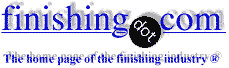
Zinc Phosphate coating problems & issues; Q&A's
-----Q. Hello Daniel,
I agree with you that chromate is a better surface modifier than phosphate solution.
Is it better to use a wash primer with chromates (instead of phosphates) to prepare a bare steel surface before paint?
Regards
- Minneapolis, Minnesota
February 1, 2023
A. Hi Jose,
Not for bare steel, chromate conversion coatings are only for substrates that can be passivated by chromates or high oxidizing agents forming chromates. Steel is not one of these substrates!
Can be used over zinc, zinc alloys, aluminium, zamak (as it is a zinc alloy), cadmium, magnesium, tin and their alloys. Other chromate conversion coatings may be too thin or discontinuous to have any beneficial properties.
Thin or thick phosphate coatings are good preparation for pre painting! You need thin grained and uniform phosphate to get the best appearance :)
Good luck!
- Cañuelas, Buenos Aires, Argentina
Q. Daniel,
I will use thin phosphate since the surface is bare steel. I am using a PPG 2 parts washing primer that is scarce in the market: 3YE-116A HEAVY METAL FREE 2 PKG VINYL CONVERSION COAT.
Do you have any experience with this wash primer? What other comments regarding mine?
Regards
- Minneapolis, Minnesota
February 11, 2023
Tip: This forum was established to build camaraderie among enthusiasts through sharing tips, opinions, pics & personality.
The curator & some readers who publicly share their info will be less likely to engage with those who don't.
A. Hi José,
No, I don't have experience with those types of wash primers, so I can't help you with this one. Maybe some other colleague has a word on it.
PPG has little to no presence here in Argentina, so they have products only for punctual applications.
Hope you can solve this issue!
- Cañuelas, Buenos Aires, Argentina
⇩ Related postings, oldest first ⇩
When things are electroplated, they're made cathodic (negatively charged) to attract the positively charged metals ions dissolved in the plating solution. As a result, a side reaction occurs: to some extent water in the solution is electrolyzed into hydrogen gas and hydroxide:
2H2O => H2^ + 2 OH
This is of no concern when plating low carbon steel, but in hardened steel this hydrogen can permeate into the metal and terribly weaken it, turning it to a glass-like brittleness such that it can spontaneously fracture under a heavy load or sudden impact ("hydrogen embrittlement"). The routine cure is immediate baking, and you can search the site for more about embrittlement and baking.
Can zinc phosphate replace zinc plating?
Q. I am looking for info on zinc phosphate. The application is a small set screw used to hold a lever handle on an interior door and the screws have been zinc dichromated for many years. Recently the screws have had a nasty hydrogen embrittlement problem - and it appears to be linked to the plating process. We have used three different suppliers and all have the same problem - perhaps the material is the problem.
Temporarily we have switched to zinc phosphate. I am investigating the possible change to zinc phosphate on a permanent basis.
I am interested in the corrosion resistance of zinc phosphate as compared to zinc dichromate. I have some info from our supplier, but the info on the phosphate seems a bit vague.
We have a salt spray chamber and I will begin testing some assemblies today.
I would appreciate any info or direction on this subject.
1998
A. If this condition appeared abruptly, my guess is that the screws are of a higher carbon content or are heat treated to 24 Rc or harder.
Prebake is one help. Longer post plate bake is another. Probably the biggest is getting the screws into the oven faster after plating. All three together should make your problem less.
- Navarre, Florida
A. CHRIS,
IF YOUR PART IS ROCKWELL 38C OR HIGHER IN HARDNESS, THEN THE COATING SHOULD BE MECHANICAL ZINC WITH A DICHROMATE FINISH. BE CAREFUL USING PHOSPHATE COATINGS, WE ARE PRESENTLY DOING A PHOSPHATE - BAKE - OIL FOR A CHRYSLER UNDER THE HOOD SPRING AND THE SPEC CLEARLY STATES 'NO ACID PICKLE'.
CONTACT GORD ALLISON AT Macdermid IN WATERBURY CT, HE CAN SEND YOU A 5 YEAR CORROSION STUDY SHOWING ALL ZINC FINISHES.
- CAMBRIDGE, ONTARIO, CANADA
A. Chris,
Hydrogen embrittlement (HE) is associated with zinc plating. A number of processes have been developed to minimize and even eliminate hydrogen embrittlement. Acid chloride zinc plating process is able to reduce the HE problem to some degree. Most importantly, baking is strongly recommended to immediately follow the zinc plating process in order to eliminate the risk of HE. I suppose your suppliers should be able to solve the problem related to plating processes.
You mentioned that you are intending to replace zinc plating with zinc phosphating. Of course, zinc phosphating can provide the limited corrosion protection to steel substrates. However, zinc phosphating is generally used as a paint base instead of a major corrosion protection measure. This is because zinc phosphating coatings cannot provide the corrosion resistance comparable to that resulting from zinc plating with the chromate conversion coatings. Zinc plating has a sacrificial function in protecting steel substrates while zinc phosphating only acts as a protective barrier with some micro pores.
Ling
- Grand Rapids, Michigan
Multiple threads merged: please forgive chronology errors and repetition 🙂
Zinc Phosphating Defects (Nubbing)
Q. Hello,
Tai and Myself have been following the postings here at Finishing.com and have yet to post a question or response. We have come to appreciate this excellent resource of information and hope that we may be of assistance to the finishing community in the future. Tai is The Quality Control Supervisor, and I am his assistant. We work in an E-Coat Facility using Chemfil and PPG Chemistries.
Our Problem,
Excessive Crystal growth (nubbing) in the zinc phosphating stage. On our hoist line we process steel, zinc plated steel, Galvanneal and electro-Galvanized parts, and on rare occasions a bar of Aluminum. We only have a problem with nubbing on the zinc-plated parts.
For the processing of these parts we use mildly alkaline cleaners with both dip and spray rinses prior to the titanated phosphate pre-rinse and a zinc/nickel phosphate bath.
- - This problem has occurred sporadically across a bar of racked parts with no preferred location.
- - With low and high agitation in the phos tank
- - With fresh and old: cleaners, rinses, and pre-rinses
- - We have even replaced the entire phosphate solution.
- - With high and low additive levels
- - With high and low Fluoride levels in the phos bath.
One bar may have no nubs, the next every part will have them and the next will only have 20 pieces / 800.
We have tried to reproduce this problem in the lab with no success (most likely due to its sporadic nature).
We have worked on this costly problem along with our suppliers for some time with no resolution.
Any ideas would be greatly appreciated
Regards,
metal finishers - Mississauga, Ontario, Canada
2000
A. Chasing sporadic problems is a pain in the butt. My first thought is that maybe you're getting parts with some inclusions in plating, or stress cracks, or maybe just a soft spot in the plating. Any of these things will cause the coating to form differently in those areas.
Try flexing a part to from stress cracks, smack one with a wire brush to from dimples in the surface, and maybe abrade one to see if the abraded area looks like the "nubbing" problem.
Another thought is that your cleaning may not be up to snuff, but it sounds like you've addressed that, and chemfil products will do the job. Maybe check the location on the rack of the problem parts to see if it coincides with any apparent dripping or running of solution that could carry trash onto the parts. Good luck.
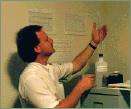
Jeff Watson
- Pearland, Texas
The Problem has been eliminated. After changing jobs, to work in a zinc plating plant, Tai and myself have been better able to troubleshoot the problem. We hypothesized that there were catalysts trapped in the matrix of the zinc that caused the phosphating reaction to be accelerated. The highest concentrations of these "catalysts" would exhibit the nubbing effect.
We then took a look at a very long list of possible substitute chemicals which can act as a catalyst in the phosphating, and found that an extensive number of different organics can behave in such a manner. And as we were aware, zinc plating uses many organic components to achieve the desired plating properties.
We then decided to test the zinc phosphated part for phosphate coating weight and found them to be very high. Tai then tried to significantly reduce the immersion time in the phosphate bath, resulting an an acceptable coating weight with no nubbing. So, it seams that this reduced time is enough to achieve desired coating weights without promoting the localized excessive phosphate crystal growth.
Regards,
- Mississauga, ON, California
2002
Multiple threads merged: please forgive chronology errors and repetition 🙂
Q. We are doing Zinc Phosphate and Stearate coating on Carbon steel wire rods.This steel is meant for further drawing. Our present systems include acid pickling, rinsing, phosphate coating, rinsing again and stearate coating.
The entire process is a batch process carried out in respective process tanks. We would like to know the following :
a. Method of getting a uniform phosphate coating.
b. Similarly, method of getting uniform stearate coating.
c. Sometimes we find that after the phosphate coating and stearate coating the material develops rust spots.How to prevent this?
d. Above Coated material at times gives sound while wire drawing to a smaller size. What could be the reason?
Note: Phosphating is done at 65 °C and Stearate coating is done at a temperature of 65/75 °C.
- Navi Mumbai, Maharashtra, India
2001
A. Hi,
Let me answer a step at a time:
a. Method of getting a uniform phosphate coating. Presumably you are using HCl acid; ensure sufficient time for complete descaling; tease the coil out on the hook to open the coil up to the solutions; immersion rinse in water then power wash the coil with high pressure sprays. This will remove residual acid and smut. Failure to rinse properly will contaminate the phosphate and slow the process up. Give 10 min process time in the phosphate minimum.
b. Similarly, method of getting uniform stearate coating. Alkalinity of the soap bath must be controlled. More alkaline soap will give heavier soap weights but will also dissolve more phosphate. A rinse in borax
⇦ on
eBay or
Amazon [affil links]
solution before soaping will protect the soap bath from acidic carryover.
c. Sometimes we find that after the phosphate coating and stearate coating the material develops rust spots.How to prevent this? May be due to poor storage conditions; poor rinsing; poor soap coating; incomplete descaling.
d. Above Coated material at times gives sound while wire drawing to a smaller size.What could be the reason? Note : Phosphating is done at 65 °C and Stearate coating is done at a temp of 65-75 °C. Noise will be failure of the lubricant layer and will cause premature wear of the dies.
Hope this helps,
- Croydon, UK
Zinc phosphate white stain
Q. Hi,
My company does defense contract work , mainly 60 mm mortar rounds, and they require a zinc phosphate pretreatment to paint. My phosphate line consists of an emulsifier cleaner(200 °F) hot, cold water rinse, phosphoric acid, 2 rinses, titanium activator, zinc phosphate(run w/sodium nitrite)(160 °F)rinse, and finally a phosphoric/chromic acid final rinse(160F). Problem is that I am getting a white stain on the outside of the part. I clean the line once a week and all my chemicals are in good standing (titrations good, and fresh chem.) I tried diff things such as adding neutralizer to rinse tanks, skipping certain tanks to see where the problem may lay. I think I narrowed it down to 3. the phosphoric acid (not rinsing good enough) the rinse tanks(where I believe 75% of plating problems occur) and finally the titanium activator, which is a salt, and has the power to stain parts. It may also be the phosphate bath, but I never had a problem w/this until recently.Ii didn't change anything on the line. I would like to know if anyone can help me.
Thank you,
- Nanticoke, Pennsylvania, USA
2003
A. Let me try to help you :
Your process is not the optimum one :
a.First stage: Instead of hot emulsifying cleaner replace to Alkaline colder cleaner. There are a lot in the market .
b.Second stage: Phosphoric Acid, cannot be alone component in the bath, the bath must have surfactants, I suggest as in the previous stage, buy yourself one of the commercial products in the market.
C. The two next stages must be commercial products too, not self formula products .
D. The problem might be the final rinse stage, there is no need to heat this stage, if you heat it to such a high temperature the water must be Deionized.
Shortly : Try to use well proved commercial products I'm sure you have several suppliers in your area. Do not heat the last final rinse it is not necessary at all.
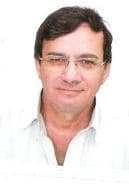
Yehuda Blau
YB Plating Engineering and Quality - Haifa Israel
A. Because your phosphate bath too hot, I suggest 140 °F max
and don't add anything (soda ash) in rinse tank, just fresh water, because your's pre-treatment line has a post rinse (Cr rinse).
- Jakarta, Indonesia
August 14, 2009
Must zinc phosphate be removed before heat treatment?
Q. Please can you tell me if Zinc phosphate can cause problems in any heat treatment processes, e.g., gas carburising. The problem we hope is from zinc phosphate left on cold drawn wire products and would like to know if this zinc phosphate should be removed prior to heat treatment.
Kind regards,
heat treatment - Brierley Hill, West Midlands, England
2003
A. I have been told by the manufacturer that zinc phosphate will destroy the carbon probe and must be removed before heat treating. If you are not running a carbon probe in your furnace I am not aware of any other problems.
Art BurkeAMT Heat Treat - Fort Worth, Texas
2005
Q. I am having a problem. I am in a pipe threading company. All this while, we are running the zinc phosphating process on pipe thread. The pipes came from L80 grade, K55 grade, P110 grade, and Q125 grade. Our zinc phosphate process are as follows;
Use kerosene to clean up the pipe thread (having grease on it)
Tank 1: Alkaline cleaner
Tank 2: Rinsing Water
Tank 3: Rinsing Water
Tank 4: Zinc Phosphate
Tank 5: Hot water rinsing
Tank 6: Oiling
The last process is to apply grease and install protector to protect the thread.
However, we always have problems of thin layer of zinc phosphate especially on the P110 and Q125 grade. After the process, you can see that some portion is not fully coated with zinc phosphate. We have to do rework.
I would like to know what are the causes? Why the L80 grade does not give us such problem as compared to P110 and Q125 grade? It has been many years that we have no answer on that and hope someone can let me know the major causes and how to solve this problem? Thank you.
Pipe Threading - Malaysia
2005
Black spots and non-uniform coating
Q. After Drawing of High Carbon Steel (SAE 52100) Wire rod in the desired size, say from 12 mm to 10.40 mm or 9.80 mm, Black spot are generated on the wire surface i.e. non uniform coating is observed on the wire surface. While forging (Producing Roller) at customer's end they face problem of Muck Formation due to poor Phosphate coating. Our standard Phosphate dip time is of about 20 min. and Pointage is 18 - 20
J R Chaurasiya- Navi Mumbai, Maharashtra, India
February 5, 2010
A. Dear sir. The most important spots are TOTAL ACID. FREE ACID, OXALATE TEST, Fe IN YOUR PHOSPHATING SOLUTION.
TA=35-40
FA=6-8
OXALATE TEST=1.5-2.2
Fe=2-3
temperature 75-80 °C
Wire drawing lubricant must contain high amount of extreme pressure in it.
Never use single or self-accelerated phosphating solution; they cause hollow spots on drawn wire.
Sulfuric acid 15% pickle -- force rinsing -- deep rinsing -- phosphating -- borax
⇦ on
eBay
or
Amazon [affil links]
solution dip at 90 °C.
reza
- Tehran, Iran
June 11, 2012
Black patches and pits
Q. Hello sir, we're doing a phosphate coating process for various dia. coils. In this we are frequently facing black batches and pitting defects in this process. I need your suggestion for sorting out this problem.
Vigneshwar Maruthapillai- Tamilnadu, Karur, India
June 20, 2013
A. Hi Vigneshwar,
You are going to have to give us a lot more detail before anyone can help you.
Firstly you need to explain the process you use (pre-cleaners, phosphate system, times, temperatures, immersion or spray process).
Then you need to tell us what you have already investigated and eliminated as potential failure sources. Have you done a full chemical analysis of all the treatment baths involved? Are they all within control limits?
Finally, and I seem to say this a lot, go and walk your process, follow every step from on-receipt of material to final sign off. This will give you an idea of where you need to concentrate your efforts for improvement.
Aerospace - Yeovil, Somerset, UK
Please never tire of your suggestion that people walk the process, Brian.
As General George Patton said:"No good decision was ever made from a swivel chair."
Regards,
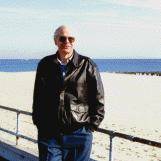
Ted Mooney, P.E.
Striving to live Aloha
finishing.com - Pine Beach, New Jersey
Q. Hi,
I came across this forum today and found some very educating and helpful information related to Chemical treatment processes.
We are into the processing and Heat treatment of wire rod and we are facing the following problems:
1. Time taken for pickling is too much (It takes 2 hours on average to finish pickling)
2. Improper Phosphate coating
3. Customer complaints of pitting in drawn wire
4. Dark spots appear and material begins to rust again if not used for drawing within a day.
Our process is following:
We are using HCl for Pickling Wire rod coils (we maintain strength of Pickling bath at around 5-7%).
After Pickling we Wash the pickled wire coil with water jet.
Then place it in Phosphate solution for 25-30 minutes. Our Zinc phosphate solution has TA of 22-24 and temperature of 50 °C.
After Phosphate coating we place it in Lime tank, the temperature of which is maintained at 40-45 degrees, then we dry the bundle using high speed fans and use the dried bundle for drawing.
Please assist me, as to what changes should be made in the overall process to ensure better quality of material coming out from Chemical Processing.
Steel wire processing and heat treatment - Ludhiana, Punjab, India
August 2, 2014
A. Hi Anshul. My initial thoughts, subject to clarification, are that 2 hours in pickling is at least 10X what I'd expect as reasonable. Although I think that the HCl should be about 2-3X stronger, these coils seem to either have extraordinary scaling, or you are pickling them as a bundle such that the acid doesn't get into the middle and work right. Is there any feasibility of obtaining pickled and oiled rod from the mill? It sounds like you may be doing primary pickling without the proper setup for it (scale breaking, continuous coil processing).
A "lime tank" is not within my personal experience. Does it contain highly alkaline water of lime? I believe the more traditional approach is a passivating rinse and/or a D.I. rinse after phosphatizing. Thanks for any clarification.
Regards,
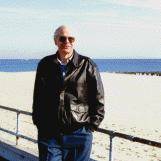
Ted Mooney, P.E.
Striving to live Aloha
finishing.com - Pine Beach, New Jersey
Q. Currently my company is conducting its own Zinc Phosphating process with Sterate Soap to act as a lubricant for deep drawing from coils of steel sheet stock. The process involves a coining step. This is creating issues with pitting. During coining something gets caught as the metal is flowing and is incompressible and creates pits in the parts.
What I am wondering is, do you know of what qualities of the coating (crystal size, microstructure density, layer thickness, etc) I should be monitoring. Also, what kind of microstructure/layer thickness should I be trying to achieve? Is there an efficient and accurate way to measure layer thickness besides gravimetrics?
Thank you.
- Charlotte, North Carolina
October 21, 2014
Q. Zinc Phosphate coating failing test panels
Process is (sorry I'm not allowed to give too many specifics due to ITAR and policy restrictions):
1) Alkaline clean (140 °F) with a common commercial cleaning solution
2) DI Rinse (125 °F)
3) Pickle with a common commercial solution
4) DI rinse (ambient)
5) Phosphatize (165 °F) common commercial solution
6) DI rinse (ambient)
7) Seal (130 °F) common commercial sealant
8) Air dry
We have weekly test panels that are examined by SEMS. Occasionally they fail to have sufficient crystal growth. A longer immersion time will usually give just barely acceptable crystal growth. Titration analysis shows all solutions to be well within targets.
What could be causing this lack of crystal growth?
Aircraft Component Manufacturing - Dayton, Ohio, USA
May 13, 2016
A. Hi Mark,
Pity you can't give us much more detail, but understand how difficult it is to work with ITAR...
Anyway, phosphate coatings are normally controlled by coating weight, so that you have a quantitative measure rather than a qualitative one, which can be open to interpretation. MIL-DTL-16232 [from
DLA]
is a good place to start on a coating weight control method.
Other than that, what else can effect coating crystal growth? The temperature of the phosphate solution, insufficient accelerator, poor pre-cleaning quality and insufficient processing time in the phosphate bath, just to give you a start.
Aerospace - Yeovil, Somerset, UK
![]() |
Aircraft Component Manufacturing - Dayton, Ohio, USA A. 1. The "pickle" may be too harsh. Try getting the rust off mechanically and skip the acid for a finer grain structure. ![]() Robert H Probert Robert H Probert Technical Services ![]() Garner, North Carolina ![]() |
Q. Hi,
My company performs zinc phosphating acc to MIL-DTL-16232 [from
DLA]
G Type Z, Class 1,2 and 3. (Using product Oakite Gardobond Z 3190)
Currently we have a chromic acid rinse/passivation as described in the MIL-standard para 3.2.5.
In order to comply with customers' demand for non hex-chrome passivation we want to establish such a process.
We have tried the Chemetall product Gardolene D 6800/6 with little success, i.e. we fail in our internal 2 hour salt spray test.
Does anyone have a solution as to finding a hex chrome free passivation which will make it possible to pass the 2 hour salt spray test?
Best regards,
Bandak NCT AS - Notodden, Norway
November 30, 2017
A. Hi Hans,
First, you should see if there is any imperfection in your coating process. All hex chrome-free sealers have less resistance than hex chrome sealers, and they are more expensive and less resistant to contamination.
You should try to increase coating weight and try again, or try with another sealer. Chemetall has two other sealers that you can try, all more expensive than the first one.
My experience with non chromic sealers is not so good, so I would test those alternatives one by one in lab and try the best one.
Best of luck to you!
Regards :)
TEL - N FERRARIS - Cañuelas, Buenos Aires, Argentina
Q. We are zinc phosphating and e-coating a zinc plated part (CRS substrate) and we are not getting a uniform zinc phosphate coating. What pretreatment process characteristics are key to getting a uniform zinc phosphate coating over Zn?
Thank You!
- Grand Rapids, Michigan
January 29, 2018
Hi Tim. I don't know the answer but am glad to see your posting! I have long felt that if zinc plating is going to be painted, it ought to be phosphatized rather than chromated because the adhesion will be better.
But on the other hand, I have never seen a plating shop that didn't chromate their zinc plating. So in this age of trivalent chromates plus topcoats, I'm wondering whether you truly are attempting to phosphatize a plain zinc plating, or if it already has a chromate & topcoat that are making phosphatizing difficult :-(
Regards,
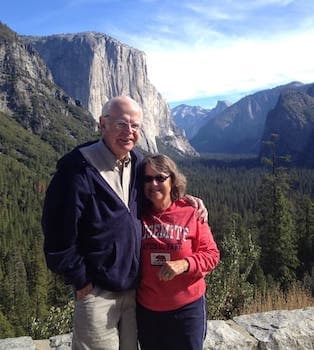
Ted Mooney, P.E. RET
Striving to live Aloha
finishing.com - Pine Beach, New Jersey
A. Hi Tim,
As Ted mentioned, if the plated part has a topcoat, it will be difficult to deposit a uniform coat of zinc phosphate. If it isn't, you need a accelerated zinc phosphate bath, because free iron-based phosphate baths are not suitable (in my experience) for that type of work.
We have an accelerated (nitrite) phosphate bath, with some nickel content (it makes the reaction a little faster and improves coating weight), originally formulated as a wire phosphatizing product. We use it on fasteners over steel or over zinc (chromated or not). Coating thickness is generally uniform, so it can be done and it can be controlled with the right parameters :)
So, if you may, tell us a little more about the zinc plated parts and about your phosphate bath.
Best of luck!
TEL - N FERRARIS - Cañuelas, Buenos Aires, Argentina
A. Hi Tim,
Why are you Zn phosphating the job which are already Zn plated? Do CED directly on Zn plated job but before that remove any passivation present on Zn plating.
- Nashik, Maharashtra, India
Q. Hello, why are phosphate crystals coarse and how can we have a soft zinc phosphate?
Ahmad hashemi- qom saas iran
September 29, 2018
A. Hi Ahmad. Are you using a grain refining pre-dip as explained on this page which we've added your inquiry to? If you search the site for "coarse zinc phosphate" you'll find several more threads on the subject if the answer isn't on this page. Good luck.
Regards,
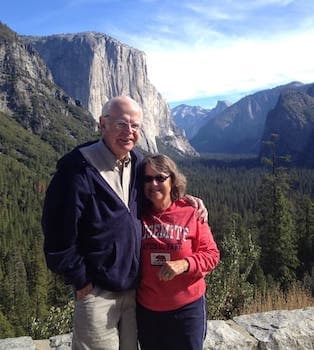
Ted Mooney, P.E. RET
Striving to live Aloha
finishing.com - Pine Beach, New Jersey
Q. Follow up question-re: 1998 post by-"Ray D.-- says "Chrysler spec says 'no acid pickle' "--what is the alternative?
Jay Dobbssteel processing - chicago Illinois usa
November 6, 2018
A. Hi Jay. Abrasive blasting is a general alternative to pickling which leaves the surface active and ready for a next step. Alkaline derusting might be an alternative to pickling for some processes. Good luck.
Regards,
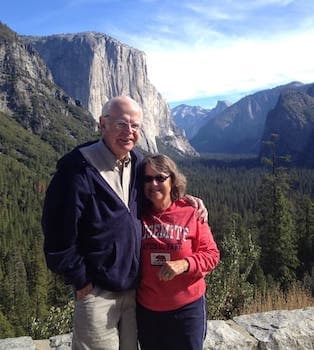
Ted Mooney, P.E. RET
Striving to live Aloha
finishing.com - Pine Beach, New Jersey
Q. Does zinc phosphate coating affect hardness testing values?
CAMILLE HERSHEY- HUMBLE, Texas USA
December 20, 2018
Zinc phosphated surface is rough for first few days of each new bath
Q. We run a 7 tank zn phos line for OEM part. We have a roughness issue at the start of a new bath. The roughness settles down only after 4-5 days on the components. Any idea why this happening and how to reduce them when we set up a bath?
Karthick rajaSurface treatment - Bangalore , Karnataka, India
February 15, 2019
A. Is this a heavy zinc bath? What do you do to build iron on a fresh bath makeup? Sounds like it takes you a couple of days to build sufficient iron from processing naturally.
Second question, what's your starting FA? If you are making up on the high side you'll have a low Ratio until you take the edge off the bath.
- Agawam, Massachusetts
Q. Hi sir I am Rajkumar zinc phosphating 13-tank process alkaline,rustban, oxalic, plxgi, phosphating.
Phosphating temperature 75 °C to 85 °C. Chastain ring will process two-pass ip 18 mettiriyal output black colour, but ring is brown colour.
Ip 18 time alkaline 60 sec temperature 85 °C
Rustban 150 sec
Oxalic 120 sec
Phosphating 60 sec
Hot water passive a 30 sec
Hot air 200 sec
Rustban. 100 sec
Plxgi 30 sec
Phosphating 50 sec
Hot water 30 sec
Hot air 200 sec
Brown issues - Chennai,Chennai India
May 18, 2019
Good luck, Raj, but I don't have much idea what you're talking about except that your phosphating is brown and I think you wish it was black :-)
Sorry, but "Chastain", "two pass", "ip", "18", "mettiriyal", "Plxgi" mean nothing to me :-(
Hopefully another reader will be more familiar with those terms.
Regards,
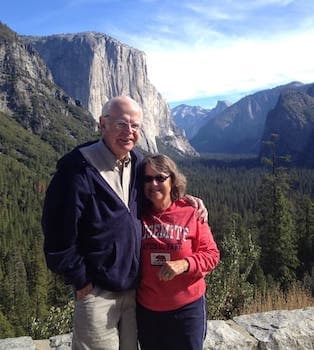
Ted Mooney, P.E. RET
Striving to live Aloha
finishing.com - Pine Beach, New Jersey
Q. Hi, my name is Anuj. We coated our couplings with Zinc phosphate coating. But the coating seems to peel off during shipping. Coating gets adhered to packaging. There is non-uniformity in coating too. Please could you suggest solution to this situation.
Can we use zinc phosphate coating to give anti corrosive coating to high alloy steel? Which coating is better zinc phosphate or manganese phosphate in terms of corrosion resistance and wear resistance ease and cost efficiency.
- Pune, India
July 19, 2019
A. Anuj,
Usually people apply an oil or other RP solution to the surface of the phosphate. Using an inhibitor or seal after rinsing the phosphate solution off may help the corrosion resistance of the couplings. The phosphate coating alone is only moderately corrosion resistant.
Non-uniformity AND the peeling of the coating could be tied to pre-treatment. Was the part completely clean (able to pass the water break free test) before going into the phosphate solution?
Zinc phos can apply heavier coating weights than manganese phosphate and is typically applied in painting application, steel wire phosphating for corrosion protection and with newer microcrystaline zinc phosphates there is even more use of them in pretreatment to prepare a surface to accept a secondary coating.
Manganese phosphate is primarily used as a surface finish to improve the reception ability of oils for corrosion protection and as a break in lubricant for pistons and things of that nature to prevent galling in the initial phases of use of the pieces.
Technical Sales Rep - Cleveland, Ohio
Q. Thank you Issac,
Is high alloy steel suitable for zinc phosphating?
We wanted to give anti corrosive coating for C5M (H) category according to ISO 12944. would zinc phosphating coating alone be sufficient to endure this condition or should we adapt any another coating option. please suggest
- Pune, Maharashtra, India
Q. I'm getting coarse Crystals on the underside of my parts repeatedly.
Process is as follows:
Cleaner
Rinse
Pickling acid
Rinse
Grain refiner
Phosphate
Rinse
TA 52.2
FA 11.2
Iron 4.3
Temp in phosphate is 165 °F
Titrations are in mLs and based on 10 mL sample.
I recently had to make a new phosphate bath.
The previous bath was running identical to what we have now and producing beautiful parts.
- Round rock, Texas
September 13, 2019
----
Ed. note: Eric also posted rather similarly on topic 14221 for a deeper understanding of his situation.
Black line on the wire after zinc phosphating
Q. hi
Our company works in the field of drawing and phosphate and annealed wire.
Our problem is the existence of a black line along the wire after phosphating.
The wire is annealed before phosphate.
This black line does not disappear after washing with acid.
In addition, our coils are closed when phosphating.
Our method of phosphating is immersion.
tanks
- iran
October 15, 2019
Q. We are doing zinc phosphating. We are not getting uniform coating: white patches are there.
Phosphating pointage - 29
FA -1.8
- Kolhapur, Maharashtra
July 7, 2020
? Hello Suraj,
You should take some pictures of the problem, introduce the base material to us, and how your phosphate line is conformed (degreasing, pickling, how many rinses, anything else?).
Without this information, all we can do is speculate :)
Best wishes,
Daniel
- Cañuelas, Buenos Aires, Argentina
September 9, 2020
Q. My question is more of a theoretical one, and it deals with the fact that zinc phosphate (hopetite/phosphophyllite) attaches to the metal substrate.
Why it does that?
What can we do to make sure it does it evenly and uniformly across the surface and with proper weighting?
What can we do to ensure that it's not easily scratched off?
Any tips would be highly helpful.
- Adelaide Australia
February 19, 2021
by Biestek & Weber
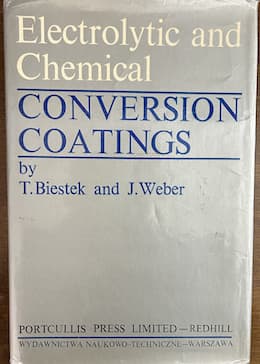
on AbeBooks
or Amazon
(affil link)
A. Hi Waqar. According to Biestek & Weber the short answer to why phosphates attach/adhere well is that they are formed "at the very reaction site". In other words, there is not a reaction out in the bulk of the solution which causes the precipitation, but a conversion reaction right at micro-sites on the surface of the metal.
I don't have enough personal experience to be able to tell you what makes for evenness of deposit and scratch resistance, but if you can get access to the book, it's very good at the theoretical level. Or you can read this thread and thread 13366 for a lot of readers' solutions to zinc phosphating issues.
But please try to post your situation and what motivated this "theoretical one"; as you are seeing here, readers usually exhibit little interest in looking up things in books, nor in sharing their experiences when the OP doesn't share theirs :-)
Luck & Regards,
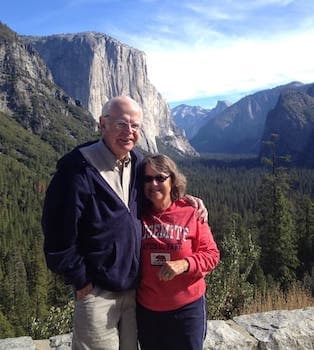
Ted Mooney, P.E. RET
Striving to live Aloha
finishing.com - Pine Beach, New Jersey
⇦ Tip: Readers want to learn from your situation;
so some readers skip abstract questions.
Q. Purple Top Coat Stain on a Zinc Phosphate Steel Part?
Will excessive residual phosphate coating (i.e/, TT-C-490 [from DLA] ) cause a staining to pass thru the dry paint film (purple)?
Joe Schilling- Burlington Iowa
April 6, 2021
Q. We have application of zinc phosphating process in S.G. [spherical graphite] Iron material. We are facing issue of patch mark (uneven white / dark layer) on the surface. Can you please suggest the probable root cause and precautions to prevent.
Chavda Rahul G.- Ahmedabad, Gujarat, India.
May 29, 2021
A. Hi Chavda,
I would suspect that in the general case, the cause of patches is improper cleaning or activation such that the substrate surface isn't homogeneous. But in the case of S.G. Iron you don't have a homogeneous surface anyway.
I think step one is to process some plain steel parts and see if they exhibit patches. If the steel parts exhibit the problem, scrub them with a scrub brush and pumice-detergent solution before running them through the line so you can rule out inadequate cleaning as the cause. Only if the pumice-scrubbed steel parts are patchy should you turn your attention to the phosphating solution and its operating parameters.
Luck & Regards,
Ted Mooney, P.E. RET
Striving to live Aloha
finishing.com - Pine Beach, New Jersey
(to help readers better understand the Q&A's)
CED = Cathodic electro deposition
(electrocoating/electropainting with the work cathodic (negatively charged) rather than anodic (positively charged).
AED = Anodic electro deposition
AED was once a popular alternative but the site moderator hasn't heard of AED in years now.
Electrocoating, like other finishing processes, requires pretreatment of the substrate, and zinc phosphatization is a very good and popular pretreatment for steel parts.
A. Hi: This is how foam formation in phosphate bath will effect the coating.
I found like dry marks after my CED coating. Then we verified that wherever foam forms over the vertical substrate, in those locations we identified those marks after CED.
We found the root cause, and how the foam can affect the coating ... for discussion and knowledge.
- Chennai Tamil Nadu, India
August 5, 2021
⇦ Tip: Readers want to learn from your situation;
so some readers skip abstract questions.
Q. In an experiment, what are the normal voltage range & current that should be supplied to an electrolytic zinc phosphating bath?
Mihiri Wijerathne- Badulla Sri Lanka
February 10, 2022
by Biestek & Weber
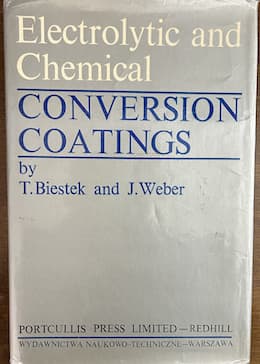
on AbeBooks
or Amazon
(affil link)
A. Hi Mihiri. According to Biestek & Weber, alternating current at 60 Hz and 3.5 A/dm2. The voltage would depend on electrode to component spacing but my guess is somewhere between 6 and 18 volts.
Please introduce yourself and your situation; it can be very helpful towards preventing miscommunication and consequent poor answers; plus readers very rarely respond at all to abstract questions. Thanks.
Luck & Regards,
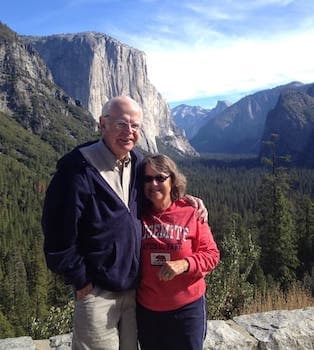
Ted Mooney, P.E. RET
Striving to live Aloha
finishing.com - Pine Beach, New Jersey
mpt =
ED = electro deposition (electrocoat/electropaint)
FA = free acid
TA = total acid
ACC = accelerator concentration
Q. Hello All,
I am working in a paint shop in automotive industry. Applying zinc phosphate mpt before ED paint. Recently suffering harsh mark after ZnPO4 tank.
Phosphate Parameters:
FA: 0,9 ml
TA: 22,5 ml
ACC: 3,2 g/l
We tried to increase activation concentration, reduce temp. and FA but it does not help.
I would be very happy if I could get your suggestions.
- India, Chankan
May 24, 2022
![]() |
? Hello, - Wooster, Ohio A. Hi Siva, Quality Manager - Cañuelas, Buenos Aires, Argentina |
A. Hi Kishore.
Please try to include your parameters, a pic if possible, and replies to Daniel's possibilities. Thanks!
The shortcut of saying you have "the same problem" doesn't move the discussion forward because surely your FA, TA, ACC are not identical to Siva's, and if responders had the benefit of seeing your parameters as well, and what you actually tried, they'd have twice as much data to work with :-)
Luck & Regards,
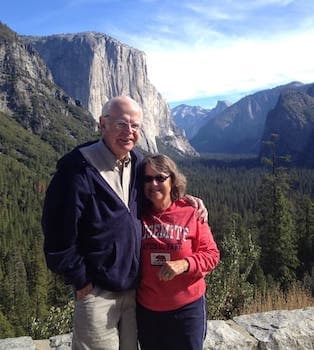
Ted Mooney, P.E. RET
Striving to live Aloha
finishing.com - Pine Beach, New Jersey
Q. Free Acid- 1.10
Total Acid-12.90
pH- 3.05
Fluoride- 449
Zinc- 2087
Nickel- 490
Manganese- 940
Phosphate- 4244
Nitrate- 3682
This is the data after acid pickling the zinc phosphating bath. It is a fresh bath. It is 7-stage zinc phosphating (pre wash, cleaner, zinc phosphating, city water rinse, non-chrome seal, Di wash, DI rinse )
We are also experiencing mapping issue. It is not in all the products, mostly in Aluminum substrate.
- wooster, Ohio
July 6, 2022
Ed. note: Thanks Kishore!
? Hi Kishore,
How do you clean the parts you phosphatize? Do you use any activating process or grain refiner? If you don't have trouble with other materials, it shouldn't be a phosphate bath problem. But aluminium is difficult to deep clean, and you need the surface evenly active to your phosphating agent.
For this, there are the activation process/grain refiners. They produce evenly grain initiation spots to avoid uneven coating thickness/grain size.
You should (in my humble opinion) focus on your cleaning process!
Best of luck :)
- Cañuelas, Buenos Aires, Argentina
Q. Hi Daniel,
The cleaning process consists pre-wash (not a bath, just two risers on either side), next is alkaline cleaner bath spray and then a alkaline rinse bath spray along with the rinse conditioner spray with two risers on either side (grain refiner stage), which is about 6 seconds and then phosphating bath spray.
What are potential solutions to change in the current set-up?
Should we go with acid cleaners? The problem with that it is a mixed metal line, where we have galvanized steel as part of the process, in case should we implement a manual acid cleaning process for aluminum substrates before the pre treatment. Right now we are applying the highlighting fluid for all the parts.
Another question, we don't measure any of the parameters in stage 1 and 2, should we measure the Ti concentration and pH of the stage? Is there any range for Ti concentration and pH range? Should we measure the coating weight, SEM for these stages and look over the performance?
With all this said, if were are able to correct the cleaning process, can we reduce the mapping issue, because we do lot of metal finishing on the substrate.
Do you think anything to focus on the AL substrate itself?
Thanks,
Kishore
- Wooster, Ohio
A. Hi,
We faced a similar situation on GA where similar pattern appeared. It was the cleaner that was impacting the substrate, and later on the phosphate coating made it more prominent.
Please let me know whether the substrate gets dry after degreasing or remains wet.
In our case the substrate was drying and where it got more dry, more marks appeared.
Please review degreaser composition and process time.
- Lahore Pakistan
July 18, 2023
Ed. note: Thanks, Shahid. I think you may be right.

Q, A, or Comment on THIS thread -or- Start a NEW Thread