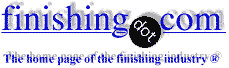
-----
Electroplating onto glass
Quickstart:
This thread discusses electroplating onto glass, with copper, gold, or electroless nickel. Silver is generally deposited onto glass by chemical means rather than electroplating, so readers who are interested in depositing silver onto glass may prefer to start with thread 415.
Copper Plating on Glass
Q. We've been copper plating large pieces of blown glass for sale at different galleries in the U.S. We are using a sandblast resist tape that originally was made by 3M to sandblast gravestones to cut a pattern onto the glass pieces. Then we are sandblasting the cut-away areas through the tape to create the pattern that we are then painting with a conductive silver paint.
t this point we are pulling off the tape and then putting the painted piece into the copper plating tank with beautiful results. Smooth or textured depending on the amount of electricity applied. Great process! The problem is we are unable to make the plating adhere to a smooth flat surface of the plates and platters with the above process. It will adhere to a piece when the pattern goes all around the piece, we believe actually shrinking a bit grabbing the piece holding tightly, but on flat surface or just halfway around a piece, it is just pealing off.
We are going to fire a luster glaze onto the surface (design pattern) ideally a copper luster (cheaper) or a silver luster , hoping that it will adhere more to the glass and then hopefully the plating will adhere better, allowing us to plate flat or partially round surfaces. Does anyone have any suggestions that would help us? Any and all advice will be greatly appreciated. thank you
1995
A. Dear Mr Anderson, firstly allow me to apologise for taking so long to respond to your question. Hawking International, a Sustaining Member of the Institute of Metal Finishing replies:
If you apply "Liquid Bright Gold" to the glass and fire the glass at a temperature just below its softening point, a conductive film that exhibits good adhesion will develop. It should be possible to plate onto the gold film providing adequate connections can be made. Hawking International, The Stenders, Mitcheldean, would be willing to supply samples if requested.
IMF - Birmingham, U.K.
Q. I've been a glass blower for over 30 years and I have a small circular glass sculpture 11" in dia. that I would like to electroplate with copper. I would like to create a crusted, beaded organic type surface around the edges of the glass sculpture.
I'm wondering what kind of processes I'll need to go through to achieve this effect.
1. Will I need to sandblast the areas where I want the copper to adhere?
2. What chemical do I coat the surface of the glass with?
3. What will I need as far as electrical equipment goes?
a. what kind of transformer?
b. What type of electrodes or anodes?
4. Should I use plastic as a container for the chemical bath to electroplate?
5. What kind of chemical solution do I put the glass into, and does it have to be total submerged?
6. What size copper shavings will I need?
Thank you for your time.
- Tucson, Arizona USA
2006
by N. Kanani
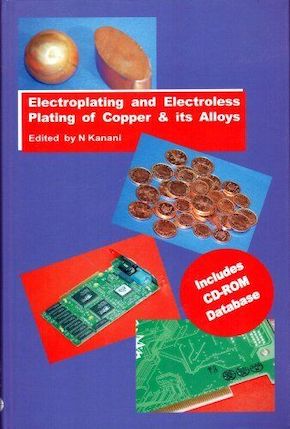
on eBay or Amazon
or AbeBooks
(affil link)
A. You would first of all need to apply autocatalytic electroless copper as your structure will be non-conducting. This would involve immersing the structure in a catalyst solution containing palladium and tin ions, e.g. palladium chloride, tin chloride, and then dipping it into electroless copper solution, e.g. Shipley 3350 solution. This process does not require any electrodes and the copper ions will be displaced out of the solution by the presence of the catalyst on the structure. This process will build up a copper layer of up to about 5 microns in thickness. Generally the rougher the surface the better the adhesion of the copper would be. To build the copper layer up thicker you would then have to apply electroplating to the structure.
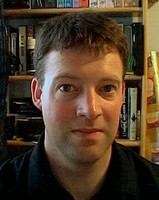
Dr. Gary Callon
University of Dundee
Arbroath, Scotland
A. The electroless method might be best if you are doing large quantities but another idea to consider is silvering the glass and then plating using acid copper. The acid copper process is probably going to be cheaper and easier to operate than the electroless one.
In order to plate the glass this way you must first make it conductive with a conductive paint or you can silver the glass using the Brashear process.
You can find vendors for the acid copper bath and ingredients for the Brashear process using your favorite search engine.
I have copper plated glass and plastic tubing with this method. The adhesion is limited on smooth glass but the copper will hold nicely if the shape permits. Since your object is circular, the copper layer should hold itself on nicely.
- Huntington Beach, California
RFQ: I have a similar requirement for plating on glass (though a different shape) and need to know where to get sensitizer, activator, and plating solutions. A Japanese report I saw suggests a methanol [affil links] rinse after sensitizing and activating to promote adhesion. I plan to try that, once I get set up.
Phil Ekstrom- Shaw Island, Washington, USA
June 2, 2009
Ed. note: This RFQ is outdated, but technical replies are welcome, and readers are encouraged to post their own RFQs. But no public commercial suggestions please ( huh? why?).
Q. Hello,
I am a PhD student doing research for school. I was given a task by my advisor to plate a glass cylinder with silver for use in a laser system. It needs to be a certain thickness for the EM wave to be trapped inside, essentially. We chose silver for it's high conductivity yielding a low thickness. This was several months ago.
After talking with a few people, I was told of a silver plating solution that would electroform above a certain temperature. To check this, I was able to electroform onto solid copper. I plated a few glass slides using vacuum evaporation with copper, silver, and even gold. The later two would dissolve off the slide as I placed them in the solution. The copper had better results, but it too would dissolve in places making it unusable. I now realize that this might be an adhesion problem, and that etching the glass in a HF solution might be a good idea.
But, instead, I was wondering if electroforming with copper might be a better idea. The conductivities of the two are close so the thickness would be as well. It also seems that dealing with the copper solution would be much easier. So, my questions are as follows:
1) Should I bother with trying to etch the glass in either case (silver or copper)?
2) Electroforming with copper, should I precoat the glass copper? (i.e. would it be harder to plate copper on copper rather than some other conductor?)
3) What solutions would you recommend? I am not going for shiny, just thick (about 10 microns)
Thanks for any advice and wisdom that you can offer!
Student - Chicago, Ilinois
November 18, 2011
A. For Glass you will need a layer of Chromium or Titanium as first layer, these can be sputtered with excellent adhesion on Glass. After that you should sputter a layer of a metal which is easy to activate for electroplating, copper should do fine. Maybe you need to sputter several layers with a cleaning procedure in between to avoid pinholes.
Good luck
- Zug Switzerland
A. I recommend that you contact a mirror manufacturing chemical supplier. They sell the necessary pre-treatment supplies and also copper and silver plating process chemicals for deposition onto glass.
Lyle Kirmanconsultant - Cleveland Heights, Ohio
A. Electroforming on a glass mandrel is quite commonplace. You first of all need to make sure the glass is as clean as possible by using conventional wet cleaning systems. Then you spray the glass using a twin headed spray gun - one jet sprays ammoniacal silver nitrate solution and the other sprays a reducer, such as dilute formaldehyde and glucose. The two jet sprays should combine about 6-10 cms from the glass surface; you will initially get a dark deposit, but this brightens up as the thickness increases. Keep the spray gun moving at all times. Do not overspray it or the deposit can become powdery. I would suggest spraying for about 30-45 seconds, but this will depend on the geometry and capacity of your system. Once coated, wash the glass and leave it for 24 hours to harden off.
Be careful - silver salts and ammonia
⇦ on
eBay or
Amazon [affil links] solution can form a contact explosive, so make sure everything is thoroughly washed after use.
You can then electrodeposit metal onto the silvered glass, but you will probably need to ramp up the current. Make sure you have plenty of electrical contacts to the silver and start with a low current density. The precise current will depend on the metal being deposited. Once you have a reasonable deposit thickness (say 2-3 microns) you can start to increase the current to a more conventional current density. The trick to it is to take your time and be gentle!
Further information on this technology can be found in any technical article concerning the manufacture and production of vinyl records (if you remember them!) or CD's.
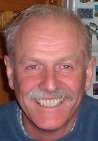
Trevor Crichton
R&D practical scientist
Chesham, Bucks, UK
Q. I had a question regarding the electroplating process. I'm trying to electroplate a backing of copper to start on a piece of stalactite ... It's been a very difficult and frustrating process. I'm not sure how to even begin. I've researched as much as I could via the internet and I'm running full force into a brick wall.
Stalactite is a glassy surface. I've roughed it with sanding grit to make the back more porous and painted a thin layer of copper conductive paint to it ... Let it cure and it chipped away. My second method included backing the stalactite crystal with an epoxy/resin and ... Fail. Lol
I've mixed the copper paint with the epoxy ... Same no luck. My hope is to plate a thin layer of metal to the back of the crystal and continue to add thickness and eventually electroplating to silver/ gold.
Any help would be phenomenal thank you in advance.
Springfield, Illinois
September 20, 2015
A. Your best bet is to electroless plate this glass-like article with either copper or nickel, it would be best electroless nickel followed by bright copper plating then silver/gold. There are some recipes for nickel and copper on google search. There are a few companies selling the electroless nickel in the USA.
How electroless copper or nickel on glass-like surface? You must sensitize and then activate the surface. The sensitizing is done using stannous chloride, the activation is done by a colloid of precious metal chloride (Silver/gold/rhodium/Palladium/Platinum) the most preferred one is Palladium, like 0.1g per liter. Silver can be used instead to save on costs.
This is my plan for 3D printed plastic parts(ABS)
Acetone vapor treatment to smooth the part, bright electroless copper plating, immersion Silver plating (Silver plating creams) immersion gold plating (electroless but not Autocatalytic, )
- Managua, Nicaragua.
A. CuSO4 [copper sulfate] + C6H8O6 [ascorbic acid] -> Cu + C6H6O6 [Dehydroascorbic acid] + H2SO4 [sulfuric acid].
An aqueous solution of copper sulfate plated the surface of my beaker with the addition of ascorbic acid. The solution was clear.
I'm not sure if this requires a base pretreatment or acid pretreatment to functionalize the glass surface for adhesion.
Hobbyist - McAllen, Texas
March 8, 2025
Tip: This forum was established to build camaraderie among enthusiasts through sharing tips, opinions, pics & personality.
The curator & some readers who publicly share their info will be less likely to engage with those who don't.
Electroplating onto glass like iPhone screens
Q. HI,
I tried coating a glass surface in my lab using sputter coater but the problem is it gets off even by the touch of a finger.So I would like to know if there are any more ways to coat a glass hard with gold and also a few confirmation tests which can prove the strength of the gold coated on to the glass surface
- Cleveland, Ohio, US
February 16, 2011

Q. Here is a link to what I am talking about:
How are they able to electroplate the reverse side or inside of the glass, or any help on how this can be done. I been looking into it and searching the forum and internet but haven't found anything useful.
Krunal PatelChalfont, Pennsylvania
March 28, 2017
Ed. note: That eBay page no longer exists.
A. Hi Krunal. Although it is possible to electroplate glass, and although they call it "chrome electroplating", I doubt that it actually is, because of the low cost and the available colors. I think it's PVD "vacuum metallizing", similar to what would be applied to a shiny mylar party balloon.
Regards,
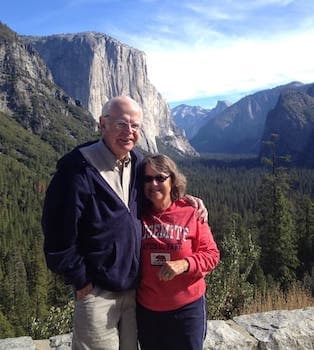
Ted Mooney, P.E. RET
Striving to live Aloha
finishing.com - Pine Beach, New Jersey
Gold plating on glass
Q. I am looking for gold plating on sealed hollow glass tube. plating should be done on half of circumference of the tube and should be visible from other end. plating thickness should be mini. 10 microns. pl. help
Nandkumar Barhate- Pune, India, Maharashtra
2000
by Reid & Goldie
-- hard to find & expensive; if you see a copy cheap, act fast!
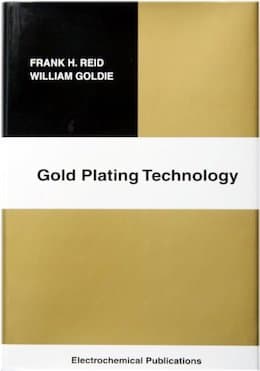
on eBay or Amazon
or AbeBooks
(affil link)
A. If the purpose of the gold film is to reflect light through the tube, I may have a better solution for you. We sell a gold film that already has an adhesive that will apply easily to the tube and give a good bright reflective finish against the glass surface.
Terry CollinsGold Touch Inc.

Cleveland, Ohio
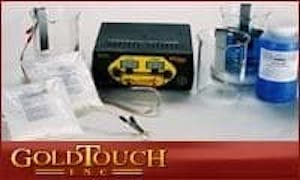
Q. Dear Mr. Terry Collins,
I need to plate glass from outer surface with 10 microns, Purpose to reflect UV/ IR rays. I request you. if you have any more idea about this please let me know.
Regards,
Nandkumar Barhate [returning]- Pune, India
A. If you are looking to reflect UV/IR than most any metal will do the job, not just gold. Most of those metals will do a wonderful job with only 1 micron instead of 10. Is there any other reason for choosing gold? Any reason for the thickness?
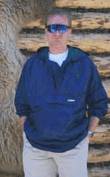
John Davis
- Berthoud, Colorado, USA
Q. Dear Mr. John Devis,
Purpose is Only to reflect IR Rays. 10 micron is my customers requirement,
Please let me know more about other metals,
Regards,
Nandkumar Barhate [returning]- Pune India
Electroless nickel plating of glass
RFQ: Need to plate 20 pieces of Pyrex glass (3/8" dia x 5/8" length) with electroless nickel to develop a soldering process for an automotive company. If successful, large quantities will need to be plated on a regular basis. Please contact me if you have experiences in plating glasses.
Brian L [last name deleted for privacy by Editor]R & D - Columbus, Ohio
2005
Ed. note: This RFQ is outdated, but technical replies are welcome, and readers are encouraged to post their own RFQs. But no public commercial suggestions please ( huh? why?).
Q. Hi,
Is it possible to carry out electroless Ni plating on glass? I wanted to make conductive glass spheres (0.5 to 1.0 mm) and someone suggested this method.
- Mumbai, India
March 17, 2015
A. Sachin,
Yes, it is possible and I have done it many times. After applying a coating, soldering and other operations become possible. Surface prep is key, as always. For a very robust system, consider lightly roughening the surfaces, cleaning then using a primer (such as an e-less Cu followed by electrolytic copper). Finally, the electroless Ni can be added as a topcoat. There are a few other methods as well. Good luck!
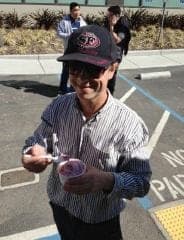
Blake Kneedler
Feather Hollow Eng. - Stockton, California
Q, A, or Comment on THIS thread -or- Start a NEW Thread