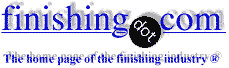
-----
Electropolishing bath: Specific gravity testing, replacement of electrolyte

Q. Greetings,
We use a phosphoric-sulfuric blend for our e-polish bath and we are trying to titrate by Acid Normality. We have found a suitable range however, when we attempt to lower total acidity by decant and refill with DI water, we notice the normality increases.
To reduce acid normality, would it be advisable to replenish with fresh electrolyte? It just seems counter intuitive if we're trying to "weaken" the bath
Metal Finisher - Phoenix Arizona
March 16, 2024
Update: The acidity has been controlled and we have a functional analysis method.
Q. I do have a question regarding ramping. Is there a defined ramp process to bring parts to determined load size? I just feel over-energizing a product to full load uncontrolled will cause pitting.
Any inputs are greatly appreciated.
- Phoenix, Arizona
March 21, 2024
A. Hi Mr. Mueller,
Voltage ramping (or current limiting, which achieves the same result) is necessary in anodizing because until the surface has a resistive anodized layer on it, it's conductivity is high and burning would result; then, as the anodized layer builds, more voltage is necessary to overcome the resistance of the anodized film.
But what leads you to feel it is beneficial in electropolishing?
My electropolishing knowledge comes only from books, curating this website, and designing electropolishing lines. I don't have hands-on electropolishing knowledge -- but operating at low voltage/current produces etching instead of electropolishing, then oscillation, so I'm not seeing why you would want to ramp.
I'm not saying I'm right, but rather that I'd like to hear your theory.
Luck & Regards,
Ted Mooney, P.E. RET
Striving to live Aloha
(Ted can offer longterm or instant help)
finishing.com - Pine Beach, New Jersey
Q. Hi Ted,
When we energized a couple samples (i.e. (5) 4"x7"x.032" test panels) with the parameters set by our vendor's Tech Data sheet, we determined a load size of 296 ASF. When I placed the samples into the bath and raised the amperage immediately to 296, we notice pitting after the cycle time.
On another trial run, When I gradually raised the load size to 296 ASF-- and not the entire load size out the gates, I did not see any pitting.
What I would like to understand is if raising the amperage little by little seems to work, what would be the preferred method in reaching full load size? Is there a formula to follow or is the process mostly based off trial and error?
We are new to the electro-polish (E-polish) process but our team has more than 50 years experience in anodizing. I'm curious to see if I can apply a function similar the 720-rule to this application
Thanks for your suport.
Note: With this electrolyte, typical cycle times varies between 5 - 10 minutes.
- Phoenix, Arizona
March 21, 2024
⇩ Related postings, oldest first ⇩
Q. We electropolish stainless steel parts (300 series) in a 60% phosphoric, 20 % sulfuric, 20% di water solution, and at 100 amps/ft2. I have two questions; What is the operating range for specific gravity and dissolved iron?, and What type of cathode material is best for this bath? Thanks in advance.
Dave BernardiniHorseheads, New York
1999
A. We here at our company use a commercial product; 50 % vol. Phosphoric acid, 40 % vol. sulfuric acid and 10 % vol. of some secret stuff. We have been supplied with these figures:
At 20 °C:
- 2% Fe: 1,77 g/mL
- 3% 1,78 g/mL
- 4% 1,79 g/mL
- 5% 1,80 g/mL
and so on. It may depend on the composition of your electrolyte, your amps, temperature, polishing time and so forth.
Hans Henrik Larsen- Denmark
A. Hello Mr Bernardini.The stainless steel (316L) is better cathode for electropolishing of Steels.
H.Valizade- Tehran, Iran
Q. Our firm has been electropolishing stainless steel wire for quite a few years. The process is rather archaic and I am trying to improve the process somewhat.
One such problem that I am trying to solve is that the electrolyte is never tested, it just "loses effectiveness" and the whole lot is thrown out. I have heard mention that testing of specific gravity and metal ion contamination should occur and the electrolyte should be topped up and parts replaced (but not the whole lot).
Can someone please explain specific gravity (in relation to how an electrolyte works) and also some tests that should indicate how effective the electrolyte is and when it needs to be replaced.
We currently use a Phosphoric (81%) and sulfuric acid bath with the following concentrations: 2.5L phos, 880 mL sulfuric plus 620 mL of water.
The parts that we electropolish are fine wire to small rods between 0.3 mm and 5 mm diameter.
Thanks,
Kayte Worrall- Melbourne, Victoria, Australia
2001
A. While it is possible to gain some measure of control by using specific gravity, I think you should look at using titration of the solution to accurately determine both acids.
For Sulfuric-Phosphoric mixtures, you can use this procedure:
1) pipette [pipettes on eBay or Amazon [affil link] 20 ml of bath solution into a 100 ml volumetric flask [100 mL flasks on eBay or Amazon [affil link] . Fill to the mark with DI water.
2) Pipette 10 ml of this diluted solution into a 125 ml Erlenmeyer flask ⇦[125 mL flasks on eBay or Amazon [affil link] or beaker [beakers on eBay or Amazon [affil link] , and add 20 ml of water.
3) Add 2 drops of methyl orange ⇦ on eBay or Amazon [affil link] indicator solution, and titrate with 1.0 N NaOH [1N NaOH on Amazon [affil link] to the yellow endpoint. Record the amount of NaOH as volume A.
4) Pipette a second 10 ml of the solution from step 1 into another 125 ml Erlenmeyer flask or beaker, and add 20 ml of water.
5) Add 2 drops of phenolphthalein ⇦ on eBay & Amazon [affil link] indicator solution, and titrate with 1.0 N NaOH [1N NaOH on Amazon [affil link] until a persistent pink color appears. Record this volume of NaOH as volume B.
6) Calculate volume C = B - A
%(v/v) Sulfuric Acid (66° Be') = (A - C) x 1.36
%(v/v) Phosphoric Acid (85% or 59.2°Be') = C x 3.4
- Thorndale, Pennsylvania
A. If you take the specific gravity with a hydrometer [hydrometers on eBay or Amazon [affil link] that reads satisfactory in that range e.g., 1.4 -1.7, after make up, then maintain at that SG with additions of the same mix as make up as loss will be from dragout. A drop in SG will indicate excess water from drag-in or absorption. There will be a slight increase due to some metal dissolving.
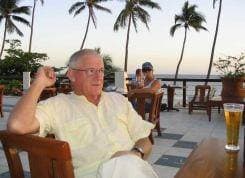
Geoffrey Whitelaw
- Port Melbourne, Australia
Electropolishing of 304 stainless steel wire baskets
Q. I work on the electropolishing of 304 stainless steel wire baskets. I want to know the bath (solution) of electropolishing to have less pitting on metal and time. I work in sulfuric and phosphoric 70/30. But result is not that good. Have any idea of any other solution?
Thanks
kalyan Maharathra, India
2006
A. Hi, Sayed,
It is hard to recommend that you simply change your solution formulation, when the problem could be improper cleaning, poor current control, insufficient agitation, excess water in the solution, or several other things. Nonetheless, a number of solution formulations are included in the Electroplating Engineering Handbook ⇦ this on
eBay,
AbeBooks, or
Amazon [affil link]
. Good luck.
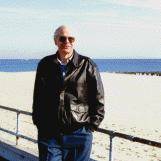
Ted Mooney, P.E.
Striving to live Aloha
(Ted can offer longterm or instant help)
finishing.com - Pine Beach, New Jersey
Q. We are 304 stainless steel wire basket manufacturer doing EP with 70% phosphoric acid 30% sulfuric acid but not getting good result and take a lot of time for finish. We mailed our problem to central electropolishing company they suggested to add 7% Diethyleneglycolmonobutylether as additive. Run parts at 125-165 °F @ 9-12 V DC . Try 2-5 minutes and adjust time accordingly to the results. As per their suggestion I added 7% Diethyleneglycolmonobutylether. but the duration time is same as before. While EP'ing, the foam is about 3 to 4 inches floating on bath. If the EP process continues for 4 to 5 hrs the thickness of foam also increases and takes 30 to 40 minutes for finish, so please suggest some solution or other bath
Thanks
kalyan Maharathra, India
2006
(affil links)
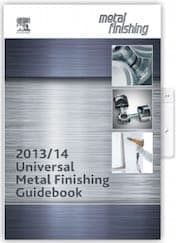
free pdf is currently available from academia.edu
A. Excessive time indicates inadequate current density, most likely from inadequate fixturing. Cathodes should conform to the basket geometry, both inside & out. Try a frame of copper strip 1/4" thick by 3/4" wide (wide enough to drill bolt holes), with coarse copper mesh for the cathode surface. Remove from the EP solution when not in use. The basket (anode) fixturing must also allow sufficient current.
The EP solution with 7% Diethyleneglycolmonobutylether is listed in the Metal Finishing Guidebook, so should work, but how is it analyzed? I suggest a solution 60-65 wt% phosphoric + 15-20% sulfuric + 20-24% water, with acids determined by titration & specific gravity. A bit of surfactant (0.05-0.1 %) aids wetting and reduces gas bubble problems.
Search this site for more information on electropolishing.
- Goleta, California

Rest in peace, Ken. Thank you for your hard work which the finishing world, and we at finishing.com, continue to benefit from.
A. Sayed,
I am a Technician at a reputable electropolishing company. From my experience there is only one thing that causes pitting during the polishing process, that is running the part in the acid bath for too long. If you're not getting a good polish in a short amount of time you are: Not running sufficient volt's/amperage for the part you are running, or your cathode (negative copper field) is not in close enough proximity of the part to polish effectively, or you are racking your part so that gasses are trapping between the part and the cathode (causing what we refer to as gassing, which will make a part look as if it never polished), or you could have an improper chemical balance in your EP fluid.
There are endless things that can cause a part to not get shiny but only one that causes pitting and that as I said above is from polishing a part for way too long.
Anthony Kansas USA
July 20, 2012
Electropolish specific gravity problems
Q. Our electropolish tanks fall out of specific gravity range during the summer months probably due to humidity. We try to raise the tank temperatures to burn off the excess water but once we put the tank back in production it falls out in a couple of days. We can't remove much solution and replace it because we have designated iron content levels. Does anyone have any ideas?
Jay Bells- Denver, Colorado
July 25, 2018
and Chemical Polishing
of Metals in
Research and Industry"
by W.J. Tegart
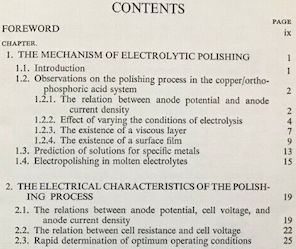
on eBay or Amazon
or AbeBooks
(affil link)
A. Hi Jay. If air conditioning or de-humidifying isn't a practical answer, you probably can't do much about the absorption. But as Geoff reminds us, just because absorption is worse in summer and puts you over the edge, doesn't mean that drag-in is playing no part of course. Maybe it's practical to slightly reduce the drag-in, maybe with a warm water rinse?
Regards,
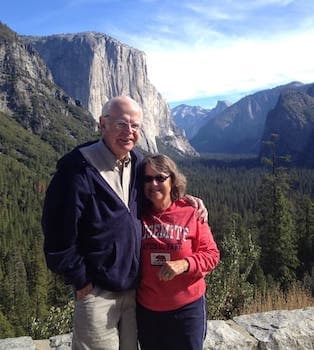
Ted Mooney, P.E. RET
Striving to live Aloha
(Ted can offer longterm or instant help)
finishing.com - Pine Beach, New Jersey
Retaining some portion of electrolyte when dumping electropolishing bath
Q. Hello everyone,
I was gathering some information on the aging of electrolyte bath used for Electropolishing in industry.
Would someone please let me know if there is a standard value for the amount of charge that has to be maintained per unit volume in order to achieve a quality controlled approach for EP?
- Montreal, Quebec, Canada
May 16, 2019
A. Hi BV. If you're looking to gather general information, you won't find a quicker or better path to learning about electropolishing than the "Electropolishing" chapter by Dean Ward [dec.] in the Electroplating Engineering Handbook ⇦ this on eBay, AbeBooks, or Amazon [affil link] . In 20 pages it covers all aspects of Electropolishing.
There are both "finite life" and "infinite life" electropolishing baths. For the "infinite life", you must periodically decant or otherwise remove the precipitated salt sludge from the bottom of the tank, and I'm sure there is no 'standard amount' to discard (you discard the 'sludgy' part and retain the 'non-sludgy' part and that is always going to be a matter of balance, judgement, and how much sludge you find there.
For the "finite life" type of solution it is true that in many metal finishing operations it is conventional to retain some portion of the old solution to serve as a "seed" when dumping it, but I don't know if that is commonly done with all electropolishing solutions.
Hopefully someone with experience in that will chime in on that ... but readers tell us they're quite drawn to helping people with actual situations where there is back-&-forth from which they can learn something, but much less interested in one-directional technology transfers in response to abstract questions :-)
Good luck, and Regards,
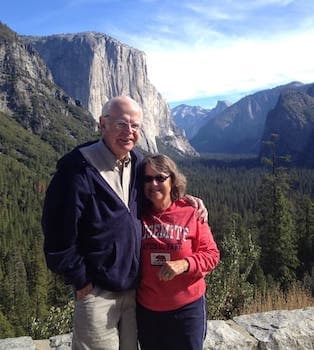
Ted Mooney, P.E. RET
Striving to live Aloha
(Ted can offer longterm or instant help)
finishing.com - Pine Beach, New Jersey
Q. Hello Ted,
I am a Research student and my work is on EP.
I am in the process of studying the electrolyte aging in the industry; if they use any kind of parameters to judge the electrolyte aging.
And I was wondering if the industry has a standard value for the amount of charge that has to be maintained for a unit volume of electrolyte for perfect electropolishing, and below which the electrolyte will no longer deliver desirable results and thus, it had to be replaced fully or decanted.
Thanks,
- Montreal, Quebec, Canada
May 17, 2019
A. Hi again, BV. Can you give me a couple of synonyms for 'charge'? I previously thought I understood your question but, apologies, now I am not sure what you are asking about :-(
Metal finishing solutions can almost always be replenished and 'juiced up' as time & tide consume their active ingredients. You don't dump because you run out of acid or other solution component, you dump because the contaminants, even if only water, have become problematic. Electropolishing solutions build up in metal if they are 'finite life' and must be dumped due to the metal buildup; they must be decanted or filtered or whatever to remove the metal if they are the 'infinite life' type. You are asking for a 'standard value' for a concept that I'm not even fully understanding :-)
Sorry, and Regards,
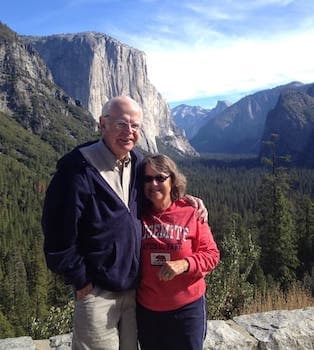
Ted Mooney, P.E. RET
Striving to live Aloha
(Ted can offer longterm or instant help)
finishing.com - Pine Beach, New Jersey
Q. Hello Ted,
Currently, I am studying the aging of electrolyte as part of research in Electropolishing.
I was trying to figure out if the industries use any kind of standard parameters to evaluate the aging of electrolyte, i.e., to determine if the electrolyte is fit/ unfit for prolonged use, like by measuring the charge density or current density.
Thanks.
- Canada, Quebec, Montreal
May 17, 2019
A. Hi once more. Your question is posted and we'll see if it gets any responses. As explained in the reference that I suggested, you must electropolish at a fixed current density (probably about 150 ASF) because if the current density drops, you get etching instead of polishing. So people will generally set their power supply to deliver that much current density. I suppose it's possible that the current density could drop below that despite their effort, and signal the need to replace the solution, but that is not something I have personally seen, so I doubt that it's 'standard'.
Have you had an opportunity to visit an electropolishing shop or maybe to do some small-scale electropolishing in the lab? It has been done in shotglass-size processing tanks. It's difficult to suggest realistic ways to scientifically establish a dump schedule or bleed-&-feed schedule because there are a lot of different situations. Sorry :-)
Regards,
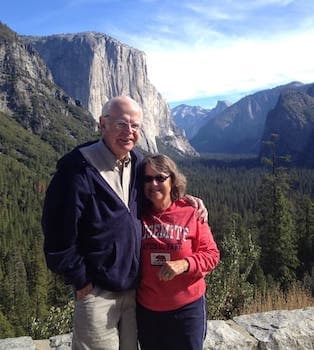
Ted Mooney, P.E. RET
Striving to live Aloha
(Ted can offer longterm or instant help)
finishing.com - Pine Beach, New Jersey
![]() |
Q. Hello Ted, I could find the book "Electroplating Engineering Handbook" in the library, but only the second edition. - Montreal, Quebec, Canada May 18, 2019 A. If you're running the conventional phosphoric/sulfuric electropolish bath: ![]() Jeffrey Holmes, CEF Spartanburg, South Carolina |
Q. Hello Jeffrey,
Thanks for the input.
I am trying to figure out the ways to determine the aging, i.e., at which point to decide that the electrolyte solution has aged and now it has to be replaced/decanted.
Industries would definitely have some kind of judgement parameters to evaluate the solution aging.
Would you please let me know if you have some kind of knowledge on this?
Thanks,
- Montreal, Quebec, Canada
May 21, 2019
A. Hello again, BV:
Let me try again. I have many, many years experience electropolishing, parts ranging from fractions of an ounce to multiple ton weight.
Assuming you are using the common 3:1 phosphoric/sulfuric bath.
After a fairly extended period of use, the metals will begin to form sludge on the bottom of the tank. This sludge causes no problem until it becomes deep enough to interfere with use of the tank.
At that time, the sludge is removed, and the volume made up with fresh acid.
To repeat - there is no testing/measurement of aging. The bath never ages out. It is self regulating through the formation of sludge which is removed periodically.
The above process can be continued eternally. There is never any need to replace the liquid portion of the bath. There is no analytical control beyond measuring specific gravity. If the specific gravity is low, heat the bath to drive off the excess water. The specific gravity will never be too high as dissolved metals are removed by settling to the bottom as sludge.
I repeat: the electropolish solution is never replaced. Not ever. As it is used the excess dissolved metals drop out as sludge. The sludge is removed when it becomes deep enough to interfere with processing, and new acid is added to restore volume.
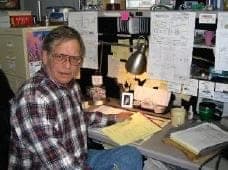
Jeffrey Holmes, CEF
Spartanburg, South Carolina
Hello Jeffrey,
Thanks for the reply, helped to understand the industrial practice to handle the electrolyte.
Regards,
- Montreal, Quebec, Canada
May 23, 2019
A. Hello Jeffrey,
From my experience, the current density does get limited after a certain concentration of metal ions is achieved. We analyze the iron concentration in the bath monthly and we need to change a part of the bath and replace it with 'virgin' acid to get the metal concentration back in the possible work range. What we noticed when current density gets limited is that we need to apply higher voltage to get the diameter spec but in which case the EP becomes too aggressive and we have pits and impacts on the workpiece.
- Samut Prakan, Thailand
May 5, 2022
A. One last thing to add to this discussion of maintaining an EP bath in good condition is the importance of keeping the cathodes themselves clean. They will, at least in my experience with copper cathodes, build up a layer of sludge on the surface which needs to be removed regularly with a stiff brush (polypropylene or polyethylene bristles will stand up to the solution just fine) to keep the tank functional and predictable.
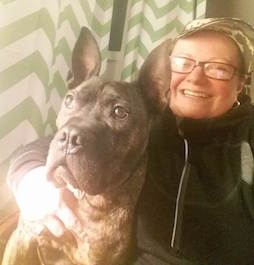
Rachel Mackintosh
lab rat - Greenfield, Vermont
What gets dissolved in the electrolyte solution during Electropolishing of Stainless Steel Grade 316?
⇦ Tip: Readers want to learn from your situation;
so some readers skip abstract questions.
Q. Hello Everyone,
Would someone here please let me know what gets dissolved in the electrolyte solution during Electropolishing of Stainless Steel Grade 316?
Would someone here help me with this question as well:
What happens to the Electrical Conductivity of the electrolyte when the electropolishing solution ages?
Will it increase or decrease?
I am considering a mixture of sulfuric acid, Phosphoric acid and water.
And what are the factors responsible for the diminishing quality of the final finish when the electropolishing bath begins to sludge?
Thanks.
- Montreal, Quebec, Canada
June 28, 2019
Q. Hi, I am vignesh willing to start electropolishing company. Will you guide me?
Vignesh surendran- Chennai, tamilnadu, India
May 17, 2019
A. Hi cousin Vignesh. As suggested to BV, please review the 21-page chapter in Electroplating Engineering Handbook ⇦ this on eBay, AbeBooks, or Amazon [affil link] the Electroplating Engineering Handbook for a quick introduction to electropolishing. If you need more thorough info than that, there are two books on the subject, referenced previously on this page. If you have specific questions, please get back to us with them. Thanks. Good luck.
Regards,
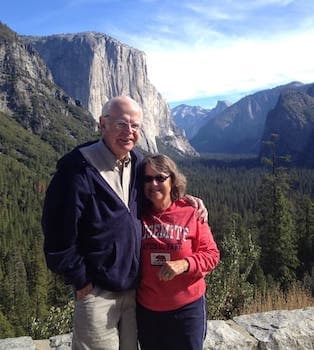
Ted Mooney, P.E. RET
Striving to live Aloha
(Ted can offer longterm or instant help)
finishing.com - Pine Beach, New Jersey
Q. Hi,
I am vignesh. I would like start a electroplating business in Chennai india. I need your help by suggesting me which electroplating will be more profitable and least costliest.
- Chennai, tamilnadu, India
June 26, 2019
(affil links)
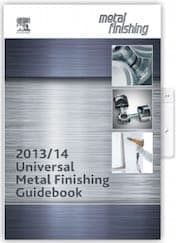
free pdf is currently available from academia.edu
A. Hi Vignesh. Unfortunately, the least costly to enter is very unlikely to be the most profitable; why would anyone anywhere spend more to try to enter a more expensive business with lower profits? But actually, whichever process you can do with close to zero rejects & zero defects will probably be the most profitable. I think it would be a mistake, however, to start a business you know nothing about; please try to take a job with an electroplating or electropolishing jobshop for at least a few months first, while taking an inventory of your own past experiences and your interests. If unable to do that, at least visit a couple and spend a few weeks thumbing through one or more of The Electroplating Engineering Handbook ⇦ this on eBay, AbeBooks, or Amazon [affil link] , the Metal Finishing Guidebook, and the Canning Handbook [on eBay, Amazon, AbeBooks affil links]. Best of luck.
Regards,
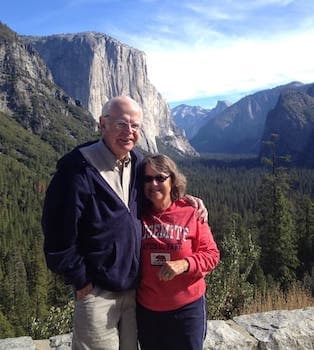
Ted Mooney, P.E. RET
Striving to live Aloha
(Ted can offer longterm or instant help)
finishing.com - Pine Beach, New Jersey
⇦ Tip: Readers want to learn from your situation;
so some readers skip abstract questions.
Q. Can anyone tell me what the viscosity of the phosphoric acid/sulfuric acid solution is at 120 °F?
Rudolph R MillanConsultant - Walnut Creek
March 12, 2022
A. Hi Rudolph. The phosphoric acid / sulfuric acid solution is presumably per patent number US2334698, which seems to be expired. It is very high in acid, low in water, and quite viscous -- but sorry I do not have the viscosity numbers for you.
Luck & Regards,
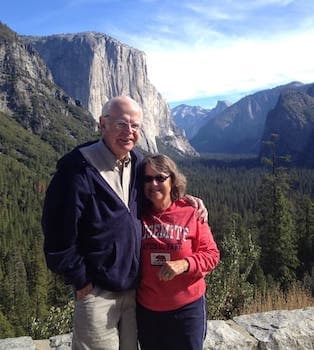
Ted Mooney, P.E. RET
Striving to live Aloha
(Ted can offer longterm or instant help)
finishing.com - Pine Beach, New Jersey
⇦ Tip: Readers want to learn from your situation;
so some readers skip abstract questions.
Q. I want to ask what are the ratios of phosphoric acid and sulfuric acid?
- Bursa, Turkey
September 13, 2022
A. Hi Gulhan. We added your question to a thread which already offers that info. Commonly 70 parts sulfuric to 30 parts phosphoric, or 75 to 25. More detail on the ratio is offered on this thread.
But it probably should be mentioned when people ask for the ratio, that the exact ratio is far from the key to successful electropolishing. I know of one major shop which electropolished without any phosphoric acid, and the Electroplating Engineering Handbook offers a dozen or so different formulations for the electropolishing solution. If you can, please present your actual situation. Books are best for abstract & theoretical questions; for troubleshooting, public forums where experienced readers are presented with actual situations are usually best.
Luck & Regards,
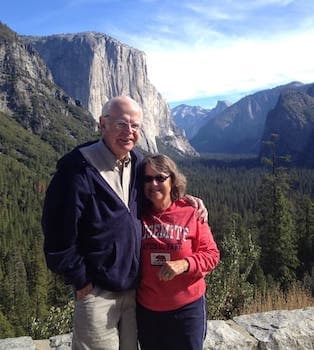
Ted Mooney, P.E. RET
Striving to live Aloha
(Ted can offer longterm or instant help)
finishing.com - Pine Beach, New Jersey
Q, A, or Comment on THIS thread -or- Start a NEW Thread