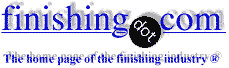
-----
Plating time too long (acid zinc) / Calculating best plating rate

Q. In acid Zinc barrel plating, 2 mm washer is taking 2 hours for 5 micron plating, can this time be reduced?
Yoginder thakurEmployee - Faridabad, India
January 15, 2023
A. Hi. The plating time can be reduced and it should be. Based on experience, barrel plating of 5 microns of zinc should take somewhere around half an hour, not much over, certainly not 2 hours. Probably your rectifier is too small, or the barrel holes are too small or plugged up, or you are overfilling the barrels. What size are the barrels and what amperage and voltage are they drawing?
Luck & Regards,
Ted Mooney, P.E. RET
Striving to live Aloha
(Ted can offer longterm or instant help)
finishing.com - Pine Beach, New Jersey
⇩ Related postings, oldest first ⇩
Q. I am using ammonium chloride zinc plating (barrel plating). For getting 3-4 microns it takes 2-3 hrs. We are plating to the fasteners of different types. How shall I reduce the time of plating? What factors can affect the plating time.
Santosh Z [last name deleted for privacy by Editor]- Dubai, UAE
2002
A. Hi Santosh. It sounds like you have about one fifth of the current you would need. Please start by cutting the load in half without reducing the amperage and tell us what happens. Thanks!
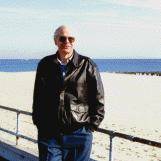
Ted Mooney, P.E.
Striving to live Aloha
(Ted can offer longterm or instant help)
finishing.com - Pine Beach, New Jersey
A. Adjusting your current density higher will increase plating rate. Also optimize other parameters in the solution, zinc metal, pH, temperature. Another variable to look at will be barrel design, barrel speed and loading in barrel. You should have a barrel that has the largest open surface area so you can get the most transfer of solution into the barrel.
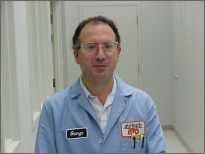
George Shahin
Atotech - Rock Hill, South Carolina
A. Factors that can affect plating rate.
1. Current Density can be increased to increase the plating rate. However, there is a maximum point where too high current density will create another set of problems such as burning and poor quality work.
2. Increasing the metal concentration in the process solution will increase the plating rate.
3. Bath pH concentration will impact plating rate. At lower pH concentration, hydrogen will plate out like a metal; thus, competing and lower the plating rate of the desired metal.
4. The concentration of the organic package such as wetters or brighteners will affect plating rate depending on the situation. For example, too much organic additives may reduce the plating rate, or wetters may be required so the part to have a good cathode film which may increase the plating rate.
5. Unwanted organic or metallic contamination will negative impact on the plating rate.
6. Temperature: most chemical processes increasing temperature can increase the rate of reaction such as increasing the plating rate, but it may also have a negative impact on the plating rate as well depending on the situation.
7. Solution agitation will affect plating rate. Increase the solution agitation will increase plating rate.
8. In a barrel plating operation, slower barrels speeds will increase the plating rate by increasing your coefficient of electrical contact within the barrel.
- Lebanon, Kentucky
Acid zinc plating problem
Q. Hi Everybody,
1. I have a problem in ammonium chloride zinc plating bath of not getting desired current. I am passing 10-16 volts but getting 500 amps, where it should be 1000 amps. What could be the reason.
2. Also if I process 33.6 sq.m. surface area in one barrel by passing 500 amps current, the what time it should take to get the 3-5 microns coating. Our supplier has given following spec. -
0.5 to 1.0 amp current per one Sq.Decimeter
time - 1 hour
coating thickness - 13 micron.
3. Also please let me know, for high carbon containing compounds which process is suitable, alkaline zinc (non-cyanide) or acid zinc, keeping in the mind that no loss of production rate.
Regards,
Santosh Z [returning]- Dubai, UAE
2002
A. Hi Santosh.
1). It "should be 1000 Amps" based on what? Wanting it to be 1000 Amps so you can plate twice as fast is one thing, but having a valid reason to expect 1000 Amps may be another thing :-(
2). The Metal Finishing Guidebook has an "Electrochemical Equivalents" shortcut table which factors metal densities and valences into Faraday's Law so that you can directly read that it takes 14.3 A-hr/ft2 to deposit a 0.001" thickness of zinc, assuming 100 percent efficiency. Converting square feet to square decimeters, it should take 1.544 A-hr/dm2 to deposit 0.001". Converting mils to microns, it should take 0.0608 A-hr/dm2 to deposit a micron at 100 percent efficiency. Your supplier's numbers say you'll need 0.038 to 0.077; so let's go with the 0.077 A-hr/dm2 to deposit a micron. So 3 to 5 microns will take you .23 to .39 A-hr/dm2 to get your thickness. I hope there is a typo in your question because 33.6 square meters is several times too large of a load and would take 773 to 1290 Amp-hours to deposit 3-5 mils. I'd like to see you plating for about 30 minutes, not 1-1/2 to 2-1/2 hours, for 3-5 microns coating. Again, please put half the weight into the barrel and get back to us with what happens.
3). For high carbon, you need acid zinc. Because of hydrogen overpotential you can't easily plate them in an alkaline bath.
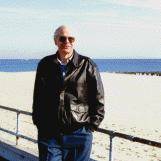
Ted Mooney, P.E.
Striving to live Aloha
(Ted can offer longterm or instant help)
finishing.com - Pine Beach, New Jersey
Multiple threads merged: please forgive chronology errors and repetition 🙂
Low current density
Q. Hi Everybody,
We are plating screws in acid zinc plating process. The screws have threads & so in barrel plating, the current passes varies with different areas.
Always we are getting poor coating at low current density area, somewhat grey/black coating. How shall I improve to get good coating in low current density area. As there is poor coating rate at low current density area we require more time to achieve the required coating. Please help.
Regards,
Santosh Z [returning]- Dubai, UAE
2002
A. You are probably over-filling your barrel. Adding an extra 10% to the load and having 90% failure rate is not cost effective. Second, check your barrel. Have the holes been peened shut slightly? Can you open the hole up a few thousandths to get better solution flow into the barrel?
James Watts- Navarre, Florida
A. Sounds like the barrels are too full or the barrel holes are plugged . Solution transfer is most important. You should use the largest hole you can without losing parts. Check to see if the holes are plugged or closed and if so clean them or drill them out!
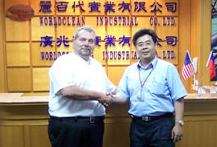
Drew Nosti, CEF
Anodize USA

Ladson, South Carolina
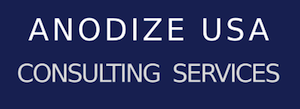
A. As is already suggested you may be filling the barrel little too much. Also check the Metal : Chloride ratio. To get best results at LCD it should be 1 : 5 / 1 : 5.5.
R.K. Khare- Mumbai, India
A. I am in agreement with both arguments about oversized load and ratio of chloride/metal. Instead of clogged barrel holes you may be using a cylinder with too small holes resulting in a lower than anticipated current density. Also, by having a brightener imbalance you may not be getting the best LCD coverage. Further, check your pH. Operating at the lower end of the range will generally improve LCD distribution at a marginal increase in brightener consumption. The ratio of metal/chloride will vary from process to process. Check your vendor recommendations. Also check bath temperature. Too low temperature will result in dull, gray LCD. BTW, check with your vendor for a troubleshooting guide.
Gene Packmanprocess supplier - Great Neck, New York
2002
Multiple threads merged: please forgive chronology errors and repetition 🙂
Q. Hi Everybody,
We are using ammonia-ammonium chloride acid zinc plating chemicals in barrel plating. The suppliers specification is at 0.5 to 1.0 amp/sq.dm. current we should get 13 microns coating thickness. But we can achieve only 3-4 microns in hour. Our barrel load is 60 kgs of screws i.e. about 13 sq.m. area. As per standard specification for load the screws should be loaded about 30 kgs. We are processing double surface area due to high production requirement. The anode surface area we are providing for three barrels, i.e., 39 sq.m. cathode, is just 4 sq.m.
I would like to know if there is any relation of anode surface area with coating formation rate. Please tell me if I increase anode surface area then shall I get faster coating formation?
Regards,
Santosh Z [returning]Dubai, UAE
2002
![]() |
This is the 4th time you've asked the same question, and the three previous times it's been answered by at least 7 plating experts, every one of them telling you that you are overfilling the barrels ... but you insist upon rejecting their answer and continuing to overfill the barrels :-( No matter how badly you may WANT to, it simply will not work!! Your situation is NOT UNIQUE, Everyone, Everywhere, the World Over would love to put twice as much work in their barrels for more production :-) Please operate more shifts ... or install a 2nd plating line .... or farm out part of the volume or ... ![]() Ted Mooney, P.E. Striving to live Aloha (Ted can offer longterm or instant help) finishing.com - Pine Beach, New Jersey A. I am normally kinder than this response. BUT! this is a typical stupid management decision. The specifications are there for a reason! In short, you cannot drive enough current thru the holes or mesh to plate. In addition, the barrel cannot function properly because it is too full so does not flush enough new solution into the tank to have enough metal ions to be able to plate. I am sorry, but I have lived thru just this stupidity of managers who know absolutely zero about plating. James Watts- Navarre, Florida |
? Hi Jim,
I wouldn't blame management stupidity with just the available information. Loading of barrels and barrel cathode current density are highly variable.
I want to know about how full (by volume) the barrels are filled, What size and how many holes in the barrel, chemistry of the bath, how many amperes, pH, temperature, distribution of plating on the screws.
And I would ask: Size of the anodes, composition (slab, slugs, type of basket), distance from barrels, how many across from each basket, are two barrels sharing anode baskets?
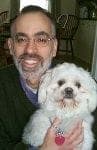

Tom Pullizzi
Falls Township, Pennsylvania
A. Sorry Tom, the man said his spec was for 30 KG and he was putting in 60 kg. The spec came from somewhere, probably the Mfgr.'s recommendation for that product. Sounds to me like the barrel is so overloaded that it just is not going to work if that is the case! Ted's response covers it well. The man is looking for fu fu dust to make his improperly operated line work. I have yet to find a reliable vendor for it.
James Watts- Navarre, Florida
Hi Jim,
Armed with the knowledge that this letter has been around the track 4 times already, I am no longer interested in it either.


Tom Pullizzi
Falls Township, Pennsylvania
A. Hello Santosh!
The plating thicknesses is mainly a function of
1. Plating time
2. Current and voltage fed
3. The appropriate surface area of the material to be plated
4. Plating Bath pH, etc.
If you constrain all other factors you have to alter the
1. voltage and current fed
2. Total Mass of material to be loaded into a barrel
As you said you are loading almost about twice of the barrel capacity then to get the desired plating thickness you have to change the other process parameters to compensate the increased surface area.
1.plating time
2.voltage and current fed
because the surface area directly gets doubled if you load twice the capacity.
Hope it may help...
Best regards,
- Rajkot, Gujarat, India
December 20, 2017
Hi Bhavik. Thanks for replying to this letter. Although it's an older one, this site is intended for long term reference, and your reply will help future readers if not Santosh.
Although it's true that you need twice the current if you put twice the load in the barrel, that does not mean that you can make grossly overloaded plating barrels work. Let's be careful about offering a desperate man a will-o'-the-wisp :-)
Regards,
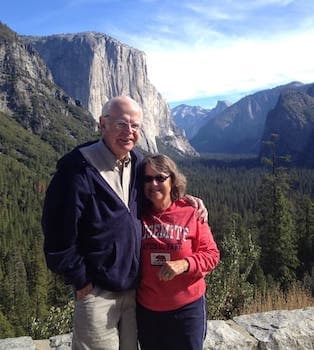
Ted Mooney, P.E. RET
Striving to live Aloha
(Ted can offer longterm or instant help)
finishing.com - Pine Beach, New Jersey
Q. I am recently started barrel plating of zinc chloride bath but I am unable to calculate the desired value of current and voltage, I normally plate nuts, blots, washers etc. My barrel size is 18" X 42" Please help me, and let me know the calculations also.
ABHISHEK KALIA- Ludhiana Punjab
January 8, 2021
A. Hi Abhishek. Bolts and nuts have a lot of surface area due to their threads, and small fasteners have much more surface area per pound/kilogram than large fasteners. Ideally you should know the surface area, and your process vendor will give you the suggested current density. But lacking such figures, you might be able to successfully plate over 300 pounds of large fasteners but only 125 pounds of small ones because they would have about the same surface area. And you usually have to plate rather heavy on the crests of the threads to assure coverage at the roots.
You don't really have to worry about controlling both the current and the voltage because you can't independently control them, they are not independent, they are tied together by Ohm's Law.
You must also know the required thickness of the plating. Some standards dictate that it be a minimum of 5, 8, 13, or 25 microns depending on the service conditions. 5 µm or a little less is probably typical of what most hardware sold to consumers is, and 8 µm is probably the most common automotive spec. The thickness of plating will be directly proportional to the current X time according to Faraday's Law -- that is the 'calculation' you are looking for.
Some of what we know about plating is empirical rather than based on first principles though, and you can probably fill your barrels no more than about 1/3 full even for large fasteners; it will probably take 25 to 45 minutes of plating to get to those 5-8 µm thicknesses, at a voltage of between 7 and 12 Volts, and an amperage between 400 and 1200 Amps. So that should serve as a "reasonableness" check of your process vendor won't help you get started.
The earlier entries on this thread should be informative and entertaining :-)
Luck & Regards,
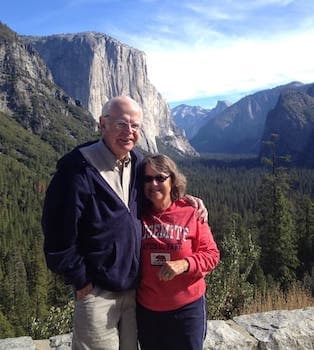
Ted Mooney, P.E. RET
Striving to live Aloha
(Ted can offer longterm or instant help)
finishing.com - Pine Beach, New Jersey
Q. Hi
My name is akil from india.
I am using acid zinc plating.
My bath often get heated.
And it takes almost one hour to plate.
Please help me.
Zinc electroplating - Coimbatore, tamilnadu, India
February 14, 2019
A. Hi Akil. Your acid zinc plating bath requires cooling coils or a heat exchanger. All the heat (power) you are putting into the plating bath with your rectifier must be removed with a cooling system (BTU/hr of cooling = Volts x Amps x 3.412). Good luck.
Regards,
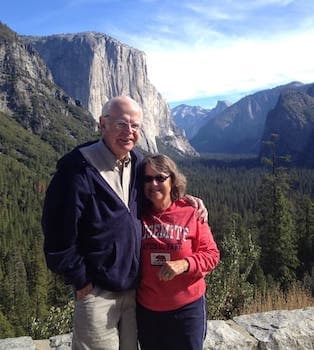
Ted Mooney, P.E. RET
Striving to live Aloha
(Ted can offer longterm or instant help)
finishing.com - Pine Beach, New Jersey
Q. Hello sir,
My Question is: 1 Micron/Dm2 How Much Zinc Metal Consumption?
Plating Shop Employee - India, Gujarat
October 31, 2022
A. Hi Mahipalsinh.
If you multiply the surface area (in dm2) of all the parts you want to plate by the plating thickness you want (in microns) you must divide by 100,000 to get the volume of the zinc in dm3 (because a micron is 1/100,000 of a dm).
Zinc weighs 7.13 kg/dm3.
But it is very difficult to get an even thickness of plating -- it is not at all unusual for some areas to have twice the plating thickness (or more) than other areas.
Luck & Regards,
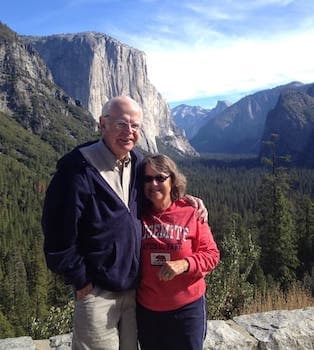
Ted Mooney, P.E. RET
Striving to live Aloha
(Ted can offer longterm or instant help)
finishing.com - Pine Beach, New Jersey
Q, A, or Comment on THIS thread -or- Start a NEW Thread