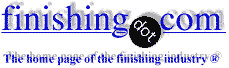
-----
Required Bright Tin Plating Thickness for Soldered Parts
Our Solder lugs are plated Bright Tin over Copper Flash. The plater normally plates to a thickness of .0001 to .0002 bright tin over .00005 Cu. My question is whether the .0001 thickness would be considered too thin for good solderability. We also have some parts that call for .0003 thickness, is this too thick? Also, I would like to know if .0002 would be the standard call out or if 200 micro inches would be the standard. Any guidance will be apprciated.
Barbara ThomasProduct Engineer - Bowling Green, Ohio, USA
May 28, 2008
May 30, 2008
Step 1, matte tin will be solderable for a lot longer than bright tin will be.
Your thickness is driven by your customer's specs.
200 micro inches is exactly the same as 0.0002 inches. Now 200 micrometers is a whole lot thicker, so watch your spellings.
- Navarre, Florida
June 4, 2008
James,
Thank you for the information. Our customers do not call out the specs. for plating thickness. We stamp or buy unplated parts that we send for plating. We are trying to come up with the best plating thickness for solderability whether matte or bright.
In recent months, we have had complaints about poor solderability and we are trying to solve this problem. The plating is RoHS compliant and we wish to stay compliant so Pb is not an option in our plating.
Barb
- Bowling Green, Ohio, USA
First of two simultaneous responses --
Barbara,
Plating thickness is not the only variable that will affect solderability. The organic content of the tin deposit (generally expressed as percent carbon) will have a very noticeable effect. Brighter tins are higher in organics than matte tins (usually). Storage of tin plated parts usually will reduce solderability due to the formation of oxides on the surface. The use of the proper flux is also important. These are just some of the factors. Sit down with your vendors and discuss this. If they are not willing to do this find new vendors. If they do not have the expertise to analyze this problem, ask them to talk to their vendors.
process supplier - Great Neck, New York
June 6, 2008
Second of two simultaneous responses --
The MIL spec used to call for 0.0005" of stannate tin for soldering. If it is to be reflowed, it is somewhat common to use a little thicker coating.
Matte is more solderble than bright tin because it has far less organic material in it that will make soldering more difficult.
You do not say what the substrate is. If it is brass, you need a thicker copper undercoat to slow down the zinc migration which forms an intermetallic that is very difficult to solder.
Your parts will stay solderable for a longer period of time if you have your plater dip the finished (and baked if required) parts in a solution of stearic acid
⇦ on
eBay or
Amazon [affil link] in Xylene
⇦ on
eBay
or
Amazon [affil link] . The formula is contained in some spec that I no longer have. Weird as it sounds, it works.
Note that tin plated parts have a shelf life for solderability. Fresh plate just works a lot better. Oxides?
We were able to rejuvinate some real old parts for a customer by a dip in a caustic cleaner, rinsed and a dip in dilute sulfuric acid,rinsed, dry and do the stearic acid
⇦ on
eBay or
Amazon [affil link] dip. We actually did a multi process investigation to see what would work and was the cheapest.
- Navarre, Florida
June 6, 2008
Q, A, or Comment on THIS thread -or- Start a NEW Thread