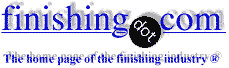
-----
Hydrogen embrittlement in cadmium plating
Q. Does anybody have any experience of correcting notched tensile test pieces failures used to prove hydrogen embrittlement in a cad solution? The test is 200 hrs @ 75% of the UTS.
Greg Yates- Manchester, England
2001
EVALUATION OF CADMIUM PLATING SYSTEMS FOR HYDROGEN EMBRITTLEMENT by Theodore G Ozan (1962)
A. Two things that help:
1. Etch the absolute minimum that you can live with. Abrasive blast if necessary to hold it down. Etch is by far the largest cause of failures in cad plating.
2. Get into the bake oven as soon as possible after plate. To me, that is a maximum of 30 minutes.
James Watts- Navarre, Florida
A. Pre-treat by blasting only. Cadmium solution is to be free of all organics - carbon filter all the time. If your solution has had brightener put in it you will never pass. De-embrittle at 190 °C for 24 hours.
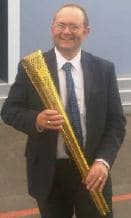
Martin Trigg-Hogarth
surface treatment shop - Stroud, Glos, England
A. I respectfully disagree. Blast and plate, minimum time to bake, bake for 4 hours and ZERO failures, with cyanide cad and acid cad.
James Watts- Navarre, Florida
? Please can you tell the tensile strength of the steel that you are plating as I am talking of process for cadmium plating of steels in excess of 1450 MPA (210 KSI or 94 ton per inch). I would not treat these for four hours.
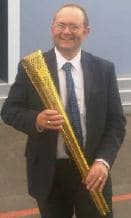
Martin Trigg-Hogarth
surface treatment shop - Stroud, Glos, England
A. Martin,
I do not remember the exact KSI, but the notch bars were 4340 treated to max hardness with a 400 °F draw temp.
It seems to me that it was a lot higher than 210K, but I do not remember.
To clarify my last response. Time from plate to oven was under 15 minutes. Bake was 375 °F for 4 hours.
Process was abrasive blast, about 1 min in a medium alkaline soak, 10 seconds in a 25% HCl and plate as required.
Notch bars were run with parts and did not receive any special treatment.
Mil Spec certified testing company did the bars.
James Watts- Navarre, Florida
Thanks for getting back to me. What I say is you live and learn. I would of thought that four hours was too short a time going by the standards that we work to, but the fact that the test bars pass shows that the method works.
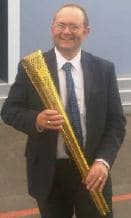
Martin Trigg-Hogarth
surface treatment shop - Stroud, Glos, England
A. A longer bake can be helpful if your parts do not have generous radius or are ground after hardening. The main "secret" is getting them into the oven as soon as possible which limits the depth that the hydrogen can penetrate to.
James Watts- Navarre, Florida
Q. Hi!
I work in the spring industry that frequently requires plating in marine environments. We have several applications where we need a suitable finish (Cadmium) for marine environments with carbon steels but run the risk of hydrogen embrittlement. Are you familiar with materials that can be plated with CAD without running this risk? I am looking into Hard Drawn material over OT and chrome alloys. Any thoughts on circumventing this issue or selecting a proper material?
- Los Angeles, California, USA
March 22, 2013
A. Hi Tim. First things first. Cadmium is a biocumulative toxin that we all all working to remove from the environment. We never plate with cadmium if we are seeking only one of its properties, like corrosion resistance, because it's possible to simply plate a heavier layer of something else. We use it only if we need the unique combination of properties offered by cadmium including malleability, compatibility with aluminum, freedom from gummy corrosion products, etc. Please carefully consider whether a substitute like tin-zinc or hot dip galvanizing might suffice.
All spring steels are hard and, as far as I know, subject to hydrogen embrittlement. We appended your inquiry to a thread which explains the protocol for hydrogen embrittlement relief. Good luck.
Regards,
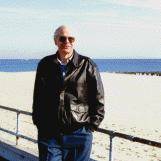
Ted Mooney, P.E.
Striving to live Aloha
(Ted is available for instant or longterm help)
finishing.com - Pine Beach, New Jersey
A. Hi Tim,
To add a bit more to Ted's answer de-embrittlement requirements are usually determined based on either the hardness or the Ultimate Tensile Strength (UTS) of the steel.
In the UK we tend to work on the basis that any steel will require de-embrittlement if its UTS is greater than 1100 MPa (160,000 psi). In the USA it tend to be done on hardness. I have seen varying requirements from 36 HRC to 40 HRC considered the lowest hardness, dependent on the customer.
SAE / AMS2759 is a good reference source.
Aerospace - Yeovil, Somerset, UK
Q. Is there a way to stop hydrogen embrittlement (ASTM F519) in a pH 9 cleaning solution (surfactant blend) containing nitrite and silicate as inhibitors? Substrate is Cd plated steel.
Rob CrouchSurfactant Manufacture - Phoenix, Arizona USA
June 19, 2017
! Hi Rob. I guess I'm not fully understanding the proposition, but why would immersion in a pH 9 surfactant solution be expected to either cause or cure hydrogen embrittlement?
Regards,
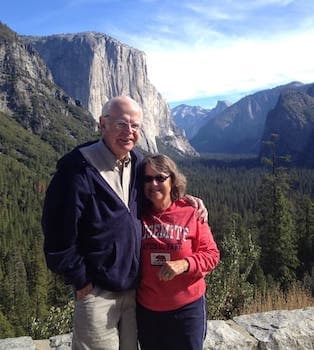
Ted Mooney, P.E. RET
Striving to live Aloha
(Ted is available for instant or longterm help)
finishing.com - Pine Beach, New Jersey
Q. Post Cadmium Plating Tarnish from Baking
Hello, we have a small cadmium tank, 30 gallons. After the plating process we have been baking our parts for 8 hours. There is a tarnish effect on our product after baking.
Is there a solution or process to prevent the parts from discoloring?
We are looking to clear chromate our product, but it has been suggested we do this post baking. We would like to treat our parts to stop the discoloration.
Thank You
- Bend Oregon
February 28, 2023
A. Hi John. I assume the parts are hardened steel and therefore you have to bake them at a spec'd temperature for a spec'd time for hydrogen embrittlement relief?
I think excessive brightener might make the problem worse, so look for that ... but can you bake them in a nitrogen or other inert atmosphere, or are they small enough to put into stainless steel heat treatment bags? Thread 37180, "De-rusting/De-scaling of Heat Treated Parts" includes more detail on such topics.
Luck & Regards,
Ted Mooney, P.E. RET
Striving to live Aloha
(Ted is available for instant or longterm help)
finishing.com - Pine Beach, New Jersey
A. It's expected that some discoloration will occur during the baking process. I have clients who will immerse the baked parts back into the cadmium tank for a short dip to remove the tarnish, then rinse and chromate the parts. Chromating prior to bake will not give you good results since the bake will damage the chromate. You can also make up a post bake cyanide dip if you don't feel comfortable using the cadmium tank.
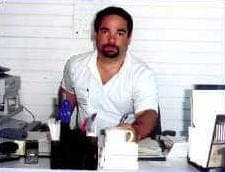
Jim Conner
Mabank, Texas USA
Q. We have 304L Stainless steel, the requirement is to CADMIUM process Type IIA, CLass 2.
After the completion of this , is there a need to embrittlement relief.
I have the understanding that 304L is austenitic steel, and these don't need to go thru embrittlement, is that a true statement?
Please help?
Supplier Quality - Orange County- California
April 11, 2023
A. Hi Victor. I am not a metallurgist so I can't really say whether hydrogen embrittlement relief will be necessary ... all I can do is warn that Sandia Labs says it's not automatically unnecessary :-)
Hopefully you realize that when plating onto stainless steel a Wood's Nickel Strike or equivalent will probably be necessary before cadmium plating.
Luck & Regards,
Ted Mooney, P.E. RET
Striving to live Aloha
(Ted is available for instant or longterm help)
finishing.com - Pine Beach, New Jersey
A. Hello Victor
Typically, austenitic stainless steel does not require Hydrogen Embrittlement relief bake. However, as Ted said, it is not 100% situation. I would recommend to check AMS2759/9 for Hydrogen embrittlement requirements - what material and for how long it has to be heat treated.
Please note, that some Cadmium plating specifications may have even more tough baking requirements than actually listed in AMS2759/9.
Good luck,
- Winnipeg, CANADA
April 17, 2023

Q, A, or Comment on THIS thread -or- Start a NEW Thread