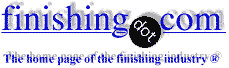
-----
Galvanizing high silicon steel

Q. Hello everyone,
I am a chemical process engineer in a hot dip galvanizing unit in Tunisia. I want to ask about the best technique to reduce consumption of zinc when we galvanize steel with Si % is between 0.2 % and 0.5 %. We will buy the steel from China and they told us that they don't face any problems when they galvanise this steel.
- Sfax Tunisia
April 10, 2023
A. Adding Ni to your Zn to about 0.06% Ni will modify the relationship between coating thickness and % Si in the steel.
There are several ways to add:
1. But pre Ni added Zinc
2. Add Ni/Zn alloy - usually about 5% Ni
3. Add Ni tablets. Ni powder in a wax with flux additives.
There are other methods that in my opinion do not work as well as these three.
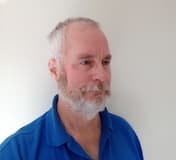
Geoff Crowley, galvanizing consultant
Crithwood Ltd.

Bathgate, Scotland, UK
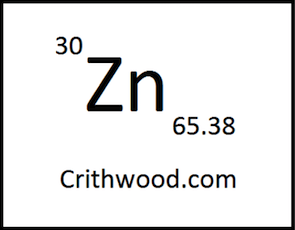
May 4, 2023
⇦ Tip: Readers want to learn from your situation;
so some readers skip abstract questions.
Q. Thank you sir for replying.
Actually, we add nickel tablets about 0,05%. What additive to flux do we need to add?
What can bismuth at 0,05 or 0,1% can help us to reduce consumption ?
- Sfax/ Tunisia
May 4, 2023
![]() |
A. Adding something to flux will depend on what you have in there already. You didn't give details of your flux. ![]() Geoff Crowley, galvanizing consultant Crithwood Ltd. ![]() Bathgate, Scotland, UK ![]() A. Dear Amin, - Hagen - Germany |
Q. We are experiencing galvanizing problems with some of our products fabricated with steel tubing with a high silicon content. The galvanizing is flaking in certain areas. The galvanizer is recommending we use a low silicon steel. The cost and availability is excessive and we would like to know if there is any pretreatment or process modification that will eliminate this problem?
Michael Prestonarchitectural metalwork
1997
by Kuklik & Kudlacek
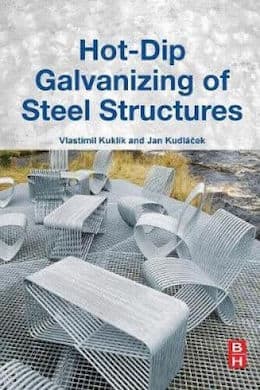
on eBay or Amazon
or AbeBooks
(affil link)
A. I am not a galvanizer, but I thought galvanize would stick to any clean metal. Chemical treatment will involve a lot of transportation and other costs. Try grit blasting a piece and see if that helps. If this material has been machined or cut, what did you use to remove the cutting fluid. Worst case, is it a silicone cutting fluid? If it is and the part got hot, nearly nothing will take it off.
James Watts- Navarre, Florida
A. We manufacture steel poles and outdoor sports lighting fixtures. We experienced the same thing you are experiencing about 1 year ago.
Our problems were either related to
a) high phosphorus content, or
b) high silicon content.
Our galvanizer first alerted us of the problem before the product had even made it out of their plant. They speculated what the problem was, but asked if they could keep a couple samples to have chemically analyzed to confirm for us. We agreed and sure enough they were right. To date, every time we've had problems with galvanizing this has been the problem.
Through a lot of headaches, we were able to work with them to define the chemical content of the steel. This information is available through the American Hot Dip Galvanizers Assoc. They can also give you information that I won't really go into (particularly since I'm no expert) to explain the effects of high silicon and/or high phosphorus. If you continue to pursue, you will likely find, as we did, that good galvanizing can be assured if the chemical content of the steel meets one of the 3 following criteria.
1)
Carbon < or = .25%
Silicon < or = .04%
Phos. < or = .02%
2)
Carbon < or = .25%
Silicon between .15% and .20% {we've had success going as high as .25% on silicon with this criteria)
Phos. < or = .02%
3)
Carbon < or = .25%
Silicon + 2.5 (PHOS) < or = .09%
The farther you can stay below the upper limits the better your success will be. Also, you'll find that equation 2 primarily pertains to ASTM A36 material. Equation 3 will allow silicon or Phos to exceed the limit in equation 1, as long as the other decreases.
Lastly, when we added these specs to our prints our vendors' first reaction was that it would be more costly material. That has never really materialized. We do require mill certification now with all steel received that will be galvanized.
Hope this helps
Jim Bernslighting manufacturer - Muscatine, Iowa
1997
A. We have very good experience with galvanizing steel with a high silicon and/or phosphorus content. Also with products in the "sandalin" range. The problem is the reactivity of the steel in the zinc melt. It is possible to decrease the reactivity by adding aluminum into the zinc melt. The aluminum content must be around 0.025 %.
Piet de Vries- Netherlands
A. Dear Sirs,
Actually I'm not an expert in galvanizing field. You are speaking about high Silicon content in the steel which causes problem in galvanizing. It is called "Sandelin Range" of Silicon. There is a kind of Zn-Ni alloys marketed by Union Miniere Group of Belgium which has local sales offices called Sogem in more than 20 countries. Contact their specialists to check what further information you can get.
Hope this would help.
Best regards,
Yutha Krainarong- Bangkok, Thailand
A. Michael,
I wanted to clarify item #3 from my message above.
I've noticed this was printed in Metal Finishing and does not coincide with the equation I was attempting to get across. In looking back on the above message, I see better clarity on my part would have helped.
Criteria #3 should have read:
Silicon + (2.5 x Phosphorous) < or = .09%
Thus if Silicon were .05% and Phosphorous were .01% the equation would be:
.05 + (2.5 x .01) = .075%
This steel would meet criteria #3, but would not meet the other 2, but would still galvanize acceptably.
Jim
Jim Berns (returning)lighting manufacturer - Muscatine, Iowa
A. It has been my experience that proper activation of the surface prior to galvanizing is the critical issue. Metallurgically speaking it is possible to have scattered areas of iron silicates that have a different etch rate. Using an acid which can attach this type of material more aggressively will eliminate the problem, such acid are: Phosphoric, Fluoboric, and hydrofluoric. Concentrations should be around 10% to 20% by volume. I hope this is helpful.
Cleanliness, Cleanliness, and CLEANLINESS is the single most critical parameter.
Bob Callihamtechnical consultant - Newton, North Carolina
A. My experience with high silicon or phosphorous steel has been that some customers can only afford the less expensive steel with the afore mentioned contents. Our solution: quick immersion and withdrawal from the kettle. It is unfortunate however that the content is nearly impossible to detect. Pass this info to your galvanizer and see if it helps.
BJ
Bradley Jones- Cincinnati, Ohio
A. I am a galvanizer for the past 18 years and we run into this silicon problem occasionally. We have added nickel to our kettle and that helps dramatically. I have also heard that you can lower the zinc bath temperature and that will help the silicon problem.
Robert Olsen1999
A. Steels containing high amounts of silicon can be galvanized satisfactory by controlling the temperature of the galvanizing bath to a temperature of approximately 820 °F. This slows down the alloying process and reduces the thickness of the coating. Additions of nickel to the galvanizing bath can assist in the galvanizing of silicon steels. The amount of nickel must be controlled to prevent the onset of higher amounts of dross and/or skims to the galvanizer which will affect the cost structure. Galvanizing of steels in nickel-containing kettles will reduce the alloying process and generally will result in coatings that are not blotchy.
Robert C. Martingalvanizing shop - Baltimore, Maryland
2001
Q. Dear sir
I am with a consultant firm in Canada, part of my job is investigating about standard procedures on hot dip galvanizing companies in Middle East who are using Dry Hot Dip Galvanizing methods. We have noted a that large number of Galvanizers are not using drying chambers or oven, but for drying the steel components after fluxing and they were dipped directly into the melting zinc kettle. That, in our opinion may cause discoloration and may affect the quality... Unfortunately no hard documentation or analysis in our hands to prove that ...
What makes the matter more complicated is that an Ireland furnace manufacturer had written to some of those galvanizers to assure them that no galvanizer in Ireland is using drying chamber to dry the prefluxed component prior to dipping in the kettle.
Could you please send me some of the information regarding such matter, and advice if there is no harm of utilizing this method and under what conditions?
Thank you for your efforts
Frank Shaheen- Toronto, Ontario, Canada
1999
A. Good drying is a very important part of the galvanizing business.
Oliver Herwig- Hagen, GERMANY
2000
"Galvanize adhesion on high silicon steel problem"
Q. How do you avoid poor adhesion of hot dip galvanize on high silicon steel.
Charles Logue- Dubai U.A.E.
2006
A. Sir:
In galvanizing silicon killed steel (phosphorus also causes problems), it is important to have short kettle times and low kettle temperature. Reactive steels attain about 1 mil (25.4 microns) for each minute they are in the molten zinc. Coatings greater than 6 mils are subject to impact and flaking off. Thus kettle times longer than
6 minutes should be avoided. Often the flux solution is the problem. It can be contaminated with sodium chloride or potassium chloride, iron salts, sulphate, have too low of an ammonium chloride/zinc chloride ratio (I "coined" this "ACN"; meaning ammonium chloride number in my articles in the journal
METAL FINISHING; some of which are available on the internet.) These "poor" fluxes are not volatile enough and result in long "cook out" times. The flakes in this case are brittle and thick.
Regards,
Galvanizing Consultant - Hot Springs, South Dakota, USA
Q. Sir,
From last few months we are facing adherence failure in hot dip galvanizing coated sheet. We have checked everything like dew point, combustible (we are using Natural gas as an fuel), leakages ... but found satisfactory. The adherence failure is random and occurs at our line's top surface in centre. What could be the probable cause of this can any tell me ?
- New Delhi, Delhi, India
August 6, 2012
Q, A, or Comment on THIS thread -or- Start a NEW Thread