphate solution contamination. Please comment if anyone has any solution.
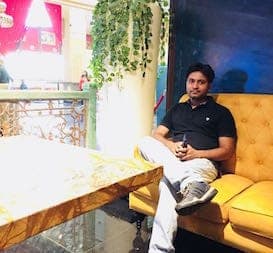
Nikhil Singh
Steel strips wheels ltd - Jamshedpur, Jharkhand, India
July 16, 2018
Hi Nikhil. Can you give us the "Total Titanium/Filterable Titanium and pH" which David suggested that you monitor? Have you made a "demand that your chemical supplier investigate the problem"? Can you tell us anything else at all?
I know you're only looking for quick help, but when someone asks for help, and it is offered, then a 3rd person offers no new data to evaluate, just says "I have the same issue and you were wrong, keep guessing", it rarely works.
Best of luck, and keep your fingers crossed for a helpful reader :-)
Regards,
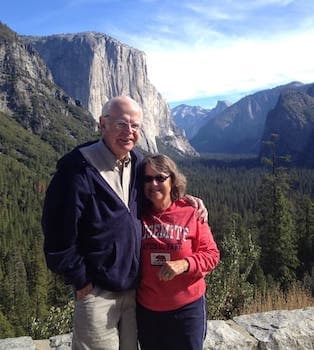
Ted Mooney, P.E. RET
Striving to live Aloha
(Ted can offer longterm or instant help)
finishing.com - Pine Beach, New Jersey
July 2018
Multiple threads merged: please forgive chronology errors and repetition 🙂
Necessity of Grain refiner for phosphating
Q. In the process of looking for alternative suppliers for grain refiner for zinc phosphating I realized that I do not even know what the grain refiner is. Our MSDS say nothing about ingredients because apparently none of them are "hazardous". I have looked in reference materials such as Metal Finishing Guide Book, Electroplating Engineering Handbook ⇦ this on eBay, AbeBooks, or Amazon [affil link] , Chemical Surface Treatments of Metals (book), and Conversion Coatings (book) and have not seen any discussion of what the refiner is and how it works. Are you aware of resources that discuss this?
Tim DenhofJob Shop Engineer - Chicago, Illinois, USA
2005
A. Grain refiners are chemical compounds usually added in activation (pre-dip) bath and/or the phosphating bath to reduce the crystal size in manganese and zinc phosphating processes.
Grain refinement in phosphate coating could be achieved by activating the surface using colloidal titanium phosphate prior to phosphating. During activation, the colloidal titanium phosphate particles are physically adsorbed on the metal surface and when the activated substrate comes in contact with a zinc phosphating bath, an ion exchange between the sodium ions on the surface of the titanium phosphate particles and the zinc ions of the phosphating solution takes place. The ion-exchanged particles act as nucleation agents for the zinc phosphate crystals because they have nearly the same stoichiometry and offer a crystallographic plane for an epitaxial growth.
The process for activating steel surface prior to phosphating was given in many patents. Use of 1-2% disodium phosphate solution containing 0.01% of titanium compounds have been extensively used in industries. Dilute solutions of cupric or nickel sulphates, oxalic acid and polyphosphonates also help in increasing the number of initial nuclei formed during phosphating and their subsequent growth, to yield thin and compact coatings of fine-grained nature.
The incorporation of calcium ions in a zinc phosphating enables a reduction in the grain size of the phosphating coating. The reduction in grain-size (25 micrometer to 4 micrometer) and the improvement in the compactness of the coating and corrosion resistance make this kind of modification of zinc phosphating baths as an important type of phosphating and it has been classified as calcium-modified zinc phosphating.
Similarly, addition of manganese and nickel ions in the zinc phosphating bath proves to be useful in refining the crystal size and improving the corrosion resistance of the resultant phosphate coatings.
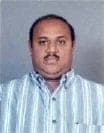
T.S.N. Sankara Narayanan
- Chennai, Tamilnadu, India
(ed.note: The good doctor offers a fascinating blog, "Advancement in Science" )
Nickel in zinc phosphate solution
Q. Sir,
we supply zinc phosphate solutions which are nickel free to customers who use for paint-base applications on MS. however I would like to know if its alright to add nickel if we want to broaden our range of applications.
Thanks,
electroplating chemicals - Thane, Maharashtra and India
2005
A. Modification of the phosphating baths with nickel salts assumes significance with the introduction of pre-coated steels such as zinc, zinc alloy coated steels, etc., for automotive body panels which present challenges regarding the stability of phosphate coatings. These pre-coated steels show good performance with regard to formability and weldability. The extent of perforation and cosmetic corrosion is also less with these materials and they also posses a good surface appearance. When zinc and zinc alloy coated steels is phosphated using a nickel-free zinc phosphating bath the resultant coating will comprise only the hopeite (zinc phosphate) phase. Phosphate coating on these substrates having only the hopeite phase is not desirable for subsequent cathodic electrophoretic painting.
Nickel modified low-zinc phosphating formulations are the most significant modification proposed to cope up with the cathodic coating, particularly in the automobile industry. The presence of Ni2+ ions in these phosphating baths has several advantages. Although there is a decrease in coating weight, crystal formation occurs at an early stage and the crystal size is fine. The Ni2+ ions participate in the formation of phosphate crystal and enables crystal refinement. In this perspective, nickel addition in zinc phosphating baths is beneficial. However, the metal finishing industries are facing stringent regulations in effluent disposal and there is a transition from Cr(VI) free, Cd free and Pb free processes. Nickel is also carcinogenic. So you might consider other alternatives.
One possible alternative:
Addition of manganese salts in zinc phosphating bath could also perform a similar role as that of nickel in phosphating of zinc and zinc alloy coated steels. The addition of Mn2+ ions in the phosphating bath helps to increase the rate of formation of coating and also the working width of the phosphating bath. Also, the presence of manganese in the zinc phosphate coating resists the formation of white spots on galvanized steel. Manganese modified zinc phosphate coating possesses better corrosion resistance.
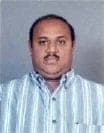
T.S.N. Sankara Narayanan
- Chennai, Tamilnadu, India
(ed.note: The good doctor offers a fascinating blog, "Advancement in Science" )
2005
Shri Narayanan,
Thank you for the reply. Our inclination is to go Ni-free.
electroplating Chemicals - Thane, Maharashtra and India
2005
Multiple threads merged: please forgive chronology errors and repetition 🙂
Building small zinc phosphate crystals
Q. I am zinc phosphating using an immersion system, soap,rinse,pretreatment,zinc phosphate, rinse sealer, then RO rinse. The problem I am having is I am getting a few large crystals growing with many voids in between them, I am getting 400 mg coating weight which is ok but I want more and smaller crystal growth to give me a better feel for not having adhesions issues in the field.
Todd DirkesProduction Manager - Longmont, Colorado, USA
2007
![]() |
A. Though it has been some years since I was involved with phosphating, I recall that one of the important factors in regulating the property you speak of is the type, and concentration of catalyst present in the solution. I don't know that this is something that the user controls directly. When I did process control analysis on these baths, the only things that I tested for were total and free acid, and iron. ![]() Dave Wichern Consultant - The Bronx, New York 2007 A. For a really nice zinc phosphate surface, consider using a calcium modified zinc phosphate from one of the advertisers at this site. I had great luck with it. James Watts- Navarre, Florida 2007 A. Dear Sir - New Delhi, INDIA 2007 |
Zinc Phosphate grain size problem
April 28, 2010Q. Dear friends.
I been having trouble with my zinc phosphate process
1.- degrease
2.- rinse
3.- rinse
4.- rinse
5.- acid (HCl)
6.- Phosphate
7.- rinse
The appearance of phosphate looks with big grains and some parts of the pieces with out phosphate, we can see the substrate.
Thanks for your comments I hope you can help us.
plating shop employee - Saltillo Coahuila Mexico
May 3, 2010
A. Dear Alexandro Ramirez,
For the bigger grain's causes
1) More sludge deposition on your phosphating bath
2) If you have the agitation tank, air pressure may be high or rpm of the stirrer is high
3) Or do the continuous filtration.
or may be the chemical is suitable for only making the Big Grains, better check with the chemical supplier.
Because for the powder coating or paint for the under coats , big grains are advisable for higher finishing thickness.
- Salem, Tanil Nadu, India
A. Hi Alexandro,
Without having seen how your operation is set up, I have to ask some questions and this may lead to a solution. I wonder why you have an HCl stage right before the phosphating stage. The drag-in from the HCl stage will contaminate the phosphating stage and lead to problems like an uneven coating and will make it difficult to control the bath. The extra acid will mess up your titrations.
If it is feasible for your operation, I would do the following. Switch the HCl stage with one of the three preceding rinse stages. Ideally, I would put the HCl stage in Stage 3; this way, you have a rinse between each chemical stage.
I would also ask your chemical supplier about a grain refiner and put it in the rinse stage prior to phosphating. This will decrease crystal size and help keep coating deposition uniform.
- Naperville, Illinois
May 7, 2010
April 22, 2011
Q. I am a job coater.My process flow is KOD-water rinsing(2 times)-surface conditioning-Phosphating-E.D.coating.
My customer's requirement is --Phosphating grain size less than 10 microns.
How to achieve it?
Parameters are as follows-
T.A.-20 to 22
F.A.-.8-1.1
Accelerator-3.1-3.5
Temp. 43 °C.
Plating shop employee - Nasik, Maharashtra, INDIA
Necessity of activation stage in spray pretreatment plant?
July 9, 2011I am a consultant for metal finishing line.
I am designing a spray treatment plant. The chemical supplier has suggested to add activation zone before passivation.
What is the necessity?
Sudir Apte
Consultant for metal finishing plants - Chipalun, Maharastra, India
July 12, 2011
Hi, Sudir.
There are so many finishing processes called 'passivation' that I must apologize that I don't know quite which one you are speaking of. Stainless steel is 'passivated' with nitric or citric acid . Zinc and zinc alloy platings are 'passivated' in chromate conversion processes. Steel can be 'passivated' through the application of an iron phosphate or zinc phosphate; but to make it even more confusing, sometimes the 'final rinse' after phosphatization is called the 'passivation' step for the phosphate coating :-)
Since you are speaking of a spraying plant, I'm thinking that the word 'passivation' means 'phosphatization' in this context? Usually an iron phosphate would not involve an 'activation' step, but a zinc phosphatization or tri-cationic phosphatization probably would. But basically, if the customer is purchasing proprietary chemistry to obtain the benefit of the supplier's chemical expertise, you have to follow their advice and have an activation stage if that is what their process involves.
Regards,
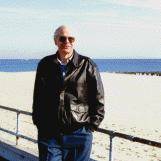
Ted Mooney, P.E.
Striving to live Aloha
(Ted can offer longterm or instant help)
finishing.com - Pine Beach, New Jersey
Q. How can I prepare a surface activation chemical and which raw materials are used to prepare it and in what quantity?
Thanks.
- Balasore, Orissa, India
March 13, 2013
A. Hi Dpak. If you prefer not to buy a proprietary activator, then Saravanan's information that it is a titanium based weak alkali should be a good basis for your in-house development efforts. Also, it is very easy today to do a search for expired patents and get some further ideas from them.
But nobody can openly publish the exact formulation of trade secret products. Good luck.
Regards,
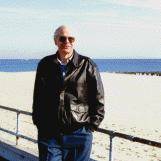
Ted Mooney, P.E.
Striving to live Aloha
(Ted can offer longterm or instant help)
finishing.com - Pine Beach, New Jersey
March 13, 2013
Zinc Phosphate Crystals Too Big for Wire Drawing
February 5, 2016Q. Dear Members,
I am using zinc phosphate on Carbon Wire Rods using the following parameters:
1) Acid cleaning (HCl at room temperature). Normally for 30 mins
2) Jet Wash
3) Rinse 1 (Ph above 3)
4) Rinse 2 (PH above 4)
5) Phosphate Bath ( 10-12 mins at 70-75 Degrees, TA 40-50, FA 7-8, TA/FA = 5-7), Accelerator 2-4
6) Rinse
7) borax
⇦ on
eBay
or
Amazon [affil link]
Problem is the phosphate bath starts forming large crystals too soon which hinders the drawing process as they break too quickly in drawing. Another indication of disturbed chemistry of the bath is that its color changes to BLACK.
I have the following questions:
1) How do I prevent the bath from making large crystal or turning black?
2) If large crystals are being formed, how do we bring the bath back to its original form making smaller fine crystals?
3) How do I check the Fe content of the phosphate bath? Is it similar to testing the Fe content of Acid?
Thanking the members in advance for their anticipated valued input.
- Karachi, Pakistan
A. You can test iron in the bath as the following: Iron points --
Reagents:
0.1N potassium permanganate
⇦ on
eBay or
Amazon [affil link] solution, sulfuric acid (50 %), Urea.
Procedure:
1. pipette
[pipettes on
eBay or
Amazon [affil link]
100 ml bath sample into 250 ml conical flask.
2. Add 2 ml sulfuric acid (50 %).
3. Add 2 g urea.
4. Stir the solution until the urea has dissolved and wait for approx. 3 min.
5. Titrate with 0.1 N potassium permanganate solution to a stable pink color (stable for at least 15 s).
Consumption in ml = iron points
Fe (II) = iron points x 0.5585 g/l
- Egypt , Cairo
A. Hello Mr Saud,
Crystals turning black can mean you have iron in your bath. You can easily know if there is with filter paper strips (qualitative grade, any brand) imbibed in 1% alcoholic orthophenanthroline. You let the papers dry, and dip them in the phosphate. If they turn reddish, you have iron in solution. Then, you must add accelerant until your phosphate bath is white in color and there is no reaction in the paper test strips.
You can measure as Mahmoud said the iron content, it must not rise from 0.3 g/l.
Then, you have EVERYTHING in the right level, and you still have the big-crystal-problem: I advise you talk with your vendor, there are many solutions but every one depends on the phosphate bath formulation. I cannot advise any of them without knowing the bath formula...
So, I hope you can solve your problem! Regards,
Daniel
TEL - N FERRARIS - Cañuelas, Buenos Aires, Argentina
March 29, 2016
August 11, 2016
Q. My process is surface conditioning/Phosphating
My customer's requirement is gray coating on Hero motorcycle fuel tanks
How to achieve it?
Parameters are as follows-
T.A. -- 18 to 20
F.A. -- 0.3-0.6
Accelerator -- 3-5
Temp. 41 °C
T.C -- 1-2
pH -- 9-11
But F.A is not controlled down to 0.0; even T.A is 20.3; and I get blue coating in Hero Splender+.
- Delhi, India
Q. Is it really required to check the alkalinity in activation process?
R Ramesh- Chennai, Tamil Nadu and India
August 20, 2016
Hi Ramesh. Saravanan said it was necessary in the first answer on this thread, and I'm not experienced enough to challenge him on it :-)
Please explain the full details of your situation whereby we might question his recommendation for your particular case. Thanks!
Regards,
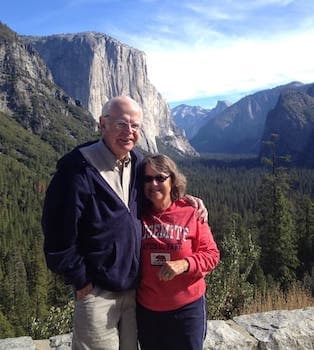
Ted Mooney, P.E. RET
Striving to live Aloha
(Ted can offer longterm or instant help)
finishing.com - Pine Beach, New Jersey
August 2016
Q. Dear sir,
I am working on preparation of zinc phosphating bath. Earlier problem I was getting was of low coating weight. Now coating weight has improved but grain size and grain distribution is not uniform. What are the possible ways to improve grain distribution with high coating weight.
Calligraphy - India
January 8, 2017
A. Hi Rahul. You had an original formulation and operating conditions which you haven't disclosed but the coating weight was too low ... then you modified the formulation and/or the operating conditions ... and those modifications, which you haven't disclosed, have improved the coating weight but the grain size is inconsistent?
We've appended your posting to one of many threads on the subject, which may offer food for thought, and the opportunity to ask for clarification. The basic problem is that there are countless books of hundreds of pages each about phosphatizing, and there are file cabinets full of expired patents about modifications; I hope someone is able to help you, but I doubt that they can help with your formulation and operating conditions until you describe them. Thanks and good luck!
Regards,
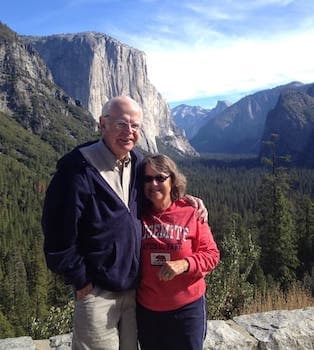
Ted Mooney, P.E. RET
Striving to live Aloha
(Ted can offer longterm or instant help)
finishing.com - Pine Beach, New Jersey
January 2017
December 13, 2017
A. Hi Hans,
First, you should see if there is any imperfection in your coating process. All hex chrome-free sealers have less resistance than hex chrome sealers, and they are more expensive and less resistant to contamination.
You should try to increase coating weight and try again, or try with another sealer. Chemetall has two other sealers that you can try, all more expensive than the first one.
My experience with non chromic sealers is not so good, so I would test those alternatives one by one in lab and try the best one.
Hi Jonathan!
Usually these red patches are cleaning issues. See if your pickling process is effective, try to improve it with concentration, temperature or agitation, add wetting agents and rinse with a lot of clean water.
If nothing is effective, try to load less weight in your racks, because it is difficult to clean between spires.
Best of luck to you, too!
Regards :)
TEL - N FERRARIS - Cañuelas, Buenos Aires, Argentina
Q. I am currently getting adhesion on 110k steel, but the grain size is unsatisfactory.
We have tried Keykote 62 from our supplier and it didn't work.
TA is at 9.5% (we had the same results from 5-8% as well).
Any recommendations to try refining grain size?
Thank you.
- ROUND ROCK, Texas
August 21, 2018
A. Hi Eric. What do you mean "it didn't work" ... do you mean the crystal size is still larger than you wish? Some postings on this thread from the estimable TSN Sankara suggest using a grain refiner to reduce crystal size, but I believe Keykote 62 is a zinc phosphate process rather than a grain refinement activator.
Regards,
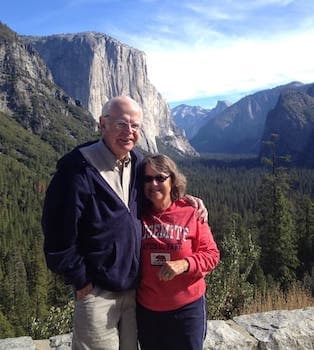
Ted Mooney, P.E. RET
Striving to live Aloha
(Ted can offer longterm or instant help)
finishing.com - Pine Beach, New Jersey
August 2018
Q. Keykote 62 is a grain refiner. There was no reduction in crystal size.
Eric Winters [returning]- ROUND ROCK, Texas
August 22, 2018
A. Hi Eric,
I don't have experience with Keykote 62, but I have some inquiries about your process:
1- You have a Keykote 36 (or other) process? Where and how did you use the refiner?
2- What is your cleaning (pretreatment) process?
3- 110K is K110? (AISI D2) Grain size depends on carbon and alloys content...
Hope we can help to solve this issue!
Best of luck!
TEL - N FERRARIS - Cañuelas, Buenos Aires, Argentina
August 25, 2018
Q. Here is our process:
Isoprep 172. We have tried running from 7% to 20%
Rinse.
Keykote 62. (refiner)
Keykote 36. Ran from 5% to 10%
Rinse.
At this point we are grasping at straws in attempts to resolve the issue. We ran a part and it came out perfect. Then a different part with the same process and it was horrid. The only difference in parts aside from shape is the machine they came off of and their heat lots.
- ROUND ROCK, Texas
A. Hi Eric!
I asked if the material was AISI D2 (K110) or if it is another steel, so I can get a closer idea of what is happening.
Grain size changes with surface preparation, rugosity before treatment, chemical composition of the substrate, microstructure of the substrate, grain refiners, TA/FA ratio, accelerator/iron content, and chemical composition of the phosphate bath (in this case a formulation from MacDermid, we know it is a -usually- nickel-accelerated zinc phosphate which works with dissolved iron).
With this type of phosphate bath, you can only trust in a grain refiner, but the surface of your part should be uniform, and the chemical composition and microstructure should vary within a range.
We do zinc phosphate to cold forged parts of low carbon steel (QT or Carburized) only, so I can't bring you any more data, but there are more grain refiners available and more phosphate technologies, so ask your vendor for a solution first, and see if you have any luck with this new data you exposed.
Best of luck!
TEL - N FERRARIS - Cañuelas, Buenos Aires, Argentina
August 28, 2018
Q. Hello, why are phosphate crystals coarse and how can we have a soft zinc phosphate?
Ahmad hashemi- qom saas iran
September 29, 2018
A. Hi Ahmad. Are you using a grain refining pre-dip as explained on this page which we've added your inquiry to? If you search the site for "coarse zinc phosphate" you'll find several more threads on the subject if the answer isn't on this page. Good luck.
Regards,
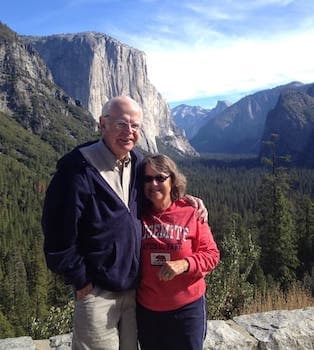
Ted Mooney, P.E. RET
Striving to live Aloha
(Ted can offer longterm or instant help)
finishing.com - Pine Beach, New Jersey
September 2018
A. Zinc phosphate relies on a precipitation reaction to form. As the acid in the solution reacts with the substrate the pH goes up and the zinc phosphate is no longer soluble. Keep in mind that cleaner is also caustic and will cause the crystals to precipitate on top of it if not rinsed properly.
The crystal refiner, usually titanium phosphate, provides nucleating sites which effect the crystal size.
The exposure to the substrate iron is self limiting based on contact with the phosphoric acid which is consumed at the interface. Alloying elements in the steel which may or may not react with the acid will play a profound part in crystal size.
Coil Coating - Brampton, Ontario, Canada
November 13, 2018
Zinc phosphate coating is covered with rust
February 14, 2019Q. Hello, all.
I posted on here mid-2018 about our phosphate line.
Since then my employer has overhauled the line and gotten a new chemical supplier (Dubois).
Our new line was running 80 ksi steel well for a few days.
Now our results are covered in a veneer of rust.
Our line is set up as follows:
Unikleen
Rinse
Rust remover
Rinse
Pretreatment
Phosphate
Rinse
Oil
TA 44.8
FA 7.4
Ratio 6.054
Iron 2.65%
Line operator - Round rock, Texas
A. Dear Mr. Eric, please go through the detailed answer given by Mr.Rodger Bridger. You will find the exact solution (Topic 10242)
Avinash Vidhate- Nashik, Mahatashtra, INDIA
February 17, 2019
A. Eric,
When in the process do you notice the rust? Is any seen between acid and phosphate, phosphate and oil, or is it all after the oil? Is this a manual line/do you have long dwell times between stage? Second what are the TA/FA/R/Fe parameters called out on the data sheet?
Follow up on these questions and I can try to get you back on track.
- Agawam, Massachusetts
February 18, 2019
Q. If I have pretreated a steel panel with a solution, how can I check if the metal surface is activated for powder coating ? What are the other options and methods other than SEM analysis ?
Jui Joglekar- Pune, Maharashtra, India
November 6, 2019
A. Hi Jui. Your question is very brief so I'm not sure if you are misunderstanding something or I am somewhat misunderstanding you... Although it's true that before electroplating you need 'the metal surface properly activated', in the case of powder coating you need the surface properly phosphated, and an activation process may be one step in that pretreatment, and you can often get a good understanding of how well the phosphating has been done just by looking at it or through salt spray testing. What type of phosphating are you doing, and how many steps? Thanks.
Regards,
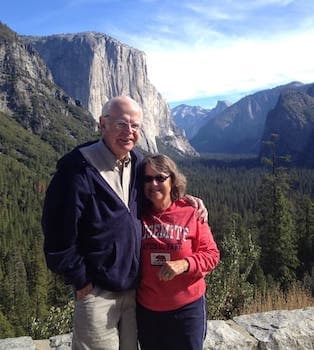
Ted Mooney, P.E. RET
Striving to live Aloha
(Ted can offer longterm or instant help)
finishing.com - Pine Beach, New Jersey
November 2019
⇦ Tip: Readers want to learn from your situation;
so some readers skip abstract questions.
Q.
Titanium based weak alkali chemical.
How to make this?
- greater noida, India
September 14, 2021
by Biestek & Weber
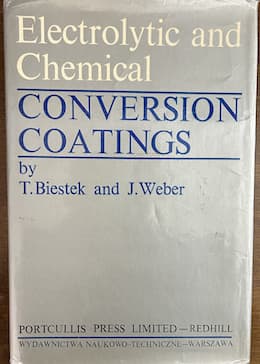
on Amazon
on AbeBooks
(affil link)
A. Hi Santosh. Finishing shops do not usually mix this chemical, they buy it from suppliers of the process chemistry.
You did not introduce yourself, but if you are a process supplier wanting to develop a line of surface activation chemistry rather than being a finishing shop employee, you might want to consult Biestek & Weber's "Electrolytic and Chemical Conversion Coatings" which discusses several different possibilities including 1% to 2% disodium phosphate with 0.1 to 0.5 mg of Ti per liter, with the Ti supplied as a titanium orthophosphate solution. Good luck!
Regards,
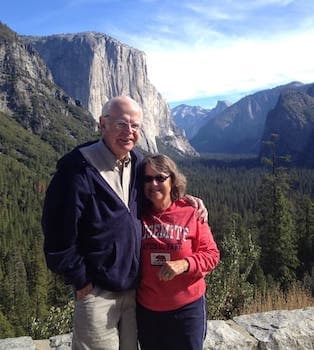
Ted Mooney, P.E. RET
Striving to live Aloha
(Ted can offer longterm or instant help)
finishing.com - Pine Beach, New Jersey
September 2021
Q. How to make phosphating solution ? Anyone tell me?
Santosh kumar Yadav [returning]- greater noida, India
September 27, 2021
[returning]
Q. How can I make cold phosphating solution?
Can you tell me please?
- greater noida, India
September 28, 2021
Can you tell me please how to make phosphating bath chemicals?
Santosh kumar Yadav [returning]Employee - greater noida, India
October 5, 2021
A. Hi cousin Santosh :-)
If you can pose a highly specific question which can be answered in a paragraph or so, I suspect that readers will enthusiastically & cheerfully do so. Meanwhile, there are numerous good books on phosphating chemistry, many of which are listed on this page if you want to look for them in a library, but they run 250 pages or so. There are countless patents and expired patents you can read on the subject at patents.google.com, and hundreds of technical articles you can read on the subject at scholar.google.com or elsewhere.
There are countless variations in phosphating chemistry, and they are complicated, and virtually all phosphating is done using trade secret proprietary chemistry anyway. So, unfortunately, the idea that anyone can & will tell you in the couple of paragraphs appropriate to a public forum how to formulate, operate, control, and troubleshoot phosphating solutions in general, plus cold phosphating solutions, plus titanium-enhanced phosphating solutions probably isn't realistic.
Best of luck!
Regards,
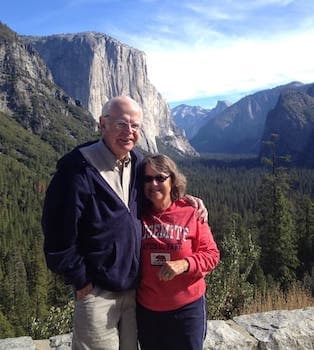
Ted Mooney, P.E. RET
Striving to live Aloha
(Ted can offer longterm or instant help)
finishing.com - Pine Beach, New Jersey
October 2021
Q. Dear Sirs,
Could you advise us (as separate process) activator formula for process of Zn phosphating of pipe's thread.
Thank you in advance,
Vadim.
- "New Jersey"
June 13, 2022
----
Closely related threads include:
- Topic 10242 "Zinc Phosphating Problems & Issues"
- Topic 874 "Zinc phosphate coatings to deter galvanic corrosion"
- Topic 51772 "What is Tri-cationic phosphating?"
Q, A, or Comment on THIS thread -or- Start a NEW Thread