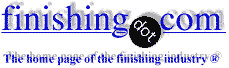
-----
Brush Plating Nickel
I've been reading the responses to Ms. White's question in letter 1298 in this forum and nobody seems to be giving her a straight answer. What is the big secret about nickel plating? For about a week now, I have been trying to get information about brush plating nickel .008" to .010" thick on the rear surfaces of the locking lugs on a rifle bolt. I've gotten conflicting information about how to do it myself with my brush plating kit.
I can't find information on books on the subject at the local library web site, I can't get straight information about what books to study, I can't get straight information about vocational/correspondence schools that teach brush plating and I can't even find a professional plater who can do the job for me! One plater doesn't even know what brush plating is!
Again I ask, what is the big secret?, and, is there anyone out there who can give us some simple, straight answers to our questions, that my simple intellect can understand, to be able achieve my purpose?
Thanks much.
- Bethlehem, Pennsylvania, U.S.A.
2001
Electrochemical Metallizing by Marv Rubinstein
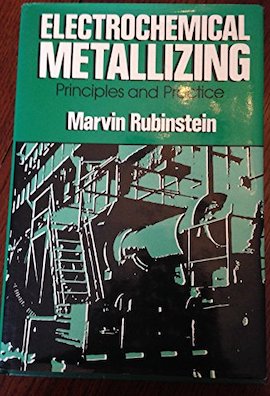
on eBay or Amazon
or AbeBooks
(affil link)
A. Hi Norman.
Regarding the books you asked about: There is a terrific one, "Electrochemical Metallizing" ⇨
which is solely about brush plating. For others, please see our Books page.
Regarding the correspondence schools you asked about: Kushner Electroplating School runs an introductory plating course, as does AESF. For a course specifically on brush plating, please try contacting the suppliers of brush plating systems. They can also refer you to brush plating shops if that's your preference. For more plating shops, please see the Directory of Jobshops.
There are no secrets, but when readers spend decades fully learning their trade, they do have a problem condensing everything you need to know into a few paragraphs. My first hint is that plating doesn't start with plating, it starts with a spotlessly clean and chemically active surface. Plating isn't painting, it's a process where metal grows on metal, and a quick guideline is that most plating problems are the result of a surface that is not truly clean. After you think it's already as clean as can be, scrub it with a tampico brush and a water solution of powdered pumice while wearing rubber gloves. If the surface isn't "waterbreak-free" it's not clean enough for plating.
Luck & Regards,
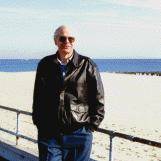
Ted Mooney, P.E.
Striving to live Aloha
(Ted can offer longterm or instant help)
finishing.com - Pine Beach, New Jersey
A. Hi Norm,
Most professionals are gun shy about about helping out hobby platers because there frequently is zero indication of what level of experience they have. Re-read Ms White's original letter. She gave zero information in her request about what she had tried or even what she was doing. ALSO, notice that she did not share her newfound information with anyone else but complained in the follow up letter about others that did not share.
Brush plating is very simple, but is extremely operator sensitive, like possibly 10 times what tank plater operators are.
The best answer is to follow the instructions of the vendor that you bought the kit and chemicals from.
When I was plating, I would not work on guns because of the liability. There are lots of things that can go wrong. 0.008" is a lot to try to put on a lug and have it stay on forever. Consider having it professionally done.
Good luck with your efforts. Try it on a dummy part before you try it on the gun.
- Navarre, Florida
Q. Dear Jim Watts;
Thank you for your response to my "tirade". Please understand that I have become quite exasperated over what I'm trying to accomplish. If I can do it myself, fine, but I keep getting conflicting information about this. If I can't do it myself, okay, then I'll send it to a professional plater. Thusly, for the last two weeks or so I've been trying to find a professional plater that can and will do the job at a reasonable cost. (For "$250.00 minimum" I can buy a new rifle!) I am an Engineering Designer and so I know something about what a small brush plating job such as this would entail. How much trouble can it be to plate a total surface area of 1/8 of a square inch with nickel, chrome or other reasonably hard material .007" to .008" thick?
Some people just seem to insist on making simple things complicated. Could it be that this is so they can charge "through the nose"? Liability?, I would play hell trying to prove that a plater, who added a thickness of plating per my specifications, was the cause of my rifle blowing-up.
Again, thank you for your response. I'm back to the "find a plater" wars.
- Bethlehem, Pennsylvania
2001
A. Whoever you bought the "brush plating kit" should be able to provide you the sequence of chemicals and power to use.
Problems: the metal actually absorbs a minute amount of oil that is very difficult to get out. Any trace of oil will reduce the adhesion of an already difficult job. I would soak it in a hot alkaline cleaner for about an hour and then rinse well.
You will need to have an appropriate mask for the "not to be plated area", this is typically tape. If this "spot" is elevated, you will need to build up layers of tape to get the surrounding area very nearly level with the spot to be plated. Now you need an area of conductive foil to act as a thief or robber or bleeder so that you do not have an extremely high current density area on the sharp edges. Typically, this is metal tape with the end bent over and taped to the parent metal so that it is conductive. Aluminum does not live thru the cleaning step very well, so think about copper or lead.
The real secret to brush plating is the setup. For critical jobs, you really need a separate handle and brush for each solution and for the + or- direction of the current if it is used both directions. A very rapid changeover is required.
Keeping the part wet at all times is 100% mandatory, even if it is only water.
Use a good strike to where you see solid color. Not too much though, as this is terribly internally stressed.
Always start your brush stroke -- off of the part and sweep on/off. Your brush will probably be much larger than your part so you can stay on for a long time if you have a flow thru system. If you have a dip system, I really doubt if you will succeed. One method that can help is to use a lab wash bottle (squeeze squirt bottle) and try to keep the pad wet from above.
You probably will want a hard nickel, but typical max would be around 0.005" on an easy part. There are some "high build" nickels on the market that are hard. Sulfamate will be too soft but builds much better. There are some hardened sulfamates.
I have trained people in brush plating, including some very difficult ID parts, and I would only give myself a 30% chance of pulling your part off on the first try.
It is doable, but it is one big challenge.
Pre-bake your part after the alkaline soak for 4 hours at 375 to 400 °F. Bake it after plate also.
- Navarre, Florida
A. Hi, Norman. That 'baking' instruction has to do with this: Hydrogen embrittlement relief is a crucial element of plating hardened steel. If it isn't done both before and after plating, the plating absolutely can cause a rifle to blow up! While you wouldn't be expected to know that, every plating shop should -- so I don't think you'd "have to play hell" to show their liability over something they should know but you wouldn't be expected to know.
Sorry for your troubles, but the main reason for your exasperation may be that plating isn't quite as straightforward as we'd all like.
Best of luck.
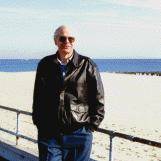
Ted Mooney, P.E.
Striving to live Aloha
(Ted can offer longterm or instant help)
finishing.com - Pine Beach, New Jersey
A. YOU CAN BUILD THE THICKNESS UP WITH AN ACID COPPER SOLUTION at 8 VOLTS THEN NICKEL PLATE ON TOP WITH THE NICKEL FOR HARDNESS EASY HONEST ...
David Park- Cornwall, England
January 20, 2008
Thanks, David. That sounds like good advice!
Regards,
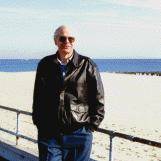
Ted Mooney, P.E.
Striving to live Aloha
(Ted can offer longterm or instant help)
finishing.com - Pine Beach, New Jersey
Multiple threads merged: please forgive chronology errors and repetition 🙂
Nickel Brush Plate Edge Thickness
Q. Hello Everyone,
I have gotten a 4340 steel RC 42-46 part brush nickel plated by professional contractors, to a max. thickness of 0.005 in., but have experienced several chipping incidents. Many of the failures start at a chamfer, measuring 0.08 in. x 45 degrees. I think that if I change the chamfer to a radius, that it may solve the chipping problem. However, I cannot find minimum edge radius specifications anywhere. Does such a specification exist? Is there a minimum radius around which brush nickel plating should be applied ?
Any suggestions would be greatly appreciated.
Thank you,
- Lakehurst, New Jersey
2001
A. The MFSA's Quality Metal Finishing Guide recommends a radius of at least 1/64" and preferably 1/32" for decorative copper-nickel-chrome plating; but it doesn't address brush plating. But I don't think the nickel should chip or peel regardless.
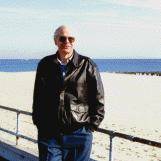
Ted Mooney, P.E.
Striving to live Aloha
(Ted can offer longterm or instant help)
finishing.com - Pine Beach, New Jersey
Just wanted to say thanks to Ted Mooney for the quick response.
Thank you,
- Lakehurst, New Jersey, USA
A. Hello Mark,
Ted mooney is correct. There should be no chipping or peeling from the edge of a brush plated deposit. There are procedures that will enable brush plated deposits to be built well over .005" with no chipping on an edge.
- Valencia, California, USA
RFQ Looking for nickel Brush Plating Services in the New England area for approx. 100 pieces of carbon steel castings. Looking for approx. .002 buildup in a .875 keyway.
Ron B [surname deleted for privacy by Editor]Gear MFG - New Hartford, Connecticut, USA
2004
Ed. note: This RFQ is outdated, but technical replies are welcome, and readers are encouraged to post their own RFQs. But no public commercial suggestions please ( huh? why?).
Multiple threads merged: please forgive chronology errors and repetition 🙂
I have been reading this forum and particularly this topic for a while now, and I am also exasperated with the silly comments...e.g., you can't do it right on the first go, you need to read a lot of books, build a library etc. All these comments may be true and helpful in some way, but it does nothing for instant gratification, which is why people post, they've exhausted other methods and come here, which is exactly what I have done. I have to sift through multiple unhelpful comments to get to 1 or two posts with snippets of useful comments. Surely the idea of this is to help rather than 'off-put' people?
We all know that a there is a certain amount of 'experimenting' and failure with plating when we start and most of us don't want to do it in a professional capacity, so why all the sermons I wonder. Just a 'good basis to start' comment, or 'try mixing this much with that' is far more helpful.
So please, there are those that want to help and it shows, so good on them, but let's have less of the silly pedantic, unhelpful comments, yes, you are in a position of knowledge and power, get off your high horse and provide some useful comments.
- Swindon UK
February 10, 2008
A. James Watts and David Park offered excellent practical advice to Norman, and I suggested the books, training courses, and plating shops that he asked for.
A beginner, Norman, first time out, asked how to do nickel plating that is 3 times as thick as most experienced professionals will even attempt; Mr. Watts spent a great deal of time with him on two occasions both explaining this and offering specific answers -- but Norman still seemed to insist that Mr. Watts was wrong, that plating of that thickness shouldn't be difficult, and that people were only claiming it was so they could "charge through the nose". Considering the circumstances, it was not pedantic to make it clear that -- sorry -- plating 3X thicker than professionals can do is hard.
I've spent 40 years in plating and still learn a lot every day, and am not ashamed that I can't quickly tell a beginner how to do a plating job that most professionals won't attempt. But besides my advice on proper cleaning, the second piece of advice I'd offer is that you have to practice on scrap, and not once or twice but 10, 20, 50 times if necessary, until you get the hang of it.
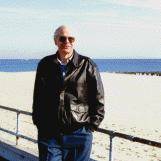
Ted Mooney, P.E.
Striving to live Aloha
(Ted can offer longterm or instant help)
finishing.com - Pine Beach, New Jersey
!! DON'T PLATE THE LUGS ON YOUR RIFLE, THIS WILL BLOW YOUR HEAD SPACE AND MAKE YOUR GUN INTO A GRENADE! IF YOU PLATE THE LUGS YOU MAY NOT BE ABLE TO COMPLETELY CLOSE YOUR BOLT WHICH WILL OBDURATE THE CASE HEAD SUPPORT AND POSSIBLY RIP THE LUGS OFF BOLT, SENDING THE BOLT CRASHING INTO YOUR FACE. AND IT DOESN'T TAKE A SCIENTIST TO KNOW YOUR FACE IS SOFTER THEN THE METAL THAT WILL BE FLYING AT YOU. GOOD LUCK WITH THAT THOUGH.
Tom Peacock- Denver, Colorado, USA
February 7, 2008
A. There is a good article in (AMERICAN GUNSMITH) NOV. 1992, titled "Electroplating Small Parts".
Brush-plating small parts is easier than you think. It just takes practice and a little patience.
Hurchell Holmes- North Plains Oregon USA
February 20, 2012
Multiple threads merged: please forgive chronology errors and repetition 🙂
Q. Hello all! I'm a C.I. Manager with an aviation components company and we are trying to fill in some gaps on an old process, nickel brush plating, and the company that provided our initial documentation and training (Brushtronics) has since gone out of business.
We are trying to determine the following items:
1. Why do you pull versus cut the cotton when wrapping the anode?
2. What is the impact to the plating process if the red leads are plugged into the black sockets and vice-versa?
3. Is there an industry leader in or near Michigan that could visit and provide training or advice on the process?
Any help would be appreciated.
Thank you in advance!
aviation component manufacturer - Grand Rapids, Michigan, USA
September 24, 2008
A. Hi, Robert. If you are now lacking any documentation maybe you could try to find a copy of Rubinstein's "Electrochemical Metallizing", which is the bible for brush plating.
Regards,
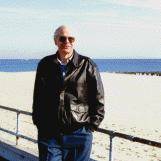
Ted Mooney, P.E.
Striving to live Aloha
(Ted can offer longterm or instant help)
finishing.com - Pine Beach, New Jersey
A. Ted's advise is the way to go, but in the mean time I will try to answer your questions.
1- You are supposed to use long fiber cotton and pull it to wrap it tight around the anode. If you cut it in short pieces, it tends to loose and move or un-wrap during processing (anode sleeves are not enough to keep it tight)
2- The color of the cables is theoretically irrelevant. As long as you connect the brush to the positive terminal on the power pack and the part to the negative for plating (FORWARD). Of course, etching and some cleaning steps on some metals require REVERSE polarity. Then the brush is negative and the part positive. If you make a mistake you may ruin the part. For instance if you use forward polarity when cleaning a high strength steel you may induce hydrogen embrittlement in the part. If you use reverse with an acid solution you may dissolve metal from its surface instead of plating it or building it up.
3- The best vendors advertise here. Just take a look.
Monterrey, NL, Mexico
A. Hello,
I am Bob Brookshire's last stepson and a former employee of Brushtronics Engineering.
From my memory Guillermo Marrufo's answers #1 and #2 are correct.
Found this thread through a random Google search. Hope Guillermo's answers are helpful.
JW
- Laurel, Maryland, USA
December 30, 2008
Great to hear from you, Jesse!
Luck & Regards,
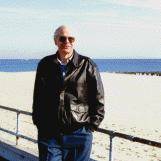
Ted Mooney, P.E.
Striving to live Aloha
(Ted can offer longterm or instant help)
finishing.com - Pine Beach, New Jersey
Nickel brush plating a copper sink in place
Q. I am looking for advise on a reasonably efficient process/chemical combination to brush plate a solid copper sink, first in nickel, then I know how to do the gold. I am fairly new to brush plating but have been getting good results with gold repairs and touch-ups. Looking for some guidance for this next project. Thanks for your time, Michael
Michael GoldbergYacht carpenter and finishing expert adding brush plating services to my company - Fort Lauderdale, Florida, USA
April 14, 2012
![]() |
A. It's going to be a very time consuming job, and will require someone with lots of expertise. It will be much more difficult than touching up small spots with gold. ![]() Jeffrey Holmes, CEF Spartanburg, South Carolina A. You will need a dense acid nickel to improve adhesion, avoid porosity and migration of gold into copper. For decorative applications, a nicely polished copper, a thorough clean with a paste of very fine pumice dissolved in non-greasy soap or a detergent with abrasive particles will suffice as a pre-clean and activation step. Half a mil thick of nickel and then the gold. Caution should be taken to avoid draining haz chemicals to the sewer. Monterrey, NL, Mexico |
Thank you both for the input, it is helpful. I have also been told by a local plater that I can get a fairly good result by polishing the copper to a high shine and going direct with the gold. I was told that it may get a little rose colored over time but, will have a very good bond between the two metals. Any additional feedback would be appreciated.
Thanks, Michael
- Fort Lauderdale, florida, USA
April 20, 2012
A. Hi Michael. I think you've heard right. The nickel serves two purposes: brightness, and preventing diffusion between copper and gold. So if you're not nickel plating, you do need to get the copper quite bright and reflective before doing the gold plating.
Luck & Regards,
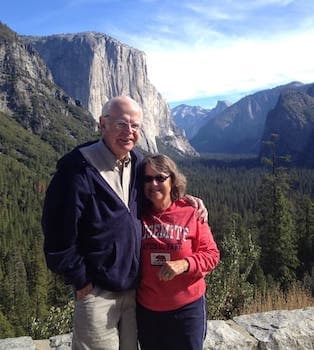
Ted Mooney, P.E. RET
Striving to live Aloha
(Ted can offer longterm or instant help)
finishing.com - Pine Beach, New Jersey

Q, A, or Comment on THIS thread -or- Start a NEW Thread