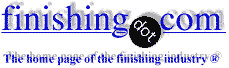
-----
Zinc Plating on 12L14 Steel (Blistering/Flaking)
Q. I am a large volume zinc job shop. Periodically we experience difficulty plating certain CNC parts made from 12L14(leaded steel). The process is as follows: soak clean-electroclean-2 rinses-pickle acid 25% HCL-2 rinses-condition (first rinse after plating)-plating W/alkaline-non cyanide 1.0 oz/gal. Zinc 15 oz/gal NaOH, 3 to 6 amp. per ft2 -2 post plate rinses-sour .75% HNO3 - clear, yellow or black dichromate. This customer manufactures all his parts (over 200) from 12L14, but only a very few (2) won't plate the first time through the process. We have skipped the cleaners skipped the acid and we still (may) have problems with these particular parts. We have run them once, pulled them off line, let them set 2 or 3 days and re-plate satisfactory. All other parts, stampings, CNC W/12L14, weldments. cold roll, hot roll, including parts from this particular CNC customer plate OK. There does not seem to be a logical explanation to the problem. WHAT AM I MISSING?
Don Penzenik- Elkhart, Indiana
2001
A. You need fluoboric acid et al to activate the 12L14.
I believe your other parts may not have the best adhesion if all you are using is HCl.
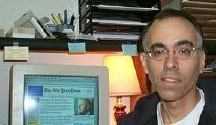

Tom Pullizzi
Falls Township, Pennsylvania
A. 1: Degrease
2: Electroclean Reverse current (rinse)
3: HCl pickle (about 10 seconds) (rinse)
4: 20% Fluoboric or sulfamic acid dip (30 sec - 1 min.) (rinse)
5: Plate
- Grand Rapids, Minnesota
Multiple threads merged: please forgive chronology errors and repetition 🙂
Q. We are zinc electroplating on machined 12L14 steel and we are experiencing blistering on the finish.
The zinc process is a rack operation, chloride zinc. When the parts are processed for the first time, the small blisters can be seen only with magnification (22X).
The parts had to be reprocessed due to the wrong chromate, and the second time these blisters are much more visible, with the naked eye. They are very small and uniform.
The chromate is yellow and we can see the blisters are grey in color. Each time we process again the parts, more blisters appear.
The 12L14 steel is known as a free-cutting carbon steel, resulfurized and rephosphorized, with the following compositions in %; Carbon 0.13 max., Manganese .85-1.15, Phosphorus .07-0.12, Sulfur 0.24-0.33 and Lead 0.15 to 0.35.
We are blaming the lead content on the steel. What is the best way to clean and process new parts? What can we do with the reprocessed parts? Are we bringing up (to the surface) the lead?
Any help will be greatly appreciated.
Enrique Segovia- Monterrey, Mexico
2001
A. It could be the lead, but my guess is that you are etching out the large manganese sulfide inclusions that will be in the microstructure of this steel. Each time you reprocess, the inclusions are etched out to a deeper depth - thus increasing the severity of the problem.
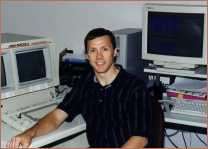
Larry Hanke
Minneapolis, Minnesota
Q. Larry,
Thank-you for your help. What preparation process do you recommend if this inclusions are manganese sulfide, as you mention.
Thank you again for your help,
Enrique Segovia [returning]- Monterrey, Mexico
A. Plating on 12l14 leaded steel. You can generally tell when you are dealing with it as any acid treatment to remove rust in a 50% HCl solution will cause it to gas and stink. But that treatment is held to a minimum and only as long as it takes to remove any rust. From that point I use a solution of 10% fluoboric acid for about 2 minutes to remove the oxidation from smeared lead on the surface.
Have had success plating electroless nickel direct on the surface or cyanide copper strike or plate. The plated parts pass all Quality tests including destructive testing.
Todd Huehn- Blaine, Minnesota
Multiple threads merged: please forgive chronology errors and repetition 🙂
Zinc Plate Flaking Off 12L14 Carbon Steel During Forming
Q. I have a problem/question regarding zinc plate of 12L14 steel. We have a cylindrical case made of 12L14 that is zinc plated 200-400 microinches (our specifications). During the subsequent assembly process, we place a plastic cap into the case ends and roll the case ends using a pneumatic press and mandrel to capture the plastic caps. The rolling operation causes flaking of the zinc plate, which can cause electrical failures due to metallic particles inside the case. What are my alternatives to zinc plate that will not flake off during the rolling of the case ends, and what are the tradeoffs?
Mike McMonagle- Houston, Texas
2002
A. Machinists love leaded steel. Platers hate it for exactly the problems you have. Normally, using a fluoboric acid dip will remove enough lead to give better adhesion. This is a more expensive acid and may have to be in addition to the muriatic or sulfuric the plater is using. Most tank lines do not have the capability of adding another acid tank and associated rinse tanks. Two main choices:
1. go to a NON free cutting steel or
2. go to a plater that can use the fluoboric treatment.
- Navarre, Florida
A. Maybe a more ductile plate? Try Zinc Iron... if the specification does not allow a plating change, are you getting it plated with acid or alkaline zinc? Are there cosmetic concerns for the finished assembly?
Brian Lucas- Wolcott, Connecticut
Multiple threads merged: please forgive chronology errors and repetition 🙂
Q. WE HAVE A PROBLEM WITH PLATING RECENTLY, OUR PRODUCTS GET ZINC PLATE WITH YELLOW DICHROMATE THE MATERIAL IS 12L14 WE REQUEST THAT OUR PLATING THICKNESS BE .00015 TO .0003 ON ALL PARTS FOR YEARS IT WAS EXCELLENT. NOW THE PLATING BUBBLES AND SEPARATES FROM THE MATERIAL AND FLAKES OFF BY TOUCHING ESPECIALLY ON CORNERS WHY IS THIS HAPPENING THE PLATING HOUSE SAYS IT IS NOT THEIR FAULT IT IS OUR MATERIAL. WE HAVE USED THIS MATERIAL FOR 18 YEARS.
Buford Sparrowgroveelectronic and liner governors for off road use - Rockford, Illinois, US
2006
A. Steel varies from manufacturer to manufacturer and even between lot numbers from the same manufacturer. You are using leaded steel! An increase in the amount of lead from the minimum to the average amount is enough to have problems with plating. That said, the plater should be using appropriate chemicals to insure that the traces of lead are removed from the surface. If the plater took the job knowing that it is leaded steel, then it is up to them to properly plate it or prove that the amount of lead is out of specification HIGH. It is not being properly plated and the plater can not say that it is the steel unless he proves that it is out of spec. The fact that they plated it for 18 years without a problem does not negate his responsibility. If I were the plater, I would strip the parts and send them back to you with a "sorry". Basically, you will have to find a new plater or work with this one to make modifications to the line, which will mean a higher price.
James Watts- Navarre, Florida
Multiple threads merged: please forgive chronology errors and repetition 🙂
Q. Hello,
I have an ongoing problem with zinc-plated steel pipe that flakes AFTER crimping operations. Plating is not flaking before any material deformation. However, different lots of material will flake after crimping. We have reviewed the obvious culprits, like surface cleanliness before plating and plating thickness. I have noticed that higher concentrations of silicon (above 0.010%) had flaking issues, but the metallurgist doesn't think that's the issue. So, what else can I look at? The lot #'s with asterisks were the lots with adhesion issues.
Lead Sulfur Silicon
876475 .280 .310 .003
998853 .280 .340 .002
998995 .280 .350 .002
998995 .280 .350 .002
L1394H .270 .320 .011
35179108* .190 .270 .020
724006* .263 .319 .005
Quality Engineer - Solon, Ohio
May 18, 2010
![]() |
A. I will bet you a cheap cup of coffee that it is because you are using leaded steel. This needs a fluoboric acid activation step rather than HCl or sulfuric acid. - Navarre, Florida A. The smeared lead on the surface forms insoluble salts with sulphates and chlorides, you must dip in 30% fluoboric acid and enter the zinc "hot", or the very best you can do is to strike in zinc fluoborate and cover the lead, then the flaking will be minimized. ![]() Robert H Probert Robert H Probert Technical Services ![]() Garner, North Carolina ![]() A. It is a leaded steel. ![]() ![]() Sara Michaeli Tel-Aviv-Yafo, Israel |
Thank you so much for your responses! I know the platers "pickle" the parts, but I can't say for sure if the acid is fluoboric. Actually, I am thinking it's hydrochloric.
So, could this could also mean that different zinc bath chemistries (alkaline zinc and acid chloride) could also play a part?
Thank you so much!
Dean
- Solon, Ohio
May 24, 2010
Multiple threads merged: please forgive chronology errors and repetition 🙂
Q. We are plating a material (12L14) of very small (Φ 4.9 & length 5mm). Now the customer found bubble on the part (but the bubbles are only on the face portion not on the round area).
Our process is Soak Cleaning, Water Rinse*2, Anodic Cleaning, Water Rinse*2, Acid Pickling (60-80%), Water Rinse*2, Neutralizer, Plating.
We work on every stage but didn't found the root cause.
Now some chemistry suggest to go for Descaling chemical instead of Anodic Cleaning.
If any one have some suggestion, we are very grateful.
Kindly revert asap....
Employee - Faridabad, Haryana, India
April 4, 2023
A. Hi Sumit,
Many experienced platers (including Tom, Scott, Todd, James, Robert, & Sara) have told us above that an acid containing fluoride is necessary to deal with the lead in 12L14.
We're open to hearing of advances which would change this situation, but customers want robust plating adhesion, not adhesion that works sometimes but is "iffy" ... and trying to process leaded steel without fluoride, may work sometimes as long as the lead is not smeared, but it is simply not a robust process, it will remain "iffy".
Luck & Regards,
Ted Mooney, P.E. RET
Striving to live Aloha
(Ted can offer longterm or instant help)
finishing.com - Pine Beach, New Jersey
Q, A, or Comment on THIS thread -or- Start a NEW Thread