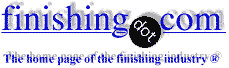
-----
Zinc Phosphating Problems & Solutions
Q. Hi guys, I'm currently working in Die-Casting Company. After casting, our products undergo phosphate treatment process. Our current problem is the white stain after phosphate. This white stain is still visible after ED - Coating. ⇐ answer?
Elmerson Montiano- Calamba Laguna
August 6, 2024
Q. 1. Rusting appearance after zinc phosphating.
2. White patches, un coated visible after Zinc phosphating
- Telangana, India
August 5, 2025
Tip: This forum was created to help build camaraderie through sharing tips, opinions, pics & personalities.
The operator & those readers who want that might not engage with anonymous posters.
Multiple threads merged: please forgive chronology errors and repetition 🙂
Q. Dear Sir,
Problem is that I have trouble in my zinc phosphate bath; process sequence as follows --
1 cleaner, temperature 50-75 °C
2 water rinse
3 water rinse
4 zinc phosphate with catalyst, temperature 55 °C
5 water rinse
After above process I get bad result: phosphating solution colour turns brownish, result like uneven layer of phosphate. What is your suggestion for how I can get good results? If we make up new one, after two loads the results turn bad. Please tell me about the problem, remedy, possible causes, thank you.
- Karachi, Pakistan
2002
A. Hi Shaikh,
You need to give more details about your operation before a precise answer can be given. Specifically, is this system spray or immersion? What are the contact times in the cleaner and phosphating stages? What exactly do you mean by a bad result?
From what you have written, I can do a little troubleshooting. You say that the phosphate coating comes out uneven. Are you getting adequate cleaning in Stage 1? Is the work coming out water-break-free? The metal surface must be free of all oils and contaminants before a homogenous phosphate coating can be deposited. You also said that the phosphating bath was turning brown. Is something being carried over from Stage 1?
Are you overflowing the rinses in Stages 2 and 3 sufficiently? Poor rinsing will make the problem of carry-over even worse. Remember, water is your cheapest chemical!
Is the phosphating bath made up properly? Are you breaking in a new bath by dissolving some iron in it? Are your total acid and free acid numbers in the proper ratio? Your chemical supplier will be able to tell you the proper ratio for your application. An out-of-balance phosphating bath will produce poor coatings.
You say that your phosphate solution has a catalyst; I assume this means accelerator. Is the accelerator present at the proper concentration? Not having the accelerator at the right concentration can also have a detrimental effect on the coating.
Would it be possible to convert the rinse in Stage 3 into an activation stage? Your chemical supplier should be able to provide you with a Ti activator, which will help in the formation of a uniform phosphate coating.
I have presented a lot of "what-ifs" here. Without knowing more about your system, it will not be possible to pinpoint the problem.
- Naperville, Illinois
A. Hi,
From your scarce info I would say you are running a dip bath. The catalyst is probably sodium nitrite.
1. The brown colour is due to the build up of ferrous iron.
2. I would say that the temperature needs to be 60+ °C
3. You are either putting too much steel into the bath or you are not adding enough accelerator. If it is a liquid add 500 mls per load per 1000 liters tank capacity for the first few loads. Control with starch iodide test papers.
4. The low temp will favour the build up of ferrous iron hence higher additions of nitrite will be required. The new bath will work at first until ferrous iron builds up.
- Croydon, UK
A. Shaikh,
May I suggest after your 2 rinses from the cleaner, dip your parts into phosphoric acid. This will pickle the metal, remove any unwanted oxides from your metal, and make the part more susceptible for the phosphate (which is really a glorified form of phosphoric acid). After that, rinse first in cold water then hot water. Next, after the hot rinse use a titanium activator to get more uniform coverage on your part. Next would be the zinc phosphate (165 °F): use 1 pint of sodium nitrite for every 400 gal. to remove unwanted iron (this is important... you want this bath to be free of iron, where you may be picking up the brown stains).
Then rinse in cold water, and last, rinse in a solution of chromic and phosphoric acid (160 °F). This last rinse serves 3 functions:
1. dries part off quickly
2. prevents short term corrosion
3. leaves the surface slightly acidic which is the best condition for paint or any other organic coating to adhere to.
- Nanticoke, Pennsylvania
2003
A. Well, how I can understand your process have a problem on the final stage. The most of times the final stage it's occupied a bath called "sealing" that have a chrome solution and other stage (rinsing) to eliminate the excess of chrome.
The first two degreasings steps are made it with NaOH to clean the surface and eliminate the scale and rusting of steels.
If you have a final stage with this compound you can have a detrimental phosphating coating because NaOH to undo the crystals and the paint not have a good adhesion.
Check your final stage.
- Santiago de Querétaro, Querétaro, Mèxico
2007
Granules, streaks, and poor adhesion in zinc phosphating
Q. Dear everybody,
I am working for automaker company. We have spray line (5-stage) for pretreatment of cars:
2 stages of degreasing, 1 stage rinsing, 1 stage zinc phosphating, 1 stage passivation+rinsing.
Unfortunately our line is very compact and usually some liquid from each stage overflows to other stage (specially degreasing to rinsing and rinsing to phosphating).
At the final stage our contractor uses NaOH for passivation the surface. We have granules on our cars and a streaky surface.
We tested our painting on it (cross cut test for adhesion) and failed.
Could you please guide me about troubleshooting of zinc phosphating line and guide me about suitable source (book, article, document) to see good zinc phosphated surface?
Best regards
- Tehran, Iran
2007
A. Hello, Nader. You have already identified what the principal problem is (carryover from one tank to another), and you know that it must be fixed.
Just one person's opinion: Don't talk yourself into wasting time on further "investigation" rather than confronting this difficult problem :-)
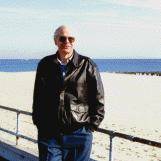
Ted Mooney, P.E.
Striving to live Aloha
(Ted can offer longterm or instant help)
finishing.com - Pine Beach, New Jersey
A. If bath solution shows brown color, it means your cleaning and rinsing is not proper. To avoid this, improve the rinsing and cleaning processes.
Also check that if you are adding chemical in old bath then check the pointage of phosphate and iron contamination.
- Mumbai, Maharastra, India
November 25, 2012
A. HI, CHECK THE PHOSPHATE LAYER WITH A SOLUTION OF 20 G/L SODIUM CHLORIDE AND 7.5 G/L POTASSIUM FERROCYANIDE
⇦ on
eBay
or
Amazon [affil link]
.
DIP A PIECE OF FILTER PAPER INTO THE SOLUTION AND AFTER DRAINING EXCESS LIQUID , PUT IT ON THE PHOSPHATED PART. AND AFTER 20 MINUTES IF YOU OBSERVE BLUE SPOTS ON THE PAPER LOOK FOR PROPER SUPPLIER.
BEST REGARDS,
REZA.
- TEHRAN ISLAMIC REPUBLIC OF IRAN
November 17, 2013
Phosphated metal turns red in molding process
Q. Why does the phosphated metal gets a reddish colour on its surface when it is molded?
Thoufiq P A- Mysore, India
February 21, 2014
A. Thougiq,
We had the same problem years ago and weren't able to find a solution. The only thing we could think of was there was excess water in the rubber and during the molding process, the water flashed into steam and rusted the metal. There weren't any blemishes or any indication of water in the rubber after molding, except the redness.
- Kansas City, Missouri USA
What is this Zinc Phosphate Coating
Q. Hello my name is Cody and I work for an automotive supplier. We have recently had some testing performed on a sample part and we cannot figure out what type of coating this part has. The testing method used was an X-ray energy dispersion Spectroscopy for samples in Scanning Electron Microscope. The test results showed that the main elements in the coating were oxygen, zinc, and phosphorus. The problem is the part doesn't look like it has a coating. It is a dull grey with a smooth finish and it does not have the typical zinc phosphate appearance. The part looks like it was not coated using a bulk/barrel operation. This may asking too much but we are looking for a Specification that matches the coating. We are looking for a Ford, GM, or Chrysler Specification. We have not found one yet that has the resultant surface finish. ⇐ answer?
Cody Belknap- Grand Rapids
March 18, 2014
Acid won't reliably rinse out of stitch welded area of zinc phosphated parts
Q. Hi
We are having a problem with acid being trapped in the 7 stage zinc phosphate process. In some cases these steel plates are laser cut and stitch welded together; in the areas where the plates are pressed up against each other but not welded, the acid is not washed away completely (counter-flow rinse tanks with overflow is being used) ... and then there is some corrosion due to the trapped acid even as far down the line as complete powder-coated fabrications.
Adding another rinse bath is not really an option for us, is there some way to enhance or improve the rinsing? Is raising the rinse bath's temperature an option?
⇐ answer?
- Johannesburg, Gauteng, South Africa
June 11, 2014
Q. Hi,
I have many problems in my phosphating unit. I have immersion bath at temperature 70.
1- a lot of sludge formed very quickly,
2- sometimes a white color presented above wire immediately,
3- wire turned to brown color after two days storing,
4- very low corrosion resistance,
5- sometimes a blue color observed after only one hour from phosphating.
- cairo -Egypt
October 7, 2015
A. 1: -maybe you are adding excess of Accelerator in the Phosphating bath.
2: -This might be excess of sludge on the wire rods or you are maintaining the Lime/Borax temp on a lower side then specified.
3&4: -This might be acidic atmosphere/ because of detrimental Phosphate coating you're observing rustiness on the wire rods.
5: -I don't exactly get what you mean blue colour observed on wire rod after phosphating, kindly specify this observation found on any particular grade/ found in all grades.
Regards
Pravin H.
- MUMBAI MAHARASHTRA, India
March 25, 2021
Rust prevention after leak testing at welding market area
Q. Dear friends, we are coating some leak-tested components but we are facing rust problem each time. We have dip PT process as follows
Emulsion cleaner
alkaline degreaser 2 stages
Water rinses 2 stages
Activation
Zinc Phosphate
Water rinse
Dm water
Ced
Uf rinses 2 stages
Dm spray
We want to remove rust and burnt oil residue from components. Is there any chemical need to add or any new stage to add?
Now we are manually pre cleaning and de-rusting components using acidic agents; problem is minimised but not completely solved.
Please help me.
I am engineer and working in paint shop. - Pune, Maharashtra, India.
August 12, 2017
A. Hi Vishal. Is there any chance of abrasive blasting or tumbling? Chemically removing scale is difficult, and chemically removing burned-on oil can be next to impossible. But if you were able to blast these parts, it seems to me that the rest of your process is very robust.
Regards,
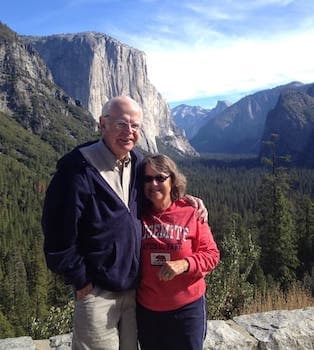
Ted Mooney, P.E. RET
Striving to live Aloha
(Ted can offer longterm or instant help)
finishing.com - Pine Beach, New Jersey
Q. Hello everyone, I work on a phosphate line with the following process:
1/2 - Alkaline Drawing (85 ~ 95 °C)
3/4/5 - Rinsing with running water
6 - Stripping with hydrochloric acid
7/8 - Rinsing under running water
9 - Neutralizer (calcium carbonate)
10 - Refiner (titanium salt)
11 - Phosphate (Bonderite MZN 880) (75 ~ 80 °C)
12/13/14 - Rinse Water D.I
15 - Passivator (active silane).
I usually work with TA = 20 ~ 25 ml and FA = 2 ~ 3.5 ml, accelerator titration (sodium nitrite) between 1.0 and 0 and iron content between 0 and 4.0 points.
I still have some problems, such as stains on the phosphate layer, as if the layer looked open, yellowing and phosphate powder. I would like to understand why, since I have control of the bath.
Today I am working with 3 iron points, the phosphatizing bath is dark brown / black, I believe because of the high iron content.
Please, even taking control of the bath I have problems.
Atte;
- Ribeiráo Preto, Sáo Paulo, Brazil
February 20, 2018
A. Mateus,
At a glance this looks like you have some sludge depositing on the work while it is being processed. This sounds like an older bath from your appearance description; have you been de-sludging regularly? It is an unavoidable by-product of the reaction that you need to take care of to keep the bath running optimally.
Sludge gets kicked up from the bottom when you add work to the tank and it can stick to parts, causing powdery coating in random spots, thus resembling stains or blotches.
- Indian Orchard, Massachusetts USA
Q. Hello everybody, it's me again. I am still having problems while the spots appear to be flawed in the phosphate layer. I have been working with iron content between 1.5 and 2.5 (last measurement performed) it seemed that the stains were a little more present. Here are photos on my problem:
Another point to be raised is that these pieces even having these faults have a layer between 3.5 and 6 g / m2. Being that client requires me to only layers between 2.0 and 5.0 g / m2.
While the mud, I clean the tank monthly, always leaving a little mud in the bottom not to rejuvenate it completely.
In addition, I would like to know if there is any text or url to download text that speaks about the phosphatization process, reporting the care to be taken, as well as common problems and causes and how to repair them.
Kind regards.
- Ribeiráo Preto, Sáo Paulo, Brazil
February 21, 2018
A. Hi Mateus,
Streaking on your phosphated panel is due to:
Poor rinsing after HCl pickling
Dip time in Ti activator should be 2 mins
Accelerator titration should be 2 to 4
Increase nitrite
Temperature is fine and TA is fair. Increase immersion time
Hope this helps.
- India,gujarat
Q. After zinc coating the colour of component was found silver grey. Is it due to some traces of aluminium or any other thing. Please guide me.
Abdul Mateen- rawalpindi Pakistan
March 31, 2018
? Hi Abdul. Are your parts the same 'silver grey' as the photos from Mateus? Please mail some photos to and tell us what you find objectionable. Are your parts made of aluminum or of steel?
Regards,
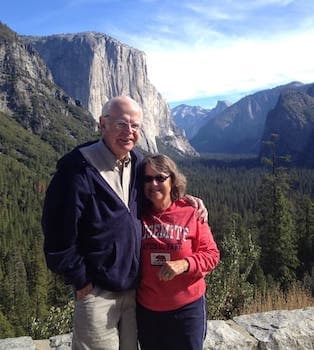
Ted Mooney, P.E. RET
Striving to live Aloha
(Ted can offer longterm or instant help)
finishing.com - Pine Beach, New Jersey
Q. Hello everybody, very quick question. I'm having some problems with my zinc phosphate. Parts are coming out with some yellow stains? Could it be the material? If so what can I do to get good results? Parts go into cleaner, acid and then phosphate
Matt Dempsey- Houston Texas
April 22, 2020
A. Typically a yellow appearance after surface finishing is a result of iron contamination. Iron is required for this process to be properly "seasoned", but an excess can prematurely corrode causing the staining you see. Using the following titration you can check for that level. At above 11.0 "points" a decant is typically necessary:
1. Remove 10 ml sample of operating solution
2. Add 5 - 10 drops of 50% Sulfuric Acid
3. Titrate with 0.2N potassium permanganate
⇦ on
eBay or
Amazon [affil link] (KMnO4)
4. The change to a pink/purple color is the end point
Since the pink color will fade, titrate until the color persists.
5. Number of ml of 0.2N Potassium Permanganate = "Points Iron"
- Cleveland Ohio
Q. Hey guys! I'm currently working for a magnet manufacturing company. Before epoxy coating, our magnets undergo zinc phosphate treatment process. We are currently encountering jig marks on the surface of our magnets after the pretreatment process. From our initial investigation, the embossed marks on the surface of the magnets are the points where there are magnet-to-jig contact (we place our magnets into jigs before dipping them in tanks for pretreatment process). What could be the possible reason for this occurrence?
- Binan City, Laguna, Philippines
February 4, 2021
A. Hi Vea. Unfortunately I haven't really learned much from that photo :-(
But most finishing processes, including phosphating and its associated cleaning and activation, do not have magical powers to penetrate underneath the rack contact points. At best we can minimize rack marks, we cannot eliminate them. You may need to process in barrels, find a different racking point, move the part on the rack mid-process, or whatever.
Luck & Regards,
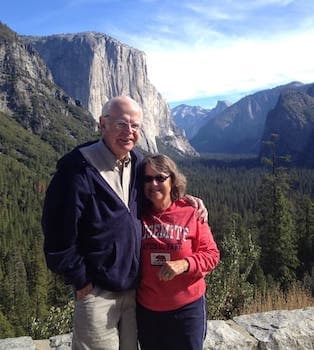
Ted Mooney, P.E. RET
Striving to live Aloha
(Ted can offer longterm or instant help)
finishing.com - Pine Beach, New Jersey
⇦ Tip: Readers want to learn from your situation;
so some readers skip abstract questions.
Q. We are observing crater issue in zinc phosphate steel sheet, kindly revert with solution.
Mohd JaidSr. Technical executive - Alwar
June 17, 2021
A. Hi Mohd. Besides this thread, topic 10242 and topic 50266 cover Q&A's about zinc phosphating defects ... and we have other threads, as well :-)
Please send photographs of the defect to mooney at finishing.com for posting here, if you can, and give us as much as you can about the operational parameters, and hopefully you'll get useful help.
Luck & Regards,
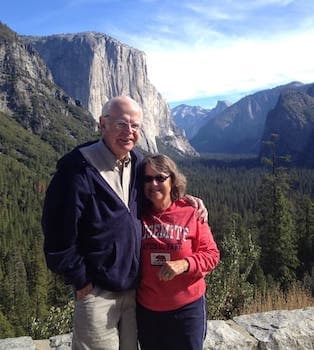
Ted Mooney, P.E. RET
Striving to live Aloha
(Ted can offer longterm or instant help)
finishing.com - Pine Beach, New Jersey
Q. I work in an automotive company and we are facing a problem after pre-treatment. The steel sheet turns yellow. This happens with several non-coated steel sheets for body parts to different extents. We don't know if the steel sheets have problems or the problem is with the Pt. We are looking for two things:
1. A standard for the extent of yellowness telling us the limits,
2. The reason for this problem. It would be nice of you to help me with this as I am new and this seems complicated.
With many thanks.
New Employee - Shalr, Iran
September 23, 2021
A. Hi Sahar. I Brown suggests below that iron contamination may be responsible for this. Please try to follow his/her instruction. But if it doesn't seem to be your situation, then send us photos for posting here and a description of your pretreatment sequence. Thanks.
Luck & Regards,
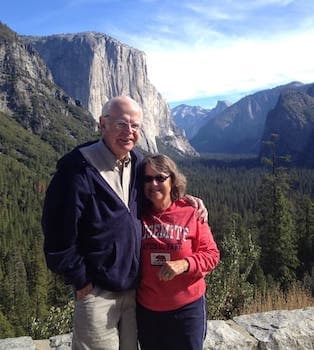
Ted Mooney, P.E. RET
Striving to live Aloha
(Ted can offer longterm or instant help)
finishing.com - Pine Beach, New Jersey
Q. Working as Engineer in the coating department of a sheet metal fabricator. We noticed that after completion of phosphate conversion coating all the surface have nonuniform patchy layer; but if we skip the De-rusting (phosphoric acid based) process the surface resulting is awesome grey phosphate layer. Means, is that because of De-Rusting?
Dayanidhi Jeeva- Coimbatore, Tamilnadu, India
February 16, 2022
A. Hi Dayanidhi. I think it means that you are not doing the de-rusting properly or in the correct sequence. If you have a serious rust problem on the parts your sequence should probably be: de-rust (or maybe abrasive blast), alkaline clean, MILD activation, phosphating. If you are doing alkaline clean, STRONG derust, phosphating I think patchy phosphating could result.
Please try to flesh out your inquiry with some details.
Luck & Regards,
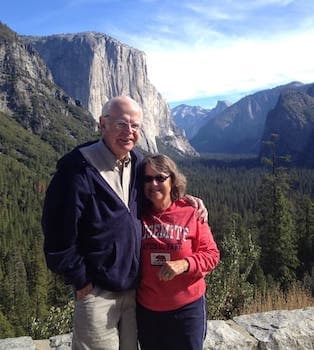
Ted Mooney, P.E. RET
Striving to live Aloha
(Ted can offer longterm or instant help)
finishing.com - Pine Beach, New Jersey
Q. Yellow staining?
I work in paint shop of an automobile manufacturer.
I am facing a problem of yellow staining on GA-sheet car body.
car body's metal sheet is galvanized coated (GA to be specified) and after zinc phosphating process the sheet gets too much yellow. (pic attached). it feels like issue is caused by the GA sheet.
CRS/SPCC parts are okay, they don't tend to get yellow after phosphating process.
I couldn't find the root cause of this issue. Please support me in this regard.
what could be the reason of this?
How can it be prevented?
how to solve this issue?
Line Data:
Degreaser: Free Alkali = 8 to 12 ml immersion for 3 min @ 55 °C temperature of degreasing solution
Surface conditioning: Zn concentration 3 to 6 ml immersion for 90 sec @ room temperature.
zinc Phosphate:
Free Acid = 0.8 to 1.2 ml
Total Acid = 24 to 28 ml
accelerator = 2.8 to 3.2 ml
immersion for 3 min @ 45 °C temperature of phosphating solution
⇐ answer?
- Gujranwala, Pakistan
May 27, 2022
Q, A, or Comment on THIS thread -or- Start a NEW Thread