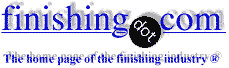
-----
Zinc Plating of 12L14 Leaded Steel
Q. What can I do to add some corrosion resistance to my parts made from leaded steel? I've read about the issues surrounding zinc plating and I'm not willing to gamble with my parts. I need something economical that's a sure thing. The parts are roughly 1.25" long, 1.125" diameter and will be exposed to fresh water, although not submersed.
Paul Somlo- GREELEY [Colorado]
September 22, 2024
A. Hi Paul.
If paint is acceptable, you can phosphatize and paint them. But if you need a metallic coating, zinc plating is the most common plating, the most economical, one of the simplest, and one of the few that offers cathodic protection to steel.
Things can go wrong no matter what you choose to do, but if you identify what the parts are made of and send them to a reputable plating shop with the ability to plate them, it's not a high risk situation.
Luck & Regards,
Ted Mooney, P.E. RET
Striving to live Aloha
(Ted can offer longterm or instant help)
finishing.com - Pine Beach, New Jersey
Multiple threads merged: please forgive chronology errors and repetition 🙂
Q. I am an engineer at Mallory Ignition/Erson Cams. We produce race/performance automotive components. One of our popular line of products is our adjustable fuel pressure regulators. We use 12L14 steel to make the seat and the plunger (which slides on the seat). To reduce wear, we case harden both components. Then, to reduce corrosion, we send the parts out for Type II zinc plating with gold/yellow dichromate. The problem is, when you take a handful of these parts out of the box, you will find that your hands will have "glitter" on them as if small pieces of the plating is coming off the parts. Sometimes you can even see blistering of the plating. In these cases, you can scratch the plating off with your fingernail. Those small pieces of plating cause problems when they get into the fuel injectors. I have called both of the platers we have tried and got no real concrete answers. Is there a different type of plating that I should use or are the platers just doing something wrong?
I would really appreciate any help.
Mallory Ignition/Erson Cams - Carson City, Nevada, USA
2002
A. Leaded materials in sulfuric forms lead sulphate which will smut up the part and result in adhesion failure whether it's lead in steel, brass or a tin-lead soldered joint! Fluoboric acid may not be as common as sulfuric, hydrochloric or nitric, but it's well known to anyone whose ever dug below the surface of a plating adhesion problem on lead bearing materials!
The other problem with hardened steel is that exposure to any acid may result in a carbon smut on the surface. There is nothing more difficult to remove chemically than carbon smut. Therefore, we often use mechanical preparation such as glass bead blasting only and then directly into the plating bath.

Milt Stevenson, Jr.
Plating shop technical manager - Syracuse, New York
Multiple threads merged: please forgive chronology errors and repetition 🙂
Best Malleable (Non-Flaking) Finish for 12L14
Q. We have a 1" diameter cylindrical housing made of 12L14 and currently plated with zinc/clear chromate. The cylinder has plastic inserts set into an internal step on each end that are retained by a slight rolling of the housing ends after installation. We have an ongoing issue with plating flaking during this rolling operation that can cause electrical shorts if introduced into the assembly. We are looking for the best finishing option for the 12L14 that can give us equivalent (or better) corrosion resistance of 12 hour salt spray per
ASTM B633, but must be extremely malleable to eliminate any possibility of flaking.
Any and all options are welcomed for consideration, thanks.
- Houston, Texas
2002
A. Zinc would not normally flake if I understood your process correctly. I feel that the problem is in the plating. You have a leaded steel and the preprocess should have a fluoboric acid dip to remove surface lead. Without that, you will have decent adhesion for many purposes, but not physical abuse. Another alternative is to go to a non free cutting steel. Machinists will whine, but proper inserts, coolants,feeds and speeds and you can nearly maintain current production levels
James Watts- Navarre, Florida
Q. After receiving advice on this forum (thank you) about the plating of 12L14, I asked our plater if they were using a fluoboric acid dip prior to plating. They told me they used a sulfuric acid dip and have never heard of fluoboric acid. Will the sulfuric acid work as well as the fluoboric acid on leaded steel? If so, do we have a different problem? Could the problem be that the part is case hardened? Does the high concentration of carbon near the surface prevent the zinc from sticking to the part?
Robb McMackinMr. Gasket - Carson City, Nevada
A. Sulfuric acid will not touch the lead. It will etch some of the iron away from the lead, leaving it on the surface in a greater percentage than originally. An etch is mandatory for adhesion. I have never seen a published process for leaded steel that did not encourage a fluoboric acid step. Some use a combined sulfuric fluoboric etch, but that would not be my preference, especially since it is used on non leaded parts also. Fluoboric acid is common! It is just not a common as sulfuric and hydrochloric.
Case hardened steel can be more difficult than unhardened to etch and to not smut.There are steps that can be taken, but that is getting out of the realm of this site and into consultants or good reference material. I am totally unimpressed by any plater that says they have never heard of fluoboric acid. Can you send a few parts to a better plater to see if they can do better. They need to know that it is leaded and that it has been case hardened!
- Navarre, Florida
Multiple threads merged: please forgive chronology errors and repetition 🙂
Pre-treating 12L14 Steel Prior To Zinc Plating
Q. Regarding adhesion problems with Zinc plating over 12L14 steel, it is my understanding that pre-treating the material in a fluoboric acid bath should help eliminate the problem. What is the proper chemical make-up of the fluoboric acid bath? Also, what is the most desirable temperature and soak time when doing an adhesion bake after the Zinc plating process?
Scott Johnson- Florida
2003
Multiple threads merged: please forgive chronology errors and repetition 🙂
Best cleaning or prep method for 12L14 machined material to be trivalent zinc chromate plated
Q. Hello,
I have seen much on the proper cleaning of 12L14, but am interested in what may be the best cleaning method from a zinc plating standpoint. The product is screws.
I am also interested in knowing what cleaning methods to stay away from.
Thank for your help.
metal products fabrication - Rochester, New York
2005
A. Since it is a leaded metal, your acid etch needs to be a fluoboric acid etch. A normal caustic cleaner should be useable. If you use a silicated one, do not let it dry on the parts as it is difficult to get off. Excellent rinsing is a must! An absolute must because the threads tend to hold solution. I assume that you are going to use a barrel plating method.
James Watts- Navarre, Florida
A. Hi. James is right on, as usual, but just so wrong inferences aren't drawn, a typical process would be alkaline soak clean, alkaline electroclean, good rinsing, fluoboric acid, rinse, zinc plate, rinse, possible dilute nitric acid dip, chromate, good rinsing.
Luck & Regards,
Ted Mooney, P.E. RET
Striving to live Aloha
(Ted can offer longterm or instant help)
finishing.com - Pine Beach, New Jersey
Readers may also be interested in these related threads:
• Topic 7863 "Zinc Plating on 12L14 carbon Steel (Blistering & Flaking Problems)"
• Topic #34370 "Zinc Plating Adhesion to Leaded Steels"
Q, A, or Comment on THIS thread -or- Start a NEW Thread