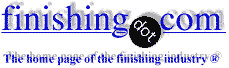
-----
Problems with thick Electroless Nickel Plating (>40µm)

Q. I need to plate a thickness of 40 mils with electroless nickel, I'm looking for a company that could do that or that sells the chemicals to do it.
Thanks in advance
Robin Francois- Boston, Massachusetts
2000
![]() |
A. 40 mils is extremely difficult to do. The bath has to be tweaked to no pit and not passivate. This calls for it to be plated extremely slowly and would very nearly have to be a zero or low internal stress or you will have problems. It will be expensive and you can expect it to be stripped several time or be blind dumb lucky to get it on the first try. I have heard, but never seen 10 mills, but never 40. What is wrong with something like a sulfamate nickel heavy plate, machined and an EN top coat of say 3 mills. James Watts- Navarre, Florida 2000 A. Sirius Technology in Oriskany, NY is a manufacturer of EN chemistries. Their developmental people can help you with this application. ![]() Megan Pellenz - Syracuse, New York 2000 ---- |
A. If it is not feasible to electroplate economically, try thermal spray technique. There are job-shops providing the service.
Mandar Sunthankar- Fort Collins, Colorado
2000
Q. I am looking for some info about thick Ni-P (P wt.%
>11%).
I would like to let the deposited layer more than 150 um, or more than 300 um.
is there any method to prevent the pinholes on the thick EN surface?
is it possible that electroplating method can get the thick EN with more than 11 wt.% P and without pinhole?
thank you,
- Taipei, Taiwan
2006
2006
A. Pinhole free high phosphorus type EN coatings are possible, but require that the substrate also be free of defects (like pores and inclusions) that will initiate pinholes or other coating defects.
EN coatings of 250 - 300 µm are commonly plated for salvage of worn or mismachined parts without difficulty. With these thick coatings it is helpful to mechanically agitate the parts during plating, along with general air agitation of the solution.
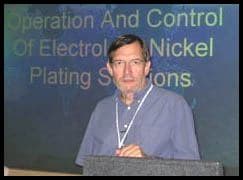
Ron Duncan [deceased]
- LaVergne, Tennessee
It is our sad duty to note Ron's passing on Dec. 15, 2006. A brief obituary opens Episode 13 of our Podcast.
A. As properly stated by Mr. Duncan pin holes generally come from existing superficial defects. Also, from gas bubbles that adhere to the plated surface (then they look bottom-rounded and bright), from solid particles in the bath due to improper filtration, poor chemistry or poor processing practices. In general, if the corrective measures are not taken, the same results may be expected from an electrolytic NiP process.
Guillermo Marrufo2006
Multiple threads merged: please forgive chronology errors and repetition 🙂
Q. We found that it is difficult to electroless plate Nickel on the brass to achieve the thickness greater than 43 µm.
I will appreciate it if you can give me advice on the successful process you used to achieve the required thickness.
Thank you very much
Medical Device MFG - Tucson, Arizona, USA
2006
A. Over 1.5 mils of EN, though quite possible, is not very common. Brass is also not a very common substrate either. It is not catalytic to the reaction for it is more electropositive than the nickel ion. So, you need to start it first to attain good adhesion. A professional and reliable start would be to preplate strike your parts in a conventional Watts bath. Alternatively, a brief electric kick as soon as the parts get into the EN bath using an inert anode may work. Something else, if your substrate has lead, its presence over the surface may also be a problem.
Guillermo MarrufoMonterrey, NL, Mexico
2006
Q. I did the Nickel strike as preplate. But we found pinholes when the layer grow thicker than 32 µm. It is hard to grow any more with extended time. Is there any advice on reducing the pores or pinholes?
John PengMedical Device MFG - Tucson, Arizona, USA
2006
A. John, you do not say what sort of brass you are using - if it is free machining brass it probably contains lead and this can cause lead smear and problems in coverage. I am surprised you have to go as thick as 30 microns to get a continuous coating - I would normally expect to get a continuous coating in about 5 microns of electrolytic nickel and perhaps a bit more (up to 10 microns in electroless), especially if the bath isn't agitated and gas bubbles removed. However, there are so many variables with these processes, it is difficult to generalise. Brass is not easy to initiate for electroless nickel, so you may need to give it a gentle poke by starting it with some gentle cathodic polarisation; once the electroless nickel bath is going, it will keep doing so. I do not fully understand why you need such thick electroless nickel - perhaps you may want to consider using electrolytic nickel, which is quicker and cheaper. Furthermore, you can plate directly onto brass once it has been correctly cleaned and activated.
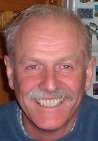
Trevor Crichton
R&D practical scientist
Chesham, Bucks, UK
2006
A. Pores or pitting is sometimes an issue with simple low cost EN formulations, more so when plating thick layers. Review what Mr. Crichton pointed out but also check for a pore free formulation with your actual chemicals vendor or go out for shopping somewhere else.
Guillermo MarrufoMonterrey, NL, Mexico
2006
A. Talk to your vendor's tech services! You should be able to plate 42 with no problem with a proper bath and proper plating operation. You can expect to run into a few problems when you try to go over 50 and a lot of problems with a simple bath at over 60.
Get the vendor involved. They tend to get real interested when you say that you will have to switch to another vendor if they can not solve the problem. If you do not like what they say, talk to another vendor and see what they will guarantee.
- Navarre, Florida
2006
A. The Wood's Nickel could be contaminated with organic materials. In this case you will have to filter with activated carbon.
Enrique Bustos- Cordoba, Argentina
2007
A. Hi John,
What is the thickness that you are aiming for? There are other methods to coat nickel which can give a thickness above 50 microns.
Coating - Baton Rouge, Louisiana
2007
Problems in High Phosphorus Electroless Nickel Plating
Q. We are plating 38-45 microns of Nickel through High Phosphorus Electroless Nickel Plating. We are using Glass heaters to maintain the temp b/w 83-89 °C.
We are facing serious problems of Rough deposition after 15-20 microns. Also we are facing pin holes on the surface. Please suggest us how to overcome this.
- Bangalore
August 11, 2013
August 13, 2013
A. A lot more detail of your set up is necessary to get a meaningful answer from this site.
What are your pre-treatments?
What is the typical plating rate?
What is the analysis of the tank like? Are you seeing high variations in nickel and/or pH?
How many metal turnovers (MTO) do you run to?
What sort of filtration and agitation do you have?
Pinholes can be caused by many things such as poor agitation, lack of wetting agent, pH imbalance...
Roughness is usually caused by inclusions in the coating, such as dust or nickel "seeds".
Take some time to give more detail and I'm sure you will get something to help you.
Aerospace - Yeovil, Somerset, UK
A. Brian gave a very complete answer for the information given.
The chemistry is something that you should be maintaining a tight control over. With that as a given, improving the filtration should help. Improving the agitation will definitely help.
The "nickel seeds" intrigued me. How often do you strip your tank?
- Navarre, Florida
August 13, 2013
August 16, 2013
Q. Mr.Brian Terry,
I would like to give clarifications to your questions.
1. Pre treatment is with de-greasing with alkalies at 45-60 °C temperature, followed by anodic cleaning.
2. Plating rate is 10 microns per hour.
3. We are doing analysis every 30 minutes. Plating tank size is 130 ltrs.
4. Maximum 2.5 metal turnover.
5. We have continuous 1 micron bag filtration.
6. Currently we are not using agitation because the filter runs continuously.
7. Nickel metal maintained b/w 5.2-5.8 dms/ltr
8. pH maintained is 4.4 -4.8
9. Bath temperature is 83-89 °C
Kindly explain what is nickel seeds?
Hope with this you can give your valuable suggestion.
electroplaters - Bangalore, Karnatala, India
A. A huge amount of this depends on the company that manufactures the EN solution and what their ops sheet calls for.
My experience with 2 high P EN would say that your temp is a wee bit low, and your plate rate is a bit low. Our pH was a tiny bit lower than yours, but it all depends on the formula for the EN.
Oil less air agitation would probably give you more metal turn overs and probably a better plate rate. It is not that expensive and it is mandatory for some formulations as well as beneficial for any formulation that I have heard of.
We could plate to 45 micron with no problems, but had some problems over 55 microns. (skip plating)
- Navarre, Florida
August 16, 2013
A. Nickel strike is a must for good adhesion.
In order to be able to plate a thick deposit, you MUST operate your solution with a slow plating rate like 4-5 microns per hour.
To prevent pitting use a wetter. Ask your vendor for an appropriate wetter.
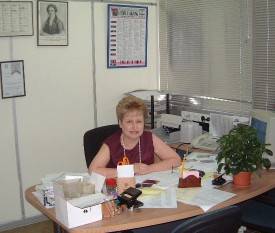

Sara Michaeli
Tel-Aviv-Yafo, Israel
October 31, 2013
A. Sara and I have been at this site a long time and we rarely disagree, but I will this time.
First, ideal plate rate depends on the chemistry of the solution.
On the 2 high P EN solutions that I used, the bath would try to self destruct at that plate rate. The costs of the extra time for labor, lab, electricity and etc would make it very expensive.
The lowest that we used was about 15 per hour and typical was 25 per hour with zero problems to about 50 microns.
- Navarre, Florida
November 1, 2013
A. Jim,
It is rare to plate 50 microns when the plating speed is 15-25 microns per hour.
The plating rate is not only a function of chemistry. You can lower the plating rate by lowering the pH, temperature and Nickel concentration.
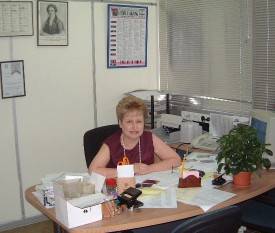

Sara Michaeli
Tel-Aviv-Yafo, Israel
November 18, 2013
A. I guess that our tanks were like bumble bees which do not know that aerodynamically, they cannot fly, so they do.
We rarely plated less than 30 and normally 45 thickness and did it at 20 to 25 per hour.
Drip additions, lots of air, good temp control and pH control.
- Navarre, Florida
November 18, 2013
Q, A, or Comment on THIS thread -or- Start a NEW Thread