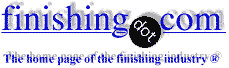
-----
Optical matte black anodize on aluminium
Q. We are building a satellite (a student project, as follow-on to SUNSAT 1) and have problems in obtaining a matte-black finish on some of the aluminium (7075) parts of a telescope (lens mounting rings and baffle).
Lord Corp. Aeroglaze Z306 will work for the baffle, but the mechanical engineers would like to Anodize some of the internal parts of the telescope, as they are scared that Z306 might outgas, and being close to the CCD, might condense on it. The baffle, being an open structure, can vent to the 'outside' and even if some (however little) condensation does take place on the exterior first lens element, is would not be on a focused surface (as would be the case with the CCD).
The problem is how to obtain a matte-black, non-reflective anodize surface. The normal dyes used to color anodize aluminum Black is organic, which is likely to outgas and might not be stable under UV exposure.
Do you have any experience or suggestions in this regard?
Kind regards,
Francois Strumpferelectronics systems lab. - Stellenbosch (near Cape Town), South Africa
2001
A. Dear Francois,
There are dyes that are commercially available that have excellent lightfastness characteristics. There are also inorganic dyes that are available in black. As for your requirement for a matte finish, this can be achieved by using a proper etch prior to anodizing. If there is a specific reflectivity requirement, then I would suggest processing some test panels prior to actual production.
Best of luck.
Ira Donovan, M.S.F.Kansas City, Missouri
2001
A. Hi,
We once did some satellite bits for a space telescope.
We used nickel acetate dip then ammonium sulfide to convert the nickel to nickel sulfide.
It works but take my advice and do not try this method, the hydrogen sulfide gas is toxic and the stuff of stink bombs.
As it worked out the parts never got to space due to the rocket having the wrong control system and was blown up.
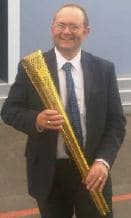
Martin Trigg-Hogarth
surface treatment shop - Stroud, Glos, England
2001
A. Dear Francois,
I would suggest using the two step (non fade) inorganic black anodize or the Type II black anodize finish. Are there specific reflectivity and emissivity requirements? If so, you should run some test panels and check the optical readings. We at Highland have plated and anodized baffles, propulsion systems, field rings, field stops, etc.. We helped many engineers, like yourself, achieve the right amount of thermal control. We have optical instruments in house that can take the reflectivity and the emissivity readings. Depending on the process and the material, you can achieve anywhere from 0.05 - 0.3 reflectivity and 0.85 to 0.9 emissivity reading.
Best Regards,
Andrew Boussarath- Los Angeles, California, USA
2001
Multiple threads merged: please forgive chronology errors and repetition 🙂
2002
Q. Dear Gentlemen,
I am in the process of setting up a small lighting manufacturing firm here in Mexico.
For the production of the required parts I found a couple of job shops, among them an anodizing firm.
Now I encountered following problem:
Some of the required parts have to be machined in mills and lathes, the cutting process generating heat in the material.
Since I want the surface to have a matte appearance, I encounter the problem that with the anodizing process for a matte appearance, on the machined parts there appear the crystals as small shiny spots, which is undesirable.
Can anyone tell me the correct process of matte anodizing of machined parts which have suffered heating during the cutting process, so no spots will be visible?
Thank you very much,
Hans J. Preisendanz- Mexico, D.F. Mexico
A. Matte anodize can be achieved by matte etching the aluminum prior to anodize. Typically done with either warm caustic soda ⇦liquid caustic soda in bulk on Amazon [affil link] bath or warm fluoride acid bath.

Milt Stevenson, Jr.
Syracuse, New York
2002
Q. Dear Milt, thanks for your reply.
This is what my anodizer did. The result is that now there is a bunch of silvery shiny spots on the matte surface which are absolutely undesirable. My anodizer tells me that this comes from the crystalline structure showing up because the structure suffered some changes due to the heat generated during machining (turning).
So for the moment I am still with the question on how to achieve an evenly matte anodized finish on machined (turned)parts. I am looking for a finish just like the one used on some of the trendy european watches.
Hopefully someone can help me resolve this.
Thank you.
Hans J. Preisendanz [returning]- Mexico, D.F. Mexico
2002
? WHEN YOU SAY THERE ARE "CRYSTALS" ON THE ALLOY SURFACE, DOES THIS OCCUR AFTER MACHINING, OR AFTER ANODIZING?
MARK DEWITT- ROCHESTER, New York
2002
Q. Dear Mark, according to my anodizer, these crystals form because of the heat generated during machining. However they are not visible after machining. They become visible after the matte anodizing process where caustic soda ⇦liquid caustic soda in bulk on Amazon [affil link] is applied to etch the surface for a matte appearance.
Hans J. Preisendanz [returning]- Mexico, D.F. Mexico
2002
A. Hi,
6061 tends to show a crystalline grain structure when over-etched. Try mechanical surfacing (tumble,etc.) and then anodizing WITHOUT caustic etch.
Good luck,
Bill Grayson- Santa Cruz, California, USA
2002
A. Hans,
If your machinist is generating enough heat to affect alloy properties, I would look for another machinist. Being in the anodizing business for almost 20 years, I think the problem lies with the matte etch process. I can tell you that it is a very difficult etch to produce desirable and consistent results . The "spackled" finish is usually the result of over-etching. While machining does generate some heat, the trick is to achieve a matte etched surface that is also cosmetic. I have used a nitric acid/ammonium bi-fluoride/water mixture at low temperature to achieve a cosmetic matte surface for black anodized optical components. However, different alloys produce various degrees of "matte" than others. Obviously, the more aluminum content, the better results you will see. The other variable is experience. If your anodizer is new to producing a cosmetic matte anodize, it may take some time to research and test etching processes, alloys, machining operations and patience to finally get the results you want.
Good luck!
Mark DeWitt- Rochester, New York
2002
2002
Q. Dear Bill,
I did glass bead blasting with 200 mesh glass beads, obtaining a wonderful surface. Only new glass beads where used and the sandblast booth cleaned thoroughly before, to avoid contamination.
I then asked the anodizer NOT to etch the part, only deox and anodize it. The result is that the part turned out awful dark gray. We then put the parts in caustic etch for 20 seconds and again they came out matte silver. so far so good. Only after anodizing the crystalline structure became visible again, although only very slightly, but still visible.
My questions now:
1.- Does this dark gray/brownish color come from the residual silicon building up in the pores after glass bead blasting? If so, how can this be removed before bringing the parts to the anodizer?
(Mechanically/Chemically) The anodizer wouldn't install a deox line with ammonium bifluoride for small quantities of parts.
2.- Is it recommendable to further lessen the etching time? How much time would be minimum to avoid showing up these crystals after anodizing and removing any silicon from glass bead blasting?
Is there anyone having similar problems?
Any advice or information is very welcome.
Thank you in advance.
Hans J. Preisendanz [returning]- Mexico, D.F. Mexico
A. Hans, during anodizing, the substrate is dissolved during formation of the oxide film. 1. A warm/hot anodize tank 2. too high current densities applied 3.mixing parts in a tank load to optimize production 4.using titanium racking vs. aluminum racking 5. if the anodize tank is lead lined or if cathode square footage greatly exceeds parts square footage 6. poor tank agitation ... all these factor in to excessive surface loss (and your bead blast finish). If your part looked good after a 20 second etch and acid de-ox, my hunch is one or more of the above conditions exist. You never mentioned required coating thickness or if the anodize is functional or cosmetic. If it is merely cosmetic, a thin oxide film under strict conditions, your anodizer should be able "customize" his process to produce acceptable, fairly repeatable parts.
Mark DeWitt- Rochester, New York
2002
Multiple threads merged: please forgive chronology errors and repetition 🙂
Need to achieve an 'optical matte black anodize finish'
October 2, 2009Q. Hello. I need to anodise an aluminium plate 1 mm thk with a matte black finish. It is to be used as an optical mask and therefore needs to be as black and matte as possible. Any advice for specifying the finishing process it terms of
- material surface roughness
- thickness of anodise
- dyes used
- etc
thanks
astronomy engineer - UK
![]() |
October 5, 2009 A. Graham, ![]() Harry Parkes - Birmingham, UK A. Dear Graham, "astronomy engineer": - Incheon, South Korea October 5, 2009 |
Matte Black Anodization
Q. I am located in India and making mechanical components of aluminium for companies in Europe. The components are perfect as far geometrical parameters are concerned. But I face problem when I get them anodized. The buyer wants them to be matte black. My anodizer only does glossy finish and does not know the process for matte finish. I need help on this point how to get matte finish (non-reflecting optical quality).
Thanks
workshop owner - Ambala Cantt, Haryana, India
September 14, 2019
Ed. note: This RFQ is outdated, but technical replies are welcome, and readers are encouraged to post their own RFQs. But no public commercial suggestions please ( huh? why?).
A. Hi Naresh. I think you probably ought to either find another anodizer who knows how to do it, or at least ask your anodizer to investigate for himself how to get matte black anodizing instead of doing it for him because such situations involve a lot of "ifs, ands, & buts" -- for example, whether he can add another tank for etching, whether he can add a separate dye tank, what alloy is being anodized, whether the parts are racked vs. anodized in a basket, whether his line is set up with a bright dip he can't conveniently skip, whether it's practical for him to bead blast before anodizing, what chemicals he is allowed to use, whether he has a reflectometer, what your customer means by "matte" (just reasonably non-shiny vs. for use in optical devices), whether he'll need a different seal process, etc.
But we've appended your inquiry to a thread which discusses matte black anodizing, and we have several more including:
Topic 1210, "Simple method of black anodizing aluminum wanted"
Topic 4581, "Optical Black Anodize / Martin Black" and
Topic 42754, "Anodizing to a matte black finish"
Best of luck with it, but almost never is it as simple as "do this" or "don't do that".
Regards,
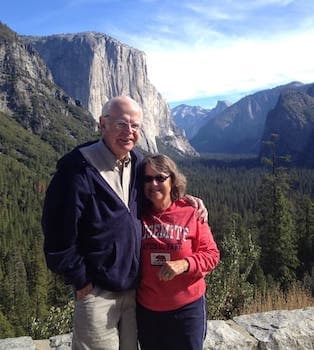
Ted Mooney, P.E. RET
Striving to live Aloha
finishing.com - Pine Beach, New Jersey
September 2019
Thanks.
Naresh Kumar [returning]- Ambala Cantt, Haryana, India
September 18, 2019
Q, A, or Comment on THIS thread -or- Start a NEW Thread