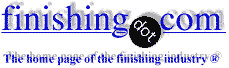
-----
Questions on Molybdenum disulfide (MoS2) & tungsten disulfide (WS2) dri-film coating process
Molybdenum disulfide applied on 17-4PH?
Q. My application is 17-4PH (H900) aircraft cargo handling structure. Chemical analysis identified the coating as Molybdenum Disulfide .0005" Thickness. One of the mating parts is 17-4PH casting per AMS5344 cad plated per QQ-P-416, TY II, CL 3 & bake. Per MIL-L-24478C Prohibitions and precautions section 6.1.1.1 states that Molybdenum disulfide shall not be applied on 300 series or type 17-4 stainless steel component surfaces. For this method of application, what is the reasoning for prohibiting these materials? Does heat cured application per MIL-PRF-46010 eliminate the issue? Any recommendations? Thank you.
Donny Searight- Greenville, SC
May 10, 2024
⇩ Related postings, oldest first ⇩
Q. Hello folks,
I work as a tool and die maker for a small company that manufactures extruded vinyl products that primarily are used in commercial refrigeration. I was wondering if it would be possible to use a coating of molybdenum disulfide on my extrusion dies to prolong the run times to help make production more efficient. If it is possible this product is suitable for the food grade industry?
Any comments would be appreciated.
Thanks and best regards,
James Mahuronextrusions - Salem, Indiana
2001
A. Dear James,
In regard to your question on possible coating of MoS2 for improving the dies function, I can say "YES". However much more result will come out with the Tungsten Disulfide powder, which will be sprayed on the die surface at room temperature. This coating does not require curing or any binder for the adhesion on the substrate. The powder will form molecular bonding on the surface. It withstands up to 535 °C.
You will find smoother flow of plastic powder with reduced process temperature, better releasing without release agent and prolonged die life.
Wishing your success,
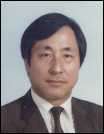
Jason Yu
- Seoul, Korea
A. DEAR SIR,
I HAVE DEALT WITH ALL KINDS OF DRY FILM LUBRICANTS FOR 36 YEARS IN AUTOMOTIVE APPLICATION.
IN ENGINES THE MOLY PLATING IS REPLACED BY MOLY IN THE OIL, BUT AS A DRY FILM TYPE LUBRICANT I SUGGEST DOW CORNING SPRAY = MOLY+GRAPHITE. NOW THEY HAVE A MOLY WITH ANOTHER SOLID FILM LUBRICANT THAT IS AN EXTREME PRESSURE LUBRICANT WITH LOWER FRICTION THAN MOLY BY ITSELF. IT'S CALLED GN-PASTE ⇨
DENNIS ALAN LEAVITT, TRIBOLOGIST = LUBRICANT ENGINEER- DRAPER, UTAH, USA
2003
Lubricant specifications Question
Q. Is Dry Film Lubricant per MIL-L-46010/MIL-PRF-46010 [from DLA] , Type I, the same as SAE AS5272, Type I.
If so, then do parts that are coated with MIL-L-46010, Type I automatically meet AS5272, Type I?
Did the latter supersede the former?
Thanks,
Rich Davis- Newport News, Virginia
2002
Need molybdenum disulfide surface treatment on steel
Q. WE ARE OEM COMPANY. IN SOME OF OUR PARTS OF SOME EQUIPMENT IN THE DRAWING IT IS GIVEN THE ITEM TO BE MOLYBDENUM SULPHATE TREATMENT ON THE SURFACE. CAN YOU PLEASE CLARIFY WHAT PROCESS IT IS AND HOW IT IS DONE AND WHAT IS THE USE OF SUCH COATING?
Dey SK- India
2003
A. My guess is that it is MoS2, which is Molybdenum Di Sulfide and not sulphate which is MoSO4. The MoS2 is a very common primary material in "dry film lubrication". It typically is black or dark grey as applied and does not have the drawbacks of graphite. There are lots of formulations. Some are air dried and some are baked on. Some call for a phosphate undercoat (normally zinc phosphate). It is available from several major manufacturers. In the USA, most of us would use one from the military QPL (qualified products list), since nearly everyone will accept a proper product from that list.There are a few tiny companies and some fly by night repackagers, but you are running a significant risk for a few pennies savings. My personal opinion.
James Watts- Navarre, Florida
Q. I want to apply WS2 coating in some parts due to its properties, but I don't know what processes (cold spray, CVD, PVD or MOCVD) can be used, and how strong adhesion of the coating to the substrate?
Thanks very much.
University of Waterloo - Waterloo, Ontario, Canada
2005
Multiple threads merged: please forgive chronology errors and repetition 🙂
Solid lubricant application to reduce wear in a plate sliding over a set of plates supporting it
Q. Hi there.
I would like to expand my problem like this:
I am trying to reduce frictional wear of a set of plates and the arrangement of plates is such that there are five beams placed parallel to each other over beams, i.e., on the upper surface of each beam there is a plate i.e. sheet of metal (mild steel) been welded and this is called wear plate [length 13 m, width .175 m]
These 5 plates carry a load of around 50 tons as another plate of same length and a width equal to the distance between the wear plates at the extremes of this arrangement. this plate is 15 ton heavy and loaded with a material of load equal to 40 tons. Everything is fine except that this loaded plate is pulled on the wear plates back and forth by motors and the loaded plate slides over the wear plate arrangement and this causes a lot of frictional wear and loss of life of loaded plate as well as the wear plates, of course grease is used.
What I would like to do is to coat the wear plates with a solid lubricant layer and eliminate the friction to improve the life of my equipment. But I am finding problem in collecting information about suitable choices of solid and dry lubricants (the cost and their load carrying capacity and other properties).
Can you, please, help?
engineering trainee - Jhunsi, Allahabad, Uttar Pradesh
2005
A. The most common dry lubricants are either graphite or molybdenum disulfide. You can also use PTFE or Polyphenylene sulfide, but with the loadings you use, I don't think any lubricant will last indefinitely. If the plates are continuously moving, then grease would be an ideal option, but if they are allowed to stop, you have the added problem of inertia. You may also consider using different types of metal on the mating surfaces. A high chromium surface on one face may prove beneficial.
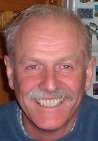
Trevor Crichton
R&D practical scientist
Chesham, Bucks, UK
Q. I have been buying machine screws from a company located in New Jersey. The screw is coated with black Phosphate which serves as a lubricant. However, the lubrication is not good enough when my technicians assembled parts using it. The company proposed to switch to dry film lubricant finish that meets the requirement of Mil-Pre-46010 and AS5272. I have done some readings about lubricant and it seems like Moly DiSulfide (MoS2) is a good one. Unfortunately the company cannot answer my question about their dry film coating whether it is MoS2 or something else. The engineer just directed me to read the mil spec. Can anyone help?
Henry Leung- Bloomington, Minnesota
2006
RFQ: In regard to "Tungsten Disulfide powder which will be sprayed on the die surface at room temperature. This coating does not require curing or any binder for the adhesion on the substrate . . ."
I would like to know more about the product and availability to purchase
Regards
S.Guna
- Shah Alam, Selangor, Malaysia
November 2, 2009
Ed. note: This RFQ is outdated, but technical replies are welcome, and readers are encouraged to post their own RFQs. But no public commercial suggestions please ( huh? why?).
Need both solid film lubrication and corrosion resistance
RFQ: We are presently utilizing Zinc plating on some Auto components. The spec. required is 200 hours to white rust and 400 hours to red rust with 10 to 20 microns thickness. We could achieve the spec., but the component does not meet the requirement of noise level with plating.
Now customer proposes MoS2 based coating with phosphate as base coat to reduce the co efficient of friction and also to achieve the corrosion resistance.
Kindly suggest suitable MoS2 product. Can we achieve 400 hours red rust with single coat or is a primer required?
Regards,
engineer - Chennai, India
February 7, 2010
Ed. note: This RFQ is outdated, but technical replies are welcome, and readers are encouraged to post their own RFQs. But no public commercial suggestions please ( huh? why?).
A. Dear Murugan Srinivasan,
Normally MoS2 Coatings will come Black in colour because the nature of MoS2 is Black in colour.
Maybe better you try with PTFE or Xylan coating with MoS2 Base. It will give 400 Hours salt spray of 10-20 Microns.
- Salem, Tamil Nadu, India
Corrosion resistant alternatives to molybdenum disulfide [Australia]
Q. Hi, all.
I'm currently employed as an engineer and have been given the task of minimizing corrosion on the equipment that we manufacture. At the moment, we coat many steel components with molybdenum disulfide (ranging from fasteners like nuts and bolts to 50 kg+ mild steel fabrications). This lasts longer than zinc coating and black oxiding, but from what I have read, MoS2 is principally used for dry-lubrication properties, rather than corrosion resistance, so there could potentially be a treatment that is more applicable to us, as we only care about corrosion resistance. Being a fresh (clueless? :D) graduate, I don't have much of an idea of what potential solutions there are out there, (perhaps a zinc oxide conversion coating would outlast the MoS2?)
The environment that most of the components are in is "standard factory conditions," if there is such a thing. In some areas, the parts are exposed to extreme heat (600-700 °C or 1100 to 1300 degrees Fahrenheit)... the MoS2 doesn't cope particularly well with this anyway, so while it would be nice, high operating temperature is not absolutely necessary
In short, I'm looking for a coating that is more corrosion resistant than molybdenum disulfide, but less expensive than nickel coating. Can anyone help me?
Engineer - Dandenong, Victoria, Australia
July 21, 2010
![]() |
A. Dear Jared Tyler, - Salem, Tamil Nadu, India A. There is a massive range of products formulated to give a mixture of low friction and corrosion resistance. For an indication of the possibilities you may want to look at Bostik's Never Seez* range. Aerospace - South Wales, United Kingdom |
Dry Film Lubricant vs. Solid Film Lubricant
Q. What is the difference between Dry Film Lubricant and Solid Film Lubricant?
Chris LowEngineer - North Tonowanda, New York
October 7, 2010
A. These are just two different terms for the same thing. Lubrication is by means of a solid phase (PTFE, MoS2, etc.) rather than a liquid (mineral oil, animal fat, etc.).
Toby PadfieldAutomotive module & component supplier - Michigan, USA
Prepping zinc-nickel plating for dry-film lube coating
Q. Another question.
Is it possible to apply solid film lubricant to zinc-nickel plating? I.e., does it offer adhesion to organic coatings?
Regards,
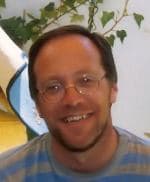
Arnold Langeveld
- Papendrecht, The Netherlands
March 31, 2011
A. Sure, you can apply a dry film such as moly disulfide in an epoxy carrier to almost anything.
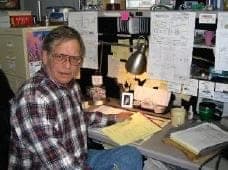
Jeffrey Holmes, CEF
Spartanburg, South Carolina
Q. How do I prep nickel plating for dry film lube?
Timothy Kaszak- Baltimore, Maryland, USA
December 18, 2013
Applying Tungsten Disulfide to Hardened Steel Parts
Q. How to coat or procedure for applying WS2 over hardened steel parts?
We are posting this question because in a textile machine application ... we need to reduce friction between metal to metal sliding application. In this we can't apply any oil or grease. Need dry lubricant. Came to know WS2 has very low friction in a dynamic application. But we need to know how to apply WS2 coating on a steel part.
machine works - Coimbatore, Tamilnadu, India
June 5, 2014
A. The best method is by sputtering. There aren't many companies that offer the service, though.
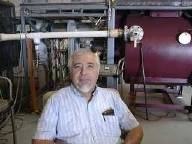
Jim Treglio - scwineryreview.com
PVD Consultant & Wine Lover
San Diego, California
Q. Hello folks,
I have a problem with friction.
I must form a steel sheet by a 40 mm ball, which is from a ball bearing, and measure the forming force, etc. -- but friction interferes with my measurements.
Can I reduce to it to less than 0.05? Since the contact pressure is very high, about 200MPa, does MoS2 work well in this condition or there are better options?
How can I coat the ball with a solid lubricant, like MoS2?
Thank you for your response!
I am eagerly waiting to hear from you!
E
University - pretoria, GA, South Africa
August 25, 2014
A. MoS2 can handle the load -- in fact, it does better under high loads. Various methods for applying it. Best is sputtering, but there are other methods as well. May need coating to be doped if you need to use it in a high humidity application. Works well with most petroleum-based liquid lubricants.
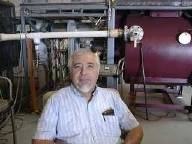
Jim Treglio - scwineryreview.com
PVD Consultant & Wine Lover
San Diego, California
Q. Thank you Jim.
Actually, I am going to coat a stainless steel ball, took out from a ball bearing so its surface is very fine, to make an indentation on a pipe. The process is similar to sheet deep drawing. Which process do you suggest to coat the ball or perhaps the pipe. First I wanted to use just Teflon sheet between the ball and the pipe to reduce friction, then I tried to coat the Teflon and the ball with MOS2. I compressed the MOS2 on the Teflon sheet, but when I look at the coating under the microscope, I noticed it is not uniform, so it may increase the friction in comparison with the teflon itself. What is your suggestion?
Regards
University - pretoria, GA, South Africa
September 9, 2014
A. I would skip the Teflon step and sputter deposit MoS2 or WS2 on the ball, depending on what is available. Keep the coating thickness under one micron. Any other process will give you an uneven coating.
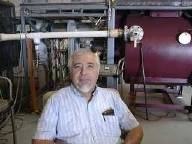
Jim Treglio - scwineryreview.com
PVD Consultant & Wine Lover
San Diego, California
Can WS2 Dri-film adhere to Silicone?
Q. Is it possible to bind WS2 to porous surfaces like silicone? I have a component of a quasi-medical device that needs to contact both clothing and skin, and currently use a thin, vacuum formed sheet of LDPE to reduce friction, but it's not lubricious enough. I'm looking for alternatives in the form of a direct coating or a coating on a sleeve that still allows the spongy, conformant properties of my component to shine through.
I'd appreciate any thoughts.
Thanks.
- New York, New York USA
May 23, 2019
RFQ: Need the nearest Finisher to Somerset Kentucky that does Moly Coat.
Anthony Viggiano- Groton Connecticut
November 24, 2021
Ed. note: This RFQ is outdated, but technical replies are welcome, and readers are encouraged to post their own RFQs. But no public commercial suggestions please ( huh? why?).
Q, A, or Comment on THIS thread -or- Start a NEW Thread