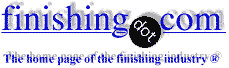
-----
How to improve the solderability of tin electroplating? Peel-off & Blistering
Q. We are using acid tin bath to plate on copper bars, we are getting frequent soldering issues, What are possible reasons for tin plating layer peel-off during soldering on copper substrate? Can anyone share your suggestions.
San Royal- Bengaluru, MLR, KA, India
April 24, 2024
A. Hi San.
Poor adhesion is probably caused by either inadequate cleaning or a pretreatment sequence which is inappropriate for the specific copper alloy you are plating.
Perhaps you can bake a few plated parts at soldering temperature to demonstrate whether or not the plating peels irrespective of the influence of solder?
Luck & Regards,
Ted Mooney, P.E. RET
Striving to live Aloha
finishing.com - Pine Beach, New Jersey
⇩ Related postings, oldest first ⇩
(to provide context, hopefully helping readers more quickly understand the Q&A's)
A general problem is that customers want bright tin plating, but the organic brighteners which bright tin requires interfere with solderability. Don't use bright tin plating unless you have to; and if you must, then use the absolute minimum :-)
Q. We're having trouble soldering brass parts plated with electro-tin plate, bright. Is the "bright" finish part of the problem? What is the best finish to call out? Thanks!
J. Willis1997
A. Dull Tin (no organics added) remains solderable longer, but fingerprints badly, so it depends.
Other possibilities: The bright tin bath may need a carbon treatment, or your pre-plate cycle may not be leaving a clean base metal. Do you strike first with cyanide copper ? Are you etching the brass before plating? I was going to write "over-etching", but you should not etch at all, the brass should stay bright in the pre-plate cleaning step, the cleaners could be too hot, the acid could be too concentrated.
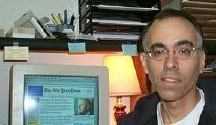

Tom Pullizzi
Falls Township, Pennsylvania
for engineers, shops, & specifiers
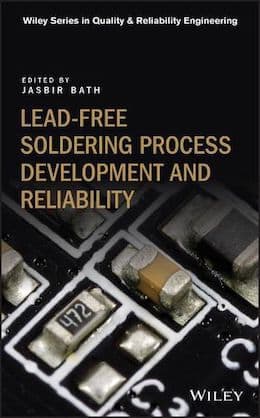
avail from eBay, AbeBooks, or Amazon
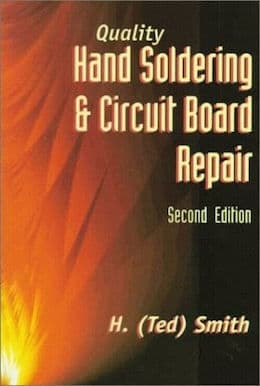
avail from eBay, AbeBooks, or Amazon
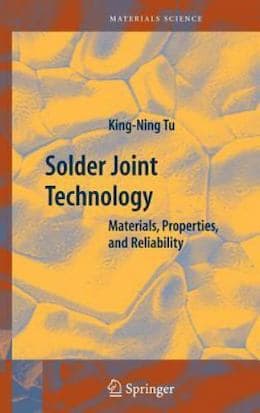
avail from eBay, AbeBooks, or Amazon
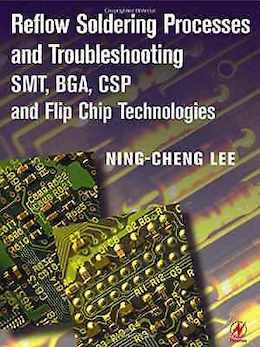
avail from eBay, AbeBooks, or Amazon
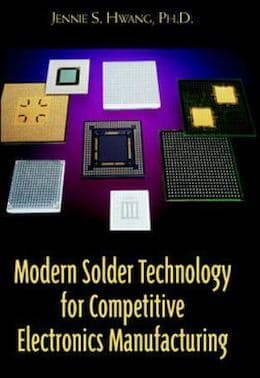
avail from eBay, AbeBooks, or Amazon
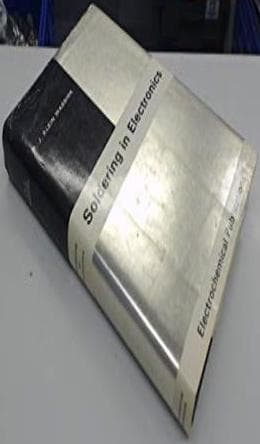
avail from eBay, AbeBooks, or Amazon
(as an Amazon Associate & eBay Partner, we earn from qualifying purchases)
A. You may try analyzing the tin plate bath for Copper, Zinc, Iron, etc. contamination. These contaminants are usually detrimental if over 500-1000 PPM.
good luck,
Dave
SUNNYvale, CA
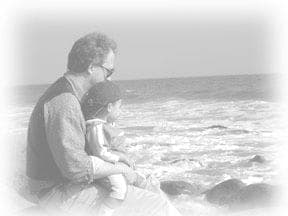
Dave Kinghorn
Chemical Engineer
SUNNYvale, California
A. How long between plating and soldering? If parts have been on the shelf for an extended period, especially if at elevated temperature or for more than six months, or if there is no barrier plate between brass and tin, zinc and/or copper diffusion can poison the tin. This usually shows as a dark discoloration of the tin deposit, but might also affect solderability. If freshly plated, ignore this line of reasoning.
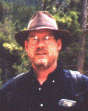
Bill Vins
microwave & cable assemblies - Mesa (what a place-a), Arizona
A. Another problem you may have is conversion of the metal tin plating to intermetallic. If the plating is mostly intermetallic, solderability is greatly diminished.
Intermetallic conversion is a time and temperature dependent process. Has the material been plated for a long time, i.e. many months? Have the parts been through any elevated temperature processing after plating? Either of these factors will contribute to formation of intermetallics in the plating. Intermetallic formation can be prevented in most cases by a nickel flash between the copper or brass and the tin.
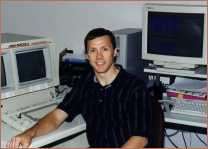
Larry Hanke
Minneapolis, Minnesota
Q. We have problem about pure bright tin plated on brass, we found soldering failure (condition used 60/40 Pb/Sn flux, 400-420 °C, 3 sec.) when plated sample have insert in polypropylene after have soldering this layer was peel off. How I can solve this problem, Sorry about my English.
Thanks,
Warawut PrachasirisakulMatsushita Electric Works, Ayuthaya - Thailand
2002
A. I suggest you should give a under coat of Nickel (3-5 microns) before plating bright Tin. Further, 60-40 can perform well at 230 °C, you need not have such a high temperature for your operation. Hope this should help solve your problem.
Good luck,
Karthik [last name deleted for privacy by Editor]- Singapore
A. As suggested by Karthik, use a Nickel undercoat and reduce the soldering temp. The liquidus temp for a pure tin alloy is 232 °C and the liquidus temp of 60/40 is 188 °C. Soldering at the temperatures you have stated will almost certainly be damaging to your tin plate. A nickel undercoat and a soldering temp of 230 should be sufficient.
Rich Mosley- UK
Q. I am a post-education in Beijing. My project is acidic Tin electroplating, The tin plating is bright, and passed the salt spray test. But the solderability is bad, I need some advise to deal with this problem.
MENG HUIstudent - Beijing, China
2004
![]() |
A. Sounds like you have an organic brightener film left on the tin surface. Try an alkaline cleaner after tin plating, and try to reduce the brightener concentration in your tin bath. ![]() Jeffrey Holmes, CEF Spartanburg, South Carolina A. The two major killers of soldering tin are too much brightener in the plate- use matte tin if you want better solderability and two: tin oxidizes over time and it takes an aggressive flux to break thru the oxide enough to let the joint "wet". James Watts- Navarre, Florida |
Q. Thanks! The solderability was improved by alkaline cleaner. I have found the tin plating was loose by SEM! My project is to obtain tin bright plating -- matte tin is not allowed.
How to avoid the tin oxidizing?
- Beijin, China
A. Yes, I have dealt with customers who demand bright tin plating and then complain that all the 10 platers that they have used have a bad product because it will not solder after a month on the shelf. Plate with the absolute minimum amount of brightener that will work. You will also probably have to dump the bath more often than you would like. Anti oxidize-- The only one that I have heard of is a dilute solution of stearic acid ⇦ on eBay or Amazon [affil links] in Xylene ⇦ on eBay or Amazon [affil links] . Sorry, I do not remember the ratio. I originally got it from an old mil or ams specification.
James Watts- Navarre, Florida
Thanks, Mr.Watts! I will do it by your advice, and tell you the result!
- Beijing, China
Q. Hello,
I'm Malina Jaafar from Malaysia.I'm working at plating company in Research and Testing Department. We are currently having problem with tin copper (SnCu) plating over Ni-Ag part when it failed the solderability test done. We have tried different Sn bath and even changed the activation and neutralization throughout the plating process without success. Does anyone have any ideas as to the root cause of these problem?
plating company employee - Shah Alam, Selangor Darul Ehsan, MALAYSIA
2005
Q. I have an issue that after tin plating on brass with copper layer on it soldering is not happening. What can be the reason over it.
Poshendra Mahant- INDIA
September 6, 2018
A. Hi Poshendra. We appended your inquiry to one of several threads about this problem. Note Tom's suggestion that bright tin is more difficult to solder than alkaline tin, and Larry's that intermetallics may have formed in storage.
Please search the site for "solder problem tin plated brass" to get some additional understanding of the possible causes for this problem, then get back to us with the details of your situation. Thanks!
Regards,
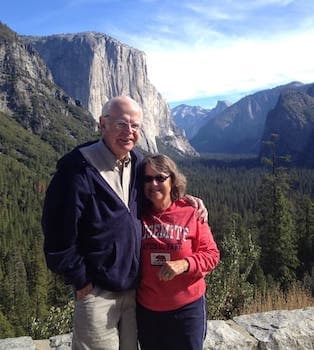
Ted Mooney, P.E. RET
Striving to live Aloha
finishing.com - Pine Beach, New Jersey
Q. Hello,
Recently I began to have problems with pieces coated with bright tin -- the main problem is that when doing the solderability test, it did not adhere properly.
We have tried to attack the problem by changing chemical solutions such as degreasers, activated (HCl), and we have even changed the tin solution to rule out contamination.
We have even changed the flux and the solder of the pot where we do the test.
Any recommendation or observation that you can give me? The same thing happens with the client when they perform the test.
I really appreciate your advice.
- Matamoros Tamaulipas, Mexico
January 3, 2022
Q. Hi Team,
We are facing a tin plating issue during soldering --
Soldering Temperature applied - 250+/- 5 °C, and Peel off issue coming on this as per attached drawing.
Part material is brass, plating is Tin plating with thickness of 5-10 micron.
- rok
July 16, 2022
Ed. note: No drawing received; please attach it to an e-mail to mooney@finishing.com.
Or see this related thread:
• Topic 48893 "Required Bright Tin Plating Thickness for Soldered Parts"
Q, A, or Comment on THIS thread -or- Start a NEW Thread