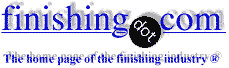
-----
Zinc Plating Adhesion to Leaded Steels
Q. Several threads on this forum suggest the use of fluoboric acid to etch 12L14 steel prior to plating. I too am trying to solve zinc chromate flaking that results from cold forming the part after plating. My plater is willing to experiment but needs specific information on concentrations, times, etc. Can anyone help me help my plater?
Also, why does the zinc have a problem sticking to the lead areas of the part?
BD LewisManufacturer - Kalamazoo, Michigan
2005
A. Cold forming will flake off the very best chromate conversion coating. Chromate cannot withstand any mechanical, chemical, or thermal attack.
Your zinc is not sticking to the leaded steel because in the presence of chloride, lead forms an insoluble compound that flakes off. And he is plating in a Zinc Chloride solution with free hydrochloric acid. It did no good to go thru the fluoboric and then set it down in the zinc chloride plating solution.
Have the plater get in a hurry after the fluoboric acid dip, make contact outside the plating solution, and go in "hot".
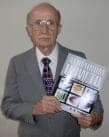
Robert H Probert
Robert H Probert Technical Services

Garner, North Carolina
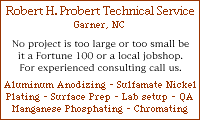
2005
A. Please forgive me for oversimplification. The reason the zinc plate is non adherent to the leaded areas is that the surface preparation suitable for activation of the steel area leaves the lead passive. Lead is not soluble in any of the common acids used for activation (sulfuric, hydrochloric, proprietary acid salts, etc) and therefore must be treated in an acid it is soluble in, namely fluoboric acid (lead fluoborate is formed in the acid solution). I would try using a 20% by volume solution of fluoboric acid at room temperature for about 1 minute. Move concentration and/or time up as necessary.
By the way, if you are cold forming the part and using an acid chloride zinc process, you also need to look at the ductility of the zinc deposit (flaking is notorious when bending chloride zinc plated parts). If this is the case, constant carbon filtration and frequent additions of an oxidizer to reduce organic contamination are very helpful.
Gene Packman- Great Neck, New York
2005
A. I cannot help with the zinc chromate as I know nothing about it. However, the lead in the steel may cause a problem because of lead smear. Lead is normally added to help machinability, but it leaves a thin film of lead on the steel. This inhibits adhesion of overlays. To remove the lead, you will need to soak in fluoboric acid (say 20% for 2-5 minutes, depending on the temperature, amount of lead smeared and the type of steel). To check this, ask your supplier for advice.
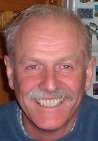
Trevor Crichton
R&D practical scientist
Chesham, Bucks, UK
2005
Q. Thank you for the responses; the lead oxide explains the problem. I should have been more clear on the electroplating process. We are using an alkaline process and a hex chromate.
Also, ductility was mentioned. Does anyone know where I can get mechanical properties for zinc coatings that I can use to evaluate against our forming process?
Thanks again for the response.
BD Lewis [returning]- Kalamazoo, Michigan USA
2005
2005
Q. I am doing zinc electroplating on M.S. round pipes in hexavalent chrome. After plating, when we press the component for processing, the pressed portion of chrome passivation peels off. |
ACRONYMS: |
What may be the reason and how it can be stopped.
Sushil Kumarplating shop - Gurgaon , India
2005
A. Mr Sushil Jain
Hello and Greetings..
Please rinse twice after dragout.
Activate in 20 Mls per liter Nitric acid dip. 2 percent solution...
Rinse
Chromate
Replenish the nitric at 5 mls per liter every 4 hours worked..
This will solve peel off of Chromate over alkaline zinc
Regards
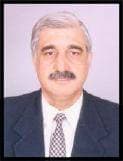
Asif Nurie [deceased]
- New Delhi, India
With deep regret we sadly advise that Asif passed away on Jan 24, 2016
Black spots when alkaline zinc plating EN1a leaded parts
Q. I have a problem with alkaline zinc plating using vat method on EN1a leaded material, the problem is there are black spots on the component.
Kindly suggest me the ways to correct it
Thanking you.
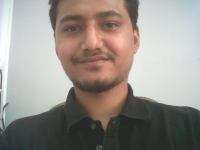
Aditya Kochar
electroplating business - Jaipur, Rajasthan, India
July 13, 2011
July 13, 2011
? Hi, Aditya.
I'm not familiar with "EN1a". Can you tell us what standard or numbering system this is found in?
Are the black spots present before the chromating, or only after chromating? Do they appear immediately after chromating or do they only develop after several days? You say you are "vat plating" . . . does that imply that you are rack plating, or are you barrel plating. Some photos of the spots might help.
Regards,
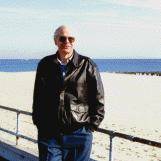
Ted Mooney, P.E.
Striving to live Aloha
(Ted can offer longterm or instant help)
finishing.com - Pine Beach, New Jersey
Q. It is rack method also called vat method, trivalent passivation; the black spots are visible immediately after passivation.
I even tried doing fluoboric acid no result.
This material is equivalent to SAE 12l14,11smnpb30.
EN1a leaded is european standard.
Will be mailing the pics soon of the defect soon.
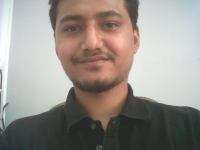
Aditya Kochar
electroplating business - Jaipur, Rajasthan, India
July 15, 2011
Q. I have same problem EN 1A LEADED. We are doing alkaline zinc plating rack type. Black spots visible after one month at customer end.
dhinakaran karan- hosur, tamilnadu, India
August 29, 2015
Q, A, or Comment on THIS thread -or- Start a NEW Thread