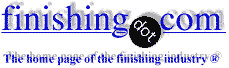
-----
Optimum Nickel Sulfamate Strike Parameters
2001
Q. Seeking information on Optimum Parameters for a Nickel Sulfamate Strike Bath. We are a medium sized plating house doing Nickel Sulfamate Flash Plating prior to nickel brazing for a variety of Nickel and Nickel Cobalt aerospace alloys (controlling specification AMS2403 / AMS2424). We very recently switched to use of a Nickel Sulfamate Strike from a Wood's Nickel Strike in the interest of reducing the number of rinse tanks needed in a newly installed processing line. We have very little experience with this new chemistry and would like advice on optimum process parameters.
Our strike bath make-up is;
4 oz./gal. Boric Acid
1.54 fl. oz./gal HCl
2.7 oz./gal Sulfamic Acid
We currently maintain our bath at;
10-12 oz. wt./gal Ni
4 oz./gal minimum Boric
0.4-1.0 fl. oz./gal Chloride (as Cl)
pH 1.5 Maximum
This is done through regular chemical analysis and add recommendations by our lab.
The bath is equipped with Nickel S-Rounds in Titanium baskets (changed over from rolled depolarized in old Wood's strike) with double anode bags. The bath is currently maintained 24/7 at 125 degrees F. in order to allow evaporative feedback of downstream rinse (following Nickel Sulfamate Plating tanks)and to prevent the crystallization and fallout of the Boric Acid. All water to line is DI @ 3 microsiemens or better quality. Rinse waters are filtered through 10 micron particulate and activated carbon filters before being introduced back to strike (or plate) tanks for level make-up. We do a continuous particulate filtration and activated carbon filtration on the bath through an recirculation pump and canister filter. We also continuously electrolytically dummy the tank in a deep overflow weir (side tank) with low current density dummy cathodes.
We have not experienced problems yet with this bath but have heard that it is a more sensitive and less forgiving strike than the Woods Nickel Strike. I am interested in feedback and advice on the particular sensitivities and best practices to assure that we operate trouble free.
B. Pettegrow- North Berwick, Maine, USA
A. There are as many opinions as there are platers on this subject. You did not mention pH. This is probably the critical element for the strike because as the pH rises, you will become closer to a conventional sulfamate tank and your plate rate goes up rapidly and your adhesion goes down.
It seemed to me that the old Allied Kehlite spec for the strike called for a higher amount of chloride.
It is a very functional strike for many purposes, but for my two cents, it is inadequate when you try to plate on very high nickel or cobalt SS such as waspalloy or incolloy and is iffy on 718.
Other than your reason, its main advantage is the higher pH and the faster plate rate than the Woods Strike.
James Watts- Navarre, Florida
2001
Q. Our pH is maintained at 1.5 MAX by specification. Our specification calls for pH adjustment with Sulfamic Acid. Currently the pH is running 1.5 to 1.6. A conservative add of 0.2 oz. wt/gal of sulfamic acid did not appreciable impact the pH. Could someone with experience with this bath offer insights in the best practice for pH adjustment and maintenance?
We have had some feedback that small HCl adjustments can be very effective but chloride level needs to be closely watched to stay in the required range.
Thanks for your assistance.
Brent Pettegrow [returning]- North Berwick, Maine, USA
2001
A. That is the pH range that I thought that it was. By comparison, a Woods Nickel strike is around a pH of zero. Remember, pH is a logarithmic measurement. It takes ten times as much sulfamic to change a ph from 3.1 to 3.0 as it takes to change the sulfamate bath from 4.1 to 4.0.
Then it is going to take 10 times that amount of acid to change it from 3.0 to 2.0 and about 6 times that much to change it from 2.0 to 1.5 A very crude estimate is 160 times as much to change it from 1.6 to 1.5 as it takes to change the main bath (same volume) from 4.1 to 4.0.
The nice part about it, if it is not "eating" your substrate, it will stay at 1.5 for a long time. Make your chloride adjustments with HCl when you can stand the pH adjustment. Kills two birds with one stone. You certainly will not need any more nickel unless you had a spill or horrible dragout. Strikes are terribly inefficient at the cathode, so plan on making periodic "bleeds".
You should not be using S rounds at this chloride and pH. They will slowly dissolve just setting in the tank, and you have more than enough corrosion capability to use rolled depolarized stick anodes. S rounds also ends up putting a lot of sulfur in solution causing it to stink and blisters or lack of adhesion start showing up. Carbon treatment really helps, but it does not completely cure this problem.
James Watts- Navarre, Florida
2001
A. I agree with James Watts. There is no need for S-Rounds in a bath with this chloride content. Chloride ions are required in a plating bath to promote corrosion of regular nickel anode material. Chloride also increases the plating stress, an important consideration in many applications. sulfur depolarized nickel (like S-Rounds) dissolve in baths with no chlorides. Electroformers using low chloride sulphamate baths to control the plating stress use sulfur nickel. In a bath with plenty of chloride, regular nickel squares or R-Rounds should dissolve just fine.
Don Piett- Thompson, Manitoba, Canada
2001
adv.
"The Sulfamate Nickel How-To Guide"
by David Crotty, PhD
& Robert Probert
published Oct. 2018
$89 plus shipping
Q, A, or Comment on THIS thread -or- Start a NEW Thread