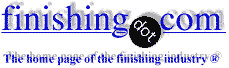
-----
DI water with stainless steel 304 and 316
Current question and answers:
Q. RO water causing rust in 316SS spray nozzles.
We are using 316 stainless steel spray nozzles in a cleansing kiosk for eyewear and jewelry. The system uses deionized water which is essential for the cleansing. Why are the 316 stainless steel nozzles rusting?
- San Gabriel, California
March 20, 2021
A. Hi David. Ultrapure DI water, such as is used in semiconductor manufacturing, is very hungry to dissolve ions into it and corrosion of 316 SS is not unheard of, as you'll read below.
It seems unlikely that you need or are using ultrapure water though, and RO water should probably not corrode 316 stainless steel. I would suggest double checking that they are in fact 316SS, then removing them and having them passivated. Do not let them contact plain steel tools when re-installing.
Luck & Regards,
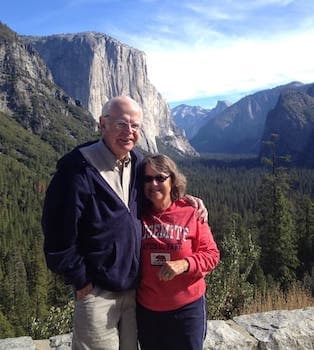
Ted Mooney, P.E. RET
Striving to live Aloha
finishing.com - Pine Beach, New Jersey
March 2021
Q. My previous inquiry was answered. I need to add more information. The water system I referred to cycles RO water and it is subjected to UV irradiation each cycle. Should this then be considered ultrapure water?
David DeMoss- San Gabriel, California
March 21, 2021
A. Hi again. I am not a DI water expert, but my understanding is that "ultrapure" actually suffers from having two meanings: its theoretical meaning of freedom from every single ion except for H+ and OH-, resulting in a resistivity of 18.18MΩ-cm; at 25 °C. ... and a practical meaning of very very pure water appropriate to the application. Thread 14693, "Factors affecting the Quality of Ultra Pure DI water", might be interesting to you.
I did not fully digest "Ultrapure Water -- The Standard for Resistivity Measurements of Ultrapure Water" by Anthony C. Bevilacqua nor pretend to fully understand it all, but in his Table 4 he offers this shocking (to me at least) relationship:
Also, a "Myths" paper at thermofisher.com notes that exposure to normal CO2 in the air will quickly reduce the resistivity from 18.18MΩ-cm; at 25 °C. to about 1MΩ-cm.
Wikipedia offers some analytical values for allowable contaminant levels in ultrapure water for the semi-conductor industry, and that stainless is no longer used there. It also references some standards for the pharmaceutical industry and notes that stainless is still widely used there.
My understanding is that UV can reduce TOC and keep biological growth at bay.
I don't understand your systems' exact needs or operation. But I'd say if it's somehow sealed away from the ambient air so that carbon dioxide cannot enter the system, maybe you do need PVDF coating or nozzles; but if not, then it surprises me that you are finding 316SS insufficient such that my first reply still sounds applicable.
Luck & Regards,
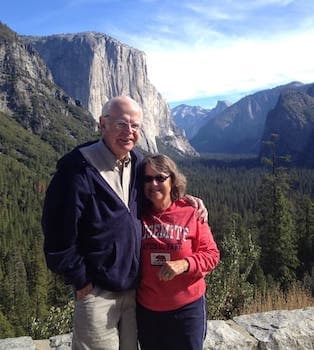
Ted Mooney, P.E. RET
Striving to live Aloha
finishing.com - Pine Beach, New Jersey
Q. Sorry to be a pest. Please review www.opticwash.com to view the product I have mentioned. Rust on the 316 stainless nozzles continues to be a problem. I am certain the nozzles have not been passivated but I would like to be reasonably sure the passivation would effectively address the issue. I am hopeful the nozzle supplier (a German company) can provide passivation. Short of that is there a periodic cleaning regimen of the nozzles that might suffice in terms of removing the rust? Thank you so much for your comments and input.
Dave DeMoss
- San Gabriel, California
March 21, 2021
A. Hi again. (Actually, we like questions that continue and which generate feedback; it's short abstract questions that can be tiring).
This doesn't look to me like an ultrapure water scenario where I would expect 316SS to rust. The nozzles can probably be cleaned, the rust removed, and passivated perhaps in place, but certainly at least on site, with a citric acid formulation. I would suggest that you contact Stellar Solutions [a finishing.com supporting advertiser] who specialize in that.
Luck & Regards,
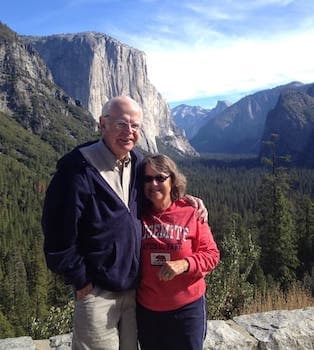
Ted Mooney, P.E. RET
Striving to live Aloha
finishing.com - Pine Beach, New Jersey
March 2021
Q. I have a problem with 316SS corroding or rusting over time. We are running DI water with a ppm of 0 through these fittings and in less than a year they are rusting. I was under the impression that 316SS will not rust.
Bryan Myers- Ocala, Florida
March 25, 2021
A. Hi Bryan. The issue is that for general DI or RO water, passivated 316SS should work, but for 'hungry' ultrapure DI water it won't. Please have a lab test and verify that the material is 316SS, then make sure it is properly passivated and does not contact carbon steel during installation. If it then still rusts you'll have to upgrade to plastic coating or solid plastic.
Luck & Regards,
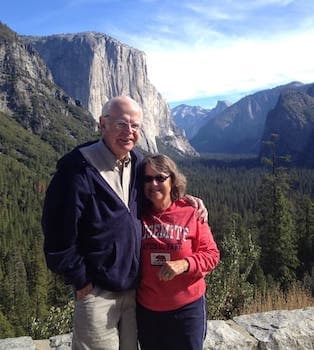
Ted Mooney, P.E. RET
Striving to live Aloha
finishing.com - Pine Beach, New Jersey
March 2021
⇩ Related postings, oldest first ⇩
Q. I have industrial pumps made of 17-4 SS and 316 SS that are filled with DI Water and Glycol (50/50) which are rusting during the shipment process to the end user. These pumps are filled with the 50/50 mix and then sealed to prevent air in leakage.From what I can gather, SS needs to be exposed to oxygen in order to generate the protective oxide layer that prevents corrosion? DOES SHIPPING THESE IN THE WATER/GLYCOL MIX ACTUALLY CAUSE THE CORROSION?Any help as to how to prevent this corrosion?Thanks,
Johnna Calveraseaerospace - Anaheim, California, United States
2001
![]() |
A. Johnna:The question is, were the pumps passivated prior to packaging and shipping? If there was no post manufacturing treatment of the surface to remove the free iron and aid the development of the oxide layer, then naturally you expose your product corrosion. ![]() Joel Levinsohn - Sydney, Australia 2001 2001 A. The DI water is a relatively aggressive environment that could corrode the 17-4PH in a relatively short time of exposure. I would not expect 316 SS to have a problem with this environment in the absence of contamination or other contributing factors. I have two basic suggestions:1) Make sure that the components are clean and passivated before filling with the water/glycol mix ![]() Larry Hanke Minneapolis, Minnesota |
A. Johnna:You are correct in that you need to have a chromium oxide layer on the surface of the ss to prevent corrosion. This happens naturally in the air. However, in order to give the optimum in corrosion resistance, you should maximize the chromium content on the surface by passivation of the surface. This can be done in a number of ways, but it is fairly easy with 17-4 and 316SS. See ASTM A967.There is a lot of additional information necessary to determine the cause of your rusting, and the best solution. Which glycol are you using? A medium of DI water/glycol could set up a current between the 17-4 & 316SS in the tank, also. Is it impossible to use all 316 or 316/304?Passivation before use will give you the best results in this situation, but it may not be enough if you have a battery set up in the container.
adv.
We would be happy to discuss it further with you.Regards,
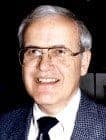

Lee Kremer
Stellar Solutions, Inc.

McHenry, Illinois
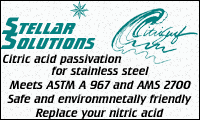
2001
Multiple threads merged: please forgive chronology errors and repetition 🙂
Dispensing Deionized Water
Q. My work involves dispensing DNA on glass slides. As part of our process we perform several manual rinse steps with DI water. The DNA dispensed is basically looking for it's partner to complete it. We can not introduce any contaminates that can bind with the DNA, especially bacteria. I would like to inexpensively automate the process. We found out the hard way that stainless steel will rust, rust contaminates the DNA. I am concerned about contaminates that could occur with deionized corrosion. I need to know specifically what materials are corroded by DI water, so I can get an idea of what material to use for the mechanical parts that will spray the DI water. The part would process DI water 24 hours 7 days a week.
Miranda Goffbio science - Mesa, Arizona
2003
A. What you should really be looking at is what grade of DI water you need. This will then help determine the materials used. Very pure DI water will dissolve eventually anything. I have found that the best material to use is teflon coated 316L stainless steel. (sometimes the 304 rusts)
Mike Wellsplating stuff - Jamestown, New York
2003
A. Teflon would be a good material to look at for any parts teflon is available in. There are many different Stainless steel alloys. Carpenter 20 is very corrosion resistant. Do you know which alloy you have tried. The more common 304 is a little less corrosion resistant.Thanks,
Tim HoneWater Treatment - Farmington Hills, Michigan, USA
2003
A. You may want to use PFA 0r PVDF tubing and fittings if the application is really critical, but for most applications, polyethylene or polypropylene are adequate. In order to assure that the water is bacteria-free, however, there should be final filter with a pore size of .05 or .02 microns.
Lyle Kirmanconsultant - Cleveland Heights, Ohio
2003
Multiple threads merged: please forgive chronology errors and repetition 🙂
Q. I am an equipment provider. My customer is asking me to give a solution which is using DI water. My current system is designed based on stainless steel 304. Cleanliness is crucial in this process. I wonder whether should I change my material from 304 to 316 in order to have better resistance.
Ken Loh- Flexlink, Malaysia
2005
A. You will always get better corrosion resistance with 316 than with 304, so if you need the best use 316L or better. DI water CAN give you problems with 304, but it is usually okay depending on the process.
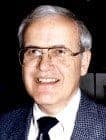

Lee Kremer
Stellar Solutions, Inc.

McHenry, Illinois
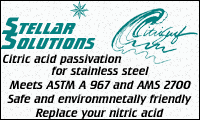
2005
2005
A. DI water penetrates stainless steel over time. This is especially true at elevated temperature.
I have the data for demineralized water and distilled water at boiling water 2 & 20 mil/yr respectively.
If you passivate the surface it will help.
As such, the rate of penetration is expected to be more or far more than 2 mil/yr.
Q. I like to know the rate of penetration for DI water near boiling point though.
Al Badakhshan- Los Angeles, California, USA
Multiple threads merged: please forgive chronology errors and repetition 🙂
Will Stainless Steel change Deionized water?
Q. Sir My name is Muhammad Noman-UR-Rehman and I am a bio Medical Engineer. I want to know if deionized water passes from a small area of Stainless Steel passage then can it alter the properties of the DI water or not? I mean to say can it change its pH or its conductivity?
Muhammad Noman-Ur-Rehmanbio medical Engineer - Pakistan
2007
![]() |
A. It is all relative! - Navarre, Florida 2007 2007 A. With long exposure to DI water there may be some corrosion, particularly if it is a lower grade of stainless steel. But, if the water is moving, it will happen much too slowly to make any measurable difference. consultant - Cleveland Heights, Ohio |
Multiple threads merged: please forgive chronology errors and repetition 🙂
Corrosion in DI Water Piping
May 13, 2009Q. There is corrosion in the demineralized water pipe (pipe material = stainless steel) frequently.
I have two questions:
1-How much is the corrosion effects of the pH of the demineralized water on the stainless steel pipe.
2- How can I increase the pH of the ddemineralizedemin water to 8.5-9.5.
Specification of the demineralized water:
pH 6.5
temperature 25 °C
total Fe = 0.5 ppm
I have added phosphate (Na3P4) but it was not useful.
buyer - Isfahan, Iran
![]() |
A. Really pure DI will attack stainless pipe, even 316L SS. - Navarre, Florida May 19, 2009 May 20, 2009 A. Can't help with your question 1; but with question 2 realise that if you add anything to the DI water it is no longer DI. ![]() Bill Reynolds [deceased] consultant metallurgist - Ballarat, Victoria, Australia We sadly relate the news that Bill passed away on Jan. 29, 2010. |
![]() |
May 22, 2009 A. Hi Mehdi, ![]() Freeman Newton [deceased] (It is our sad duty to advise that Freeman passed away April 21, 2012. R.I.P. old friend). May 22, 2009 A. May I suggest you eliminate the corrosion problem by using polypropylene, PVC or ABS pipework. ![]() Trevor Crichton R&D practical scientist Chesham, Bucks, UK |
June 4, 2012
⇦ Tip: Readers want to learn from your situation;
so some readers skip abstract questions.
Q. What is the best pipe material for Demineralized water, and grade if found; and best TDS in ppm?
0 ppm
2 ppm
4 ppm
If we need to coat the pipe, please advice with what material.
What is the effect of ultra filtration units before cooling tower systems?
international desalination and water treatment - Cairo, Egypt
Q, A, or Comment on THIS thread -or- Start a NEW Thread