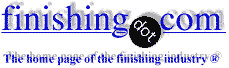
-----
Electroplating on complex geometry, a microlattice structure...

Q. Hello Experts,
I am trying to plate microlattice structures printed with Resin 3D printer.
The sequence I follow is, first I do the electroless Nickel plating followed by nickel electroplating with Watts plating bath.
The problem I am facing is I am unable to get uniform thickness at all the locations of the microlattice structure...
I am using two parallel nickel anodes at the centre of which my part is placed.
Kindly give suggestions to resolve the issue.
Thank you.
- Pune, Maharashtra, India
November 27, 2023
A. Hi Swapnil
The practical question first: Why can't you just electroless nickel plate it?
Luck & Regards,
Ted Mooney, P.E. RET
Striving to live Aloha
(Ted can offer longterm or instant help)
finishing.com - Pine Beach, New Jersey
Q. Hello Dr. ⇩ Ted Mooney,
Thank you for your prompt reply.
Actually, I need a thickness of 100 micron on this structure. Once I get this thickness, my target is to dissolve the internal polymer scaffold.
Hence, I am moving to nickel electroplating.
Student - Pune, Maharashtra, India
November 28, 2023
A. Hi again,
As I'm sure you realize, electroplating follows Faraday's Law of Electrodeposition, i.e., the thickness is directly proportional to the current density at any given point, whereas electricity 'seeks the shortest path', so it's difficult to get electricity to flow to the innards of your scaffold.
Brighteners and addition agents can help a bit, but they have limited influence. I would suggest pulse plating in hopes that it can help agitate the solution at a micro level, with less need for the ion migration to escape the attraction of the outer border elements.
It may prove necessary, though, to redesign the scaffold arrangement to minimize the difficulty current has in flowing to the innermost elements without being coaxed away by the outer elements.
But personally, I would not give up on heavy electroless nickel --
According to Chapter 8, 'Engineering Applications of Electroless Nickel; in Mallory & Hajdu's "Electroless Plating" [on
eBay ,
Amazon, or
AbeBooks affil links]
, thicknesses of 100 µ and more are used in a number of applications.
Luck & Regards,
Ted Mooney, P.E. RET
Striving to live Aloha
(Ted can offer longterm or instant help)
finishing.com - Pine Beach, New Jersey
Thank you again for your detailed explanation Dr. ⇩ Ted Mooney.
Will give it a try to achieve higher nickel thickness using electroless process.
Can you suggest the suitable bath composition for achieving this?
The electroless bath I am using contains, Nickel sulphate, Sodium Acetate, Sodium Citrate (complexing agent), and Sodium Hypophosphite (Reducing agent).
- Pune, Maharashtra, India
December 3, 2023
A. Hello again Swapnil.
Your ingredient list sounds reasonable, but you may not realize that in the West it is unheard of to make up your own e-nickel formulation. Rather, we buy a fully developed process from suppliers who have already invested the many man-years of research towards perfecting the formulation.
Although many components are plated 100 µm thick, the overwhelming majority are not. So 100 µ would probably be considered special. An electroless nickel process vendor can surely help you attain it. EN expert Ron Duncan (dec.) suggests that mechanical agitation as well as air agitation will be required. Please see thread 43258.
Luck & Regards,
P.S.: No stolen valor for me please. I certainly never endured the long & strenuous process of obtaining a PhD :-)
Ted Mooney, P.E. RET
Striving to live Aloha
(Ted can offer longterm or instant help)
finishing.com - Pine Beach, New Jersey
Q, A, or Comment on THIS thread -or- Start a NEW Thread