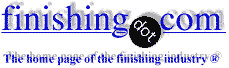
-----
Galvanizing Vats Overheating ... Quantifying Damage to Kettle
This question was originally posted in Portugese. The following transcription is after translation by translate.google.com, and interpretation by Ted Mooney of probable intent ...
Q. Good afternoon, blessed people.
I'm facing a very worrying situation right now.
I've been a production manager in a galvanizing industry for 9 years. Since then, we still haven't replaced the galvanizing tanks.
But, two months ago I noticed a difference in the temperature data, the tank behaved very strangely and suddenly there was an extreme heat that made the lead that was at the bottom of the zinc bath rise, and the zinc turned completely blue and the pieces came out brown and the zinc did not adhere to the metal.
I took action on this problem, stopping production, turning off the power supply, letting the zinc stand for three hours to precipitate the lead and lower the bath temperature. I called the electrical technician to correct the problem of poor heat supply from the resistors. After the temporary correction, I checked the zinc level in the bath and what surprised me was the significant increase in zinc sludge. I removed a total of 6 tons of zinc sludge. With the empty space generated I could see that the thermocouple was damaged and the zinc tank showed a line about 2 to 3 mm deep and 2.5 cm wide along the entire edge of the tank wall.
I would like your help, in giving me a specification of maximum wear or limit of a zinc tank before its replacement. I have many photos & videos that I would like to share with you, but unfortunately, I do not know how.
I thank you all
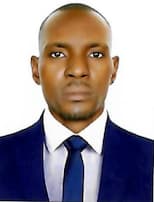
Utane Domingos
- Luanda Angola
September 28, 2024
![]() |
Dear readers, please post in English. The purpose of a public forum is to involve the readers in mutual interaction which isn't possible for postings in the many other languages of the world in a forum which has used the English language for 35 years and where the overwhelming majority of readers speak English. It's easy for posters to use services like translate.google.com to turn a posting into English, unfortunately it is not nearly so easy for us because we use forms and software which convert the original posting into the required HTML formats for the Internet, and in doing that they wreak havoc on foreign language postings, turning characters with foreign accent marks into gibberish. Plus if a reader doesn't translate to English and do a quick search of the site, it results in frequent duplicative Q&A's which discourages the other readers. Thanks for your understanding. |
A. Hi Utane.
The way to share additional photos is to attach them in e-mail to mooney@finishing.com and we will post them here. Thanks
Luck & Regards,
Ted Mooney, P.E. RET
Striving to live Aloha
(Ted can offer longterm or instant help)
finishing.com - Pine Beach, New Jersey
A. Utane,
There are some questions and clarifications required in your post, but based on what we know so far after Google translation and Ted Mooney efforts to interpret. (thanks!)
It sounds like your kettle in electrically heated? Correct?
Lead is much more dense than zinc. I cannot float to the top.
Also the limit of solubility of Pb (lead) in Zinc (Zn) is about 1.1%. No more will dissolve in the zinc, it will just settle to the bottom of the tank as liquid Pb, a lot hotter than its melting point.
It sounds like your thermocouple failed and your zinc overheated.
The normal wear of a kettle is about 2mm/year. It can vary between 1mm and 3mm under normal conditions and operating temperature of the Zn of 450C. If the zinc is heated hotter, the rate of wear on the kettle reaches about 10mm / day (thousands of times faster). In all these cases the steel of the kettle is dissolving in the zinc. When it dissolved it forms dross, an alloy of iron (Fe) and Zn, usually a crystalline formation, but the crystals are very brittle and break for make what looks like grains of sand. This dross is slightly heavier than zinc, so sinks to the bottom. It is lighter than Pb, so it sits on top of the Pb if there is some liquid Pb on the bottom. The ratio of Fe to Zn is about 1:19. In other words a kilogram of Fe makes 20 kg of dross, and to do so consumes 19 kg of Zn.
The zinc turning blue is an indication of very hot zinc.
You cannot "precipitate" lead from zinc easily, and there's only maximum 1% Pb dissolved anyway. That was not your problem.
Your pictures show other problems than just kettle erosion. There is excessive build-up of crusty ash/zinc near the top that will prevent good heat transfer and so allow the kettle steel to get hotter than the zinc, causing faster erosion. The dross (you have called it zinc sludge),will sink to the bottom where it can also prevent heat transfer into the zinc and cause accelerated wear. I have seen too many kettles with holes caused by these two reasons.
You said you removed 6 tonnes of zinc sludge (dross, the Fe/Zn alloy like sand), but we don't know your kettle size to get any idea if that much is a problem or not. What we can say is that it all came from dissolving steel (Fe) somewhere. Removing dross should be done every 2 weeks, or 1000 tonnes of production - whichever comes first. Any less often leads to danger in the kettle of a hole forming, and of the dross going hard making its removal harder still. Normal dross production is about 0.6% to 0.9% of tonnes galvanized. (6-9kg dross per tonne steel galvanized). More than this indicates problems somewhere.
The limit for a zinc tank is often 30mm thick. It starts at 50mm thick (most often, some are thicker) and should be replaced when the thinnest part is 30mm left. It is possible to measure the thickness of the remaining steel of the kettle with the zinc still in and still liquid. It takes specialist equipment, but this is available along with experienced technicians to do the job. Typically takes about 4-8 hours. Most kettles live for anything from 6-15 years, but this is very dependent on how much work they do. At 10,000 tonnes a year, expect about 10 years life. At 60,000 tonnes a year maybe 6-8 years. Not many kettles last more than 15, but a small number have done 20 years. These numbers are for well made kettles. For kettles from some suppliers, divide these numbers by 3. Changing kettles is a long job and costs a lot.
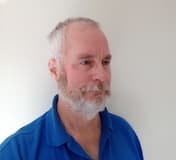
Geoff Crowley, galvanizing consultant
Crithwood Ltd.

Bathgate, Scotland, UK
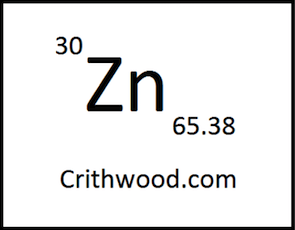
I can only thank you for all the technical clarification provided here. And as a Chemist by training, for me, it's another learning experience. And I hope you understand me when I'm asking some questions about technical situations, I feel I'm still very new in the sector. And learning from you is a great privilege.
My kettle measures (7.5m X 1.5m X 0.9m).
It has never benefited from maintenance for 9 years.
RFQ: I am also looking for suppliers of various products to supplement production, such as: Portable RFX spectrometer, Portable long probe thermometer, Benchtop spectrophotometer, nickel and zinc alloy for hot dip galvanizing bath, aluminum alloy and zinc for the hot dip galvanizing bath and others that I will be able to share later.
Greetings
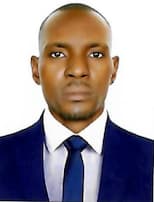
Utane Domingos [returning]
- Luanda Angola
privately respond to this RFQ
Ed. note: As always, gentle readers: technical replies in public and commercial replies in private please (huh? why?)
A. I only supply knowledge, and am independent of manufacturers, chemical suppliers etc. I do know most of the better known suppliers and can comment privately on their products. I do wonder though why you need some of the equipment you have specified? Its is quite feasible to run a hot dip galvanizing plant without sophisticated analysis instrumentation. Most Galvanizers will have a hydrometer, thermometer, burette, a few bits of glassware for titrations, some reagents and that's enough.
Consumables like zinc, pretreatment chemicals alloys etc have many suppliers.
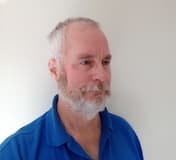
Geoff Crowley, galvanizing consultant
Crithwood Ltd.

Bathgate, Scotland, UK
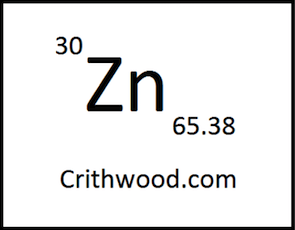
A. Dear Sir,
Apart from above answer, I'd like to add following points.
1. 2-3 mm deep line is due wash line of zinc level in that particular area. Ash sticks to wash line also.
2. Dross formation happened due to excess temperature than requirement (450 °C).
3. You are requested to check zinc ingot quality that you have purchased.
- Vadodara
October 17, 2024
Q, A, or Comment on THIS thread -or- Start a NEW Thread
