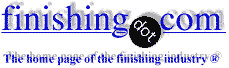
-----
Acid Copper Plating issues Q&A

⇦ Tip: Readers want to learn from your situation;
so some readers skip abstract questions.
Q. Sir ji, my plating is very slow. I use copper sulphate ⇦ on eBay or Amazon [affil link] 250 p/l and s.acid 50 p/liter.
Sanjay verma- delhi, India
January 28, 2022
A. Hi Sanjay. You've given us no introduction to your situation. Assuming you are a professional production plater with acid copper plating experience who has suddenly experienced a big drop in plating speed, it's probably polarized anodes.
Luck & Regards,
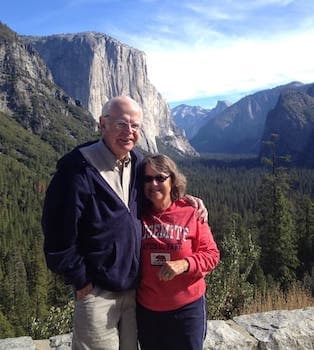
Ted Mooney, P.E. RET
Striving to live Aloha
(Ted can offer longterm or instant help)
finishing.com - Pine Beach, New Jersey
⇦ Tip: Readers want to learn from your situation;
so some readers skip abstract questions.
Q. Hi sir, I'm Sanjay Verma from India. Sir I use acid copper plating: my acid bath is very slow. I use 250 g/L copper sulphate and 50/L. I want my plating fast and thick. Help me.
Sanjay verma [returning]- delhi, India.
March 26, 2023
A. Hello again Sanjay. Your copper sulphate is slightly high, but I doubt that that is the actual problem. As I said last time, my guess is that the problem is polarized anodes (what happens, as I understand it, is that the anodes dissolve too easily, building a highly concentrated syrup of copper sulphate around them which does not easily pass electricity, so even with the voltage turned up, little current flows).
What is your chloride concentration? And please tell us the specification for your anodes. And give us some background are you a hobbyist or in a professional plating shop? Did your shop once plate much faster? Thanks.
Luck & Regards,
Ted Mooney, P.E. RET
Striving to live Aloha
(Ted can offer longterm or instant help)
finishing.com - Pine Beach, New Jersey
⇩ Related postings, oldest first ⇩
Lack of ductility in acid copper plating
Q. We are experiencing inconsistency when plating acid copper on lead projectiles in a barrel application. Process is as follows: cathodic clean, acid, cyanide copper strike, acid copper plate. Plating thickness required is 3 to 5 thousandths. Randomly we have ductility problems with the acid copper. The deposit seems to become brittle and adhesion is questionable. We have noticed that the higher the temp in the acid copper the better the ductility. 110-120 °F. The supplier of the brightener system recommends 75-85 °F.
George Wulfplating - Miami, Florida
2001
A. I think you need to give data on composition of acid copper bath. Give also current density used, Cl content. Have you tested hardness of deposit? How pure is your bath with contamination? Lower temperature is better for acid copper as recommended.
Payal Mag- Charlotte, North Carolina
A. The last time I heard this problem it was in Miami and it was bullets. A barrel had dumped a load of lead into the tank. In the Hull Cell ⇦ huh? we did have an additive to handle the excess amount of lead. Lead is only slightly soluble in sulphate, but more so in the presence of current. Get your supplier on the phone and ask him how to handle an excess amount of lead.
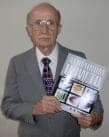
Robert H Probert
Robert H Probert Technical Services

Garner, North Carolina
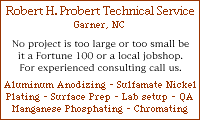
Acid copper is treeing
Q. Recently we have increased the acid content from 80 g/l to 200 g/l in our acid copper plating tank. This was done to improve throwing power (plating of printed circuit holes). The deposits we desire are non bright and smooth up to about 100 microns. However, since the addition of acid the deposits became very rough and treeing is visible. Copper content is 20 g/l. No additives or chloride have been added because originally when acid was low, we found the deposits to be relatively smooth. Cathode CD ranging from 1 to 2 A/dm^2 has little effect. Could the absence of chloride ion be responsible for tree growth ? Are additives essential for smooth (non bright) deposits in high acid baths? Would anyone recommend reverse pulse plating as a solution ?
Adam Seychell- Melbourne, Australia
2001
A. I have never seen circuit boards plated in an acid copper bath that did not have additives. Does not mean it cannot be done. Temperature should be 70-90 °F. You should have phos-copper anodes, not pure copper anodes.
An additive promotes smooth copper deposits, assists plating in thru holes, assists in trying to obtain 1:1 thickness in the hole to the surface of the board. If you use an additive, the chloride must be present at 70-90 ppm. Don't know if no chlorides in your bath is the problem.
Should be using oil free air agitation. Side to side movement of the plating rack helps. Pulse plating may help, more expensive than standard rectifier.
Bill Hemptech svc. w/ chemical supplier - Grand Rapids, Michigan
A. You did not need to add so much sulfuric. You can turn the current down some. Adjust a little at a time. Move your anode around some, away from trees to low spots. If you will calculate the total sulfuric and in proportion add copper sulphate and distilled water, you should come out with approx. 240 g/l copper sulphate and 60 g/l sulfuric. If you do want to try chloride then separate a liter from your revised bath and try 0.08 g/l chloride. Try this first before you add to entire bath. Make sure you have air beneath the object in large bubbles. Use a very small amount of a mild liquid soap. Very small at a time. Try in the 1 liter bath first till you get the results you need. Mainly reduce the current density. Approx. 1/10th amp per S.I..
Clinton Driggars- CELINA, Texas
Thanks Clinton & Bill for replying to my post. All the recipes I've seen for printing of circuit boards plating recommend a high acid and low copper bath. Something on the order of 200 g/l H2SO4 and 60 g/l CuSO4.5H2O. Going by my experience it may be such baths require additives for smooth deposits. I have now contacted a local supplier for additives.
One interesting outcome with the change to high acid low copper bath was a significant improvement in hole wall plating. We are currently experimenting with our own carbon black method for preparing the holes for plating, and found the plate-ability over the carbon surface depends greatly on the bath throwing power.
Adam Seychell [returning]- Australia
A. Both previous answers are correct. Lack of Cl will cause treeing in high c.d. area. Keep CuSO4 180-220 g/l and H2SO4 60-75 g/l. Some call it maintaining a ratio of three. Avoid any contamination of Fe, Cr.
Payal Mag- Charlotte
Q. Sorry, I'm getting slightly confused. Are we mixing up the numbers ? My local plating supplier recommend 180-220 g/l of H2SO4 and around 60-80 g/l of copper sulphate. An online article on copper plating also shows similar ranges.
Is it sulfuric acid or copper sulphate that should be 180-220 g/l ?
Adam Seychell [returning]- Melbourne, Australia
A. There is obviously some confusion here and it is likely that decorative acid copper formulations are being mistaken for printed circuit ones. The high metal/low acid variety would generally be used for decorative baths and the low metal/high acid type are used for printed circuit boards. The low metal concentration limits the current density that can be applied to the boards but the high sulfuric acid content certainly makes this blend effective for building a thickness of copper in the holes about equal to that which is plated onto the face of the boards. And, the additives become very critical in the production of fine grained and ductile, low stress deposits.
Larry Abbott- New Berlin, Wisconsin
August 14, 2009
Removing excess chloride from bright acid copper plating solution
Q. I have trouble in my bright copper acid solution: an excess of chloride ion (124 ppm), how to lose the chloride ion to stabilize the solution?
Thank you,
mirzal
- siantar, north sumatera, Indonesia
June 12, 2014
A. Hi Mirzal. To my limited knowledge there is no practical way (except dilution) to remove them from an acid copper plating solution. Although silver chloride salts are insoluble, it may not be an economically feasible answer.
As a matter of curiosity though, I see that CuCl is insoluble, and that there is a laboratory method to precipitate it from the soluble CuCl2 by adding copper powder and steam, while excluding air, then filtering it out. See, for example, www.inc.bme.hu/en/subjects/genchem/chlorides.pdf
If there is a more practical way to remove chlorides, or if anyone has attempted this "CuCl2 + Cu -> 2CuCl" method, please advise. Thanks.
Regards,
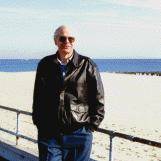
Ted Mooney, P.E.
Striving to live Aloha
(Ted can offer longterm or instant help)
finishing.com - Pine Beach, New Jersey
1) BRIGHT ACID COPPER PLATING
COPPER SULPHATE = 200 TO 250 G/LR OPT. 225 G/LR
sulfurIC ACID = 45 TO 65 G/LR
CHLORIDE = 40 TO 80 PPM
ADDITIVES FOR LEVELING & BRIGHTENING.
2) HIGH THROW ACID COPPER PLATING (MOSTLY USED FOR PCB FOR 1:1 RATIO)
copper sulphate = 75 TO 100 G/LR
sulfurIC ACID = 90 TO 110 G/LR
CHLORIDE = 30 TO 70 PPM.
ADDITIVES FOR SMOOTH LEVELING.
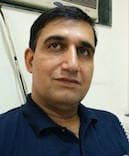
Ajay Raina
Ludhiana, Punjab, India
June 16, 2014
A. There is quite a lot of information on the internet concerning the removal of chloride from acid copper baths.
Although I have never done this, the most common method seems to be the addition of a silver compound, usually silver nitrate, silver sulphate, or silver carbonate. A silver nitrate solution would be the most convenient but the nitrate ion would remain in the bath and I don't know how this would effect the plating. In any case, 3.04 grams of silver would precipitate 1 gram of chloride, in the form of silver chloride, AgCl.
Another method that was mentioned in two references was the use of zinc dust
⇦ on
eBay or
Amazon [affil link]
in exact amounts. This would reduce some of the copper(II) to copper(I), which would then precipitate some of chloride as cuprous chloride, CuCl.
In any case, the precipitate formed would have to be completely removed by filtration before using the bath. Otherwise, any remaining in the bath would most surely produce roughness on the plated parts. It would be best to treat the solution in a separate treatment tank. In one reference, a 5 micron filter is suggested for the removal of the precipitate.
If it were me, I would first try one or more of these methods on a small portion of the bath, say a liter or so.
- Nevada, Missouri, USA
A. Silver sulphate works. Other than the expense, this is a reliable method to remove excess chlorides. High chlorides increase stress in the copper deposit.
Lyle Kirmanconsultant - Cleveland Heights, Ohio
June 23, 2014
Haze in LCD area in Acid Copper Plating
Q. Have an issue with one of our Acid Copper baths, in that a dull haze has been seen in the LCD area on a Hull Cell panel. Work has so far remained unaffected, but want to stop this problem before it manifests any further. Have dummied the bath out for 14 hours @ 5ASF, as chemical rep. thinks it may be metallic contamination, and the haziness has got better, but there's still some there. It's also had full carbon treatment and dummying prior to this 14-hour dummy plate.
It's been suggested that our Nickel Sulphamate bath (running with air @ 56 °C) that is near the acid Copper bath may be atomizing and mixing with the Acid Copper solution. Should I be dummying out at a low CD, or should I set the CD to the same as we use when we're actually copper plating (conflicting information on the internet)? Also, will the Nickel Sulphamate have any other impact on the Acid Copper solution, bearing in mind the Nickel Sulphamate solution itself has NO wetters, brighteners, or levelers added to it (i.e. no organics in it - we run it like this to achieve the correct hardness of Nickel plate)?
Process Controller - Chelsmford, Essex, UK
August 8, 2014
Q. We have a Acid Copper Bath that is 16.8 oz/gal of sulfuric acid and 8.7 oz/gal of copper. Can we reduce the sulfuric to 8 oz/gal without diluting the tank.
Thanks,
- Winston-Salem, North Carolina
October 5, 2017
Q. I am copper plating steel plates in acid copper bath. Process sequence: ultrasonic soak cleaner, cathodic/anodic, nickel strike; after that cyanide copper and then acid copper.
The problem which I am facing is that small shining star-like structures appear on the surface of steel.
(Actual results differ from the picture. Stars have less reflectivity. Following results are due to reflectivity of flash light)
Are these stars formed due to impurities or too-short plating time?
These stars reflect after bright nickel plating.
How to remove these stars?
Is it due to brighteners and levelers, micro impurities in the bath, or excess or insufficient chloride?
Kindly help me out in this regard.
I face these star-like patterns even on copper plating on zinc die castings.
- Jalandhar, Punjab, India
October 14, 2017
A. SHARMA,
STAR PROBLEM AFTER NICKEL PLATE, SURFACE OF THE PARTS ARE SMOOTH OR ROUGH,DID YOU CHECK YOUR UNPLATED PART FOR ANY DEFECT.IF SURFACE IS SMOOTH YOU HAVE PITTING PROBLEM AND ROUGH DEPOSIT NICKEL , TOO MANY REASONS.CHECK YOUR CHEMISTRY IN YOUR TANKS.
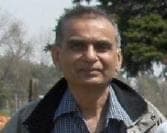
Popatbhai B. Patel
electroplating consultant - Roseville, Michigan
Q. Hello sir,
Acid copper after raw part surface comes dots. How to trouble shoot acid copper bath? We already do dummy plating for a long time and carbon treatment. No improvement ... same.
Process engineer - tamilnadu, India
February 14, 2018
by Larry Durney
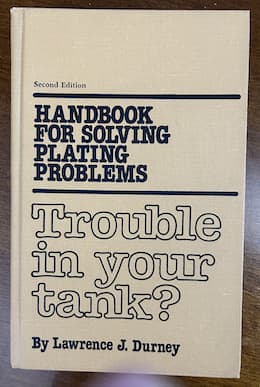
on eBay or Amazon
or AbeBooks
(affil link)
? Hi Praveen. Please try to send us (mooney@finishing.com) some pics of these defects and more data about what you are doing. There is obviously a lot involved in achieving satisfactory plating, and we know nothing of your situation yet except that you do acid copper and get some sort of dots. Thanks.
Re. how to troubleshoot: The Canning Handbook [on eBay, Amazon, AbeBooks affil links] has chapters on the operation and trouble shooting of the various plating baths, and Larry Durney's "Trouble in Your Tank" is the authority on the topic. Good luck.
Regards,
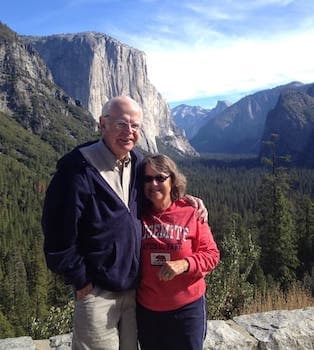
Ted Mooney, P.E. RET
Striving to live Aloha
(Ted can offer longterm or instant help)
finishing.com - Pine Beach, New Jersey
Filter/pump disintegrating in acid copper solution
Q. I have an acid copper electroplating tank that I bought from a hobby plating supplier. I have had 3 of my aquarium filter/pumps that I use to filter and agitate the solution disintegrate at the impeller (including the one that was supplied with the kit). Has anyone else experienced this problem and know what the cause is? (I remove and rinse my filters after each plating session). Is it possible that the acid is weakening the plastic in the impeller (which is white - different to the rest of the filter body which is black plastic)? And if so are there brands of filters that will hold up to the acid?
Many thanks,
Micha
- Melbourne, Victoria, Australia
September 7, 2018
A. Hi Micha. I would guess that the impeller is nylon, which is not really acid resistant like the other inexpensive plastics polyethylene, polypropylene, and PVC ... or that there is a glued joint which doesn't stand up.
I'm sure you recognize that aquarium pumps are designed for aquariums not for plating solutions. There are many brands of plating filters, all of which will stand up to years of constant immersion, but even the cheapest will cost an order of magnitude more than an aquarium filter. We don't recommend or slam particular brands here (why?), but you might look for something advertised as all PVC or all polypropylene, or with readily available replaceable impellers.
Regards,
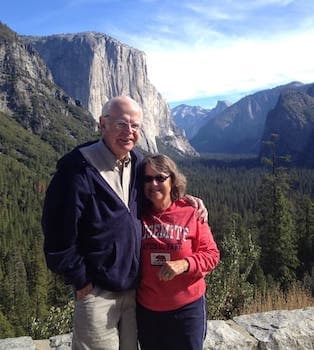
Ted Mooney, P.E. RET
Striving to live Aloha
(Ted can offer longterm or instant help)
finishing.com - Pine Beach, New Jersey
Thanks Ted, makes sense.
Best,
- Melbourne, Victoria, Australia
September 7, 2018
Ductility issue in acid copper plating
Q. How to check ductility in acid copper plating. Any method / any measurement?
Shinde Shankar rao- SANGAREDDY DISTRICT, India
September 27, 2018
A. Hi Shinde. ASTM B489 "Standard Practice for Bend Test for Ductility of Electrodeposited and Autocatalytically Deposited Metal Coatings on Metals" might be useful. And it's possible that ASTM B490 "Standard Practice for Micrometer Bend Test for Ductility of Electrodeposits" could help too.
But if the plating is not done to a spec which mentions its compliance tests, I'm not aware of any "standard" tests that would be demanded. Are you the plater or the buyer? Are the parts small enough, and produced in sufficient volume that destructive testing is not a concern? If so, ad hoc testing is common but depends on the parts. Crushing in a vice, wrapping around a mandrel, and sawing can be combination adhesion & ductility tests. Best of luck.
Regards,
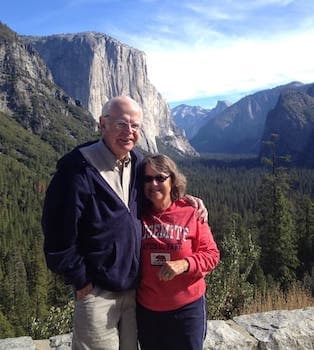
Ted Mooney, P.E. RET
Striving to live Aloha
(Ted can offer longterm or instant help)
finishing.com - Pine Beach, New Jersey
Acid Copper Plating in Barrel
Q. We are a Pakistan based company and want to do Acid Copper in Barrel.
Anyone who has knowledge of Acid Copper in Barrel please guide.
As when we do small articles like brass it does not plate, but if we do heavy parts then it gives shining result but takes lots of time.
Looking for help.
- Lahore, Pakistan
February 15, 2020
A. Hi Malik. Heavy parts taking "lots of time" is relative. What thickness do you want and what current density are you using for how much time; then we can help you figure out if something sounds wrong. Perhaps the problem is only in your expectation that plating should be achievable in less than reasonable time?
The lighter parts are quite possibly fluttering down through the solution, not contacting the cathode enough, rather than sitting in the bottom of the barrel in contact with the danglers. Try lowering the solution level and/or reducing the barrel rotation speed. Or the small brass parts may have greater surface area and therefore not enough amperage for bright plating.
Luck & Regards,
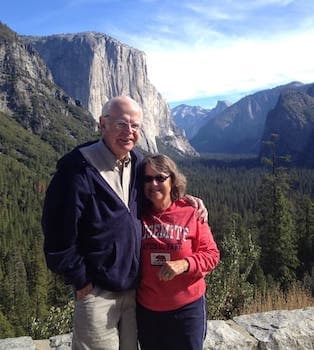
Ted Mooney, P.E. RET
Striving to live Aloha
(Ted can offer longterm or instant help)
finishing.com - Pine Beach, New Jersey
November 2020
Q. Hello,
I want to enquire the maximum current density that I can run my acid copper tank at?
Wanted to check if acid copper tank can plate copper at 50 Amps/dm^2 current density.
Awaiting for your prompt response.
- Ahmedabad India
April 30, 2021
A. Hi Tirath. Sorry, but the answer is heck no, nowhere even close. Unless there is something quite special about your installation like high pressure impingement of plating solution, you would have to be quite lucky to achieve even 10% of that.
Luck & Regards,
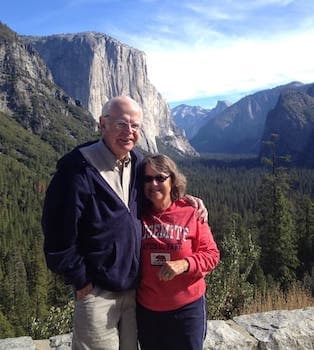
Ted Mooney, P.E. RET
Striving to live Aloha
(Ted can offer longterm or instant help)
finishing.com - Pine Beach, New Jersey
Q. What do think is the best neutraliser for rinsing after acid copper plating. I am using soda crystals,
Looking forward to your advice.
Daniel
- Belfast Ireland
June 1, 2021
A. Hi Daniel.
I am personally unfamiliar with neutralizing acid copper. In my experience you don't neutralize if there will be subsequent plating, for example nickel plating or tin plating; and if there will not be subsequent plating, it is often best to dip in a proprietary sodium benzotriazole ⇦ on eBay or Amazon [affil link] anti-tarnish, although proprietary chromate-based anti-tarnishes are occasionally used. Then again those things probably shouldn't be used for kitchen items unless they will be lacquered.
Please introduce yourself and describe what you are plating. Unfortunately, there's rarely a good answer to abstract questions -- the answer is usually "depends whether ..." :-)
Luck & Regards,
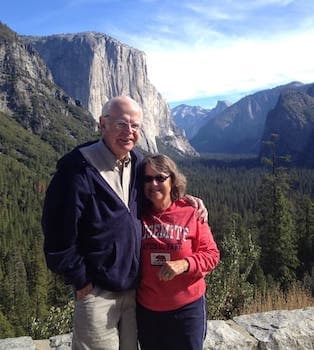
Ted Mooney, P.E. RET
Striving to live Aloha
(Ted can offer longterm or instant help)
finishing.com - Pine Beach, New Jersey
Thanks for your reply, Ted. I am electroforming (Shoe bronzing) for over 40 years and need to neutralize the shoes after rinsing them over the plating tank, then another rinse before dipping them in soda crystals 0.5 Kilo in a gallons of water. This does a fairly good job but I thought that you may know something that would be even better. A lot of web posts recommend baking powder.
You Take Care, Daniel.
- BELFAST IRELAND
Q. In the factory where I work, one of the Copper baths shows the following problem:
Along the length of the cylinder small granules form when copper plating them.
I run a dummy-cylinder this week
Sulfuric Acid is at 59.78 g/L
copper sulphate is at 230.6 g/L
What should my next move be?
I am new in this position and still learning, so please every piece of information or advice is quite welcome.
Chemical Analyst - Athens, Greece
October 1, 2021
A. Hello,
Sorry it took a while to reply, I haven't had a chance to contribute to this site in awhile.
When I worked in the plating business we would experience this same problem periodically. We found that the bottom of our tanks contained dropped parts, anode bags had holes in them, the solution level was higher than the openings of the anode baskets. It's important that the bath filtration is adequate and filters are changed on a regular basis. It could be any one of the things I mentioned. Normally roughness of the deposit or nodules are due to particulate matter in the bath, usually metallic.
Retired - WINSTON SALEM
Hello
I did check one of the Baths and as hinted we found some particles in the edges. we emptied and cleaned the bath and now it runs perfectly.
Thank you very much for your answer!!
Chemical Analyst - Athens
October 22, 2021
Q, A, or Comment on THIS thread -or- Start a NEW Thread