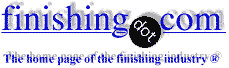
-----
Bronze plating solution composition, analysis, and parameters
RFQ -- @Terry_Van_Dien: We are looking for Bronze plating service. Can you contact me? pete@qflex.com?
pete uka- Fullerton CA USA
August 27, 2025
⇩ Related postings, oldest first ⇩
⇦ Tip: Readers want to learn from your situation;
so some readers skip abstract questions.
Thank you. Remberto Brito
S.A. de C.V.
1997
A. Remberto,
Macdermid has a bronze solution that we use for antique gold and nickel-free plating for jewellery. I do not know the hardness but you could try Macdermid.
Regards
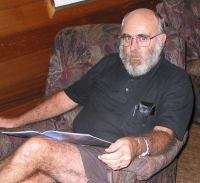
Bob Lynch
plating company - Sydney, Australia
A. Mr. Brito
We also use some Macdermid chemicals to make up a Bronze plating bath. We use oxygen free copper anodes, potassium stannate, potassium hydroxide, potassium cyanide, and Rocheltex.
Concentrations are as follows:
Copper 5 oz/gal
Stannate 1.5 oz/gal
Hydroxide 0.7 oz/gal
Cyanide 5 oz/gal
Sincerely,
Wes YanceyGeneral Electric
by William Safranek
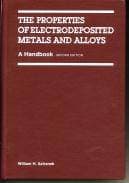
on eBay or Amazon
or AbeBooks
(affil link)
A. Hi Remberto,
Most plating textbooks will give you bronze formulations. "Modern Electroplating"
[on
AbeBooks,
eBay, or
Amazon affil links]
, for example, offers:
Potassium stannate 60 g/l
Potassium hydroxide 7.5 g/l
Copper cyanide 40 g/l
Potassium cyanide 90 g/l
Free potassium cyanide 34 g/l
(plus wetting agent, addition agent, brightener)
It looks like nearly any bronze deposit will be at least 40 Rc (although this is based on a conversion chart because the data is usually offered in kg/mm2 microhardness), but Safranek ⇨
offers lots of data on hardness vs. other parameters and says hardness is maximum at 15% tin and when operating the bath at lower than usual temperatures.
Please try your best to introduce yourself and your situation, what you want to plate, and what such data will help ... and you'll get better and more enthusiastic help. Thanks!
Luck & Regards,
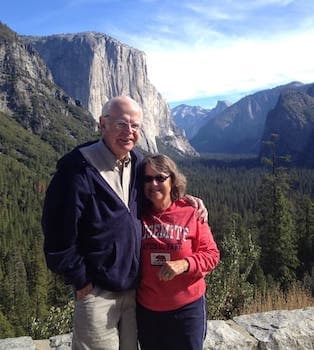
Ted Mooney, P.E. RET
Striving to live Aloha
(Ted can offer longterm or instant help)
finishing.com - Pine Beach, New Jersey
Analytical procedures for cyanide bronze plating solution?
Q. I was recently charged with the responsibility of our plating shop. We perform cyanide bronze plating on aerospace components. We currently do not perform in-house analysis of the plating baths. I need assistance in developing analytical procedures for bath control.
Any help in developing these procedures or locating resources would be greatly appreciated.
Terry Van Dien- aerospace - Beaufort, South Carolina
1998
A. Hi Terry. The vendors of the solutions, unless you are using home-brews, have procedures that are proven.
The Metal Finishing Guidebook has a nice section on analysis.
Commercial books such as The Chemical Analysis of Electroplating Solutions [affil link on Amazon or eBay or AbeBooks affil links] are good.
The Electroplating Engineering Handbook ⇦ this on eBay, AbeBooks, or Amazon [affil link] edited by Durney has an analysis section.
Do not forget to analyze your prep cleaners and acids also.
James Watts- Navarre, Florida
A. Don't blindly accept any published analysis procedure, even Metal Finishing's. Always prepare a bench top (laboratory) test solution and perform the analysis procedure on it. Then muck up the test solutions; i.e. add carbonates to your alkaline cleaners and cyanide solutions, add copper to your acid activators. Analyze these test solutions with the same procedure you initially tried. If you get the same results and the results agree with what you actually put in, then you got a reliable procedure. We found that the normal analysis procedure for alkaline solutions was useful for only newly make baths. As the baths aged they got stronger when using a phenolphthalein titration endpoint. We now use methyl orange ⇦ on eBay or Amazon [affil link] and phenolphthalein ⇦ on eBay & Amazon [affil link] endpoints (to calculate carbonate increase and hydroxide decrease). This method has given us some measure of reliability for determining concentration of active ingredients in alkaline cleaners.
Marjorie K. Turton- Winnipeg, Manitoba, Canada
1999
Ed. note: Great advice, Marjorie. Thanks!
![]() |
Q. Dear reader, I would like to produce a bronze patina/finish on a set of plain metal door hinges so that these fittings will blend with the overall appearance of the door. I was informed that a simple method involved soaking the metal hinges in a solution of ammonia. Is there any truth in this recommendation. If not can you suggest a method which is not too involved and does not rely on the use of chemicals which release harmful gases. Thank you for your help in this matter. Joseph Hayek1998 A. Hi Joseph. When you say "plain metal" I assume you are suggesting that they are made of steel? Ammonia
⇦ on
eBay or
Amazon [affil link] is sometimes used to color brass, but I don't think it nor any other reagent will react with steel to turn it to a brass color. Regards, ![]() Ted Mooney, P.E. Striving to live Aloha (Ted can offer longterm or instant help) finishing.com - Pine Beach, New Jersey |
Q. Hello sir!
I am doing the job work of imitation jewelry plating! I want to know about yellow bronze plating. What is the wetting agent used in bronze plating?
Thanking you,
Abbas LaxmidharAnkur Metal Finishers - Rjt , Guj, India
2002
A. DEAR FRIEND,
THERE ARE LOTS OF VARIETY OF WETTING AGENTS UTILIZED IN SEVERAL ALLOY PLATING PROCESSES. THEY ARE IN FACT CONFIDENTIAL AND CAN BE SYNTHESIZED VERY EASILY.
- GUJARAT, INDIA
A. Hi Abbas,
Proprietary brass plating baths are a much better idea for small processors like imitation jewelry makers, and their wetting agents are trade secret, but if you just want to do some experiments, sodium lauryl sulphate and sodium laureth sulphate are the most readily available wetting agents and are used in a variety of applications including some electroplating.
Luck & Regards,
Ted Mooney, P.E. RET
Striving to live Aloha
(Ted can offer longterm or instant help)
finishing.com - Pine Beach, New Jersey
Bronze plating process parameters
Q. I need to know what amperage to use for bronze plating in an existing cyanide bath. less than 1 sq. ft substrate area thanks!
John Wanningersilversmiths - Placerville, California
2003
A. Cathodic current density between 20 and 50 ASF; anodic current density less than 20 ASF.
(Assuming it is a cyanide bath!)
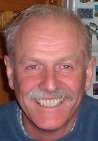
Trevor Crichton
R&D practical scientist
Chesham, Bucks, UK
Q. We are trying to duplicate a plating process on a part thru reverse engineering. The completed part has a phosphor-bronze plating (~90 copper/~10 tin) composition. The finish plating thickness is .030-.040" thick. The part base material is a ductile iron, with a nickel strike between the iron and the plating.
I am not able to find any SAE/AMS/ASTM specification covering bronze plating.
There is a specification on how to plate this material, but it is proprietary. How can I duplicate this process or write my own specification to duplicate this process? How can I insure the material is properly bonded to the base material?
Please help,
Mark Powellaircraft parts - Atlanta, Georgia, USA
2004
Ed. note: Richard_A._Schreiman states below that there are no recognized specifications for bronze plating.
A. I would define plating as a process to deposit a metal or alloy onto a surface by means of a liquid that contains metallic ions. Now, how do you know the part was plated if you didn't do it? Could it be processed by a different method? I can think of at least five different processes that can produce a rather thick layer like that.
1- conventional thermospray (porous fair bond)
2- plasma spray (less porous better bond)
3- HVOF (almost zero pores good bond)
4- spark deposition (zero pores weld bond)
5- high energy cladding (same).
All have advantages and disadvantages over plating of course, but are not proprietary.
P.S. Frequent readers are welcome to remind me or correct me.
Guillermo MarrufoMonterrey, NL, Mexico
Multiple threads merged: please forgive chronology errors and repetition 🙂
Need reliable Bronze plating bath
RFQ: I work for a small plating shop that wants to begin bronze plating for decorative purposes. We have used the guidebook's formulation in the past and found it difficult to control and a short life. I have begun researching vendors of bronze plating baths that will have stabilizers and other additives to help with the control and life but find that either they have discontinued bronze and brass baths or the vendor is located in India.
I have nothing against India but I would like to find a vendor in the US.
Can anyone direct me to a vendor that has a reliable bronze bath.
Tim H [last name deleted for privacy by Editor]Decorative Plating - Miami, Florida, USA
2005
Ed. note: This RFQ is outdated, but technical replies are welcome, and readers are encouraged to post their own RFQs. But no public commercial suggestions please ( huh? why?).
A. If the Cu-Sn plating contains phosphorus, it was most likely deposited using an alkaline pyrophosphate solution (in order to avoid the use of cyanide in the plating bath). No ASM specification currently exists to govern alkaline Cu-Sn electroplating. However, AMS2429 governs plating production of 90Cu-10Sn nitriding stop-off in a cyanide acid bath. The cyanide acid bath is a much more efficient and time-friendly process, and will typically provide a much more uniform plating layer than the alkaline bath; however, due to environmental and health considerations with the cyanide bath, more shops are considering use of the pyrophosphate alkaline baths.
Richard A. Schreiman, M&P Engineeraerospace - Irvine, California, USA
2007
Q. Bronze Plating: Cyanide vs. Alkaline Pyrophosphate [this entry appended here by editor in lieu of spawning a duplicative thread]
We are a lighting manufacturer in California and want to set up a tank for bronze Plating of brass parts. I understand that the traditional bronze plating method requires the use of cyanide, and we would like to avoid this if possible.
Is the Alkaline Pyrophosphate method as good (or adequate for brass lamps) and if so, can someone recommend the chemical make-up for a 150 gallon tank and where to purchase the chemicals?
2010
Manufacturer - Sacramento, California, USA
A. Hi, Chuck. Considering the wastewater treatment uncertainties and the safety dangers, no one would use cyanide if it weren't better and cheaper :-)
But pyrophosphate can work, and is available from the site's supporting advertiser EPI / Electrochemical Products Inc. [a finishing.com supporting advertiser] and probably other vendors; such vendors will offer technical data sheets for the setup.
One further possibility (which has found use on brass lamps) is to do bright nickel plating and follow it with a bronze-toned electrophoretic lacquer instead of brass or bronze plating. Good luck.
Regards,
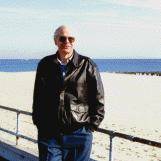
Ted Mooney, P.E.
Striving to live Aloha
(Ted can offer longterm or instant help)
finishing.com - Pine Beach, New Jersey
![]() |
Q. Please I need to know make up solution (green color bronze plating) on brass sheet. electro plating - Damascus, Syria August 11, 2009 A. Hi, Mazen. Electroplating deposits metals [not metal salts or oxides] on metal; to my knowledge it is not possible to electroplate a green coating. I believe you must either patinize the brass sheet itself or electroplate it with a conventional bronze, and then patinize the plated layer. Good luck. Regards, ![]() Ted Mooney, P.E. Striving to live Aloha (Ted can offer longterm or instant help) finishing.com - Pine Beach, New Jersey |
Best auxiliary anode material for a Bronze plating bath
Q. I am looking to make improvements in my racking system for production parts and I'm getting conflicting information. I'm just looking for another opinion.
My rack supplier is recommending titanium rod for small diameter anodes (to prevent the anode from degrading prematurely). These smaller rod anodes (0.200" - 0.375" dia.) degrade quickly and short out because of uneven wear, causing problems with my production parts. I am looking to find a way to extend the diameter / life of the anode and get more consistency with my smaller diameter parts.
I have a plating consultant who is disputing this recommendation stating that the titanium will 'contaminate' the bath and is recommending a 400 series grade tool steel. I'm unsure how this will contaminate the bath worse than the soft steel anodes we currently use.
Is the rack supplier just trying to get more money or is the plating consultant off on this one? What are your thoughts?
Thanks,
Process Engineer - Alden
June 12, 2015
A. Hi Dawn. I'm not fully understanding your description but am guessing that your plating racks (the fixtures that your parts are mounted on) are equipped with "auxiliary anodes" -- electrodes which are not designed to dissolve into the solution like consumable anodes, but to selectively deliver electricity to specific areas of your parts (like deep recesses)?
The "right" or "best" material for auxiliary anodes is usually platinum clad titanium, as it will have a very long life, but it is very expensive. For a bronze plating bath you want your consumable anodes of copper to dissolve into the solution, but you'd like your auxiliary anodes to last forever.
Regards,
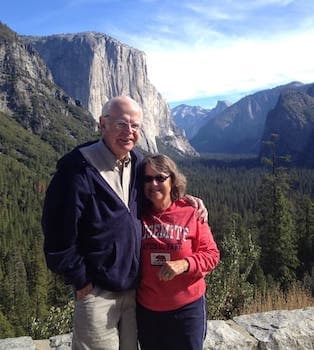
Ted Mooney, P.E. RET
Striving to live Aloha
(Ted can offer longterm or instant help)
finishing.com - Pine Beach, New Jersey
A. If mild steel is causing problems, I would personally try something else.
Hard copper comes to mind as being a bit less contaminating than iron. If it dissolves too fast it will throw off your copper - tin ratio.
I am not aware of any 400 series tool steel. There is 400 series stainless steel which is used for knives, etc.
"tool Steel" would normally be a 4xxx series.
400 series nickel rod might be a decent alternative. No chrome and no steel. I think that it would dissolve slower, but I am NOT positive about that. I have used it for an aux anode in selective nickel planting.
- Navarre, Florida
June 14, 2015
Hi, yes, our situation has auxiliary anodes and yes, we would like as little degradation and as long a life as possible out of them.
And yes, I know that it's going to be expensive. That's the question is how expensive and will it offset our scrap we get from our very small anodes being eroded away, shorting out and causing quality issues with our parts.
Thanks! That's exactly the info I was looking for! I appreciate the feedback!
Dawn
- Bellaire, Michigan USA
A. If the bronze plating solution is alkaline, then the titanium will anodize and stop passing current (just like titanium anode baskets in a cyanide solution).
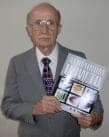
Robert H Probert
Robert H Probert Technical Services

Garner, North Carolina
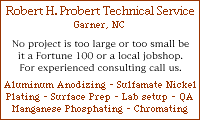
A. The anodes for alkaline bronze plating is MMO = mixed metal oxide.
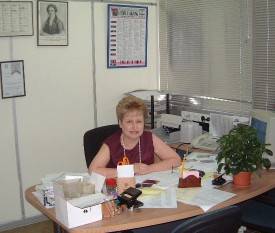

Sara Michaeli
Tel-Aviv-Yafo, Israel
Cyanide bronze bath with strange titration readings after chemical additions
Q. Good morning all...
I have an anomaly in my cyanide bronze bath titration readings and I don't know where to start looking for issues. This is completely out of the ordinary for this process.
We do a very consistent production load through the line. We make regular adds and the bath is normally VERY stable.
Our method is we do a titration first thing in the morning every day, make our add per the reading and then test the next morning (after the chemical has had time to circulate through the bath). Our bath size is approx. 12K gallons.
Recently, we did an add of both sodium and copper cyanide per our normal methods and have seen the numbers drop significantly during the next titration; however, it's not as if we have a ramped up production load. There is no obvious cause for losing the chemical.
What would I look for in the raw chemical or in our process that may cause the number to drop significantly after an add rather than stay stable? The only process change that we've done within the last month is upgrade our bath's carbon filter with some new replacement parts.
Any help in a starting point where to look would be GREATLY appreciated!!
Thank you,
Process Engineer - Alden, Michigan
October 16, 2015
A. Do you add copper cyanide directly? Is there now a different person doing the additions?
The only thing I can think of is that the CuCN being added is not properly dissolving. I have never run one of these baths, but the way I would do this is to suspend the CuCN in warm DI water, then add sufficient NaCN such that a transparent, light yellow solution is obtained.
Needless to say, this should all be done with a proper fume removal system by a trained individual wearing the prescribed PPE.
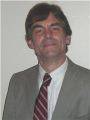
Dave Wichern
Consultant - The Bronx, New York
Thanks Dave,
Nope, nothing has changed. We thought the same thing about not being dissolved properly. We checked the props on our mixers and the circulating pump and all are functioning normally.
The operator is the same one who has been doing adds now for months.
What just came to light this morning is that we have a small metal tank in this system. All our others had been converted to poly years ago. We know that there's stray current and that the metal tank started plating, but it was very slight. Well, now we suspect that it wasn't as "slight" as we thought.
We're looking back in our records to see if that tank was operational when we were having these dips. That would explain where the copper is going!
Thanks for the help!
Dawn
- Alden, Michigan USA
Q. Can I recover work in the plating solution that has been standing for 2 days? I have been adding peroxide just for Sn2+ but I don't know how will the work come out like? I'm also worried about carbonate formation in the line.
Christina KgoboElectroplating - South Africa
December 8, 2019
A. Hi Christina. Although it is obviously a poor idea to leave parts hanging in a solution, sodium hydroxide and cyanide probably won't substantially hurt the parts if they are bare steel. If they are zinc diecastings though, or preplated/coated with anything, they're probably ruined. Get back to us with what you find, please.
Regards,
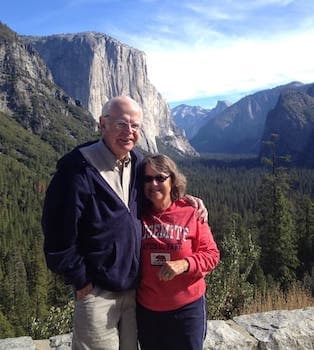
Ted Mooney, P.E. RET
Striving to live Aloha
(Ted can offer longterm or instant help)
finishing.com - Pine Beach, New Jersey
adv.: Supplier of Copper Anodes, Nickel Anodes, Bismuth Metal, & Other Metal Products for Industry & The Arts
Q, A, or Comment on THIS thread -or- Start a NEW Thread