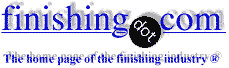
-----
Anodized Aluminum Salt Spray Testing
2001
Q. Hi all,
We are processing 7050-T7 aluminum alloy parts and test panels per the following procedure:
1. Vapor degreasing using trichloroethylene for 2 minutes at 130 °F
2. Non-etch alkaline cleaning at 135 °F
3. Deoxidizing and desmutting at room temperature for 1-2 minutes in chromic-nitric bath (Cr+6 = 8.5 g/l, HNO3 = 135 g/l)
4. Chromic acid anodizing (22 v) at 96 °F for 50 minutes (CrO3 Free = 50 g/l and Total = 59.1 g/l, Al = 1.2 g/l and pH = 0.38)
5. Dilute chromate sealing at 205 °F for 28 minutes (Cr+6 = 65 ppm, pH = 3.2)
Of course, between each of these steps we are using DI water rinsing. At the end of the process, both the parts and the test panels come out very uniform in color and have an excellent appearance. We usually obtain very good coating weight results averaging about 320 mg/ft2. However, after the panels have been exposed to the salt spray corrosion testing, they sometimes exhibit dark areas about 1 x 1 inch. These dark areas can convert into corrosion pits (white spots with head and tail appearances) as defined by the ASTM B117. We could not establish a direct correlation between these dark areas and corrosion pits.
Alain Denoyelles- Quebec, Canada
2001
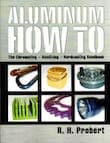
Aluminum How-To
"Chromating - Anodizing - Hardcoating"
by Robert Probert
Also available in Spanish
You'll love this book. Finishing.com has sold almost a thousand copies without a single return request :-)
A. I find it hard to find a question to answer in the above but I take it that the problem is the black marks that then lead to salt spray pits.
From all that you have said you have things well under control. The only things that I would look at:
Test panels - are they good finish before or do they have marks in them?
Test panels - are they clad - try a caustic etch and they should go black if they are white on the faces with the sides showing they have a black core they are clad.
Seal - do a seal quality test with ink.
Seal - if seal test fails check seal for silicate.
Hope this is of use to you.
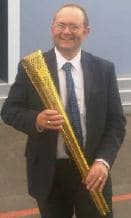
Martin Trigg-Hogarth
surface treatment shop - Stroud, Glos, England
Anodizing Thickness and Corrosion Tests
Q. Hello there,
I am a final year Irish student completing a project on Al anodising. I have successfully anodised the Al profiles, but now I am unsure of how to test the profiles for thickness, corrosion etc using the simplest and cheapest methods possible.
Any information would be gratefully accepted.
Aoife Trant- Cork, Ireland
2001
2005
Q. I have always been under the impression that the correct corrosion testing procedure of Anodized test panels as per ASTM B117 is as follows:
Test panels : 3" x 10" x 0.040" 2024-T3 bare or the most commonly run alloy (with the 10" side cut parallel to the rolling direction).
Test procedure:
Rack or hold upward on the length the panels at a 6 degrees angle from the vertical [using plastic racks or holders].
Rinse panels with DI Water
Enter the racked panels in the operational salt spray cabinet and leave them for 2 weeks (336 hours)
Remove panels and examine surface for corrosion pits.
NOTE: A corrosion pit is defined as a small depression or cavity produced in the metal surface during the exposure to the salt spray fog. In most of the cases the pits are accompanied by abundant corrosion products. In the case of aluminum alloys, the color of the corrosion product is white (aluminum chloride). A corrosion pit is a comet-like in shape defined by a head (pit (corrosion product).
The questions:
1) Is the test still valid if one holds the panels at 6 degrees from the vertical on the width (3") instead of the length (10")? This way, the dripping fog would be perpendicular to the rolling direction, and would have more resistance.
2) If a dark spot without any corrosion product is observed does it count as a corrosion pit?
I would very much appreciate any reference or specification dealing with the subject.
Thanks,
Verdun Anodizing Inc - Verdun, Quebec, CANADA
Corrosion test failure for chromic acid anodizing
Q. We have carried our salt spray testing on 2024 and 7075 test specimen chromic acid anodize bath. The test specimen sealed in DI water Temp 96 °C, time 25 minutes. The test specimen failed the salt spray test after 24 hours we observed black corrosion on entire the test specimen. Could you advise us on what things we can try in order to solve this problem.
Prakash Govindarajanplating shop employee - Belgaum India
February 18, 2011
February 18, 2011
A. Hi, Prakash. Don't spend a minute or a nickel on anything else until you've bought new test panels :-)
Regards,
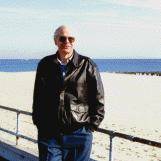
Ted Mooney, P.E.
Striving to live Aloha
(Ted can offer longterm or instant help)
finishing.com - Pine Beach, New Jersey
![]() |
A. The spec that I used to work to called for a chromate or dichromate hot seal. It helps. - Navarre, Florida February 18, 2011 A. Hi Prakash, Aerospace - Yeovil, Somerset, UK February 21, 2011 |
February 23, 2011
Q. We processed as follows
Degreasing: 07 minutes
Spray rinse
Deoxidize: 03 minutes
Spray Rinse
chromic acid anodize: 40 voltage cycle
Sealing : 25 minutes temp. 96 °C
Regards
Prakash
plating shop employee - Belgaum India
February 25, 2011
Treatment &
Finishing of
Aluminium and
Its Alloys"
by Wernick, Pinner
& Sheasby
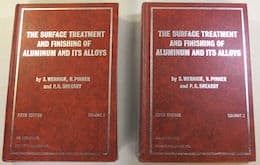
on eBay or Amazon
or AbeBooks
(affil link)
A. Hi Prakash,
OK, start with the first thing on the list. As Ted said get hold of some brand new panels. Inspect the panels for condition before you run them. Look for spots of corrosion or physical damage to the panels. Any that show either of these features reject before you start. You should now have a good clean set of panels to run through the process.
Next check all of the solution analyses for all of the baths in the process and ensure that they are meeting the specification requirements. If not ensure that process baths are adjusted and re-analysed before moving on to the next stage.
Next, and this is a thing that I favour doing as it reveals so many problems and errors you wouldn't be aware of just from reading the specification, is to follow the panels through the process, from start to finish, from the time they hit the treatment shop to the time they are placed in the salt spray cabinet. Note down ALL of the processing parameters (which baths they go in, how long for, at what temperature. Note the exact anodising cycle used, note how much fluctuation of the voltage you are getting when you get to 40 volts and, if you take it to the next step, at 50 volts, sealing time and temperature, drying conditions, etc. Check that the waterbreak check is carried out). This will give you a full map of your process. Now compare this to your specification/technique sheet that you are working to to see if there any differences.
Right, having got to this stage successfully you need to get your panels tested. Make sure that during the test all the conditions of ASTM B117 (or ISO 9227 if you are salt spraying to that specification) are being met. Inspect your panels and see what you have.
Once you have completed this exercise come back to us and tell us what you have found. From there, if you still have a problem then we should be able to help to pinpoint the problem.
Aerospace - Yeovil, Somerset, UK
Corrosion tests for anodized aluminum quality
Q.
How is the reliability of corrosion tests (acetic acid
⇦ on
eBay
or
Amazon [affil link] salt spray, copper-accelerated acetic acid salt spray) for anodized aluminum's quality? Has anyone any experience about this subject?
- sakarya,TURKEY
December 9, 2016
A. Hi Alaattin. Your question is a bit abstract (no specifics regarding your own situation) and vague (what do we mean by "reliability ... for ... quality".
But the correlation between test results and real-life endurance is zero because, among other problems, you will be testing panels which were rolled as a different lot than your actual parts and which will suffer more or less grain separation due to age. On this thread and on several similar ones you will read some opinions that the principal thing that salt spray testing of anodized aluminum reveals is how much grain separation has occurred on your test panels and, from that, how much time & money you spend on buying top quality panels and replacing them frequently :-)
Sorry, but I'm pretty cynical on this subject after several threads revealed that getting fresh test panels meant passing the salt spray test :-)
Regards,
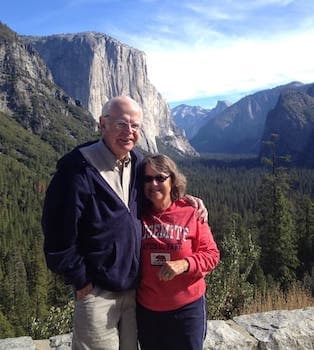
Ted Mooney, P.E. RET
Striving to live Aloha
(Ted can offer longterm or instant help)
finishing.com - Pine Beach, New Jersey
December 2016
Q. Hi Ted,
I respect your criticism. I will consider this, but I mean if we compare salt spray test and spot-weight loss test for anodizing which one is decisive for anodizing quality. I am not mentioning panels.
- sakarya TURKEY
December 12, 2016
A. Hi again. Please don't consider my comments "criticism" as I know too little about testing anodizing to criticize anyone -- it's just a "suggestion" about how to more efficiently get help on this site based on my running it for 21 years :-)
We don't know whether you are talking about MIL-A-8625 Type II anodizing or some other anodizing process, nor what alloy you are concerned with, and you haven't told us what situation is motivating your inquiry ... but we have now learned that you are speaking of destructive testing of actual parts rather than test panels.
Is the "spot-weight loss" test that you are mentioning the ASTM B680 test for seal quality that Phil Johnson describes in letter 4981? I think Phil's response on that letter may answer all of your questions about testing anodizing "quality". Good luck!
Regards,
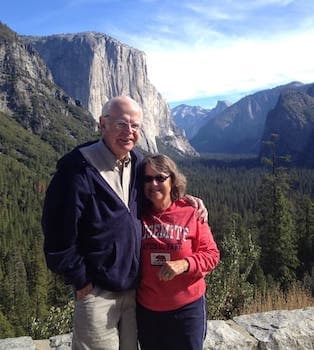
Ted Mooney, P.E. RET
Striving to live Aloha
(Ted can offer longterm or instant help)
finishing.com - Pine Beach, New Jersey
December 2016
ASTM B117 Salt Spray test how long?
Q. Dear Finishing experts
We are a small startup company in the outdoor/sports space. We have a few bicycle related products made from aluminum and magnesium alloys that we'd like to have tested to ASTM B117 salt spray standards.
The question is how long of a duration should we opt for? Our specimens range from raw (baseline) to powder coat paint, anodizing and MAO/PEO.
We are thinking 500 hours would give us a good indication but I would love to hear some suggestions and ideally references from other products or industries.
We are also opting to have photos taken for every 100 hour to document any corrosion development but I am still insecure of the total duration.
Thank you in advance!
- Dayton, Ohio
August 24, 2018
A. Hi Morten. Although many if not most people start by specifying salt spray hours, the situation ideally should be the reverse: design for the service life you need, test that your parts meet that service life, see how many salt spray hours they survive, then use salt spray testing as an early indicator of whether you still have control of the process (because parts which no longer pass the salt spray hours are unlikely to still pass the real life hours).
Some specs call for anodized aluminum to survive 192 hours, but the 336 hour requirement of MIL-A-8625 / MIL-PRF-8625 [⇦ this spec on DLA] is probably okay to specify.
Powder coating salt spray hours are often specified by the supplier of the powder. 1000 salt spray hours is probably not unusual. The promoters of MAO/PEO coatings often speak of 1000 hour salt spray resistance so that could be a starting point.
Just don't fall into the trap of believing that powder coating and MAO/PEO coatings are "3x better than anodizing" -- they may not be as good :-)
Regards,
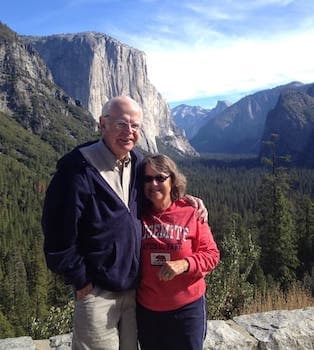
Ted Mooney, P.E. RET
Striving to live Aloha
(Ted can offer longterm or instant help)
finishing.com - Pine Beach, New Jersey
August 2018
Hard coat with PTFE fails 336-hour salt spray
Q. Hello everyone
Am Naveen kumar working as Methods engineer in one of the plating industry. We have been coating PTFE over a Hard anodized 2024-T3 panel & subjecting the same to salt spray(5%) for 336 hours and we have been continuously failing in that. We are maintaining the parameters as per the specified data sheet. Is there any other way to get them cleared?
employee - Bengaluru, India
August 23, 2019
A. Hi Naveen. Unfortunately, as you'll read on numerous threads on this site, salt spray testing of aluminum panels often reveals more about the age & quality of the test panels than about your process :-(
When you are using aluminum test panels to determine whether your process is under control, and the panels are failing, the first step is almost always to replace the panels :-)
Get back to us after you've tried new panels please.
Regards,
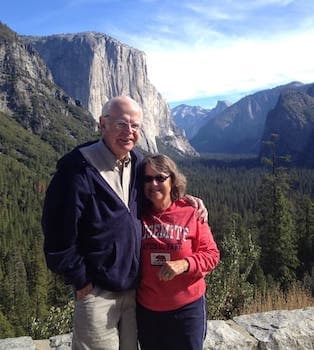
Ted Mooney, P.E. RET
Striving to live Aloha
(Ted can offer longterm or instant help)
finishing.com - Pine Beach, New Jersey
August 2019
A. Salt spray testing is the most frustrating thing...
I can think of a couple points to look at when you approach this problem. Old panels of course are a case of garbage in, garbage out.
Are you passing 336 on other anodized processes? Sealed? Dyed? But still failing ptfe?
What are your rinses like? Do you have a really good clean rinse after the ano tank? <1000 ppm for sure; the cleaner the better.
Ptfe has a working pH range that is pretty high. Be careful not to drag in any sulfuric, and set it towards the higher end of the working range before use to give yourself some wiggle room. And the tank needs to be clean. If you get any crane grease drips in there, get them right back out.
Also, and this is something someone told me over a third margarita at a conference, so take it with a grain of salt (and a slice of lime?): don't over-rinse after the ptfe tank. It doesn't sit as nicely in the microscopic honeycomb as conventional seal does.
Thankfully we haven't been asked to run that test yet but hey, next audit I half expect them to remember we offer it and start waving 3x10 panels at us ;)
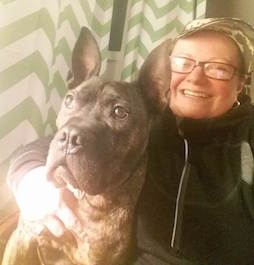
Rachel Mackintosh
lab rat - Greenfield, Vermont
September 7, 2019
Q, A, or Comment on THIS thread -or- Start a NEW Thread