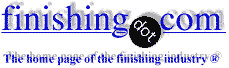
-----
Zinc oxide production by French process
May 28, 2008
Hi,
I am into Hot Dip Galvanising Business. I am planning to venture into Zinc Oxide and Zinc Sulphate production business. I have gone through the posting in the forum. They are invaluable.
As first information, I would appreciate if you could provide me information on
1) what amount of Zinc Dross would produce what amount of Zinc Oxide.
2) cost of machinery.
Keeping in mind, the plant would target a production of 150 MT/month of ZnO.
I would appreciate if anyone is aware of the same regarding production of Zinc sulphate.
Thanks in Advance.
- Hyderabad, India
June 3, 2008
Dear Umesh,
Thank you for the explanation on reasons for drop in Yield with use of HG.
as I understand if I begin with 95% pure Zinc Ingot, then effectively,
I should be able to get only 1: 1.15% Oxide Yield depending on the Pb & Fe impurities ?
also, I wanted to further enquire on process conditions which could help
reduce the Grit & Ash and improve the Yield ? should I reduce the charge/time/furnace ?
regards, Vinay
manufacturer - BKK -Thailand
June 11, 2008
Dear Mr. Vinay Dhawan,
Sir,
using dross in zinc oxide process is commercial decision. You can utilize most of metallic zinc from dross by avoiding skimming. for grit and heavy particles removal use gravity settlers effectively. You can get 99.7% zinc oxide from dross. in this process dross of 90% minimum can be used efficiently.
Process controls, variable settling systems will give good quality zinc oxide from dross.
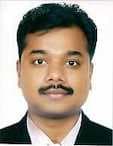
Umesh Charki
- Thane, India
Dear Umesh,
I agree to your views regarding Use of Electric furnace for ZnO production.However following issues are vital.First,Can All types of Zinc Dross be efficiently used in E-Furnace ? Or only Molten Zinc is to be transferred in the Furnace.
Secondly the Life of the Furnace and skilled manpower to run these e-furnaces,as mostly in India 99% furnaces are still Oil fired ones.
Lastly the availability of Continuous power of min 100 kW to run one furnace ?
Awaiting your views.
Thanks
- Alwar, Rajasthan, India
June 16, 2008
June 17, 2008
Dear Ankurji,
I am also working on electrical furnace. The power consumption is
800-900 KWH per Mt zinc oxide. This is single crucible furnace. Using heating elements. This resistance heating type furnace. You can operate as oil fired furnace. no special skilled workers are required. care is taken to deal with liquid zinc spillage, dust, crucible breakage detection etc. issues.
In some part of India electricity is no problem. Like in South India, you can install wind mill and get power from Electricity board. There are so many ways to go for non-conventional energy sources.
This is time to go for such things never thought in zinc oxide field.
Inputs are welcome,
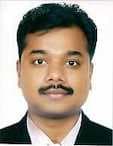
Umesh Charki
- Thane, India
we are manufacturing zinc oxide white seal from galvanising bottom dross. we are getting yield as 1 : 1.12 generally. we use furnace oil as a fuel and it generally takes 220 liters per ton of zinc dross. initially when crucible is new fuel consumption is lower but after using nearly 20 MT dross it takes more time as well as consumes more fuel. we use LAP 1 type burner and 3 HP 2800 RPM air blower.
can I do any modification in burner or air blower to reduce fuel consumption?
Director - Morbi, Gujarat, India
September 14, 2008
Dear Mr. Umesh Charki,
Thanks for clarifications on HG & Dross Yield.
now, we are looking to expand/add more 4 furnaces
& want to completely redesign our plant .
best regards, Vinay
Manufacturer - Thailand
September 29, 2008
October 22, 2008
Dear Friends,
Nice to meet you all..
We are Zinc Oxide manufacturer in Indonesia..
We want to know new information, innovation, research and maybe new application of Zinc Oxide..
I hope will get something important from this discuss for me to develop my factory in Indonesia.
Thank you for your kind attention..
Best regards
manufacturer of zinc oxide - Indonesia
Dear Mr Umesh Charki our company is a leading manufacturer in ceramic field. Currently we have a plan to produce zinc oxide from zinc with the total capacity of at least 1000 tons/months. If you are interested in cooperating with us, please contact me as soon as possible. I hope with your expertise we can save a great deal of time for not testing all the configurations.
- Vietnam
November 3, 2008
----
Ed. note: People have offered great info on this page, especially Umesh Charki. Thanks! Please remember that this site is made possible through the generosity of our supporting advertisers for camaraderie & public exchange of technical tips. Our advertisers are pleased to see this camaraderie and exchange of tips, but they obviously do not want their money spent putting potential customers into private contact with their competitors, nor steering people towards someone else's proprietary technology! Share what non-proprietary public tips you can, but if you want commercial benefit from this site, you need to become a supporting advertiser, not expect others to pay for your advertisements. Thanks.
Greetings Readers - For your information - The second International ZnO conference (organised by the International Zinc Association, Brussels) will be held at Rancho las Palmas, Palm Springs, California, USA on February 24th and 25th, 2009. We hope to build on the success of last year's meeting and we look forward to meeting readers again next year.
Best wishes,
- Fergus, Ontario, Canada
November 12, 2008
November 13, 2008
Dear Mr. Nguyen,
Installing plant with capacity 1000 MT/Month is good job. Before installing we should check for the quality required. So finalisation of plant setup and raw material can be specified.
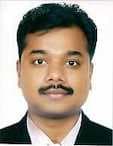
Umesh Charki
- Thane, India
December 12, 2008
Dear readers,
I'm just new into ZnO and we are putting up a plant in Haryana for Zinc oxide by French process and only source with virgin Zinc ingots. I have some Q regarding my project
1. How to get smaller particle size at least to introduce in pharma sector ? And does the diameter of cooling duct effect the particle size?
2. What are the other factors involved in particle size like , size of hood and duct, suction speed of blower , furnace temperature , and handling or packing ?
3. By which test I can get the surface area in M sqr / gram for zinc oxide?
I would appreciate for any answer.
Thanks .
- Delhi, India
December 15, 2008
Dear Suvneetji,
Zinc oxide particle size is depend upon cooling pattern of ZnO after formation. This is gas phase reaction with product in solid form.
French process limitation is to produce ZnO with surface area from 2 m2/ gm to 10 m2/gm with wide particle size distribution.
Hood design is also important as it gives such flow pattern to disperse and mix zinc vapour and atmospheric oxygen, just like combustion of fuel.
As this is gas phase reaction, partial pressures of reactants are also important.
You can measure surface area with BET method of nitrogen condensation.
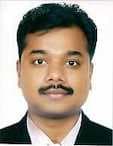
Umesh Charki
- Thane, India
December 17, 2008
Dear Mr.Umesh Charki ji,
Thanks for your reply. Sir, as you said we get surface area between
2-10 with wide distribution, but our requirement is for between 7-10, So Can you tell that what should be the proper separation to get maximum output of 7-10 and in what percentage we can expect out of total production.
On the other hand I want to ask is there any defined cooling system for cooling duct or it is naturally done. Presently we are getting
5-7 surface area.
One more thing what is partial pressure of reactants actually?
Hope to see you again.
Regards
- New Delhi, India
December 28, 2008
Dear Suvneetji,
French process can produce 2-10 Sq mt./ gm. But it requires different set of parameters. Generally this setup produces 4-7 sq.mt./gm. For higher surface area we need to design reaction in proper manner.
We are using natural cooling for this process as it is cheapest method available. And surface area is depend upon cooling rate to 450 °C; below this temp. surface area does not changes effectively.
Partial pressure is percentage of every reactant in reaction mixture for gas phase reaction.
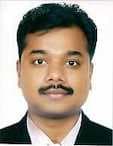
Umesh Charki
- Thane, India
December 30, 2008
Dear Umesh ji,
Thanks for your mail again,
we are putting up a new furnace of one crucible of capacity 800 kgs to get the better results.
I have a query regarding the distance between the top of the crucible and lower end of the hood. Does it help me to get the better results regarding surface area?
I want to increase the distance because to get the more air intake. presently we have 10-12 inches of gap.
If I put insulation on hood to keep it hot does it help me to get better results ?
Hope you have answers for that.
Thanks and regards
- New Delhi, India
January 1, 2009
Dear Suvneetji,
We install two crucible furnace to increase holding capacity of the furnace. Due to high holding capacity zinc dilution is possible for reducing lead content in product. In this case we can increase vapourisation time to increase productivity. Because more zinc we vapourise in 24 hrs will be add more production capacity with good fuel efficiency.
Distance between crucible top and lower end of hood defines velocity of the air at entry point. here high velocity results in better mixing of air and zinc vapours. the distance you are having is sufficient. For more surface area we need to cool down zinc oxide formed. More cold air will result in more quenching of zinc oxide formed. so you concentrate on the air volume to be suck in the system.
Putting insulation will damage the hood earlier, as it is made of MS and need to operate below 300-400 °C. And cooling of the zinc oxide is done by the air entering in the hood from bottom.
I hope most of the queries cleared,
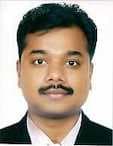
Umesh Charki
- Thane, India
February 20, 2009
Dear Sunil,
About energy consumption for French process of Zinc Oxide production, it ranges in a wide scope, from 120 L to over 250 L heavy oil per ton Zinc Oxide. Basically, the energy consumption is quite dependent on the furnace design.
During zinc oxide production, since the crucible wall is porous, the zinc vapor is trying to penetrating the crucible wall. This penetration accelerates especially when the furnace operates at very high temperature. And the penetrated zinc will oxide and deposit on the outside of the crucible wall. Once this deposit happens, the crucible will start to lower its thermal conductivity and fuel consumption will go up. So if you monitor the fuel consumption, you will find the fuel consumption is lower when the new crucible is used and after a few weeks the energy consumption will go up. In this case, an Isostatic pressed crucible with higher density/lower porosity will be better for French process.
For higher surface(higher BET) Zinc oxide:
zinc oxide produced from French process usually is lower surface area below 10 m2/g. However I believe it is possible to produce a higher surface area zinc oxide by French process. As said by Mr. Umesh Charki, French process for zinc oxide is a gas reaction, so it is quite possible to produce a higher Surface area ZnO by adjusting the parameters in the following reaction:
Zn(l) =>Zn(g)
Zn(g)+O2(g) =>ZnO(g)
ZnO(g) =>ZnO(s)
Such parameters as temperatures, pressure of Zn(g),O2 would be very important.
Normally these parameters are not controlled by the zinc oxide producers.
Hope this helps you.
- SuZhou, China
March 10, 2009
Dear all,
One of my client asked me to provide ZnO granules, can any one help me to develop the same?
Regarding my research I found that we can make granules by two ways one is pre dispersed and other is by palletizing, please advise with your best knowledge.
Thanks and regards
- Delhi, India
March 11, 2009
Dear Suvneetji,
Zinc oxide granules are less preferred in Indian market as no one is paying extra for granulated zinc oxide. There is no value addition.
Zinc oxide granulation is done by compaction (palletisation). white seal zinc oxide passed through rollers with 250 Kgs/cm2 pressure and formed flakes then broken in desired size. Here some times additives are used for particular applications.
Zinc oxide granulation by pre dispersed method is manufactured for particular application. As in rubber manufacturing rubber(elastomer) and zinc oxide is mixed in particular ratio and while compounding this ratio is adjusted.
As compaction granulation machine cost from 15 lacks to 1 crore. In India 2 or 3 manufacturers are doing this process.
Regards,
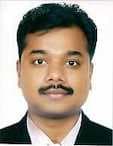
Umesh Charki
- Thane, India
March 17, 2009
Dear Sir,
I am researching about the production of ZnO from Zn(OH)2 I wonder if you could tell me what is the optimum calcination temperature. I worked at 650 °C but the mass loss was huge, not only the corresponding to the molecular mass difference between ZnO and Zn(OH)2.
Thank you very much for all your attention.
Researcher - Bilbao, Spain
March 31, 2009
Dear Mr. Diego,
In India, We are producing Zinc oxide by decomposition of Zn(OH)2. Actual decomposition temp. is 500-600 °C. But it contains sulfur compounds, which required 950 °C to decompose.
If mass loss is more than material balance. then review your calcinator design. It is normally rotary kiln with direct heating. But flow pattern inside kiln matters, as material carry over happens. Proper sizing and design of the furnace is important for desired results of conversion and yield.
In this issue I found good article on internet,
http://ntur.lib.ntu.edu.tw/bitstream/246246/92069/1/26.pdf
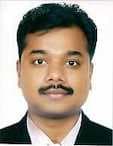
Umesh Charki
- Thane, India
April 8, 2009
Thanks for your all support.
As we are planning to make Zinc oxide granules, we don't know what kind of binder we shall use to have some hardness.
I want to try with st. acid, only worries is for that we have to melt S.Acid first during feeding into granulator, I have a query regarding the reaction between ZnO and S.Acid. Does it react enough to loose their basic properties as an activator in rubber compound.
Thanks and Regards
- Delhi
April 9, 2009
Dear Suvneetji,
stearic acid
⇦ on
eBay or
Amazon [affil link] and zinc oxide reacts but at 5 kg/cm2 pressure and 140 °C. This reaction forms zinc stearate melt. Or zinc hydroxide and stearic acid
⇦ on
eBay or
Amazon [affil link] directly reacts to produce zinc stearate in powder form. Zinc stearate used as lubricant in tire manufacturing.
Mixture of both compound is not reactive.
Binder materials used in zinc oxide are as per application. These materials used less than 1% in zinc oxide. You can try natural gum in dilute form. and sprinkle it in rotary drum filled 30% with zinc oxide. this is one type of granulation I have seen; but after it is to be dried.
Regards,
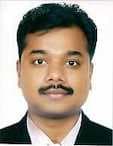
Umesh Charki
- Thane, India
sir,
Now our company is dealing with zinc oxide that is being produced through French process.the company is going for expansion and is looking to introduce new methodology in this field.
The company is looking for introducing new method of production .it is planning to introduce active zinc oxide, but we are not able to get the technical know to produce active zinc oxide
Please help me this issue...
Thanking you
- Bangalore, Karnataka, India
February 6, 2010
June 11, 2010
Respected Sir,
I am chemical engineer working in zinc oxide plant, as plant manager. We are using French process for zinc oxide production. Our capacity is 10,000 TPA I would like to know more about French Process, with respect to productivity, controlling, cost and environmental cares.
Please do the helpful, thanking you
Sattari
product designer - IRAN
June 16, 2010
Dear Mr. Sattari,
This is the same message I posted at start of this discussion. If it the same question from your side, then it is very difficult to answer in one answer. You can go through the total discussion to understand different aspects of zinc oxide manufacturing.
In case of any specific question, please ask.
Thanking you,
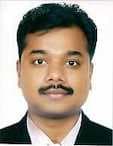
Umesh Charki
- Thane, India
----
Ed. note: Exactly, Mr. Charki!
Mr. Sattari: Please study the thread and feel free to ask any questions which will keep the discussion moving forward. But this thread has thousands of readers, and it would be unfair to them to simply run them in circles :-)
June 16, 2010
Thanks to one and all for the information you are providing on this forum.
I am planning for 1000T capacity Zinc Oxide plant, can I get some information like
1. Who can do the erection and supply the machinery for manufacturing ZnO
2. Rough estimation for 1000T capacity
3. Whether to go for 500T or 1000T capacity
Thanks,
Sai
- Hyderabad India
Dear Sirs,
I would like to know, what is the common process used to convert galvanizing zinc ash/dust into zinc oxide with higher purity. Is the only way to do it hydrometallurgical, or are there pyrometallurgical ways to achieve the above.
Thanks in advance for the answers.
Regards,
Hemanth
- Lagos, Lagos, Nigeria
June 22, 2010
Our consumption of furnace oil is 225 liters in manufacture of Zinc Oxide. Please help us on how to reduce the consumption?
sahil guptatop management - haryana India
December 20, 2010
January 8, 2011
To reduce furnace oil consumption, Furnace should be developed to save heat energy. This is done by proper designing of furnace, suitable and good quality insulation of furnace, Proper temp & pressure of furnace oil, Heat saving equipment such as heat regenerators in furnace.
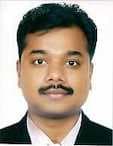
Umesh Charki
- Thane, India
Can we manufacture zinc oxide without crucible?
Irfan Darogha- Gujranwala, Punjab, Pakistan
February 9, 2011
February 5, 2011
Sir,
any one can tell me whether zinc oxide powder can be packed by automation.
If so, please inform the details.
engineer - Chennai, T.N . India
February 16, 2011
Dear Sir,
1)For My query about 'crucible-less furnace' I got more information From Dr. Peter Robinson (Canada)As follows,
ZnO will be produced in the furnace due to the Boudouard reaction-
Zn + CO2 = ZnO + CO
This reaction is at equilibrium at around 950 C, at higher temperature, formation of Zn metal is favored.
Presence of ZnO will make process very difficult to control because there will be a cold interface with the liquid zinc.
Only direct heat method that I know of that is working is the Larvik furnace. This uses a resistance element above the zinc liquid. Cost of electricity is prohibitive in most cases.
I believe crucibles are the most cost effective route to ZnO. Crucibles need to be large, semi continuous liquid charged and configured for regenerative heating.
I believe crucibles are the most cost effective route to ZnO. Crucibles need to be large, semi continuous liquid charged and configured for regenerative heating.
2)We can pack zinc oxide in automated system, only we have to workout on economy. Presently we pack 25Kg oxide precisely in HDPE bags. Machine with this kind of precision is costly. We use 2 labors for oxide unloading, packing, weighing and stacking 5 MT oxide per 12 hr. shift.
This is possible by proper and simplified mechanization of system.
Hope your queries are solved,
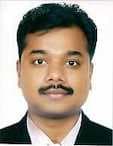
Umesh Charki
- Thane, India
February 22, 2011
Sir
We currently have installed capacity of 300 MTs per month.
Can we run 2 furnaces with same capacity together ? If yes is there any other change to be made in the plant & machinery.
Ritesh Kumar
manufacturer - Karnataka
Thanks you all as the discussion is going to be interesting, I would like to know how to controlled insoluble particle in a acid solution. we have customers having specification of CLEAR SOLUTION , it is very difficult to obtain clear solution.
Ravi RajputManager Q.A. - Palghar
March 11, 2011
March 14, 2011
Dear Mr. Ravi,
Insoluble are dust and ash in zinc oxide. This impurity is mixed with zinc oxide at suction point on furnace. You can avoid insolubles easily by following steps,
1) Maintaining clean furnace area, ash free.
2) If using furnace oil, try to block and avoid black suit generations and leakage at furnace top.
3) Avoid skimming, crucible cleaning when process blower is on and suction on furnace.
These are easy steps in operations to avoid insolubles. Also you can use settlers efficiently to separate heavy impurities.
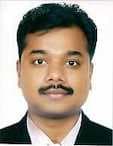
Umesh Charki
- Thane, India
I am interested to learn more about controlling factors in running a furnace to manipulate the ZnO powder produced, especially in the parameters of lower particle sizes and with low surface areas at the same time. I know there are a few different crystal structure of ZnO particles which would explain why I am currently only able to manipulate my surface areas but always in the combination of larger particles giving lower surface area but smaller particles having higher surface area. What I need to produce is smaller particles size with low surface area.
what kind of furnace and suction blower parameters do I need to control?
- Rawang, Selangor, Malaysia
June 15, 2011
August 24, 2011
Dear all.
I'm a student and I'm trying to produce zinc oxide from an electric arc furnace dust. I actually have zinc hydroxide and I want to furnace that, but I'm not sure of what temperature is the best to do it, can anybody help me, please?
Thank you!
- Monterrey, Nuevo Leon, Mexico
August 29, 2011
Dear Mr. Daniel Palacios,
There are two different things you are asking for?
1) electrical arc furnace dust contains Fe, Zn, Ca, Si etc. Out of which Zinc (in oxide form) is vaporized after carbothermal reduction and further oxidation to zinc oxide. this is done in Wealz process in rotary kiln. This process increases concentration of Zinc content and separate it from Fe impurity. Wealz zinc oxide is further processed to get electro zinc or zinc chemicals.
2) To convert zinc hydroxide to zinc oxide, we use rotary kiln and temp. required for hydroxide to convert to oxide is @ 480 to 550 °C. In certain cases if hydroxide contains sulfur then temp rises to 950 degree to remove sulfur compounds.
For more queries you are most welcome,
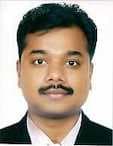
Umesh Charki
- Thane, India
Q, A, or Comment on THIS thread -or- Start a NEW Thread