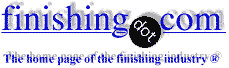
-----
Does chromate coating strength degrade above 200 °F?
Greetings,
Synopsis: Appears that chromate conversion coating detaches at about 200 to 250 °F allowing bonded metal arcs to fall off shaft.
Application: A 1î diameter steel shaft is zinc plated and then chromate conversion coated. The chromate coating is intended to enhance the adhesion of a compliant epoxy that binds metal arcs to the shaft.
What happens to the chromate coating's structural integrity, its strength, as it heats to and soaks at 200 to 250 °F?
How can I determine if the chromate is attached to the shaft or to the metal arcs? Is a visual inspection for the gold tone of the chromate, or its absence sufficient?
Related finishing.com correspondence, refer to letter #4710
M. Robert Mock- Santa Clarita, California
2000
200 to 250 degrees F is not very hot. If the chromate was probably cured (not heated above 140 degrees F for the first 24 hours), I'm surprised that you are having any difficulty with it.
However, I did not know that chromate was used to increase the adhesion of epoxy to zinc, and am quite surprised to hear of it.
I think you are on the right track regarding observing where the gold tone remains as a clue to where the adhesive failure is.
If someone has a reference to the use of chromates to increase the adhesion of epoxy I would like to learn more.
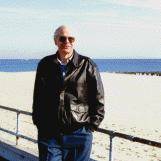
Ted Mooney, P.E.
Striving to live Aloha
(Ted can offer longterm or instant help)
finishing.com - Pine Beach, New Jersey
2000
Hexavalent chrome conversion coatings do degrade around 220F. It is hard to put an exact temperature limit on chromate since the degradation is a gradual process. The chromate film is a hydrate that contain water molecules. These water molecules are necessary for the chromate conversion coating to function normally. Once the film is exposed to higher temps (around 220F), the conversion coating begins losing the water molecules and essentially "burns off."
With no additional coating, the part will see the beginnings of white corrosion much sooner than expected. The part will also lose a good amount of resistance to red rust. The conversion coating protects the plating, while the plating protects the base metal. High temperature effectively eliminates the first defense against corrosion. I imagine the chemical structure of the chromate film would also be affected by high temperature dehydration.
There may or may not be a significant color change with heating. I think there would be, but it may not be distinguishable enough to use it as an inspection criteria. You may want to take a few parts and heat them for four hours at 250 or 300 F, let them cool, and then compare color.
Good luck!
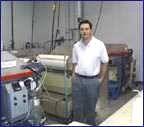
Tim Neveau
Rochester Hills, Michigan
2000
2000
M Robert Mock
I believe that you are not powder coating but here is an idea to look at from my experience with powder coating which may help or can be trash.
When applying Epoxy Powder Coat I have had a lot of problems with epoxy type power coating depending on the chemistry (also with some Hybrids) that the chromate failed, when zinc undercoating was required by spec. we just didn't chromate the parts and eliminated the problem with very good results.
Just a note that I have found that it is not so much the temperature of the chromate (as long as the chromate was cured correctly) but more the reaction between the chromate and the powder coating
Chris Snyderplater - Charlotte, North Carolina
Q, A, or Comment on THIS thread -or- Start a NEW Thread