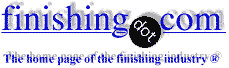
-----
Zinc oxide production by French process
September 16, 2011
Dear Sir,
I am dealing with wet process zinc oxide by ammonium carbonate (us patent 4071357). We have to make project on a chemical plant.
So I have selected ZINC OXIDE POWDER making plant which is useful in making zinc oxide active.
I have to make total process for making zinc oxide powder(wet process).
I have some of the question regarding this which are as follows
1) What is the process of making zinc oxide powder(wet process)?
2) What type of machinery is required for making it?
3) From which Material it requires?
4)The product purity is 97% to 98%? Why Opaque white or yellow color is?
5) Where can we use it? (state all the useful area)
6) If you have any picture of plant, please send it to me?
Please provide me all guidance about wet process zinc oxide plant, process, equipment required, and uses.
I will be very thankful to you if you are answering my questions.
Thanks,
Regards,
Arash akbary
chemical - iran tehran
September 16, 2011
Dear Mr. Arash Akbary,
The process you are using is Ammoniacal ammonium carbonate leaching method. This method is used as recovery is maximum in this method. And we can recycle ammonia
⇦ on
eBay or
Amazon [affil link] again and again. In India there are plants using same method.
1) What is the process of making zinc oxide powder (wet process)?
There are different wet processes for making of zinc oxide. You can leach zinc from zinc bearing waste (mostly non-metallic) using different acids. Purify the solution and precipitate in the form of zinc hydroxide or carbonate. Filter and dry the precipitate and further calcination produces zinc oxide. Wet process is mainly used for non-metallic waste of zinc.
2) What type of machinery is required for making it?
Plant and machinery includes reactors, filters, centrifuge, dryers, calcinators. In Ammonium carbonate we need steam distillation column (ammonia strippers).
3) From which Material it requires?
Zinc ash from galvanizer, waelz oxide, other zinc bearing waste. It has wide scope for zinc recycling.
4) The product purity is 97% to 98%? Why Opaque white or yellow color is?
Pure zinc oxide is opaque white powder. Yellowish color is due to impurity in oxide. The purity we check by checking Zn+ and then calculate for zinc oxide. But if there is zinc carbonate purity indications become wrong. You can first calcinate sample at 900 °C and then check for purity. Even then sample is lower in purity then there are some impurities and the purification of zinc solution is not done properly.
5) Where can we use it? (State all the useful area)
Zinc oxide has wide applications. But calcination of zinc carbonate gives high surface area zinc oxide having application in catalysts and desulfurization in petroleum industry.
You can refer the article from Iran
www.sid.ir/en/VEWSSID/J_pdf/92220080416.pdf
For more questions you are welcome...
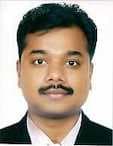
Umesh Charki
- Thane, India
Dear Respectable & honourable personalities.
1. We need to know about how we can reduce our gas expenditure?
2. Is there any other way without crucible to reduce expenditure.
Your response would be appreciated.
qamar
gujranwala, Pakistan
October 24, 2011
Dear Umesh,
1.We need full information about f/o adjustment all specific surface area because we are adjusting new crucable on this is our new experiment on f/o. your co-operation will be appreciated.
2.which one suitable burner for f/o.
3.what will expense on 1 mt for f/o.
your cooperation will be honourable.
- Gujranwala
November 1, 2011
With respect
Mzahmtvn Myshm of Iran. I want a series about the production of zinc oxide. In the case of slag in the production process and also produces zinc oxide Mytvnym do?
- Maybod, Yazd, Iran
November 30, 2011
Q. Dear Sir,
How can I make fine particle size say 2-6 microns ( 100% particles <37 microns) and 7-10 microns ( 100% particles <45 microns) zinc dust
⇦ on
eBay or
Amazon [affil link]
?
I will appreciate all information.
Regards,
Bernard
zinc - Guatemala
Reducing iron oxide in zinc sulphate
Q. Q.HOW CAN WE REDUCE IRON OXIDE % FROM ZINC SULPHATE AS A PRODUCT.THE HIGH % OF IRON OXIDE IS( 4.5) & THE LOW % IS (3.8) WHICH CAUSING OUR PRODUCT TO HAVE HIGH DENSITY & LOW DENSITY.CAN WE REDUCE TO LESS % e.g (0.1-1.5) to maintain our high density?
DENVA MASILELALABORATORY TECHNICIAN - SOUTH AFRICA
September 7, 2016
Q. Dear Sir
We are leading manufacturer of white seal zinc Oxide in India. Further we are planing to manufacture ACTIVE ZINC OXIDE Please share your knowledge and technology for producing active Zinc Oxide. Anybody ready for consultancy may contact us.
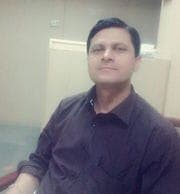
Ravi Girase
Manufacturing white Seal Zinc Oxide - Daman Daman (UT) India
September 28, 2017
Ed. note: This RFQ is outdated, but technical replies are welcome, and readers are encouraged to post their own RFQs. But no public commercial suggestions please ( huh? why?).
How to convert zinc hydroxide to zinc oxide
Q. I want to know the which condition should I use to convert zinc hydroxide to zinc oxide and this zinc hydroxide was formed by precipitation of zinc chloride solution using NaOH.
riddhisiddhi parajiya- rajkot, gujarat, India
October 16, 2017
Q. Can anyone tell me why all the zinc in the crucibles does not get vapourised/exhausted and some type of slag is found at the bottom while charging the metal. It is impossible to remove all of it and over time it builds up to 1 feet height at the bottom, and so the capacity of the crucible gets reduced.
Hari Prasad- Chennai, India
October 20, 2017
May 26, 2018
Q. I am interested in manufacturing Zinc Oxide (Ceramic Grade).
But for project physicality I need answer of few queries --
1. What are the possible raw materials of Zinc which can be utilized commercial for production of Zinc Oxide ?
2. Is zinc oxide can be manufactured from low zinc containing Zinc hydroxide ?
3. Manufacturing cost (excluding raw material cost) per MT production of Zinc Oxide (White seal) ?
4. Which fuel is good Diesel or Gas ?
5. What are the Government Clearances required for setting up of Zinc Oxide plant ?
6. What is Zinc Oxide annual Growth rate ?
I appreciate if anybody can give their recommendation on above query as much as possible.
- Surat, Gujarat, India
Hi Amit. Best of luck! But your questions cover the whole gamut from marketing studies, to government regulations, to the practicalities of fuel selection, to the costs of production, to the feasibility of alternate & emerging technologies: I think you should strongly consider retaining a consultant because just a broad brush approach to these 6 topics would be at least a week's work :-)
IZA's "Zinc College 2018" in Finland (https://www.zinc.org/zinc-college-2018/) is a 5-day introduction to several of your topics. Good luck.
Regards,
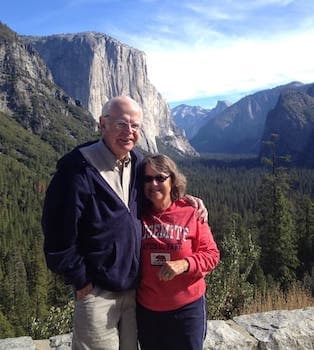
Ted Mooney, P.E. RET
Striving to live Aloha
(Ted can offer longterm or instant help)
finishing.com - Pine Beach, New Jersey
June 2018
Q. Dear Participants,
We are a manufacturer of Zinc Oxide White seal in India. We planned to start manufacturing Zinc Hydroxide to further manufacture Zinc oxide from cancellation process.
We have the following Plant and machinery including reactors, filters, centrifuge, dryers.
We reacted Zinc Chloride liquid form with NaOH to form Zinc Hydroxide but the resulting formation is not drying.
Can anyone guide me through the process of its manufacturing?
- Haryana, India
August 25, 2018
December 5, 2018
Mr. Shubham,
Normally zinc oxide from zinc hydroxide is manufactured by sodium hydrosulfite
⇦ on
eBay or
Amazon zincaffil links] manufacturers as they generate large quantity of zinc hydroxide.
When you reacted zinc chloride with NaOH, zinc hydroxide forms with NaCl salt, so you have to wash NaCl salt from the precipitate. After washing filtration of zinc hydroxide to get @ 30% - 40% wet cake. Usually this wet cake directly charged in rotary kiln for calcination to reduce carryover and loss of zinc hydroxide powder.
But you can first check the viability of the process you are planning to go with. As there are two roots, one is carbonate and second is hydroxide. In carbonate you can treat zinc chloride with sodium carbonate
⇦ on
eBay or
Amazon]
and make zinc carbonate. After calcination of zinc carbonate, you can get high surface area zinc oxide.
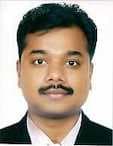
Umesh Charki
- Thane, India
Q. We manufacture ZnO via the french process.
What is the typical particle size D[4,3] and D(0.5) expected for this process?
If hood design and available reactant (oxygen) is critical for particle size formation, what hood specifications should be adhered to for optimizing decreased particle size?
Any support is greatly appreciated.
- Brisbane,Australia
February 1, 2019
March 13, 2019
A. Dear Mr. Brad,
We are more concerned about surface area than particle size analysis in India. We keep at @ 5-6 square meter/ gram, which is preferred by rubber industry. Higher surface area is preferred but it is costly.
To control particle size we need to understand the reaction kinetics and particle formation mechanism. It is Gas + Gas = Solid reaction. Actually burning of zinc vapours in air.
Also post reaction, solid particle formation is similar to crystallization. So if you want fines, rapid cooling is needed. But up to 450 °C, below there is no change in particle size. So you can design the hood for better dispersion/scattering of zinc oxide particles in air and two-stage air cooling to facilitate rapid cooling (fresh air inlet at upper part of hood).
The limitation of French process is surface area of 2 sq. mt/ gram to 10 sq.mt./ gram. So for anything out of this range you need to check with alternative processes for zinc oxide manufacturing.
You can check with Dr. Shahrom Mahmud (Malaysia), He has done extensive work on zinc oxide particle fabrication.
https://www.researchgate.net/profile/Shahrom_Mahmud
Regards,
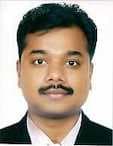
Umesh Charki
- Thane, India
A. I fully agree with Umesh. He is absolutely right in controlling particle size vis a vis surface area. But I think Brad is requesting for control of secondary particle size... Something that you measure on a Malvern. This is important for a lot of pharmaceutical applications.
Brad, the solution lies in adjusting the hood to control secondary particle size to d50 less than 1 micron. Normally you get about 4.
Self Employed - VADODARA, Gujarat India
April 26, 2019
Q. Dear All,
It is a very warm feeling to be the part of this Group. We are the manufacturers of Zinc Oxide in North India by French Process.
Please help me out: how can we terminate turbidity of Zinc Oxide Solution in Phosphoric Acid. The turbidity even persists with the HG Grade also. Is it relating with particle size or something needs to be done with our Process to get turbidity free/Clear solution.
The solution consists with Phosphoric Acid, Nitric acid, water & Zinc Oxide.
Thanks
Executive Sales & Marketing - Yamuna Nagar, India
May 18, 2019
May 27, 2019
A. Dear Mr. Vikas,
When you dissolve zinc oxide in phosphoric acid, Zinc oxide reacts with phosphoric acid and it?s soluble in water in all proportion. But free zinc in zinc oxide reacts with phosphoric acid to form zinc phosphate, which is insoluble in water. It produces turbidity in solution.
If you want a clear solution of zinc oxide in phosphoric acid, then you have to get rid of free zinc / unreacted zinc in zinc oxide. This is produced by complete burning of zinc in air and separation of heavy (unreacted) particles by using proper gravity settlers.
Regards,
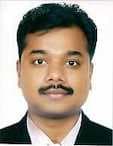
Umesh Charki
- Thane, India
June 8, 2019
Q. Dear Charki Sir,
Thank you very much for your kind advice. I have some few more doubts to be clear.
1. we have a Batch Time of approx. 11 to 13 hrs with approx. 1700-1750 Kgs of RM (Bottom Dross) per Batch.
2. We have Gravity Settlers connected next to the Suction Hopper.
Kindly Advise:
1. Should we raise our Batch Time by slowing the Blower's Suction & hence provide more time for reaction/Burning of Zinc?.
2. The Height of Hoppers are approx. 13 to 14 inches from the Lid hole; please advice is it sufficient or need to be adjusted?
Shall seek your Expert Comments.
Thanks
- Yamuna Nagar
A. Hi Vikas, I think I differ with you on some fundamentals.
Zinc Oxide is best made through semi continuous process and not batch process in a crucible furnace.
Blower speed is a secondary control for reducing rate of production, primary control is burner adjustment.
You have to control the ratio of primary air (that mainly goes through the bottom of your hood on the furnace) vis-a-vis quenching air (that enters from the gap between hood and the ducting). This can give you control over free zinc particles.
This information is quite fundamental to making Zinc Oxide. Anything beyond may not be possible.
I would suggest that you appoint a consultant. I do not know if someone like Umesh would be interested.
Self Employed - VADODARA Gujarat India
June 11, 2019
Dear Abhay Sir,
Thank you very much for your special Comments.
We are working with conventional Oil Fired Twin Crucible method (French Process) for producing Zinc Oxide. A day normally produces 2 Batches (12-13 Hrs each) with charging of 1700-1750 Kgs of RM per batch. It is kind of semi continuous process.
The Burner adjustment is okay with us & is workable, Can you please elaborate the adjustments with Primary Air & Quenching Air.
We shall definitely be thinking about appointing a Consultant.
Thanks
- Yamuna Nagar
June 20, 2019
A. Sorry Vikas, I saw your comment today only. Zn to ZnO is highly exothermic and hence you need to cool the ZnO formed as fast as possible. Any retention of ZnO at a higher temperature will spoil the surface area. (I think this was discussed by Umesh in detail earlier). That is where the use of high surface area classifier and use of quench air comes in picture. If a lot of air is supplied near the ZnO formation at the flame, quenching may not permit proper combustion of Zn to ZnO and higher free Zinc will be formed. But here you have one more degree of freedom, that is to pass quenching air by keeping a gap between the hood and the ducting. You need to to optimise these two, air passing through the bottom of the hood and air passing in the gap mentioned above. This will give you a balance between surface area and free zinc particles.
ABHAY NAGLESelf Employed - Vadodara, Gujarat, India
October 17, 2019
Q, A, or Comment on THIS thread -or- Start a NEW Thread