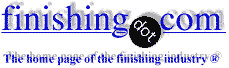
-----
Is powder coated aluminum or galvanized steel a good exterior finish?
Q. I'm about to have steel and aluminum parts powder coated. They are bases for outdoor, coin-operated telescopes. Since they are often installed near the ocean and should last 20 years or more, corrosion is a significant issue.
The head of the telescope is cast aluminum. I plan to have it phosphate coated and TGIC polyester powder coated, as I've heard this is the best approach for aluminum parts.
The welded base enclosure and various small parts are mild steel. I plan to have them galvanized and polyester powder coated. I'm not sure what type of galvanizing to spec for the base, though; it has a 4" pipe, 50" long, welded into a ~18" steel cube with a door. (I would be happy to provide drawings to anyone.)
Can these bases be spray galvanized before powder coating? I'm currently dealing with prototypes that have already been welded up, but should the production parts be galvanized before welding?
I would appreciate any advice on these issues.
I would also appreciate recommendations on galvanizing and powder coating shops in the San Francisco Bay Area.
Thanks, Wallace
- San Francisco, California, USA
2000
Ed. note: This RFQ is outdated, but technical replies are welcome, and readers are encouraged to post their own RFQs. But no public commercial suggestions please ( huh? why?).
A. You should also consider Enameling, or porcelain coating these things. It would be much more expensive, but the resulting coating would be WAY more likely to last your twenty years without failure.
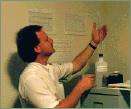
Jeff Watson
- Pearland, Texas
A. Aluminium alloys require hexavalent chromate conversion coating for max performance. Phosphating or phosphate-chromate (green chromate) are v. poor seconds. Zinc coating must be applied after welding; or it will be destroyed by the heat. Steel can be flame sprayed with zinc or even aluminium. The alternative is true hot dip galvanising of the welded assemblies.
With the latter you can get away with a LIGHT abrasive blast and powder coat, but again a hexavalent Cr process is best (not the one for Al!). 300 gm/sq. meter Zn should be more than adequate for longterm durability. If you want the paint finish to last the correct pretreat is essential.
- Croydon UK
Jeff - I'll look into the enameling. Thanks. Roger - Thank you very much for the information. I have a couple more questions:
Q. (1) What kind of vendor would offer hexavalent chromate coatings for aluminum and steel? I'm not familiar with those finishes. An electroplating shop?
I have now had our prototype steel parts hot-dip galvanized, and the surface finish leaves much to be desired. It is extremely uneven, with ~1/16" ridges of zinc in some places and large lumps of zinc in others. I suspect that hot dip is the most effective type of zinc coating for the welded steel base, since it would be difficult to spray its interior. The finish on these parts, however, was unacceptable. 300 gm/m^2 would have meant nothing to this shop; they do not have anything near that degree of control. Any tips on finding a hot dip vendor that would be more like what I'm looking for?
Thanks again, Wallace
- San Francisco, California
A. Plating or anodizing shops, including many of those listed in our Jobshop Directory, would offer 'chromate conversion coating' for aluminum parts, Wallace. It is not used directly on steel parts, it is applied on the zinc plating or galvanizing (you may have misunderstood what Mr. Bridger was saying on that subject).
Although zinc electroplating by itself would not stand up to this service, zinc electroplating followed by chromate conversion coating and powder coating might do well. And the smoothness/brightness of the finish would be far better than is possible from galvanizing. Good luck.
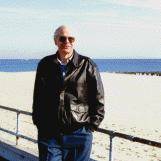
Ted Mooney, P.E.
Striving to live Aloha
(Ted can offer longterm or instant help)
finishing.com - Pine Beach, New Jersey
A. Kynar gives 20 year warranty protection on Aluminum. Electrocoats will fade and change color.
Do it with Kynar
- Flint, Michigan USA
March 4, 2008
A. Yes, Kynar sounds like a good possibility, Bob -- I know it's widely used on aluminum. Electrocoats can be an important base coat if there is any possibility of pin holes or lack of coverage in the top coat.
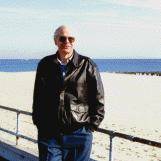
Ted Mooney, P.E.
Striving to live Aloha
(Ted can offer longterm or instant help)
finishing.com - Pine Beach, New Jersey
Update June 2017: My patio set of expanded steel which was phosphatized, electrocoated, and powder coated is going strong after 17 years of being outdoors 365 days on our salt water lagoon deck, then a week submerged under the saltwater of Superstorm Sandy, and 3 more years since :-)
A. ASTM D6386 is a standard that addresses preparing galvanizing for painting. It is applicable to powder coating except that it does not address the pre-baking for out-gassing. There are concerns about chromate quench causing poor adhesion. I am not sure how this relates to your chromate conversion coating but this document references a phosphate pretreatment for surface preparation. There has been recent movement by the EPA on hexavalent chromium. Do not know if this would enter into your decision?
Tom Neal- Baltimore, Maryland
July 9, 2011
Q. I am detailing an exterior steel structure for a building and have labeled the exterior steel to be hot dipped galvanized and powder coated white. The intent of this note was to achieve the protective properties that galvanizing offers with the low maintenance of the powder coating. After further exploration of the web I found your home page and FAQ concerning the adhesion problems of the above. Is there another finishing process that can achieve the intent and/or is the powder coated galvanized steel finish the best solution for the exposed steel?
Raymundo Vela Jr- Austin, Texas
2002
A. Hot dipped galvanized steel uses the principle of galvanic corrosion as the protection of the mild steel. That is the zinc layer corrodes instead of the steel substrate. This will only happen with air and moisture from my understanding. Powder coat is an organic substance, as is most paints and is porous, thus allowing the moisture to travel through to the zinc layer. This can be deterred by using a chromate or zinc phosphate treatment on the zinc prior to powdercoating. As for adhesion , this can be achieved by either light sandblasting to provide a mechanical key, or by using acid etching for a chemical key. Powder should perform as well as any other paint, but the thicker the coat the longer it will take for corrosion to take place at the zinc layer. Perhaps using an epoxy based primer underneath the polyester powder top coat will help achieve a greater film build and subsequently a greater barrier. Your comment re. low maintenance of powder may be slightly off center. Whilst it does not require constant repainting, it does require regular cleaning to remove oxides and maintain its glossy appearance. Perhaps using a matte or low sheen finish may slow down the times it requires cleaning. You wouldn't leave your car unwashed for years without some form of maintenance would you?
Michael Lind- Queensland, Australia
Thanks, Michael. Although I wouldn't leave my car unwashed for years, if I had towers for high-voltage wires I would leave them unwashed for decades; and if they were properly galvanized, they'd probably be okay for 50 or 75 years, despite the lack of attention. Sometimes maintenance of surfaces is do-able and sometimes not :-)
Raymundo might wish to further pursue this issue of paint adhesion on galvanizing via ASTM D6386, "Standard Practice for Preparation of Zinc (Hot-Dip Galvanized) Coated Iron and Steel Product and Hardware Surfaces for Painting" because although galvanizing can last 75 years in remote areas, where de-icing salt, acid rain, and lawn fertilizer may get on it, it will not be nearly as durable.
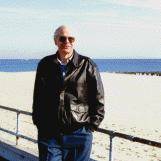
Ted Mooney, P.E.
Striving to live Aloha
(Ted can offer longterm or instant help)
finishing.com - Pine Beach, New Jersey
for Engineers, Shops, Specifiers
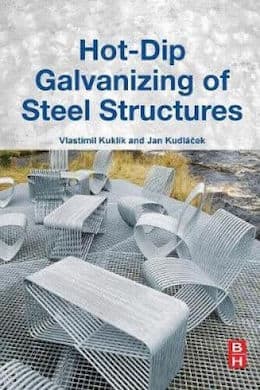
avail from eBay, AbeBooks, or Amazon
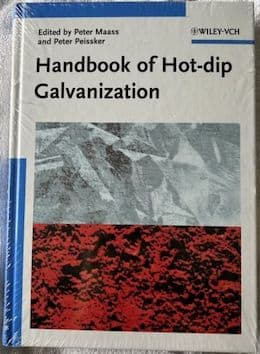
avail from eBay, AbeBooks, or Amazon
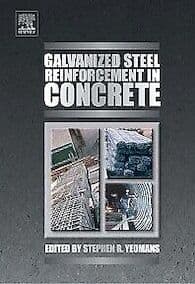
avail from eBay, AbeBooks, or Amazon
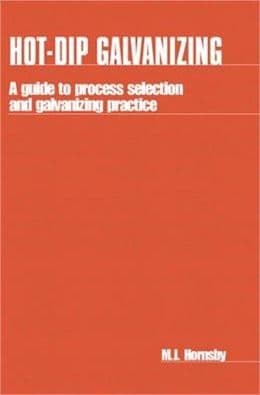
avail from eBay, AbeBooks, or Amazon
avail from Amazon
"User's Guide to Hot Dip Galvanizing for Corrosion Protection in Atmospheric Service" by NACE (1997 only rarely avail.)
avail from AbeBooks, or Amazon
(as an Amazon Associate & eBay Partner, we earn from qualifying purchases)
Q. If hot dipped galvanized steel is "squelched", what does that mean?
John GillenConsulting Engineers - Mount Holly, New Jersey
2007
A. Hi, John.
I've personally never heard that phrase and will take a wild guess that it is a mis-speak based on someone's faulty memory of the word "quenched". But if you can put it into a tighter context, there may be a better answer. Thanks.
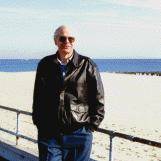
Ted Mooney, P.E.
Striving to live Aloha
(Ted can offer longterm or instant help)
finishing.com - Pine Beach, New Jersey
Q. Hi. I'm a small powder coating company about to start coating a lot of galvanized steel. I've done little bits, but not very good ("pinholeing" or just not adhering) I don't want to lose the work so any help or advice would be appreciated
Graham Mcilhaggapowder coater - Sheffield, England
August 2, 2010
A. Hi, cousin Graham.
At the least, you'll need to phosphatize the galvanized steel before attempting to powder coat it. Are you pretreating to the spec that was mentioned, and still having adhesion issues, or you haven't had a chance to consult that spec yet? Have you been able to find that book about duplex coatings by any chance? If not, what process are you presently doing for pretreatment that is resulting in poor adhesion and pinholing? What kind of powder are you applying?
Good industrial quality coating is quite involved, and it simply isn't possible to condense it all down to a one-paragraph answer :-)
But if you can give us the details of what you are doing, maybe someone can spot the weakest link. Thanks!
Regards,
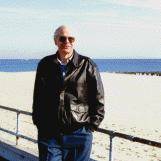
Ted Mooney, P.E.
Striving to live Aloha
(Ted can offer longterm or instant help)
finishing.com - Pine Beach, New Jersey
Q. Dear Sir,
I would like to know if Pure Polyester powder is applied on MS, then how much temperature can it withstand in day to day use?
Regards,
- Ahmedabad, India
March 2, 2012
Hi. Sanjay.
Sorry, I don't know the answer myself. Please try your best to describe the actual exposure situation, and what motivates the question. We seem to find that it intimidates readers against attempting to answer if they feel they'll have have to think through and include a dozen "ifs, ands, & buts" that probably don't apply to your situation anyway :-)
Regards,
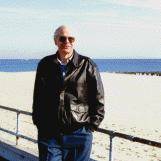
Ted Mooney, P.E.
Striving to live Aloha
(Ted can offer longterm or instant help)
finishing.com - Pine Beach, New Jersey
What non-phosphate pretreatment can we do on galvanized wire?
Q. Hi,
We are coating thermoplastics over pregalvanized substrate of wire fences. It needs no pretreatment and has superior performance. We have to coat polyester on same fences too. I am looking for an alternative way to 9-stage zinc phosphate process. Is there any new process with simple steps and without waste?
- Istanbul, Turkey
May 30, 2015
A. Hi Ates. Most vendors of phosphate pretreatment processes also offer proprietary non-phosphate pretreatments, so talk to whoever is supplying you with zinc phosphate and they'll probably process some samples for you. However, 3 cautions:
1. Thermoplastics on wire offer a "shrinkwrap" effect, whereas polyester thermosets won't -- so your principal issue is likely to be adhesion to the galvanizing rather than corrosion resistance. So whatever non-phosphate you use probably must be able to etch the galvanizing.
2. Unless the proprietary non-phosphate manufacturer can show you fencing that was manufactured 20 years ago by this process and has been in service you need to be very skeptical about claims of such life.
3. opinion! Manufacturing powder coated and galvanized steel without phosphatizing, which then doesn't last two or three seasons, when we already know how to make it last 20 years with zinc phosphating would hardly be reducing waste -- rather, it would be a sustainability travesty.
Things may be different in Turkey, but here in the USA it's hard to find any steel outdoor goods that last a few years anymore, whereas a 15-20 year life was a commonplace just a few years ago. The tons of steel repeatedly mined, smelted, fabricated, finished, packaged, transported, sold, and landfilled -- not the ounces of phosphate -- are the waste we should be concerning ourselves with :-)
Regards,
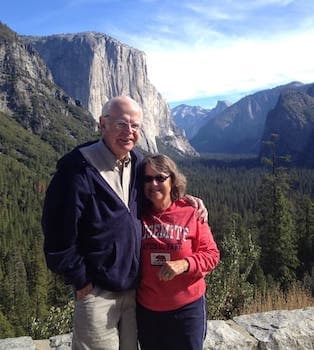
Ted Mooney, P.E. RET
Striving to live Aloha
(Ted can offer longterm or instant help)
finishing.com - Pine Beach, New Jersey

Q, A, or Comment on THIS thread -or- Start a NEW Thread