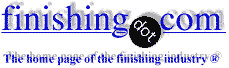
-----
304 steel continuously generates dark residue
Q. I apologize for this Q is somewhat long. I have previously asked this on metalworking and chemistry forums, and have so far found no solution. TLDR: I have a custom-made 304 steel part which is not [acting like] stainless. There is no "rust" on it per se, but it leaves a dark-grey residue when rubbed with a clean scientific-grade paper. I have never experienced this with mass-produced 304 steel parts, and I am looking for ideas on how to make the part "stainless".
Here is the long story. I have a custom-made air humidification tray welded of 1.2 mm thick 304 steel (supplier: Aperam, France, with certificates available). The tray is used in a medical device prototype: in it, the tray is filled with about 5 gal of warm di water (at ~100 °F or 38 °C), and air is blown between the water surface and a sealed acrylic lid. The warmed/humidified air is directed to an intubated patient for direct breathing. I previously used 304 and 316 commercial sanitary parts for this air circuit, and expected the 304 steel to be a suitable material for the custom-made humidifier (i.e. corrosion-and stain-free) .
When the tray arrived, it looked visually clean and degreased. I further rinsed it with soap and water. When I was wiping the part clean with scientific-grade kimwipes
⇦ on
eBay
or
Amazon [affil link]
, I noticed that the wipes turned dark grey when rubbed against the surface. This was not some grease left from the machining/welding, because additional degreasing with acetone, EtOH or even 5% NaOH did not solve the issue -- the grey residue still remained (or got even stronger). It appeared to originate from the steel itself, not from any contaminants on the surface. As a comparison, I did the same "kimwipe test" with commercially purchased 316 or 304 sanitary parts, and these left no reside on the paper (as expected).
I then tried a passivation protocol I found in this NASA publication (4% citric acid for 2 hrs at 180 °F). It did not help, instead it appeared to make the issue worse, as if activating the steel, but not making it passive.
https://ntrs.nasa.gov/api/citations/20110001362/downloads/20110001362.pdf
For passivation, I first treated the tray for 2 hrs with 5% NaOH (this turned the surface very hydrophilic and "activated", with the black residue remaining). Then I filled the tray with a boiling solution of 4% citric acid (no other additives, except that tap water was used), placed it in a styrofoam box+lid for 2 hrs and monitored the temperature. The temperature went from 170 °F to 160 °F in 2.5 hrs, which IMHO was close enough to the NASA protocol. I then rinsed the tray with tap water again. The part used to have small "rusty" spots" around the welds, and now they all turned shiny. However, the black residue, when I wiped the surface, was still there, and it got worse.
I think I cannot use this device w/o solving the issue. I do not know what the black residue is, and I probably do not want the substance leaching into water and end up in the lungs.
What are my options, and why is the 304 steel behaving like this? Should I
-- cut my losses and have a Ti piece made instead?
-- passivate professionally? but judging from the complete fail of the citric acid attempt, I am not sure if it's going to work.
-- attempt electroplating? Nickel has been suggested, but it is known to cause inflammation, thus, I am not comfortable using it. Silver plating? That will prob require Ni and Cu first, and I am not a fan of Cu in the air, either.
-- powder/ceramic coating? I have no experience with this, but I can research this further.
-- make a thick PE bag and insert it in the tray as a liner?
I apologize again for the long post.
- Freiburg, Germany
May 16, 2024
![]() |
A. Andrey, ![]() Ray Kremer Stellar Solutions, Inc. ![]() McHenry, Illinois ![]() A. Andrey, ![]() Anna Berkovich Russamer Lab ![]() Pittsburgh, Pennsylvania ![]() A. Hi Andrey, - Ballarat, Australia May 17, 2024 |
Thank you all for suggestions.
I have tried the same test with commercially purchased 304 and 316 steel parts (sanitary tri-link connectors), and there was no residue at all. These connectors are going to be used together with the tray in the final application.
There were no signs of polishing on the piece, except in some areas next to the welds. These did not appear to have more residue than other areas.
I have looked up the spec sheet of this 304 steel, and the manufacturer indicated that pickling and passivation were both required for the final product after welding. Their recommended conditions include treatment with HNO3 + HF (pickling) and 20% HNO3 (passivation). This was not done by the machine shop.
Mechanical treatment is not an option for me b.c. there are threads and hard-to-reach areas. I also expected that NaOH would remove the residue, if it had been mechanical. Finally, the paper that I cited mentioned that mechanical removal was not efficient (although they described smut, not mechanical
I will give the Italian company a call!
- Germany
privately respond to this RFQ
Ed. note: As always, gentle readers: technical replies in public and commercial replies in private please (huh? why?)
Q, A, or Comment on THIS thread -or- Start a NEW Thread